ОСНОВНЫЕ ВИДЫ КОРРОЗИИ И КОРРОЗИОННЫХ РАЗРУШЕНИЙ
АТМОСФЕРНАЯ КОРРОЗИЯ
Атмосферной называется коррозия металлов в воздухе при температуре окружающей среды. Она является одним из наиболее распространенных видов коррозионного разрушения металлов. Приблизительно 80 % всех металлических конструкций эксплуатируется в атмосферных условиях.
Различают несколько видов атмосферной коррозии.
Сухая атмосферная коррозия развивается при относительной влажности ниже 60 %. Изменение состояния поверхности происходит медленно. При появлении тончайшей пленки влаги сухая атмосферная коррозия переходит во влажную, а при попадании капель — в мокрую атмосферную коррозию.
Влажная атмосферная коррозия возникает при капиллярной, адсорбционной или химической конденсации при условиях, когда относительная влажность ниже 100 %.
Капиллярная конденсация зависит от микрорельефа поверхности и увеличивается с ростом пористости и шероховатости поверхности.
Адсорбционная конденсация заключается в образовании тончайшего слоя молекул воды, связанных адсорбционными силами. При относительной влажности ниже 100 % может конденсироваться слой влаги в несколько десятков молекулярных слоев.
Химическая конденсация обусловлена гигроскопичностью образующихся продуктов коррозии и других химических соединений, имеющихся на поверхности металла.
Мокрая атмосферная коррозия наблюдается при непосредственном воздействии дождя, снега, тумана, а также при капельной конденсации влаги на поверхности металлов при относительной влажности 100 %.
|
|
Механизм атмосферной коррозии зависит от толщины слоя электролита на поверхности металла. При толщине пленки электролита менее 10 нм наблюдается сухая коррозия, протекающая по химическому механизму.
При влажной коррозии толщина пленки составляет примерно до 0,1 мкм и при мокрой коррозии — от 0,1 до 1 мкм, такая коррозия протекает по электрохимическому механизму с катодной реакцией восстановления кислорода.
Для большинства металлов увеличение скорости коррозии в зависимости от относительной влажности происходит скачкообразно, причем для каждого металла — при разной влажности воздуха. Это значение относительной влажности называется критической влажностью; для меди она составляет 80, для железа — 70 %.
Опасность атмосферной коррозии возрастает с продолжительностью увлажнения поверхности металла, которая различна в разных климатических районах: например, для Прибалтики она составляет 3250 ч/год (наиболее опасный район), а для Средней Азии 750 ч/год (наименее опасный район). Скорость коррозии зависит также от коррозионной агрессивности атмосферы, характеризующейся температурой, влажностью и загрязнениями коррозионно-ак-тивными агентами—сернистым газом, хлоридами, аммиаком, оксидами азота. В зависимости от количественных характеристик коррозионной агрессивности условия эксплуатации изделий разделяют на 8 групп (ГОСТ 9.303—84).
|
|
Снижение уровня загрязнений воздуха промышленными выбросами химических, металлургических и других производств одновременно с уменьшением коррозионной агрессивности атмосферы имеет огромное значение для охраны окружающей среды и сохранения здоровья человека.
Для защиты металлов от атмосферной коррозии применяют защитные неметаллические (смазки, лакокрасочные покрытия) и металлические (цинковые, многослойные) покрытия, ингибиторы коррозии; уменьшают загрязненность воздуха.
ПОДЗЕМНАЯ КОРРОЗИЯ
Подземная коррозия металлов является разновидностью электрохимической коррозии, протекающей в почвах и грунтах. Подземной коррозии подвергаются нефтяные, газовые и водные трубопроводы, а также сваи, кабели и другие подземные сооружения. Коррозионная активность почвы и грунта определяется их пористостью, влажностью, солевым составом и кислотностью, присутствием микроорганизмов.
|
|
Наиболее характерным катодным процессом в случае подземной коррозии является восстановление кислорода, хотя в почвах, имеющих сильнокислую реакцию (рН ниже 3), может происходить выделение водорода. Подземные трубопроводы могут корродировать также за счет возникновения коррозионных элементов, являющихся следствием различной аэрации или неодинакового состава почвы на соседних участках. Анодные и катодные участки могут быть значительно удалены друг от друга. Грунтовая коррозия очень опасна, так как она часто проявляется в виде глубоких раковин и точечных изъязвлений (питтингов). Защита от почвенной коррозии осуществляется путем изоляции металлов нефтебитумными композициями, а также липкой полиэтиленовой или полихлорвиниловой лентой в сочетании с электрохимическими методами защиты.
Электрокоррозия — электрохимическая коррозия под действием блуждающих токов, возникающих вследствие недостаточной изоляции рельсов электротранспорта от земли и утечки постоянного тока. Металлические магистрали (трубопроводы, кабели), находящиеся в почве, становятся частью параллельной электрической цепи, причем место входа тока становится катодной зоной (происходит подщелачивание почвы и выделение водорода), а участок выхода — анодной зоной (происходит усиленное растворение металла). Борьбу с этим видом коррозии проводят путем применения комплекса защитных мер: осуществляют дренаж, т. е. отвод тока от анодной зоны трубопровода с помощью металлического проводника обратно в рельс; применяют изоляцию опасных мест металлоконструкций; увеличивают сопротивление на стыках.
|
|
МОРСКАЯ КОРРОЗИЯ
Коррозии в морской воде подвергаются металлические части морских судов, металлические сооружения портов, нефтепромыслов и другие металлоконструкции. Морская коррозия протекает по электрохимическому механизму с катодной реакцией восстановления кислорода. Присутствие хлорид-иона препятствует пассивации металла, а высокая электропроводность морской воды создает условия, благоприятные для протекания контактной коррозии. В зоне периодического смачивания поверхности металла возникает усиленная коррозия, обусловленная облегчением доступа кислорода (коррозия по ватерлинии).
Защиту от морской коррозии осуществляют с помощью лакокрасочных и металлических (например, цинковых толщиной 150—200 мкм) покрытий. Широко используют электрохимические методы защиты.
БИОЛОГИЧЕСКАЯ КОРРОЗИЯ
Биокоррозия вызывается жизнедеятельностью различных микроорганизмов, использующих металлы как питательную среду или выделяющих продукты, разрушающие металлы. Наиболее опасны анаэробные (развивающиеся при отсутствии кислорода) сульфат-редуцирующие бактерии, находящиеся в илистых и болотных грунтах. Бактерии восстанавливают ионы сульфатов в ионы сульфидов: SО42- + 8Н+ →S2- + 4Н2О, ускоряющие коррозию металлов.
Жизнедеятельность аэробных бактерий протекает только при наличии кислорода. Бактерии окисляют серу до серной кислоты, концентрация которой в отдельных местах может достигать 10 %.
Железобактерии поглощают железо в ионном состоянии и выделяют его в виде нерастворимых соединений при рН = 4 ÷ 10. Поскольку нерастворимые продукты распределяются по поверхности металла неравномерно, возникает электрохимическая гетерогенность поверхности, усиливающая коррозию.
ПИТТИНГОВАЯ КОРРОЗИЯ
Питтинговая (точечная) коррозия—коррозия металла в виде отдельных точечных поражений, когда остальная поверхность металла находится в пассивном состоянии. Питтинговой коррозии подвержены углеродистые и нержавеющие стали, сплавы на основе алюминия, никеля, титана и других легкопассивирую-щихся металлов и сплавов в морской воде, рассолах холодильных машин, смесях соляной и азотной кислот и т. д.
Питтинговая коррозия возникает, если созданы условия перехода металла в пассивное состояние: например, в растворе есть окислители — хроматы, нитраты и т. д. при одновременном присутствии в коррозионной среде ионов-активаторов (как правило, С1-, Вr-, I-) в концентрации, равной критической или выше. Критическая концентрация галогенид-иона зависит от природы металла, наличия других анионов в растворе и некоторых иных факторов. Появление питтинга связано с вытеснением адсорбированного кислорода галогенид-ионом или с разрушением оксидной пленки под действием галогенид-иона на участках поверхности, где связь металл — кислород ослаблена. Этому благоприятствует наличие неметаллических примесей, особенно сульфида марганца в сталях; некоторые режимы термообработки сплавов. Чтобы произошло взаимодействие поверхности металла с ионом галогенида, нужно, чтобы потенциал металла достиг потенциала питтингообразования. Некоторые кислородсодержащие анионы (сульфат, хромат, нитрат) предотвращают питтинговую коррозию, так как они способны вытеснять С1- с поверхности металла.
Для защиты металлов от питтинговой коррозии применяют электрохимические методы защиты, ингибиторы коррозии, рационально легированные сплавы (хромоникелевые стали, легированные молибденом, кремнием). Наибольшую коррозионную стойкость в средах с большим содержанием иона хлора имеет титан.
МЕЖКРИСТАЛЛИТНАЯ КОРРОЗИЯ
Межкристаллитная коррозия распространяется по границам кристаллитов (зерен) металла. Этому виду коррозии подвержены некоторые сплавы (хромистые и хромоникелевые стали, сплавы на основе алюминия, никеля), у которых при определенных режимах термообработки, при старении или под напряжением изменяется химический состав на границе зерна по сравнению с составом в объеме зерна. Под действием коррозионной среды одна из структур, расположенная по границе зерна в виде непрерывной цепочки, растворяется при потенциалах активного состояния; в этом случае анодная реакция локализуется на границе зерна, а само зерно металла (объем) находится в пассивном состоянии и разрушается мало.
Причиной межкристаллитной коррозии нержавеющих сталей считают выпадение по границе зерна карбидов хрома Сr23С6 или (Сr, Fе)23С6 при нагревании в интервале температур 450—850 °С. Так как при этих температурах скорость диффузии углерода выше, чем хрома, в образовании карбидов по границе зерна принимает участие весь углерод сплава, а хром—только находящийся на границе зерна. Это приводит к обеднению границы зерна хромом и уменьшению способности переходить в пассивное состояние. Поэтому в коррозионной среде граница зерна растворяется.
Для устранения межкристаллитной коррозии нержавеющих сталей нужно предотвратить выпадение карбидов хрома по границе зерен. Это достигается снижением содержания углерода в стали; легированием стали карбидообразующими элементами (титан, тантал, ниобий), образующими более труднорастворимые карбиды, чем карбиды хрома;проведением термообработки при режимах, препятствующих образованию карбидов хрома.
КОНТАКТНАЯ КОРРОЗИЯ
Контактная коррозия — электрохимическая коррозия, вызванная контактом металлов, имеющих разные стационарные потенциалы в данном электролите. При этом коррозия металла с более отрицательным потенциалом обычно усиливается, а коррозия металла с более положительным потенциалом замедляется или полностью прекращается. Контактная коррозия часто наблюдается в морской воде, имеющей хорошую электропроводность. Она может протекать и в атмосферных условиях — максимальная в месте непосредственного контакта разнородных металлов. Этот вид коррозии возникает также, когда металл имеет на поверхности пористое металлическое покрытие, отличающееся по своему потенциалу от потенциала металла основы.
В зависимости от природы коррозионной среды металлы принято подразделять на группы, в пределах которых возможны контакты металлов друг с другом, поскольку они имеют близкие значения стационарных потенциалов. На основании опыта эксплуатации металлов и сплавов в естественных условиях и лабораторных испытаний в коррозионных средах (морская вода, хлорид натрия) металлы подразделяют на следующие группы:
I — магний, цинк; II — кадмий, алюминий и его сплавы; III — железо, свинец, олово; IV — никель, нержавеющие стали, медь, латуни, бронзы, меднони-келевые сплавы; V — серебро; VI—золото, платина. Защита металлов от контактной коррозии осуществляется правильным подбором контактирующих металлов, использованием изолирующих прокладок, применением электрохимических методов защиты, введением ингибиторов коррозии.
Дата добавления: 2019-07-15; просмотров: 226; Мы поможем в написании вашей работы! |
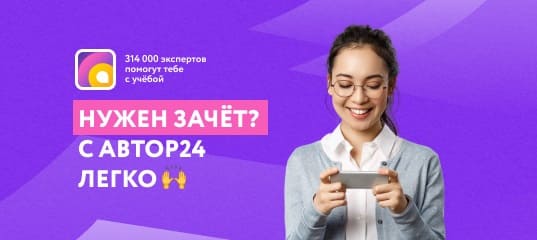
Мы поможем в написании ваших работ!