Анализ и оптимизация базового технологического процесса
Базовый технологический процесс основан на обработке давлением, что не подходит в рамках данной дипломной работы. При этом общий такт выпуска составлял: τс=7,2 мин/шт.
Изм. |
Лист |
№ докум. |
Подпись |
Дата |
Лист |
88 |
|
Выбор типа заготовки
Метод выполнения заготовок деталей машин определяется назначением конструкции детали, материалом, техническими требованиями, масштабом и серийностью выпуска, а также экономичностью изготовления. Выбрать заготовку — значит установить способ ее получения, наметить припуски на обработку каждой поверхности, рассчитать размеры и указать допуски на неточность изготовления. От правильного выбора заготовки зависит трудоемкость и себестоимость обработки.
Для данной детали можно использовать следующие методы получения заготовок: горячая объемная штамповка на молотах и прессах, горячая объемная штамповка на горизонтально-ковочных машинах, а также получение заготовки из проката.
Наиболее рациональными методами получения заготовки из вышеперечисленных для данной детали, с учетом материала, массы, конфигурации, габаритов детали и годовой программы выпуска, является метод получения заготовок из проката, так как он не требует изготовления штампов, пресс-форм и т.п.
Расчет припусков
Припуск – слой материала, удаляемый с поверхности заготовки в целях достижения заданных свойств обрабатываемой поверхности детали.
|
|
Расчетной величиной является минимальный припуск на обработку,
Изм. |
Лист |
№ докум. |
Подпись |
Дата |
Лист |
89 |
|
Промежуточные размеры, определяющие положение обрабатываемой поверхности, и размеры заготовки рассчитывают с использованием минимального припуска.
Исходные данные. Деталь «Втулка». Технические требования – диаметр 70h8, шероховатость Ra = 1,25 мкм. Материал детали – Л 68. Общая длина детали – 100 мм. Длина обрабатываемой поверхности – 72 мм. Метод получения заготовки – прокат. Обработка производится в патроне на токарном станке 16К20. Требуется определить межоперационный и общий припуски и диаметральный размер заданной поверхности заготовки.
В графу 2 таблицы 4 записывают элементарную поверхность детали и технологические переходы в порядке последовательности их выполнения.
Заполняем графы 3, 4 и 9 по всем технологическим переходам. Данные для заполнения граф 3, 4 и 9 взяты из таблиц. [5, П 1.11 и П 1.18 ]
|
|
Суммарное значение пространственных погрешностей при отработке наружной поверхности:
(3.2)
где rоп – общее отклонение оси от прямолинейности;
rк – кривизна профиля сортового проката;
rк = 3 мкм/мм;
Lз – длина заготовки.
мкм.
Изм. |
Лист |
№ докум. |
Подпись |
Дата |
Лист |
90 |
|

№ п/п | Маршрут обработки поверхности | Элементы припуска, мкм | Расчетный припуск, мкм | Расчетный размер, мм | Допуск по переходам, мкм | Предельные размеры, мм | Предельные припуски, мм | |||||
Rzi-1 | Ti-1 | ρi-1 | εi | max | min | max | min | |||||
1 | 2 | 3 | 4 | 5 | 6 | 7 | 8 | 9 | 10 | 11 | 12 | 13 |
1 | Наружная пов. ![]() | |||||||||||
Прокат | 200 | 300 | 150 | - | - | 71,579 | 460 | 72,04 | 71,6 | - | - | |
а | Точение черновое | 63 | 60 | 9 | 200 | 1500 | 70,079 | 190 | 70,269 | 70,079 | 1,771 | 1,33 |
б | Точение чистовое | 32 | 30 | 0,45 | 0 | 125 | 69,954 | 46 | 70 | 69,954 | 0,269 | 0,079 |
Находим коэффициенты уточнения для:
- чернового точения Ку = 0,06
- чистового точения Ку = 0,05
|
|
Ρ = ρо · Ку (3.3)
Изм. |
Лист |
№ докум. |
Подпись |
Дата |
Лист |
91 |
|
ρ2 = 9 · 0,05 = 0,45 мкм.
Данные заносим в графу 5.
Погрешность установки заготовок (графа 6) в трехкулачковом само центрирующем патроне при черновом обтачивании εу1 =200мкм; при чистовом обтачивании без переустановки – εу2 = 0 мкм.
На переходе шлифования обработка производится в центрах, т.е. εу3 = 0мкм.
Расчет минимального припуска (графа 7) при обработке наружной поверхности проката в патроне производится по формуле:
- при черновом точении:
, (3.4)
мкм
- при чистовом точении:
мкм.
В графу 11 записываются размеры по всем технологическим переходам, округляя их увеличением до того же знака десятичной дроби, с каким задан допуск на размер для каждого перехода.
Наибольшие предельные размеры (графа 10) определяются путем прибавления допуска к округленному минимальному предельному размеру.
Предельные размеры припусков Zi max (графа 12) определяются как разность предельных максимальных размеров и Zi min (графа 13) – как разность предельных минимальных размеров предшествующего и выполняемого переходов.
Для определения общих припусков Z0 min и Z0 max суммируются соответствующие промежуточные припуски на обработку.
|
|
Дата добавления: 2019-07-15; просмотров: 274; Мы поможем в написании вашей работы! |
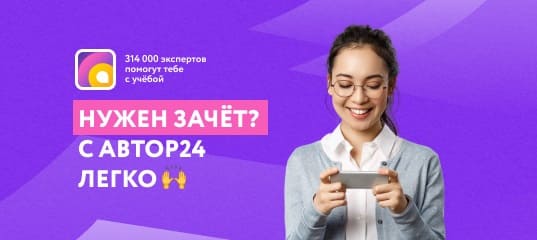
Мы поможем в написании ваших работ!