Жаропрочные и жаростойкие стали.
Жаростойкие и жаропрочные стали и сплавы используются во многих отраслях промышленности. Достижения в металловедении жаропрочных сталей и сплавов в значительной степени определяют уровень развития энергомашиностроения, авиационной и ракетно-космической техники (табл. 2.6).
Жаропрочностью называется способность сталей и сплавов выдерживать механические нагрузки при высоких температурах в течение определенного времени. При температурах до 600°C обычно применяют термин теплоустойчивость.
Жаростойкость характеризует сопротивление металлов и сплавов газовой коррозии при высоких температурах. Стали и сплавы, предназначенные для работы при повышенных и высоких температурах, должны, следовательно, обладать не только требуемой жаропрочностью, но и иметь достаточное сопротивление химическому воздействию газовой среды (жаростойкость) в течение заданного ресурса эксплуатации.
Стали и сплавы, предназначенные для работы при повышенных и высоких температурах, подразделяют на группы:
- теплоустойчивые стали, работающие в нагруженном состоянии при температурах до 600°C в течение длительного времени;
- жаропрочные стали и сплавы, работающие в нагруженном состоянии при высоких температурах в течение определенного времени и обладающие при этом достаточной жаростойкостью;
- жаростойкие стали и сплавы, работающие в ненагруженном или слабонагруженном состоянии при температурах выше 550°C и обладающие стойкостью против химического разрушения поверхности в газовых средах.
К жаропрочным относятся сплавы аустенитного класса на хромоникелевой и хромоникельмарганцевой основах с различным дополнительным легированием. По преимущественному типу упрочнения стали подразделяют на три подгруппы:
|
|
- гомогенные (однофазные) аустенитные стали, жаропрочность которых обеспечивается в основном легированностью твердого раствора;
- стали с карбидным упрочнением;
- стали с интерметаллидным упрочнением.
Жаропрочные сплавы разделены по металлу основы: сплавы на основе никеля и кобальта. Эти сплавы чаще всего подразделяют и по способу производства: на деформируемые и литые.
Жаропрочные сплавы работают при различных схемах нагружения: статических растягивающих, изгибающих или скручивающих нагрузках, динамических переменных нагрузках различной частоты и амплитуды, термических нагрузках вследствие изменений температуры, динамическом воздействии скоростных газовых потоков на поверхность. Вследствие этого применяются разнообразные виды испытания на жаропрочность и жаростойкость: испытания на ползучесть и длительную прочность при статическом нагружении, испытания на высокотемпературную и термическую усталость, испытания на газовую коррозию в различных средах, испытания в скоростных газовых потоках.
|
|
Основной характеристикой, определяющей работоспособность жаропрочных сталей и сплавов, является жаропрочность (напряжение, вызывающее заданную деформации, не приводящую к разрушению.). Если оговариваются напряжение и время, такая характеристика называется пределом длительной прочности; если оговаривается напряжение, время и деформация - это предел ползучести.
Температурная шкала эксплуатации сталей и сплавов делится на три уровня. Первый уровень - от 20 до 400°С. Конструкции из сталей и высоколегированных сплавов рассчитываются по номинальным допускаемым напряжениям, близким к пределу текучести. Второй уровень - от 400 до 600°С. Конструкции в основном работают в условиях ползучести. Стали для работы при этих температурах относятся к категории теплоустойчивых (High-Temperature Steels), температурный предел их работы - 550-600°С. Третий уровень - выше 600°С. Это группа жаропрочных сталей и сплавов.
Условия нагружения могут быть самыми различными. Крепежные соединения (болты, гайки, резьбы) и пружины, будучи нагруженными, в процессе службы не меняют своих размеров, но с течением времени при высоких температурах имеет место самопроизвольное снижение уровня первоначально заданных механических напряжений (релаксация напряжений). Соответственно, стали и сплавы, сопротивляющиеся спаду напряжений, относятся к релаксационностойким. В отдельных случаях такие стали нормируются специальным стандартом, например, DIN 17240. Примером жаропрочной стали с сопротивлением релаксации является сталь 18Х12ВМБФР.
|
|
Среди жаропрочных сталей представлены стали всех уровней легирования и основных структурных классов: перлитные, мартенситные, мартенсито-ферритные (феррита не менее 10%), ферритные, аустенитно-мартенситные. Перлитные стали относятся к категории низколегированных. К высоколегированным относятся стали, содержащие не менее 10% (по массе) легирующих элементов, если считать по верхнему пределу. К сплавам на железо-никель-хромовой основе относятся сплавы, в которых суммарное содержание никеля и железа составляет 65 % в массе. Надо отметить, что деление на стали и железные сплавы носит условный характер и в зарубежных стандартах они отнесены к аустенитным сталям.
К сплавам на основе никеля или кобальта относятся такие композиции элементов, в которых содержание никеля или кобальта порознь или в сумме составляет 55 % (по массе). Для России характерна разработка сталей и сплавов, содержащих минимальное количество никеля, кобальта, молибдена, тантала, ниобия, но зато широко использовались марганец, хром и, в некоторый период, вольфрам. Для зарубежных сталей и сплавов, напротив, характерно широкое использование кобальта, молибдена, ниобия и ванадия. В силу этих причин структурные классы являются базой для сравнения различных марок сталей и сплавов одинакового назначения, что положено в основу сравнения стандартов различных стран.
|
|
Сравнение кратковременных механических свойств и показателей жаропрочности отечественных и зарубежных сталей одного и того же класса, несмотря на разницу в подходах к системам легирования, показывает их близость. Различие в свойствах, особенно при испытаниях на длительную прочность и ползучесть, может быть обусловлена не только основным химическим составом, но и особенностями технологии производства.
Ферритные и аустенитно-ферритные стали обладают сравнительно невысокой жаропрочностью. Однако они содержат повышенное количество хрома, который в сочетании с кремнием и алюминием предопределяет высокое сопротивление окисление до температур 1100-1150°C, и устойчивы в серосодержащих средах. Это определило область их применения, несмотря на технологические трудности, связанные с изготовлением оборудования из этих сталей и их высокой склонностью к охрупчиванию в процессе службы. Как жаростойкие, ферритные стали не несут конструкционной нагрузки, кроме собственного веса. До 600°C их прочность несколько ниже, чем мартенсито-ферритных и мартенситных сталей. Аустенито-ферритные стали имеют более высокую прочность, чем ферритные, однако они содержат (хотя и в ограниченных количествах) дорогостоящий никель.
Основным материалом многих стационарных энергетических установок является аустенитная сталь. В таблице 2.6. приведены те марки аустенитных сталей, которые имеют в числе прочих и назначение в качестве конструкционного материала для высокотемпературной области. Причем низкое содержание углерода не способствуют обеспечению жаропрочности, поэтому аустенитные стали с количественным содержанием углерода ниже 0,03 % (по массе) используются только как коррозионностойкие.
Для аустенитных сталей в России характерны те же ограничения, что и для конструкционных: экономия никеля (замена его марганцем), молибдена, ниобия, тантала. В результате серия зарубежных марок аустенитных сталей оказалась отличной от российских добавками именно этих элементов.
Отечественный стандарт содержит ряд оригинальных марок с интерметаллидным упрочнением, не имеющих зарубежных стандартизованных аналогов. Учитывая особенности легирования и структурных факторов, механические свойства аустенитных сталей представлены для трех групп сталей: с карбидным упрочнением, с интерметаллидным упрочнением и с ограниченным эффектом упрочнения за счет дисперсионного твердения.
Остальные стали относятся к умеренно или слабо упрочняемым и их удобно объединять в группу, ограничив минимальные свойства, как это сделано в стандарте А276.
Сплавы на основе никеля (ГОСТ 5632) делятся на две группы: жаростойкие сплавы для работы в качестве слабонагруженных деталей при температурах до 1250°C и жаропрочные дисперсионно-твердеющие сплавы для работы в качестве высоконагруженных деталей (лопатки и турбинные диски) при температурах до 1000°С.
Отечественные марки не имеют полных аналогов зарубежных сплавов по составу.
Жаропрочные и жаростойкие стали и сплавы применяются для деталей и механизмов в условиях действия высоких температур, газов и нагрузок. Важнейшие легирующие элементы в этой стали: хром, никель, алюминий, кремний, титан. Из таких сталей изготавливают лопатки газовых турбин, детали реактивных двигателей, камеры сгорания, детали газопроводных систем, реактивной техники и т. д. Марки таких сталей, например: 1Х14Н18В2Б, 03Х18Н12Т, 12Х25Н16Г7АР, 08Х14Н28ВЗТЗЮР. Марки сплавов: ХН70ВМТЮ, ХН75МБЮ.
Жаропрочные или окалиностойкие стали применяются в условиях повышенных температур (400 – 8500С). Для использования в таких условиях, как правило, применяют марки стали 15Х11МФ, 13Х14Н3В2ФР, 09Х16Н15М3Б. детали, изготовленные из стали одной из этих марок способны противостоять высоким температурам, сохраняя при этом свои свойства. Из такой стали изготавливают трубопроводы высокого давления, лопатки паровых турбин и т.п.
Марочник сталей онлайн (сравнение свойств различных жаропрочных и жаростойких сталей) http://www.splav.kharkov.com/simil2_class.php?type_id=1
Таблица 2.6.
Марки, состав, свойства жаропрочных сталей
Материал | Температура, 0 C | Жаропрочные свойства | |||||
Марка, | Группа сталей | Средняя доля основных легирующих элементов, % | Максимальная рабочая | Начала интенсивного окисления | σв↑ МПа | σ0.2↑ МПа | 0 C |
12Х1МФ | Перлитные | 0.12 C; 0.1 Cr; 0.3 Mo; 0.2 V | 570-585 | 600 | 140 | 84 | 560 |
25Х2М1Ф | 0.25 C; 2.3 Cr; 1 Mo; 0.4 V | 520-550 | 600 | 160-220 | 70 | 550 | |
15Х5М | Мартенситные | До 0.15 C; 5.2 Cr; 0.5 Mo; | 600 | 650 | 100 | 40 | 540 |
12Х18Н10Т | Аустенитные | До 0.12 C; 18 Cr; 10 Ni; 0.5 Ti | 600 | 850 | 80-100 | 30-40 | 660 |
10Х11Н20Т3Р | До 0.10 C; 11 Cr; 20 Ni; 2.6 Ti; 0.02 B | 700 | 850 | 400 | - | 700 |
Легированные стали марок 15Х5М, 16Х11Н2В2МФ, 12Х18Н10Т, 37Х12Н8Г8МБФ используют, если температура эксплуатации будет 10000С и выше. Эти стали обладают еще более высокой окалиностойкостью.
| ![]() |
Рис. 2.13. Фотографии газовой турбины и реактивного двигателя, в конструкции которых применяются марки жаропрочных и жаростойких сталей. |
К жаростойким сталям относятся стали марок 12Х13, 08Х18Н10Т, 15Х25Т, 10Х23Н18, 08Х20Н14C2, 1Х12МВСФБР, 06Х16Н15М2Г2ТФР-ИД, 12Х12М1БФР-Ш. Из сталей перечисленных марок изготавливают паровые котлы, теплообменники, термические печи, а также аппаратуру, которая будет эксплуатироваться при высоких температурах в агрессивных средах.
Коррозионно-стойкие стали.
Коррозионно-стойкие стали - легированные стали, устойчивавые к коррозии на воздухе, в воде, а также в некоторых агрессивных средах (табл. 2.7, рис. 2.14.).
Коррозионно-стойкие стали по травиальной, сложившейся в практике номенклатуре называют также нержавеющими сталями. Термин «нержавеющие» нельзя признать полностью корректным, так как в агрессивных средах, при температурах выше эксплуатационных коррозионно-стойкие стали всёже подвергаются коррозии. Вместе с тем термин нержавеющая сталь очень широко используется и тому есть причины. В технически допустимых условиях эксплуатации скорость коррозии коррозионно-стойких сталей весьма мала и после многих лет эксплуатации внешний вид изделий из стали мало изменяется. По тексту используются оба термина коррозионно-стойкие стали и нержавеющие стали.
Основным легирующим элементом коррозионно-стойких сталей является хром (Cr), содержание которого может изменяться в пределах от 12 до 20 %. На поверхности коррозионно-стойких сталей образуется тонкая пленка нерастворимых окислов, которая препятствует разъеданию стали в условиях окружающей среды. При содержании 12% хрома нержавеющая сталь обладает высокой коррозионной стойкостью в обычных условиях и в слабоагрессивных средах, при 17% хрома - в более агрессивных окислительных и других средах, в частности в азотной кислоте. Кроме хрома в коррозионно стойкую сталь входят углерод (C), кремний (Si), марганец (Mn), сера (S) и фосфор (P). Для придания стали необходимых физико-механических свойств и коррозионной стойкости в нее также добавляют никель (Ni), титан (Ti), ниобий (Nb), кобальт (Co), молибден (Mo).
Увеличение количества хрома в сплаве увеличивает устойчивость к коррозии. Добавление никеля и молибдена также способствует устойчивости стали к ржавчине. Никель добавляется для улучшения пластичности и вязкости сплава, повышает коррозионную стойкость, механическую прочность. Титан, ванадий, медь и неметаллы (углерод, азот и кремний) используются для улучшения структуры стали.
Высокоуглеродистая коррозионно-стойкая сталь содержит не менее 0,3% углерода. Чем выше содержание углерода, тем прочнее сталь.
Высокая прочность, коррозионная стойкость, эстетичность нержавеющей стали создают предпосылки для ее использования как материала для изготовления мебели, декоративных элементов и аксессуаров интерьера. В целлюлозно-бумажной промышленности из коорозионно-стойких сталей изготавливают оборудование целлюлозных и бумагоделательных заводов (табл. 2.7.).
Таблица 2.7.
Марки, состав, характеристики коррозионно-стойких сталей.
Марки сталей | Содержание легирующих элементов, % | Характеристики | |||||||||
ГОСТ | C | Mn | Si | Cr | Ni | Mo | Ti | ||||
12Х18Н9 | 0,12 | 2,0 | 0,75 | 18,0-19,0 | 8,0-10,0 | Сталь с низким содержанием углерода, аустенитная, незакаливаемая, устойчивая к воздействию коррозии, легко поддается сварке. | |||||
03Х18Н11 | 0,03 | 2,0 | 1,0 | 18,0-20,0 | 10,0-12,0 | Сталь аустенитная незакаливаемая, пригодная для сварных конструкций. Отличается высокой устойчивостью к воздействию межкристаллической коррозии. | |||||
03Х17Н14М2 | 0,08 | 2,0 | 1,0 | 16,0-18,0 | 10,0-14,0 | 2,0-2,5 | Сталь аустенитная незакаливаемая, наличие молибдена делает ее особенно устойчивой к воздействию коррозии. Технические свойства при повышенной температуре гораздо лучше, чем у аналогичных сталей, не содержащих молибдена | ||||
08Х18Н10Т | 0,08 | 2,0 | 1,0 | 17,0-19,0 | 9,0-12,0 | 5хС-0,7 | Сталь хромоникелевая с добавкой титана, аустенитная, незакаливаемая, немагнитная, особенно рекомендуется для изготовления сварных конструкций, устойчива к коррозии. | ||||
| | ||||||||||
Рис. 2.14. Зеркальная скульптура из нержавеющей стали в Чикаго, храм в Таиланде. | |||||||||||
Области применения коррозионно-стойких сталей: машиностроение (катализаторы, выхлопные трубы), авиационно-космическая промышленность (оборудования авиалайнеров, космических кораблей), химическая промышленность (все емкости, баки, реакторы, выхлопные трубы), электроэнергетика, пищевая промышленность, медицина и здравоохранение (медицинские инструменты, оборудования). В строительстве и архитектуре нержавеющая сталь используется для отделки фасадов и интерьеров, а также в качестве материала для строительных конструкций и сооружений: противопожарные двери, бассейны, лифты. Сталь применяется также в отделке интерьеров, комбинируется с другими материалами – деревом, камнем, стеклом, пластиком.
Резюме.
Содержание железа в земной коре составляет около 4,5%. Ниже температуры 911 °C железо существует в низкотемпературной модификации a-Fe, с объёмно-центрированной кубической элементарной ячейкой (ОЦК), а=0,286нм. От 911°C до 1392°C существует модификация g-Fe с гранецентрированной элементарной ячейкой (ГЦК), а=0.364нм. Температура плавления железа составляет 1539 °С.
В системе железо-углерод существуют следующие фазы: жидкий расплав, твердые растворы (феррит и аустенит), химическое соединение Fe3C (цементит), свободный углерод в виде графита. К структурным составляющим относят перлит и ледебурит, представляющие собой механические смеси сосуществующих фаз.
Сталь – сплав железа с углеродом, содержащий до 2.14 масс% углерода.В зависимости от химического состава различают стали углеродистые и легированные. По качеству стали подразделяют на стали обыкновенного качества, качественные, высококачественные, особовысококачественные. Элементы, специально вводимые в сплав с целью изменения его строения и свойств, называют легирующими, aданный сплав- легированным.
В изотермических режимах охлаждения получают фазово-зёренные структуры сталей: перлит, сорбит, тростит, бейнит, мартенсит. Выделяют четыре основных вида термической обработки сталей: отжиг, нормализация, закалка, отпуск.
Сведения по ряду важнейших сталей (инструментальные стали и твердые сплавы, жаростойкие, жаропрочные стали, нержавеющая сталь) – систематизированы.
Вопросы для самопроверки.
1. Какие элементарные ячейки имеют α-Fe, γ-Fe? В чём сходство и различие их элементарных ячеек?
2. В каких температурных интервалах стабильна модификация α-Fe?
3. Почему растворимость углерода в γ-Fe больше чем в α-Fe?
4. Дайте определение каждой из фаз, образующихся в системе Fe – Fe3С?
5. В каких температурных интервалах существуют феррит и аустенит?
6. Каков фазовый состав перлита и ледебурита? Почему указанные двухфазные составы рассматривают как структурные составляющие диаграммы Fe – Fe3С?
7. Составьте уравнение фазового превращения, протекающего при эвтектоидном распаде аустенита?
8. Дайте определение сталям? Какие химические элементы и другие составляющие входят в состав сталей?
9. Приведите количественные характеристики, по которым стали классифицируют по содержанию углерода, легирующих элементов?
10. На основе, каких признаков стали классифицируют по качеству?
11. По каким группам поставляется потребителям сталь обыкновенного качества?
12. С какой целью проводят раскисление сталей?
13. Назовите пути попадания в стали постоянных примесей, и какое влияние они оказывают на свойства сталей?
14. Почему сера и фосфор относятся к вредным примесям? Какие свойства сталей зависят от содержания серы и фосфора?
15. В каком зёренном виде MnS содержится в сталях?
16. Почему металлические листы обшивки «Титаника» не выдержали столкновение со льдом айсберга?
17. Вследствие каких причин в материалах возникают тепловые и фазовые напряжения?
18. С какой целью проводят отжиг сталей?
19. Почему отжиг проводят только на 30 – 50 градусов выше температуры GSK?
20. В чём нормализация подобна отжигу и проводится вместо него?
21. Почему отжиг проводят при температурах на 30 – 50 градусов выше температур линии GSK, а нормализацию выше температур линии GSE?
22. Дамскую сталь получали охлаждением заготовки в бочку, над которой 3 дня держали чёрного козла. В чем данный процесс более эффективен, чем охлаждение в воду?
23. Закалку на какую фазу называют истиной закалкой?
24. Как изменяется размер и характер расположения в структуре матрицы зёрен цементита в ряду фаз перлит – сорбит – тростит?
25. В чём фазовый состав бейнита отличается от состава тростита?
26. Какие схожие элементы проявляются в фазовом составе бейнита и мартенсита?
27. В чём сущность мартенситного перехода?
28. Какую структуру имеет мартенсит? В чём структура мартенсита схожа и отлична от структуры феррита?
29. Какие процессы протекают в зернистой структуре металла при рекристаллизационном отжиге?
30. Чем отпуск отличается от отжига?
31. Какие процессы происходят в материале при низкотемпературном, среднетемпературном и высокотемпературном отпусках?
32. В каких формах легирующие элементы содержатся в сталях?
33. Какие основные легирующие элементы содержатся в нержавеющих сталях?
34. Какое влияние на свойства сталей оказывает их легирование вольфрамом? Как маркируются такие стали?
35. В чём различие свойств режущего инструмента изготовленного из углеродистых и легированных сталей?
36. К каким группам сталей относятся стали У12, 65, А11, 8Х4В9Ф2-Ш? Каков их химический состав, области применения?
37. На каких физико-химических основах создаются жаропрочные и жаростойкие стали?
38. Какими химическими элементами легируют жаропрочные стали, и какие свойства данных элементов определяют их использование для придания сталям жаропрочности?
39. Какие легирующие элементы определяют стабильность нержавеющей стали к окислению?
Глава 3. Чугуны.
До 40% веса всех машин мира
приходится на чугунные детали и узлы.
Цели и задачи.
Цель – разобраться, чем чугуны отличаются от сталей, уяснить определения чугунов, виды чугунов, их основные свойства, области применения.
Задачи:
- уяснять определение чугунов, химический и фазовый составы чугунов;
- выяснить в чём преимущества чугуна как конструкционного и функционального материала;
- в каких формах углерод содержится в чугунах;
- виды чугунов, их определения, формы зёрен свободного углерода в каждом из видов чугунов, маркировка, отличительные признаки;
- области применения различных марок чугунов, привести 10 известных Вам примеров чугунных изделий.
Дата добавления: 2019-02-22; просмотров: 885; Мы поможем в написании вашей работы! |
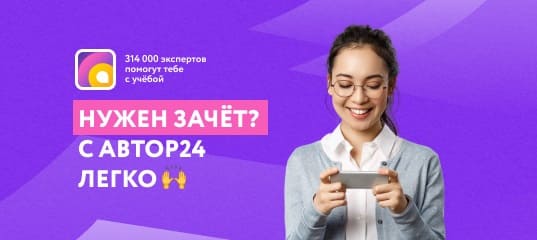
Мы поможем в написании ваших работ!