ЗАЩИТА МЕТАЛЛОВ И СПЛАВОВ ОТ КОРРОЗИИ
Противокоррозионные мероприятия необходимо планировать на стадии проектирования промышленного оборудования. В такие мероприятия входит правильный выбор материала и методов защиты его от коррозии, а также выбор рационального способа изготовления металлоконструкции в противокоррозионном отношении: чтобы не было мест для скопления влаги, было меньше щелей, зазоров, нежелательных контактов металлов и механических напряжений. При соединении узлов металлоконструкции следует отдавать предпочтение сварным соединениям перед клепаными и болтовыми.
Наиболее надежный метод борьбы с коррозией — изготовление аппаратов, машин и другого оборудования из коррозионно-стойких материалов. Однако его не всегда можно использовать в силу экономических, технических и других соображений, например ввиду того, что коррозионно-стойкие материалы имеют низкую пластичность и большую стоимость.
Коррозионно-стойкие стали устойчивы к воздействию агрессивных сред — электролитов. Наиболее широкое применение находят хромистые, хромоникелевые (10—28 % Ni), хромоникельмолибденовые, хромоникельтитановые и другие стали.
Хромистые стали легко пассивируются, поэтому устойчивость их к коррозии возрастает с ростом окислительных свойств агрессивной среды, однако при воздействии концентрированной азотной кислоты они разрушаются вследствие перепассивации. Стали, содержащие свыше 25 % хрома, устойчивы в «царской водке», в 30%-ном растворе хлорного железа. Но они разрушаются, особенно при нагревании, в средах, обладающих восстановительными свойствами (разбавленные растворы серной, соляной, муравьиной, винной, сернистой кислот), так как на поверхности металла не образуется защитных пленок. При комнатной температуре стали устойчивы к разбавленным растворам щелочей, но при нагревании и повышении концентрации они разрушаются. Им свойственна межкристаллитная коррозия, устраняющаяся дополнительным легированием сталей титаном и ниобием.
|
|
Хромоникелевые стали (07Х16Н6, 12Х18Н9Т, 08Х18Н10Т, 03Х18Н11 и др.) сочетают высокую пластичность и вязкость с достаточной прочностью и коррозионной стойкостью. Они устойчивы в азотной (до концентрации 80% и при температуре до 70°С), ортофосфорной (до концентрации 60 % и при температуре 100°С), серной, органических кислотах, в растворах нитратов, сульфатов, в сухом хлоре и газах, содержащих SO2, N203, Н2S, СО2, но разрушаются под действием соляной и концентрированной азотной кислот.
Коррозионную стойкость хромоникелевых сталей в неокислительных средах повышают введением в состав стали молибдена, титана, меди, кремния и др.
|
|
Хромоникельмолибденовые стали (10Х17Н13М2Т, 10Х17Н13М3Т, 03Х16Н15МЗ и др.) прочны, пластичны, имеют высокую ударную вязкость, хорошо свариваются, протягиваются, штампуются. Присутствие молибдена в стали способствует пассивации стали как в окислительных, так и в восстановительных, средах, и в средах, содержащих ионы хлора. Такое сочетание свойств делает незаменимыми эти стали для изготовления аппаратуры, работающей в сильно агрессивных средах, например в 10—15 %-ных нагретых растворах серной, сернистой, ортофосфорной кислот, в кипящих растворах органических кислот и т. д.
Еще более высокой коррозионной стойкостью обладают стали сложной системы Fе — С — Сr — Ni— . Мо — Си. Их широко применяют в химической, целлюлозно-бумажной, пищевой промышленности.
СНИЖЕНИЕ АГРЕССИВНОСТИ КОРРОЗИОННОЙ СРЕДЫ
Этот способ защиты целесообразно применять только при ограниченном объеме коррозионной среды. Защита металла от коррозии достигается либо снижением концентрации агрессивного компонента, либо введением в коррозионную среду веществ, снижающих скорость коррозии.
Кислород и другие окислители, присутствующие в агрессивной среде, резко увеличивают скорость коррозии. Поэтому при коррозии, идущей с восстановлением кислорода, агрессивная среда подвергается обескислороживанию, или деаэрации. Это достигается кипячением или пропусканием через среду инертных газов, обработкой среды химическими реагентами, связывающими окислители. Такой способ защиты является громоздким и трудоемким, он используется обычно для защиты теплосилового оборудования.
|
|
В кислых средах уменьшение концентрации ионов водорода достигают введением негашеной извести или щелочи:
Наиболее широкое применение находит способ защиты от коррозии путем введения в состав агрессивной среды веществ, снижающих или полностью исключающих коррозионный процесс. Такой способ защиты называется ингибированием, а вводимые в среду вещества — ингибиторами.
Концентрация вводимых веществ для снижения1 скорости коррозии при ингибировании зависит от состава и свойств агрессивной среды, ее температуры и других факторов. Действие ингибитора оценивается степенью защиты Z (в %) и коэффициентом торможения (ингибиторный эффект) γ и определяется по формулам
где К1и К2 — скорости коррозии в среде без ингибитора и с ним соответственно, г/(м2·ч).
Ингибиторы, адсорбируясь на поверхности корродирующего металла, тормозят протекание анодного и катодного процессов электрохимической коррозии, или, образуя экранирующую пленку, изолируют металл от электролита, или оказывают смешанное замедляющее действие. Они подразделяются на катодные, анодные и катодно-анодные.
|
|
Катодные ингибиторы — вещества, тормозящие отдельные стадии катодного процесса. При коррозии в нейтральном растворе, протекающей с восстановлением кислорода, такой ингибитор, например сульфит натрия, должен снижать содержание кислорода в агрессивной среде. К катодным ингибиторам относятся и вещества, сокращающие поверхность катодных участков. Так, при введении в щелочную среду хлорида или сульфата цинка скорость коррозии резко снижается из-за образования нерастворимого гидроксида цинка, который, осаждаясь на стенках аппарата, препятствует соприкосновению раствора с металлом. Кроме того, катодные ингибиторы способны повышать перенапряжение водорода [Аs2О3, Bi2(S04)3]. Такие ингибиторы применяют в процессах коррозии, идущих с выделением водорода.
Анодные ингибиторы — вещества, способные образовывать на поверхности металла тонкие (~0,01 мкм), чаще всего оксидные, пленки. Пленки тормозят переход ионов металла в раствор. К анодным ингибиторам относятся хроматы, бихроматы, нитриты, фосфаты и др.
Катодно-анодные ингибиторы, например КI, КВr в растворах кислот, тормозят в равной степени анодный и катодный процессы за счет образования на поверхности металла хемосорбционного слоя.
Кроме неорганических ингибиторов, рассмотренных выше, применяют и органические. К ним относятся органические коллоиды, поверхностно-активные и другие вещества.
Органические ингибиторы снижают скорость коррозии аппаратуры, соприкасающейся с кислыми средами. Адсорбируясь на поверхности металла, органические ингибиторы тормозят разряд ионов водорода, что уменьшает разрушение металла. Органические ингибиторы адсорбируются только поверхностью металла, продукты коррозии их не адсорбируют. Поэтому их применяют, когда надо очистить изделия из металлов и сплавов от оксидов, ржавчины, окалины, которые в присутствии органических ингибиторов легко растворяются при кислотном травлении без заметного разрушения металла. Так, органические ингибиторы широко используют при очистке котельных установок от накипи. Накипь со стенок аппарата растворяют в хлористоводородной кислоте в присутствии ингибитора:
.
Кроме того, органические ингибиторы применяют при травлении железных труб, для защиты от коррозии холодильных установок, электролизеров, цистерн, резервуаров и т. д.
Для защиты металлов и сплавов на воздухе применяются ингибиторы атмосферной коррозии (контактные и летучие).
Контактные ингибиторы—нитрит и бензоат натрия предохраняют черные металлы, хром, никель,, цинк, хромат гексаметилендиамина — черные и цветные металлы. Такие ингибиторы используются при консервации деталей и узлов оборудования и механизмов. Ингибиторы наносят на детали, погружая детали в растворы, или вводят ингибиторы в масла и смазки.
Летучие ингибиторы — нитрит дициклогексиламина, карбонат циклогексиламина и другие защищают от коррозии изделия из чугуна, стали, никеля, хрома, алюминия, фосфатированные и оксидированные металлы. Их можно использовать в виде порошка или наносить на упаковочную бумагу, картон, ткань из спиртоводного раствора; применяют для консервации инструмента и оборудования из черных металлов.
ЗАЩИТНЫЕ ПОКРЫТИЯ
Защитное покрытие должно быть сплошным, равномерно распределенным по всей поверхности, непроницаемым для окружающей среды, иметь высокую адгезию (прочность сцепления) к металлу, быть твердым и износостойким. Коэффициент теплового расширения покрытия должен быть близким к коэффициенту теплового расширения металла защищаемого изделия.
Применяемые в технике покрытия подразделяются на металлические и неметаллические.
Металлические покрытия
Металлические покрытия наносят на изделия погружением в расплавленный металл (горячий метод), термомеханическим методом (плакирование), распылением (металлизация), диффузионным и гальваническим.
В зависимости от применяемого металла покрытия бывают катодные и анодные. Если изделие покрывается металлом, имеющим более положительный потенциал, чем потенциал защищаемого металла, то такое покрытие называют катодным; например, покрытие изделия из стали оловом, медью. При нарушении целостности покрытия коррозия резко возрастает, так как металл изделия становится анодом по отношению к металлу покрытия. Если изделие покрывается металлом, имеющим более отрицательный потенциал, чем потенциал металла защищаемого изделия, то такое покрытие называют анодным; например, покрытие стали цинком. Анодное покрытие защищает покрываемый металл при нарушении его целостности, так как металл изделия является катодом по отношению к металлу покрытия. Таким образом, катодное покрытие должно быть сплошным и непроницаемым для агрессивной среды, тогда как к анодному покрытию по сплошности предъявляются менее высокие требования.
Горячий метод
Металлические покрытия горячим методом наносят на изделие или заготовку путем их погружения на несколько секунд в ванну с расплавленным металлом. Этим способом на изделия наносят цинк (tпл = 419°С), олово (tпл = 232°С), свинец (tпл = = 327°С), алюминий (tпл = 658°C), т. е. металлы, имеющие низкую температуру плавления. Перед нанесением на изделие покрытия его обрабатывают флюсом, например, состоящим из 55,4 % хлорида аммония, 6 % глицерина, 38,4 % хлорида цинка. Флюс защищает расплав от окисления и, кроме того, удаляет с поверхности оксидные и другие пленки, что улучшает адгезию металла к металлу покрытия.
Горячим методом наносят покрытия на готовые изделия, в основном из стали и чугуна, и на полуфабрикаты из них (листы, трубы, проволоку). Толщина покрытия зависит от назначения изделия, природы металла, температуры, времени выдержки изделия в расплаве и составляет от нескольких микрометров до миллиметров.
Горячий метод нанесения покрытий не обеспечивает получения равномерных по толщине покрытий, поэтому не применяется для защиты изделий с узкими отверстиями, резьбой и изделий больших размеров. При нанесении покрытий большой толщины велик расход цветных металлов.
Плакирование
Термомеханический способ (плакирование) широка используют для защиты от коррозии основного металла или сплава другим металлом (сплавом),устойчивым к воздействию внешней среды. Соединение металлов осуществляют в основном горячей прокаткой, при которой образуется прочное соединение двух металлов за счет взаимной диффузии металлов. Плакированием получают би- и многослойные металлы.
Для плакирования применяют металлы и сплавы, обладающие хорошей свариваемостью: углеродистые, кислотостойкие стали, дюралюмины, сплавы меди и др. В качестве защитного покрытия для плакирования широко используются алюминий, тантал, молибден, титан, никель, нержавеющие стали и др. Толщина плакирующего слоя колеблется от 3 до 60 % толщины защищаемого металла.
Термомеханическим способом защищают от коррозии автоклавы, фасонные изделия, листы, сосуды и др. Плакированные изделия находят применение в химической, нефтеперерабатывающей, пищевой и других отраслях промышленности.
Металлизация распылением
Металлизация—процесс нанесения расплавленного металла на поверхность изделия сжатым воздухом или инертным газом. Покрытие на изделии образуется в результате вклинивания и прилипания частиц металла в поры и неровности поверхности. Прочность сцепления покрытия с защищаемым изделием зависит от размера частиц, скорости их полета, деформации при ударе о поверхность. При металлизации получаемое покрытие имеет чешуйчатую структуру и высокую пористость, которую уменьшают увеличением толщины покрытия, шлифованием, полированием или дополнительным нанесением лаков и красок.
Металлизацию в основном применяют для защиты от коррозии крупногабаритных изделий и сооружений, например железнодорожных мостов, газгольдеров, свай, корабельных и морских труб, вулканизационных котлов и мелких изделий, к которым другие методы неприменимы.
Изделия, подвергающиеся воздействию атмосферы или находящиеся в почве, покрываются цинком и алюминием толщиной от 0,05 до 4 мм, а соприкасающиеся с водяным паром, морской атмосферой — .алюминием толщиной до 0,3 мм; контактирующие с растворами серной кислоты и ее солей — свинцом.
При металлизации расходуется большое количество металла на угар и распыление, покрытие имеет пористую структуру, неравномерную толщину, низкую адгезию к металлу.
Диффузионная металлизация
.Диффузионная металлизация — процесс насыщения поверхности изделий при высокой температуре устойчивыми к агрессивной среде элементами: алюминием, хромом, кремнием, бором. Ее проводят при совместном нагревании изделия и элемента покрытия, который может использоваться как в виде порошка с добавкой хлоридов, так и в виде паров его летучих соединений. При таком совместном нагревании выделяющийся элемент в атомном состоянии диффундирует в поверхностный слой изделия, что обеспечивает хорошее сцепление с защищаемым металлом. Образовавшийся поверхностный слой приобретает устойчивость к газовой коррозии, повышенную твердость и износостойкость.
Алитирование—процесс введения алюминия в поверхность изделий из стали, чугуна, меди. Наиболее часто алитирование проводят в твердой среде нагреванием изделий с порошкообразной смесью, состоящей из алюминия (или ферроалюминия)—45%, оксида алюминия — 53% и хлорида аммония — 2%.
Алитированию подвергают прокат, поковки, муфты, котельную арматуру и другие изделия из стали и чугуна. Алитированные изделия устойчивы в газах, содержащих сернистые и другие соединения. Они могут использоваться вместо жаростойких сталей.
Хромирование — процесс насыщения поверхностных слоев изделий из стали или чугуна хромом. Он осуществляется при 1000—1150°С в течение 20— 25 ч в жидкой, газообразной и твердой (порошках) средах. Наиболее часто используется порошковый метод, при котором применяют порошки, состоящие из хрома или феррохрома и хлорида аммония.
Поверхностный слой изделий после хромирования устойчив ко многим коррозионным средам, так как выделившийся хром с компонентами стали образует твердые растворы и хромистые соединения, а с углеродом и железом — карбидный слой.
Хромированные заготовки подвергаются изгибанию, волочению, штамповке, обработке на прессах, прокатке без нарушения защитных свойств. Полученные изделия широко используются в химической, нефтехимической и других отраслях промышленности, особенно в тех случаях, когда изделия соприкасаются с окислительными средами.
Силицирование — процесс насыщения поверхности изделий из стали или чугуна кремнием. Проводят силицирование с применением порошков (смесь ферросилиция, шамота и хлорида аммония) или газообразных соединений кремния (SiF4, SiCl4) при температуре 1100—1200 °С в течение 10—24 ч. В зависимости от температуры и времени силицирования глубина проникновения выделяющегося кремния (4Fе + 3SiС14 → 3Si + 4FеС13) различна и составляет от 0,8 до 1,0 мм.
Поверхность силицированных изделий тверда, износостойка. Такие изделия устойчивы к воздействию растворов азотной, серной кислот и растворам их солей, к атмосферной коррозии. Силицированию подвергают стальные трубы, детали насосов для перекачки кислот и солей, арматуру, детали тракторов и автомобилей.
Неметаллические покрытия
Из всех покрытий, применяемых для защиты изделий от коррозии, наиболее распространены неметаллические. К ним относятся эмали, лаки и краски, покрытия резиной, пластическими массами, смазкой и др. Особенно широко применяют лакокрасочные покрытия, ассортимент которых превышает 1000 наименований.
Дата добавления: 2019-07-15; просмотров: 324; Мы поможем в написании вашей работы! |
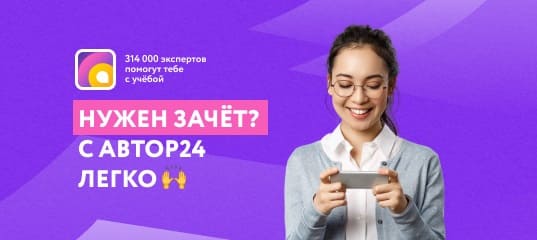
Мы поможем в написании ваших работ!