СОВЕРШЕНСТВОВАНИЕ ТЕХНОЛОГИЧЕСКОГО ПРОЦЕССА ИЗГОТОВЛЕНИЯ ДЕТАЛИ «ВТУЛКА»
4.1.КРАТКОЕ ОПИСАНИЕ ТЕХНОЛОГИИ, ПРИМЕНЯЕМОЙ В ЦЕХЕ
Механические цехи в структуре завода занимают промежуточное положение, так как начинают производственный процесс заготовительные цеха, а завершают – сборочные. Они обеспечивают превращение материалов и заготовок в готовые элементы машин и обеспечивают сборку.
В состав механического цеха входят производственные участки, вспомогательные отделения, служебные и бытовые помещения. Производственный участок служит для размещения на нем оборудования, предназначенного для выполнения технологических операций обработки и сборки изделий.
Цех, в котором происходит механическая обработка детали, предусматривает следующего универсального и специального оборудования: токарно-револьверные и токарные многорезцовые станки, вертикально-протяжные станки, хонинговальные, торцекруглошлифовальные, карусельно-фрезерные станки, сверлильные вертикальные полуавтоматы и др.
Подача заготовок из пролет и с одного станка на другой производится электрическими тележками или автокарами с подъемными платформами, а также тележечными и подвесными конвейерами. При обработке малогабаритных заготовок передача их по операциям производится небольшими партиями. Для этого на конвейере предусмотрены определенные места (лотки) для установки тары с обрабатываемыми заготовками. Для удаления стружки на рабочей зоны станки оборудованы специальными устройствами инерционного типа, которые перемещают стружку в короб, расположенный с тыльной стороны станка. Дальнейшая транспортировка коробов со стружкой от станков к местам сбора производится с помощью электротележек.
|
|
4.2 ВЫБОР ОБЪЕКТА ПРОЕКТИРОВАНИЯ
В качестве объекта проектирования выбран технологический процесс изготовления детали – втулки, которая предназначена для шлицевого соединения деталей трактора. Втулка выпускается в количестве 1000 штук в год, соответственно, тип производства – серийный.
Материал детали – сталь 25 ХГТ; твердость НВ 156…229; заготовка – паковка. Масса заготовки – 2,52 кг. Масса детали – 1,1 кг; коэффициент использования материала равен 0,436.
Механическая обработка втулки в цехе производится с помощью токарных, протяжных, шлифовальных, хонинговальных и других операций. Для данной втулки предъявляются высокие требования к качеству поверхности. Заготовка имеет простую форму, ее размеры и конфигурация близки к параметрам готовой детали, следовательно, конструкция детали технологична.
Трудоемкость механической обработки детали составляет 15,887 минут.
|
|
4.3.АНАЛИЗ СУЩЕСТВУЮЩЕГО ЗАВОДСКОГО ВАРИАНТА ТЕХНОЛОГИЧЕСКОГО ИЗГОТОВЛЕНИЯ ДЕТАЛИ
На ХТЗ в качестве заготовки для изготовления втулки используют паковку, получаемую горячей штамповкой в закрытых штампах на кривошипном горячештамповочном прессе (КГШП).Поковка имеет форму цилиндра, в котором затем прошивают отверстие диаметром 49 мм. Сердцевина заготовки после прошивки идет в отходы.
Существующий заводской вариант техпроцесса механической обработки втулки представлен в таблице 4.1.
Таблица 4.1. – Технологический процесс изготовления втулки
№ опер. | Наименование операции | Оборудование, модель | Тшт, мин |
1 | 2 | 3 | 4 |
000 | Заготовительная | ||
005 | Токарно-револьверная | Ток.-револ. 1П365 | 3,825 |
010 | Токарная | Ток.м/резц. 1Н713 | 2,417 |
015 | Вертикально-протяжная | Верт.-прот. 7Б66Н054 | 0,819 |
020 | Токарная | Ток.м/резц. 1Н713 | 3,458 |
025 | Зачистка | Верстак | 0,241 |
030 | Технический контроль | Стол контрольный | |
035 | Техническая обработка(термообр) | ||
040 | Хонинговальная | Хонинг.3М82С153 | 0,919 |
045 | Круглошлифовальная | Торцекр.-шл.3Т153Е | 1,239 |
050 | Токарная | Ток.м/резц. 1Н713 | 2,77 |
055 | Промывка | М.моечная 399-1249 | 0,199 |
060 | Технический контроль | Стол контр. | |
Итого | 15,887 |
|
|
В настоящем проекте предлагаются следующие мероприятия по усовершенствованию существующего на заводе технологического процесса:
а) применение в качестве заготовки толстостенной трубы, что позволит значительно снизить расход материала, а также уменьшить припуски на обработку.
4.4.ПРОЕКТИРОВАНИЕ ТЕХНОЛОГИЧЕСКОГО ПРОЦЕССА ИЗГОТ ОВЛЕНИЯ ДЕТАЛИ «ВТУЛКА»
От степени совершенства способов получения исходной заготовки зависит расход материала, инструмента, количество операций обработки и их трудоемкость, себестоимость процесса изготовления детали в целом.
Необходимо стремится к тому, чтобы форма и размеры исходной заготовки были максимально близки к форме и размерам детали.
На Харьковском тракторном заводе в качестве исходной заготовки выбрана паковка, полученная горячей штамповкой в закрытых штампах и прошивкой. При этом большая часть заготовки 49 мм и длиной 76 мм идет в отходы. Ее масса равна 1,13 кг.
Себестоимость изготовления такой поковки равна:
Сз=а*т3*К n (4 . 1)
|
|
где а – стоимость единицы массы металла заготовки в зависимости от его марки, геометрической сложности заготовки и способа получения, грн.;
m 3 – масса металла, затрачиваемого на производство заготовки, т;
К n – коэффициент, учитывающий тип и вид производства заготовки (для штамповки на прессе К n =2,0);
С3=2720*(0,00252+0,00113)*2=19,85 грн.
В проекте, в отличие от принятой заводской технологии, предусмотрено получение исходной заготовки из толстостенной трубы.
Данное мероприятие обеспечит экономию материала, инструмента и времени на механическую обработку втулки.
Исходная труба имеет параметры: внешний диаметр – 84 ммвнутренний диаметр – 51мм, длина – 76 мм, масса – 2,10 кг. При этом себестоимость заготовки составит:
Сзн=2720* 0,0021* 2 =11,42(грн.)
Рассчитанный показатель свидетельствует о том, что себестоимость заготовки, полученной из трубы, ниже себестоимости исходной поковки. Следовательно, предложенный выбор варианта заготовки является экономически более целесообразным.
Коэффициент использования материала составит:
Ким=1,1/2,1 = 0,52
Полученное значение коэффициента подтверждает правильность выбора метода получения заготовки.
Уменьшение припусков на обработку позволит исключить операцию чернового зенкерования отверстия втулки и обеспечит снижение трудоемкости механической обработки на 0,8 мин.
4.4. РАСЧЕТ ПРИПУСКОВ НА МЕХАНИЧЕСКУЮ ОБРАБОТКУ
Припуск – это слой материала, удаляемый с поверхности заготовки для достижения заданных свойств обрабатываемой поверхности детали.
Припуск на обработку поверхностей детали может быть назначен по соответствующим справочным таблицам или на основе расчетно-аналитического метода определения припусков.
Расчетно-аналитический метод определения припусков на обработку базируется на анализе факторов, влияющих на припуски предшествующего и выполняемого переходов технологического процесса обработки.
Ниже приведен расчет припусков на обработку наружной поверхности втулки h6(-0,022)
Исходные данные для расчета припусков на механическую обработку:
а) наименование детали – втулка, заготовка – поковка;
б) материал – сталь 45ХГТ;
в) элементарная поверхность для расчета припусков – наружный диметр h6(-0,022);
г) на всех технологических переходах для фиксации заготовки используется оправка.
Минимальный припуск при обработке наружных поверхностей равен:
2 Z i min = 2[(R z + h) i-1 + √ ( Δ І∑i-1 + ε² i )], (4.2)
где Rzi -1 – высота неровностей профиля шероховатости поверхности на предшествующем переходе;
hi -1 - глубина дефектного поверхностного слоя на предшествующем переходе;
- суммарное отклонение расположения поверхности на предшествующем переходе;
- погрешность установки заготовки на выполняемом переходе.
При шлифовании заготовки после термической обработке поверхностный слой должен быть сохранен, поэтому слагаемое h из формулы исключают.
При выглаживании припуск на обработке определяется высотой неровностей поверхности.
Небольшой предельный припуск для обработки наружных поверхностей равен:
2Zimax=Dmaxi-1 – Dmax (4.3)
2Zimin=Dmini-1-Dmini (4.4)
Значения составляющих єлементов минимального припуска Rz, h, приняты по справочным нормативным данным для расчета припусков [30,с.185-189].
Расчет припусков и промежуточных размеров по технологическим переходам при аналитическом методе расчета приведен в таб. 4.2.
Таблица 4.2 – Расчет припусков и предельных размеров по технологическим переходам.
Элементарная поверхность детали и технологический маршрут ее обработки | Элементы припуска | Расчетный припуск 2Zimin, мкм | Расчетный мин.размер мм | Допуск на изготовление TD, мкм | Предельные размеры, мм | Предельные припуски, мкм | |||||
Rz | h | Δ ∑ | ε | Dmax | Dmin | 2Zmax | 2Zmin | ||||
Поковка | 80 | 200 | 430 | - | - | 83,192 | 2900 | 89,9 | 87,0 | - | - |
Точение черновое | 40 | 40 | 57,75 | 175 | 1488 | 81,704 | 350 | 82,5 | 82,15 | 7,4 | 4,85 |
Точение получистовое | 20 | 20 | 4,08 | 120 | 426 | 81,278 | 220 | 81,7 | 81,48 | 0,8 | 0,67 |
Шлифование | 0,63 | - | 8,1 | 110 | 300 | 80,978 | 22 | 81,0 | 80,978 | 0,7 | 0,502 |
Выглаживание | 0,32 | - | - | - | - | 80,978 | 22 | 81,0 | 80,979 | 0 | 0 |
Итого | 8,9 | 6,022 |
Проверка расчета :
2 Zomax -2 Zomin = TD з- TD д
где 2 Zomax и 2 Zomin – общие предельные припуски;
TD з – допуск на изготовление заготовки;
TD д – допуск на изготовление готовой детали.
8900-6022=2900-22
2878=2878
Расчетные минимальные припуски на обработку подтверждают правильность выбора параметров заготовки.
4.4.2. РАСЧЕТ РЕЖИМОВ РЕЗАНИЯ И ОСНОВНОГО ВРЕМЕНИ
Режим резания металлов определяется следующими основными параметрами: глубиной резания t, подачей S и скорость резания V. Исходными данными для выбора режима резания являются сведения об изготовляемой детали и ее заготовке, а также данные о применяемом оборудовании и инструменте.
Необходимо рассчитать режимы резания и основное время для зенкерования на токарно-револьверной операции 005, выполняемой на токарно-револьверноя станке 1П365.
Глубина резания при зенкеровании рассчитывается по формуле:
t=0,5(D-d), (4.5)
где d и D – диметры отверстия соответственно до и после зенкерования, мм;
Подача при отсутствии ограничивающих факторов принимается максимально допустимая.
Скорость резания при зенкеровании V, м/мин., определяется по формуле:
, (4.6)
где Сv – постоянный коэффициент, учитывающий вид и марку обрабатываемого материала [31, с278, таб.29];
Т - период стойкости;
Кv – общий поправочный коэффициент на скорость резания, учитывающий фактические условия резания;
Kv = K м v KuvKtv (4.7)
где K м v – коэффициент на обрабатываемый материал [31, c.261-263, табл.1-4];
Kuv - коэффициент на инструментальный материал [31, с.263, табл.6];
Klv - коэффициент, учитывающий глубину обрабатываемого отверстия [31, с.280, табл.31];
При зенкеровании штампованных отверствий вводится дополнительно поправочный коэффициент Kпv [31, c.263, табл.5].
Значения коъффициента Сv и показатели степени x,y,m взяты по справочным данным [31, с.269, табл.17].
Частота вращения шпинделя рассчитывается по формуле:
(4.8)
Полученную частоту вращения корректируют по паспортным данным станка и расчитывают фактическую скорость резания:
(4.9)
Мощность резания при зенкеровании, кВт, определяют по формуле:
; (4.10)
где Мкр – крутящий момент, который рассчитывается по формуле:
; (4.11)
значения коэффициентов и показателей степени взяты в нормативных данных [31, с.281, табл.32].
Основное время определяют по формуле:
(4.12)
где L –полный путь, проходимый инструметов в направлении подачи.
Определяем глубину резания:
1-й переход: t=0,5(53-51)=1,0;
2-й переход: t=0,5(54,8-53)=0,9;
Определяем подачу:
S=1,1-1,3 мм/об
Рассчитываем скорость резания при зенкеровании:
1-й переход: мм/об
2-й переход: мм/об
Определяем частоту вращения шпинделя:
1-й переход: =77 об/мин;
2-й переход: об/мин;
Определяем фактическую скорость резания:
1-й переход: мм/об
2-й переход: мм/об
Рассчитываем мощность резания:
1-й переход: Мкр=10*0,09*53,21*10,9*1,20,8*1=60,36 Нм;
кВт;
2-й переход:
Мкр=10*0,09*54,81*0,90,9*1,20,8*1=46,68 Нм;
кВт;
Определяем основное время:
1-й переход: мин;
2-й переход: мин;
Время на зенкерование за два перехода снизились на 0,03 мин.
Основное время на токарно-револьверной операции 005 снизились на 0,83 мин.
4.4.3. ОПИСАНИЕ КОНСТРУКЦИИ И ПРИНЦИПА ДЕЙСТВИЯ СТАНОЧНОГО ПРИСПОСОБЛЕНИЯ.
В качестве приспособления на токарной операции выбрана цанговая оправка. С ее помощью осуществляется установка внутренней поверхностью вращения втулки и перпендикулярной к ее оси плоской поверхностью.
Оправка состоит из корпуса, фланца, цанги и штока. Фланец служит для надежного прикрепления оправки к планшайбе станка винтами. Шток проходит через шпиндель и соединяет опраку с пневмоцилиндром. Ход штока в разных направлениях позволяет открывать и закрывать лепестки цанги, которые держат втулка. Так как оправка имеет конусообразную форму, для фиксации положения детали имеется штифт. Гидропластмассовые оправки имеют пониженную функциональную надежность из-за высыхания гидропластмассы и утечек газообразной смазки. Сила закрепления заготовки – осесимметричная.(прил.Б).
4.4.4. РАСЧЕТ СПЕЦИАЛЬНОГО РЕЖУЩЕГО ИНСТРУМЕНТА
Исходные данные для выбора режущего инструмента: на токарно-револьверном станке 1П365 производится черновое зенкерование отверстия до диаметра 53Н13 на глубину 76 мм. Обрабатываемый материал – сталь 25ХГТ с НВ 156…229.
Большинство конструкций металлорежущего инструмента изготовляют – рабочая часть из инструментального материала, крепежная из обычных конструкционных сталей (сталь 45, 50, 40Х).
Выбираем насадной зенкер со вставными ножами из быстрорежущей стали P18, так как эта марка стали отличается удовлетворительной прочностью, повышенной износостойкостью при малых и средних скоростях резания и широким интервалом закалочных температур, имеет удовлетворительную шлифуемость и пригодна для обработки обычных конструкционных материалов в условиях динамических нагрузок. Крепежная часть зенкера изготовлена из стали 45Х. Рабочая часть инструмента в виде пластин из быстрорежущей стали соединена с крепежной с помощью сварки (приложение Б).
Диаметр инструмента – 53.2 мм, длина – 510 мм, число зубцов – 4.
Устанавливаем геометрические параметры зенкера по нормативам [31, с.155, табл.48] , Для обработки стали НВ 156…229 при режущей части из быстрорежущей стали передний угол γ = 12є ; задний угол α = 10є ; угол в плане
φ = 60є ; φ1 = 30є; угол наклона спирали ώ = 20є ; ширина фаски = 0,8 мм, угол наклона инструмента λ = 0 при обработке стали.
Средний период стойкости зенкера – 80 мин.
Дата добавления: 2019-07-15; просмотров: 1230; Мы поможем в написании вашей работы! |
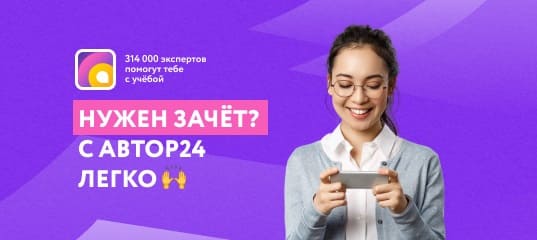
Мы поможем в написании ваших работ!