ОПИСАНИЕ КОНСТРУКЦИИ И ПРИНЦИПА ДЕЙСТВИЯ КОНТРОЛЬНО – ИЗМЕРИТЕЛЬНОЙ ОСНАСТКИ , ВЫПОЛНЕНИЕ РАСЧЕТОВ ПО ОБОСНОВАНИЮ ОСНОВНЫХ ПАРАМЕТРОВ ПРЕДЛАГАЕМОЙ ОСНАСТКИ
При изготовлении деталей их действительные размеры в силу различных причин иногда оказываются вне поля допуска. Годность действительных размеров устанавливают либо путем их измерения , либо путем контроля (приложение Б).
Для контроля отверстий используются калибры – пробки. Номинальный размер проходной стороны пробки ПР равен наименьшему предельному размеру отверстия. Непроходная сторона калибра – пробки НЕ должна входить в отверстие , поэтому ее номинальный размер равен наибольшему предельному размеру отверстия.
Необходимо проконтролировать размер отверстия 53Н13.
Для 13 – го квалитета точности верхнее предельное отклонение ES = +460 vrv? Yb; нижнее предельное отклонение EI = 0.
Наибольший предельный размер Dmax = D + ES = 53 +
+ 0,46 = 53,46 мм.
Наименьший предельный размер Dmin = D + EI = 53 + 0 = = 53 мм.
Допуск на изготовление калибров-пробок (по ГОСТ 24853 – 81 для IT13):
Н = 30 мкм.
Отклонение середины поля допуска на изготовление проходного калибра для отверстия от проходного предела отверстия ( по ГОСТ 24853 – 81 для IT 13):
Z = 48 мкм.
Допустимый выход размера изношеного проходного калибра для отверстия за проходной предел отверстия ( по ГОСТ 24853 – 81 для IT 13) :
У = 0.
Расчет исполнительных размеров калибров для контроля размера О53 Н13 производится по следующим формулам :
|
|
А) проходной калибр-пробка :
1) наибольший предельный размер проходного калибра – пробки :
ПP max = Dmin + Z + H/2; (4.13)
ПP max = 53 + 0.048 + 0.015 = 53.063
2) наименьший предельный размер нового проходного калибра-пробки :
ПP min = Dmin + Z - H/2; (4.14)
ПP min = 53 + 0.048 - 0.015 = 53.033
3) размер проходного калибра – пробки , проставляемый на чертеже :
ПP = ПР max - H ; (4.15)
ПP = 53.063 – 0.03 ;
4) наименьший размер изношенного проходного калибра – робки :
ПP изн = Dмин - У; (4.16)
ПP изн = 53 - 0 = 53;
Б) непроходной калибр – пробка
1) наибольший предельный размер непроходного калибра – пробки :
НЕ max = Dmax + H/2; (4.17)
НЕ max = 53.46 + 0.015 = 53.475 ;
2) наименьший предельный размер нового непроходного калибра-пробки :
НЕ min = Dmax - H/2; (4.18)
НЕ min = 53,46 – 0,015 = 53.445
3) размер непроходного калибра – пробки , проставляемый на чертеже :
НЕ = НЕ max - H ; (4.19)
НЕ = 53.475– 0.03 ;
Схема расположения полей допусков калибров для отверстия О 53 Н13 представлена на рисунке 4.1.
|
|
Рисунок 4.1 – Схема расположения полей допусков калибров для отверстия О 53Н13
ВЫВОДЫ
В результате предложенных в проекте мероприятий по изменению выбора исходной заготовки для детали «втулка» удалось снизить ее себестоимость на 8,43 грн. за счет экономии металла. Правильность выбора варианта заготовки подтверждает тот факт , что коеффициент использования материала увеличился с 0,436 до 0,52.
Также в результате уменьшения припусков снижается основное время механической обработки втулки на 0,83 мин. Расчет контрольной оснастки режущего инструмента и станочного приспособления доказал обоснованность их выбора на Харьковском тракторном заводе.
5. НОРМИРОВАНИЕ ТРУДА
В производственном процессе первичным звеном является рабочее место, поэтому от уровня его организации в значительной мере зависит эффективность , производительность труда. Важным фактором , способствующим эффективному высокопроизводительному труду . является рациональная планировка рабочего места.
В цехах завода ХТЗ планировка рабочего места обеспечивает наиболее удобные и безопасные условия труда . спсобствует сокращению трудовых движений , снижению утомляемости работника и экономиии рабочего времени. Асе рабочие места основных рабочих соответствуют требованиям научной организации труда.
|
|
Применяемая система обслуживания рабочих мест – регламентная , при которой службы обслуживания заранее комплектуют и централизованно доставляют на рабочее место все необходимое для выполнения очередной работы.
На заводе применяется повременно-премиальная и сдельно-премиальная системы оплаты труда. По сдельно-премиальной системе в 2000 году на заводе работало 1518 рабочих, остальные рабочие и служащие работали в условиях повременно – премиальной системы оплаты труда. Общее количество действующих норм времени – 46286 единиц, в том числе технически обоснованных – 36520 единиц. Удельный вес технически обоснованных норм времени составил 78,9 %. Средний уровень выполнения норм выработки в 2000 году составил 242,9% , что на 38,1 % превышает уровень 1999 года. Особенно высокий уровень выполнения норм выработки достигнут в цехах ;
- Механическом 1 – 274,5 %;
- Механическом 2 –280,9 %;
- Сборочном – 282,6 %;
- Окрасочном –289 %;
Отчет о выполнении норм выработки рабочими-сдельщиками представлен в таблице 5.1
|
|
На заводе для нормирования труда используются следующие нормативы :
А) общемашиностроительные нормативы режимов резания для технического нормирования работ на металлорежущих станках – М., Машиностроение , 1974 ;
Б) общемашиностроительные нормативы времени вспомогательного, на обслуживание рабочего места и подготовительно-заключительного на работы, выполненные на металлорежущих станках . Серийное производство – М.: Машиностроение, 1974;
В) общемашиностроительные нормативы времени на ручную электродуговую сварку малоуглеродных и низколегированных сталей – М.: Машиностроение, 1972.
Таблица 5.1 – Отчет о выполнении норм выработки рабочими – сдельщиками за 2000 год.
Профессия | Уровень выполнения норм выработки | Итого,чел | Ср.% | ||||||
До 100 | 100-150 | 105-110 | 110-120 | 120-130 | 130-150 | Свыше | |||
Рабочие основнх и вспомогательных цехов | - | 2 | 9 | 15 | 28 | 94 | 1369 | 1578 | 242,9 |
В том числе профессии : | |||||||||
Токари | - | 1 | 1 | 9 | 1 | 4 | 353 | 369 | 248,5 |
Токари – карусельщики | - | - | 1 | 3 | - | 9 | 84 | 97 | 236,9 |
Токари-расточники | - | - | 1 | 3 | 1 | 11 | 166 | 182 | 240,1 |
Фрезеровщики | - | 1 | 1 | 2 | 13 | 122 | 139 | 278 | 251,3 |
Сверловщики | - | - | 1 | - | 3 | 10 | 192 | 206 | 242,6 |
Сварщики | - | 1 | - | - | 4 | 13 | 103 | 121 | 234,2 |
Операторы | - | - | 3 | - | 7 | 15 | 85 | 110 | 225,2 |
Слесари- механосборщики | - | - | - | - | 4 | 7 | 145 | 156 | 252,6 |
Кузнецы | - | - | - | - | 3 | 7 | 64 | 74 | 248,3 |
Формовщики | - | - | 1 | - | 3 | 5 | 55 | 64 | 244,5 |
Из таблицы 5.1 можно сделать вывод , что на заводе значительно перевыполнили свои нормы выработки 1512 рабочих-сдельщиков. Такое перевыполнение можно объяснить ростом производительности труда , а также необосноваными завышеными нормами , действующими на заводе.
Состояние нормирования труда на ОАО «ХТЗ» представлено в таблице 5.2
Таблица 5.2 – Состояние нормирования труда на ОАО «ХТЗ»
Наименование | Численность рабочих | |||
Всего, чел | В %, к общей численности | В том числе из них по технически обоснованным нормам | ||
Всего, чел | В % | |||
Рабочие – сдельщики | 1518 | 17,6 | 1366 | 20,04 |
Рабочие – повременщики | 5328 | 61,8 | 4049 | 59,4 |
Из них : | ||||
Работающие по нормированным заданиям | 5328 | 61,8 | 4049 | 59,4 |
Специалисты и служащие | 1777 | 20,6 | 1403 | 20,56 |
Всего | 8623 | 100 | 6818 | 100 |
Под нормированием труда понимается установление норм затрат труда на изготовление единицы продукции или выработки продукции в единицу времени.
Нормы затрат могут быть выражены в нормах : времени, выработки, обслуживания, численности, управляемости.
Норма выработки определяет количество продукции в натуральном выражении , которое должно быть изготовлено за определенную единицу времени рабочим или бригадой рабочих. Определяется норма выработки по формуле :
Нв=Lсм,
------ (5.1)
Нвр
Где Lсм – длительность смены, мин;
Нвр – норма времени.
Норма времени определяет количество рабочего времени, которое необходимо затратить на выполнение единицы работы и находится по формуле :
Нвр = Тшт + Тпз
------- (5.2)
n
где Тшт – штучное время , мин.;
Тпз – подготовительно – заключительное время, мин.;
n - объем производственной партии, шт.
Для изучения . анализа затрат рабочего времени и установления норм труда рабочее время классифицируют на время работы и время перерывов. Рабочее время состоит из времени , связанного с выполнением производственного задания, и времени потерь.
Первое включает в себя подготовительно – заключительное время, оперативное время, время на обслуживание рабочего места, время на отдых и личные надобности.
Оперативное время определяется по формуле :
Топ = То + Твн * Ктв (5.3)
Где То – основное (технологическое )время, мин.;
Твн – вспомогательное неперекрываемое время, мин.;
Ктв – поправочный коеффициент на вспомогательное время.
Штучное время определяется по формуле :
Тшт = Топ (1 +(α1 +α2)/100) (5.4)
Где α1 – время на организационно-техническое обслуживание рабочего места в % от оперативного времени;
α2 – время на отдых и личные надобности , в % от оперативного времени.
Одним из важных факторов повышения производительности труда является совершенствование нормирования труда.
5.1 РАСЧЕТНОРМЫ ВРЕМЕНИ НА ТОКАРНО – РЕВОЛЬВЕРНУЮ ОПЕРАЦИЮ
Время на установку и снятие детали (Туст) в трехкулачковом патроне с выверкой по контуру необработаной поверхности составляет 1,3 минуты .
Определяем время , связанное с переходом (Тпер) :
А) время на проход :
1) на проход при зенкеровании на токарно – револьверном станке с горизонтальной осью вращения равно 0,15 мин., на 3 прохода – 0,45 мин.,;
2) на проход при точении фаски – 0,15 мин.;
3) на проход при подрезке торца – 0,22 мин.;
Б) время на приемы , свзянные с переходом , не вошедшие в комплекс :
1) изменить величину подачи – 0,06 мин.;
2) смазать деталь, инструмент – 0,05;
Итого время , связанное с переходом составляет :
0,45+0,15+0,22+0,06+0,05 = 0,93 (мин)
Время на контрольные измерения (Тконтр):
А) измерение штангенциркулем отверстия О50 после чернового зенкерования – 0,13 мин.;
Б) измерение пробкой отверстия О53 после получистового зенкерования – 0,13 мин.;
В) измерение пробкой отверстия О54,8 после чистового зенкерования – 0,13 мин.;
Г) измерение штангенциркулем размера 68 мм после точения фаски – 0,13 мин.;
Д) измерение скобой после подрезки торца – 0,09 мин.;
Е) периодичность контрольных измерений при обработке цилиндрических поверхностей инструментом, установленным на размер – 0,4;
Итого время на контрольные измерения :
Тконтр = (0,13+0,13+0,13+0,13+0,09) * 0,4 = 0,244 (мин)
Проверка : основное время равно 2,78 мин.,
2,78 >0.244
Время на контрольные измерения перекрываются основнгым временем.
Предварительное вспомогательное неперекрываемое время :
Т’ вн = Туст + Тпер, (5.5)
Твн = 1,3 + 0,93 =2,23 (мин)
Предварительное оперативное время (Т’оп):
Т‘оп = То + Т’ вн (5.6)
Т’оп = 2,78 + 2,23 = 5,01 (мин.).
Время на организационно – техническое обслуживание рабочего места (Торг-тех) при работе на токарно – револьверных станках с горизонтальной осью вращения револьверной головки составляет 5% от оперативного времени и равно
Торг-тех = 5,01*0,05 = 0,251 (мин.).
Время на отдых и личные надобности составляет 4% от оперативного времени и равно :
Тотл = 5,01*0,04 = 0,20 (мин)
Подготовительно заключительное время :
А) время на наладку станка , инструмента и приспособлений – 37 мин.;
Б) время на получение и сдачу инструмента и приспособлений – 10 мин.
Итого подготовительно – заключительное время (Т п-з) равно :
Тп-з = 37+10 = 47 (мин)
Предварительное штучное время (Т’шт):
Т’шт = Т‘оп +Торг-тех +Тотл, (5.7)
Т’шт = 5,01+0,251+0,2 = 5,461 (мин)
Предварительное время на партию в размере 100 деталей составит :
Т’парт = Т’шт *N + Тп-з,
---------------------, (5.8)
480
Тпарт = 5,461*100 + 47
--------------------- = 1,24 (смены).
480
Вводим поправочный коеффициент на вспомогательное время. При размере партии 100 штук он составляет 0,87 . На полученный коэффициент корректируем вспомогательное неперекрываемое время :
Твн = 2,23*0,87 = 1,94 (мин.)
Определяем окончательное оперативное время :
Топ = 2,78 + 1,94 = 4,72 (мин.).
Окончательное штучное время :
Тшт = 4,72 + (1+4+5) = 5,145 (мин)
-----
100
Норма времени на токарно револьверную операцию составляет :
Нвр = Тшт + Тп-з /N, (5.9)
Нвр = 5,145+47/100 = 5,615 (мин)
Время занятости рабочего на рабочем месте (Тзрм) равняется сумме вспомогательного перекрываемого и неперекрываемого времени и составляет :
Тзрм = 1,94 + 0,244 = 2,184 (мин)
Время занятости рабочего на рабочем месте (Тзрм) равняется сумме вспомогательного перекрываемого и неперекрываемого времени и составляет :
Тзрм = 1,94 + 0,244 = 2,184 (мин)
Коеффициент занятости рабочего определяем поформуле :
Кз = Тзрм / Топ, (5.10)
Кз = 2,184/4,72 = 0,463.
Норма выработки деталей за смену :
Нв = Lсм(480 минут)/Нвр, (5.11)
Нв = 480/5,615 = 85 (дет.)
Расценка за операцию определяется исходя из часовой тарифной ставки заработной платы по 3-му разряду работ и нормы времени на операцию :
Р = С” * Нвр ,
Р = 0,356*5,615 = 0,0333 (грн.) (5.12)
--------
60
Надбавка устанавливается в размере 20% от расценки и составляет 0,0067 грн. Расценка с учетом надбавки за операцию – 0,04 гривны.
Приведенный выше расчет нормы времени на токарно-револьверную операцию выполнен для существующего заводского техпроцесса изготовления детали. Расчет нормы времени по проектируемому техпроцессу выполняется аналогичным образом и представлен в приложении В.
В результате предложенного усовершенствования технологического процесса изготовления детали «втулка» (см.раздел 4 ) штучное время на операцию сократилось на 0,98 мин. Нормирование труда проводилось в соответствии с общемашиностроительными нормативами времени вспомогательного , на обслуживание рабочего места и подготовительно – заключительного для технического нормирования станочных работ в серийном производстве.
6.СОВЕРШЕНСТВОВАНИЕ БИЗНЕС ПЛАНИРОВАНИЯ НА ОАО “ХТЗ”
Как было отмечено в разделе 3 выбор стратегии деятельности предприятия подразумевает решение значительного комплекса вопросов. Эти вопросы, в основном, связаны с созданием планов по развитию предприятия в различных направлениях.
Важное место здесь уделяется бизнес – планированию в котором по сути рассматриваются все возможные пути развития и их варианты. Поэтому проектная часть посвящена разработке нового бизнес-плана предприятия ОАО «ХТЗ» на 2001 год
Данный раздел посвящен разработке мероприятий, направленных на совершенствование планирования путем разработки бизнес – плана.
Разработка нового бизнес-плана ставит перед собой прежде всего задачу привлечения к работе новых партнеров - немецкую фирму «Дойц АГ». Эта фирма уже сотрудничает с ХТЗ, но не в той мере, в какой это необходимо для улучшения производства. Харьковский завод хочет выйти на новый уровень деловых взаимоотношений, а для этого необходимы прежде всего инвестиции. Поэтому основная задача разработки бизнес-плана – это убедить и заинтересовать будущх партнеров сотрудничестве, что даст возможность увеличить объемы продукции : тракторов новой модели и модификаций.
В проекте будет разработан пример упрощенного бизнес-плана на 2001 год. Основой для его составления послужили отчетные данные за 2000 год. В бизнес-плане будет обоснована новая программа выпуска тракторов ХТЗ – 17021,оснащенных двигателем фирмы «Дойц АГ». Прочие условия по другим номенклатурным позициям остаются неизменными
Данный бизнес-план будет предназначен для предоставления иностранным партнерам, поэтому его структура должна соответствовать мировым требованиям. В связи с этим будут добавлены некоторые разделы, которые были опущены в бизнес-плане ХТЗ , но могут представлять интерес для немецкой стороны. В частности , в разделе «Характеристика продукции» будет сделан акцент именно на преимуществах нового трактора ХТЗ – 17021. Важную роль играет оценка конкурентоспособности тракторов ХТЗ по сравнению с немецкими аналогами , которая будет проведена в разделе «Характеристика конкурентов». Также в проектируемом бизнес-плане расчет необходимой численности работников будет выделен в отдельный раздел «Организационный план». В этом разделе также будет разработана подробная схема линий подчинения и ответственности между работниками на ключевых постах. Необходимость данной схемы обусловлена тем, что партнер должен знать , кто и в какой мере отвечает зареализацию запланированных мероприятий. Будет проведен расчет точки безубыточности аналитическим и графическим методами. Результаты практической реализации предлагаемого бизнес плана будут сведены в раздел «Финансовый план».
Дата добавления: 2019-07-15; просмотров: 375; Мы поможем в написании вашей работы! |
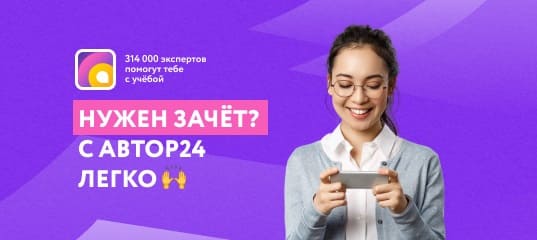
Мы поможем в написании ваших работ!