Виды чугунов доменного производства.
Среди конечных продуктов доменной плавки основным считается чугун, а шлак и доменный (колошниковый) газ – побочными.
Различают три основные разновидности доменного чугуна: передельный, литейный и доменные ферросплавы.
Передельный чугун используется для последующей плавки стали в конвертерах или мартеновских печах. На него приходится до 90% общего производства чугуна. Примерный состав легирующих добавок и примесей в предельном чугуне: 3,5-4,4% С, 0,3-1,2% Si; 0,2-1,0% Mn, 0,15-0,2% P и 0,02-0,07% S. Передельный чугун подразделяют на три вида: передельный коксовый (марки М0, Б0), передельный коксовый фосфористый (МФ0), передельный коксовый высококачественный (ПВК0).
Литейный чугун отличается от передельного повышенным содержанием кремния (до 3,6%) и в некоторых марках – фосфора (до 1.2%). Чугуны с высоким содержанием фосфора применяются в художественном литье, а с низким – для производства изделий с достаточной прочностью.
Природнолегированные чугуны, выплавляемые из руд отдельных месторождений, содержат хром, ванадий, никель и др.
Доменные ферросплавы применяются в качестве легирующих добавок и раскислителей при выплавке сталей. К ним относятся ферромарганец (70-75% Mn и более, до 2% Si, до 0,45% Р и до 0,03% S), а также получаемые ранее в доменном производстве бедный ферросилиций (9-15% Si, до 3% Mn, 0,2% Р и до 0,04% S) и зеркальный чугун (15-25% Mn, 2% Si, 0,2% P и до 0,03%S).
Классификация и маркировка чугунов.
|
|
Чугуны классифицируют по нескольким признакам: назначению, свойствам, формам углеродных внедрений, составу металлической матрицы, зерненной структуре металлической матрицы, другим признакам.
По внешним признакам чугуны подразделяют на следующие виды:
- белый чугун, в котором углерод находится в виде цементита и перлита, что придает излому чугуна блеск;
- серый чугун, в котором углерод находится в виде пластинчатых зёрен графита, что и придаёт чугуну серый цвет.
Чугун, в котором углерод одновременно находится в виде цементита и графита, называется половинчатым.
По специальным свойствам чугуны классифицируют на:
- ковкий чугун, в чугуне зёрна углерода имеют хлопьевидную форму;
- высокопрочный чугун с зёрнами углерода шаровидной (глобуловидной) формы;
- жаростойкие чугуны, легированные хромом, никелем, кремнием, магнием;
- жаропрочные чугуны;
- ростоустойчивые чугуны;
- антифрикционные чугуны – хромоникелевые серые чугуны, высокопрочные и ковкие чугуны;
- коррозионностойкие чугуны;
- кислотостойкие чугуны - ферросилиды, антихлор, нирезист.
Характерные физические свойства чугунов приведены в таблице 3.1.
По виду первичных и эвтектических зёрен чугуны подразделяют на доэвтектические (2,14 – 4,3% углерода), эвтектические (4,3%), заэвтектические (4,3 – 6,67%).
|
|
По химическому составу чугуны подразделяют на: нелегированные (общего назначения), легированные (специального назначения).
По степени легирования чугуны подразделяют на: простые, низколегированные (до 2,5% легирующих элементов), среднелегированные (2,5- 10% легирующих элементов), высоколегированные (свыше 10% легирующих элементов).
В зависимости от физико-механических свойств чугуны можно разделить по твердости на четыре группы: мягкие (HB < 149);средней твердости (HB149 – 197); повышенной твердости (HB197 – 269); твердые (HB > 269).
По прочности чугуны можно разделить на три группы:
- обыкновенной прочности (σВ ≤ 20 кгс/мм2) - серые чугуны;
- повышенной прочности (σВ = 20 – 38 кгс/мм2) - серые и ковкие чугуны;
- высокой прочности (σВ ≥ 40 кгс/мм2) - ковкие и высокопрочные чугуны с шаровидным графитом.
По фазово-зёренному составу металлической основы чугуны подразделяют на: перлитный, ферритный, перлитно-ферритный, аустенитный, бейнитный (табл. 3.1).
Углерод в чугуне может находиться в составе цементита, феррита, аустенита, перлита, ледебурита в виде свободного углерода (графита). В чугуне может присутствовать часть или все из перечисленных фаз.
|
|
Форма частиц свободного углерода оказывает значительное влияние на свойства чугунов. В сером чугуне частички графита имеют пластинчатую форму, в высокопрочном – шаровидную (глобуловидную), в ковком – хлопьевидную.
Чугуны маркируют двумя буквами и двумя цифрами, соответствующими минимальному значению временного сопротивления (sв) при растяжении в МПа ´10-1. Серый чугун обозначают буквами "СЧ" (ГОСТ 1412-85), высокопрочный - "ВЧ" (ГОСТ 7293-85), ковкий - "КЧ" (ГОСТ 1215-85). Например: СЧ 10 - серый чугун с пределом прочности при растяжении sв=100 МПа - 10 кг/мм2. ВЧ 70-5 - высокопрочный чугун с пределом прочности при растяжении sв=700 МПа (70 кг/мм2) и максимальным относительным удлинением 5%;КЧ35 - ковкий чугун с пределом прочности при растяжении sв=350 МПа (35 кг/мм2).
Табл. 3.1.
Виды металлических матриц и формы графита в чугунах. Условные обозначения: Ф – феррит, П – перлит, Гр – графит.
Для работы в узлах трения со смазкой применяют отливки из антифрикционного чугуна АЧС-1, АЧС-6, АЧВ-2, АЧК-2 и других подобных чугунов, что расшифровывается следующим образом: АЧ - антифрикционный чугун, С - серый, В - высокопрочный, К - ковкий; цифры обозначают порядковый номер сплава согласно ГОСТ 1585-79.
|
|
Передельные чугуны маркируются следующим образом: передельный чугун – П1, П2, передельный чугун для отливок — ПЛ1, ПЛ2, передельный фосфористый чугун – ПФ1, ПФ2, ПФ3, передельный высококачественный чугун – ПВК1, ПВК2, ПВК3.
Модифицирование чугунов.
Одним из способов повышения механических свойств серого чугуна является увеличение в шихте доли стального лома. Это способствует улучшению структуры металлической матрицы чугуна (наличие перлита вместо феррита) и уменьшению в нем графита. Чугун по свойствам и химическому составу стал приближаться к стали, его иногда так и называли сталистым чугуном. Если в чугуне снижать содержание углерода ниже известного предела, в структуре чугуна образуется цементит (Fe3C), придающий ему высокую твердость, хрупкость и белый излом. Такие отбеленные чугуны нельзя обрабатывать резанием, они не пригодны для машиностроения. Длительное время не удавалось решить эту проблему, невозможно было улучшить форму и распределение графитных включений. Универсальным, относительно дешевым, технологически гибким и высокоэффективным методом управления структурой кристаллизующегося сплава является модифицирование.
При модифицировании протекает объемная кристаллизация сплава с получением плотной, мелкозернистой и гомогенной структуры сплава в твердом состоянии, а также получения ряда специальных свойств.
Под модифицированием понимают ввод в расплавленный металл на определенных технологических этапах цикла плавка-разливка различных веществ (модификаторов), либо в виде сплавов, либо в виде смесей, обеспечивающих появление в расплавленном металле дополнительных центров кристаллизации, которые и решают задачу получения плотной, мелкозернистой и гомогенной структуры сплава в твердом состоянии.
Исходя из положений общей теории модифицирования и микролегирования для чугунов следует использовать комплексные присадки, содержащие щелочноземельные (Mg, Ca, Ba, Sr), редкоземельные (Y и лантаноиды - La, Ce и др.), карбидо- и нитридообразующие (Ti, Zr, V, Nb, B) элементы. Ввод этих элементов ведет к снижению в растворе концентрации серы, кислорода, азота, а также к развитию сложных физико-химических процессов образования и диссоциации окислов, сульфидов, оксисульфидов, карбидов, нитридов, карбонитридов и других промежуточных соединений. Следствием чего становится измельчение первичного аустенита за счет увеличения числа центров кристаллизации и увеличения склонности чугуна к графитизации за счет снижения в растворе карбидостабилизирующих элементов. Образовавшиеся при этом соединения играют роль дополнительных центров кристаллизации графита. В итоге это все ведет к измельчению дендритов первичного аустенита, эвтектических зерен, графитовых включений, устранению отбела при первичной кристаллизации, повышению плотности чугуна, его жидкотекучести, снижению склонности к образованию газовых раковин. Кроме того, сами эти элементы, оказавшиеся в химически несвязанном состоянии, микролегируют твердый раствор и повышают устойчивость аустенита и степень его переохлаждения при эвтектоидной кристаллизации. При этом возрастает доля перлита и его дисперсность. В ряде случаев (при микролегировании карбидо- и нитридообразующими присадками) при охлаждении отливок ниже 700°C в структуре появляются мелкодисперсные карбиды и нитриды, дополнительно повышая прочность матрицы.
Для повышения эффективности действия указанных выше присадок их надо вводить с определенным количеством кремния и (или) алюминия, которые в период эвтектической кристаллизации уменьшают растворимость углерода в растворе, повышают его активность и снижают относительное переохлаждение при эвтектической кристаллизации. Все это способствует активации образующихся при модифицировании неметаллических включений в качестве центров кристаллизации графита, изменяет форму графитовых включений и повышает графитизирующую способность чугуна.
Основное влияние на образование различных форм графита в чугуне оказывают примеси, способствующие изменению соотношения поверхностной энергии на гранях кристаллов графита. Скорость охлаждения оказывает влияние на форму графита только в чугунах повышенной чистоты. Такие элементы как C, Si, (Cu), Ni и P уменьшают поверхностное натяжение расплава чугуна на призматических гранях растущих кристаллов графита, что приводит к образованию кристаллов пластинчатой формы. Такие элементы как Ti, Cr, W, Mo, (Cu), Mg, Ce и РЗМ очищают расплав от примесей, что приводит к увеличению поверхностного натяжения расплава на призматических гранях растущих кристаллов графита и образованию вермикулярной и шаровидной форм графита.
Эффект модифицирования определяется количеством возникших дополнительных центров кристаллизации и их каталитической активностью. Частицы первичного графита выделяются в зонах растворения модификаторов, обогащённых кремнием. Кристаллическая структура частиц обеспечивает их каталитическую активность, как центров зарождения и роста зерен графита. Активные центры существуют в интервале времени между вводом модификатора в расплав и затвердеванием отливки. Создание максимального числа дополнительных центров кристаллизации достигается за счёт:
1. стимулирования выделения углеродсодержащих фаз при растворении модификатора;
2. повышения устойчивости дополнительных центров кристаллизации после растворения модификатора;
3. сокращения интервала между вводом модификатора и затвердеванием отливки.
Ввиду скоротечности процесса растворения и быстрого исчезновения в высокотемпературном расплаве зон химической, а тем более тепловой неоднородности является важным стимулирование процесса выделения углеродсодержащих фаз (графит, SiС) из пересыщенного углеродом расплава. Это достигается активацией выделения графита на готовых или неметаллических включениях (НВ),-возникающих на границах раздела «расплав-С с этой целью в ферросилиций вводятся элементы, имеющие большее, чем у Si сродство к кислороду (Al, ЩЗМ, РЗМ). Указанные элементы конкурируют с Si в зонах растворения модификатора,-в высокой (5...20%) концентрации.
Изменение концентрации Si от 60...75% в модификаторе до 1,5...2,5% в удалённых точках расплава приводит к образованию карбида кремния SiС при содержании кремния свыше 20...25% и температурах 1350...1450°C наряду с первичным графитом (при содержании кремния более 5...7%). Углеродсодержащие частицы являются дополнительными центрами кристаллизации графитной эвтектики при последующем затвердевании отливки. Однако, после завершения растворения модификатора, при выдержке расплава зоны термической и концентрационной неоднородности исчезают, и углеродсодержащие частицы становятся термодинамически неустойчивыми и растворяются, что и определяет термовременный характер инокулирующего эффекта.
Существует свыше 500 действующих типов различных модификаторов, содержащих от двух - трёх компонентов, до полутора десятков. С учетом запатентованных составов их количество переваливает за 1000. Разобраться в этом калейдоскопе модификаторов, их свойствах, довольно сложно. В результате возникает серьезная проблема экономически оптимально и технологически правильно подобрать нужный тип модификатора для заводской технологии.
Существенным недостатком любого типа модифицирования является требование достаточно высоких температур расплава перед началом модифицирования. Для чугуна >13600С, для стали > 14200C. При более низких температурах расплава модификатор плохо растворяется в расплаве и переходит в шлак («зашлаковывается») и эффект модифицирования быстро затухает. В этом случае требуется значительный перерасход модификатора.
В настоящее время в области модифицирования стали и чугуна, особенно чугуна, сложилась парадоксальная ситуация. Структурные перекосы в экономике породили и структурно-технологические перекосы в области чугунолитейного производства.
Из-за низкого качества дешевых исходных материалов для плавки и преимущественного использования вагранки в качестве дешевого плавильного агрегата (электропечи из-за высокой стоимости электроэнергии для ряда литейных производств убыточны) эффективность традиционных модификаторов резко снизилась, что привело к массовому получению конструкционных чугунов низкой прочности.
Этому явлению способствует также то, что проявление модифицирующего эффекта ограничивается температурой расплава перед модифицированием. Нижний температурный предел модифицирования, как показывает практика, находится в пределах 1340 – 1360 0С. Данный температурный предел позволяет разделить расплавы чугуна на низкотемпературные – 1200 – 1320 0С (доменный и ваграночный чугун) и высокотемпературные – 1380 – 1400 0С и выше (электроплавка и «дуплекс-процесс» вагранка + миксер). Следовательно, низкотемпературные расплавы чугунов фактически являются технологически немодифицируемыми чугунами.
Типичные физические свойства чугуна приведены в таблице 3.2.
Табл. 3.2
Типичные физические свойства чугуна
Тип чугуна | Белый чугун | Серый чугун | Ковкий чугун | С повышением температуры: + повышается, – понижается. |
Удельный вес г/см3 | 7.2 ± 0.2 | 7.1 ± 0.2 | 7.3 ± 0.1 | – |
Действительная усадка в % | 1,8 ± 0,2 | 1,1 ± 0,2 | + | |
Теплопроводность в кал/см×сек×оС | 0,08 ± 0,02 | 0,1 ± 0,02 | 0,13 ± 0,02 | – |
Динамическая вязкость при температуре ликвидус | 0,08 | 0,04 | – | |
Поверхностное натяжение в дин/см2 | 900 ± 100 | 900 ± 100 | + | |
Электросопротивление В Мк ом×см | 70 ± 20 | 80 ± 20 | 50 ± 20 | + |
Теплоёмкость в кал/г×оС | 0,13 ± 0,02 | 0,12 ± 0,02 | 0,12 ± 0,02 | + |
Коэрцитивная сила в э | 13 ± 2 | 10 ± 1; 1,5 ± 0,5 | 1,5 ± 0,5 | – |
Остаточный магнетизм в гс | 5000 ± 1000 | 5000 ± 1000 | 5000 ± 1000 | – |
Белый чугун.
Такое название чугун получил по виду излома, который имеет матово-белый цвет. Весь углерод в белом чугуне находится в связанном состоянии в виде цементита.Белые чугуны в зависимости от содержания углерода могут быть доэвтектическими (перлит + ледебурит), эвтектическими (ледебурит) и заэвтектическими (первичный цементит + ледебурит). Белые чугуны имеют большую твердость (НВ 450 – 550) из-за присутствия в них большого количества цементита; как следствие этого, они очень хрупкие и для изготовления деталей машин не используются. Белые чугуны не могут подвергаться механической обработке ни в холодном, ни в горячем виде. Отливки из белого чугуна служат для получения деталей из ковкого чугуна с помощью графитизирующего отжига, который называется томлением.
Отбеленные чугуны-отливки имеют поверхностные слои (12 – 30мм) со структурой белого чугуна, а сердцевина – серого чугуна. Высокая твердость поверхности такой отливки позволяет ей хорошо работать против истирания. Эти свойства отбеленного чугуна применяются для изготовления валков листовых прокатных станов, шаров для мельниц, тормозных колодок и многих других деталей, работающих в условиях износа. Из отбеленного чугуна изготовляются литые вагонные колеса, называемые колесами Гриффина. Используется чугун с 3-3,5%C и небольшим количеством других примесей не превышающий 1% для каждой из них. Процесс литья проводят так, что белый чугун получается на большей или меньшей толщине от поверхности; далее же, вглубь отливки, получается уже серый чугун.
Рис 3.2 Фотографии микроструктуры белого чугуна, шаров для мельниц, изготовленных из белого чугуна.
Серый чугун.
Такое название чугун получил по виду излома, который имеет серый цвет. В структуре серого чугуна имеется графит.
Серым называется чугун состоящий из металлической основы перлитного, ферритно-перлитного, ферритного фазовых составов и пластинчатых графитовых включений.
Поскольку зёрненная структура чугуна состоит из металлической основы и графита в форме пластин, то и механические свойства серого чугуна зависят от свойств металлической основы и ее количества, формы и размеров графитных включений (пустот).
Графит по сравнению со сталью обладает низкими механическими свойствами и поэтому в некотором приближении можно считать, что места, которые он занимает по отношению к свойствам чугуна подобны пустотам и трещинам. Количественное соотношение основы и пустот влияет на механические свойства чугуна, и с увеличением последних свойства резко ухудшаются. Чем более грубы включения графита, тем, следовательно, больше разобщена металлическая основа, что отрицательно сказывается на свойствах чугуна. Недостатком серого чугуна является хрупкость, препятствующая его использованию для изготовления деталей машин, подвергающихся ударным нагрузкам
Серый чугун мягкий материал, хорошо обрабатывается режущим инструментом. Серый чугун обладает малой пластичностью, его нельзя ковать, так как содержащийся в нем графит способствует раскалыванию металла. Серый чугун значительно лучше работает на сжатие, чем на растяжение. При растягивающих напряжениях легко образуются центры разрушения на концах графитных включений. Значительно лучше ведет себя чугун при напряжениях сжатия и изгибе. Получается серый чугун путем медленного охлаждения после плавления или нагревания. Температура плавления серого чугуна 1100 – 1250 °С.
Серые чугуны являются сплавами сложного состава, содержащими железо, углерод, кремний, марганец и неизбежные примеси, такие, как сера и фосфор. Фосфор частично растворяется в феррите (~ 0,3 %) а также входит в тройную эвтектику (Fe – С – Р) с температурой плавления 950°С. Присутствие в сплавах эвтектики существенно улучшает литейные свойства чугуна. Эвтектика очень твердая и хрупкая, что увеличивает износостойкость, а хорошие литейные свойства используются и в художественном литье (до 1% Р). Обычно серый чугун содержит 2,8 – 3,6 % углерода, 1,6 – 3,0 % кремния, 0,5 – 1 % марганца, 0,2 – 0,8 % фосфора и 0,05 – 0,12 % серы. Сера уменьшает жидкотекучесть и прочность чугуна, увеличивает его литейную усадку и затрудняет его сварку. Фосфор делает чугун более жидкоплавким и улучшает его свариваемость, но повышает твердость и хрупкость. Если серый чугун быстро охлаждать после плавления, то он отбеливается, т. е. частично превращается в белый, и становится очень хрупким и твердым. Наличие в составе чугуна большого количества кремния способствует получению серого чугуна. Присутствие в чугуне большого количества марганца способствует отбеливанию чугуна.
По структуре металлической основы серые чугуны разделяют на три вида (табл. 3.3).
1. Серый перлитный со структурой перлит + графит (количество связанного углерода составляет ~ 0,8 %.).
2. Серый ферритно-перлитный со структурой феррит + перлит + графит (количество связанного углерода < 0,8 %).
3. Серый ферритный со структурой феррит + графит (весь углерод в виде графита).
Графит способствует измельчению стружки при обработке резанием и оказывает смазывающее действие, что повышает износостойкость чугуна. Номенклатура отливок из серого чугуна и их масса разнообразны: от деталей в несколько граммов до 100 т и более.
Ферритные серые чугуны марки Сч10, Сч15 используются для слабо- и средненагруженных деталей: крышки, фланцы, маховики, суппорты, тормозные барабаны, диски сцепления и т. д.
Ферритно-перлитные серые чугуны марки Сч20, Сч25 применяются для деталей, работающих при повышенных статических и динамических нагрузках: картеры двигателя, поршни цилиндров, барабаны сцепления, станины станков и другие отливки разного назначения.
Перлитный чугун применяют для отливки станин мощных станков и механизмов. Часто используют серые перлитные модифицированные чугуны. Такие чугуны получают при добавлении в жидкий чугун перед разливкой специальных добавок — ферросилиция (0,3 - 0,6% от массы шихты) или силикокальция (0,3 - 0,5% от массы шихты). К таким чугунам относятся Сч40 и Сч45, которые обладают более высокими механическими свойствами из-за измельчения формы графитных включений. Эти марки чугунов применяются для корпусов насосов, компрессоров и гидроприводов.
Для деталей, работающих при повышенных температурах, применяют легированные серые чугуны, которые дополнительно содержат хром, никель, молибден и алюминий.
Марка серого чугуна состоит из букв Сч (серый чугун) и цифры, показывающие механические свойства серого чугуна в соответствии с ГОСТ 1412-85. Марка чугуна Сч 12-28, читается следующим образом: Сч – серый чугун, первые двухзначные цифры 12,15,18 и т. д. – средняя величина предела прочности при испытании на разрыв в кг/мм2, а вторые – 28,32 . – средняя величина предела прочности при изгибе в кг/мм2.
Показателями механических свойств серых чугунов в соответствии с ГОСТ 1412-85 является прочность при статическом растяжении ( табл. 3.3)
Таблица 3.3.
Механические свойства серых чугунов.
Чугун | sВ, МПа | НВ | Структура металлической основы |
Сч 15 | 150 | 163-229 | Феррит |
Сч 25 | 250 | 180-250 | Феррит + перлит |
Сч 40 | 400 | 207-285 | Перлит |
Сч 45 | 450 | 229-289 | Перлит |
Рис. 3.3 Фотография микроструктуры серого чугуна марок СЧ-15(левая), СЧ-20(правая).
Высокопрочный чугун.
Давно установлено, что наиболее благоприятная форма графитных включений шаровидная или как их назвали позже глобуловидная. Эта форма графитных включений способствует повышению пластичности и прочности чугуна. Придание графитным включениям шаровидной формы позволило существенно расширить границы применения чугуна.
У высокопрочного чугуна могут быть такая же структура металлической матрицы и химический состав, как и у обычного серого чугуна, различие состоит лишь в форме графита. Такое различие в структуре придает новому чугуну достаточно высокие необычные свойства: пластичность (относительное удлинение до 10% и более), вязкость (ударная вязкость 1,5 – 4,0 кгс/см2), теплоустойчивость, термическую выносливость и износостойкость. Прочность при этом возросла более чем в 3 раза, из-за чего он и получил название высокопрочного. Новый чугун по цвету похож на сталь, он звенит и режется кислородом почти так же, как сталь. При этом количество, распределение и размеры графитных включений практически незначительно влияют на свойства высокопрочного чугуна.
Получают такой чугун путем модифицирования магнием. Этот процесс сопровождается сильным возгоранием, поэтому чистый магний заменяют лигатурами (например, сплавом магния и никеля). После модифицирования высокопрочный чугун имеет следующий химический состав: 3—3,6% С; 1,8—2,9% Si; 0,4—0,7% Мn; 0,02 – 0,08% Mg; < 0,15% Р; < 0,03% S. Весь процесс модифицирования и получения из обычного чугуна высокопрочного длится несколько минут.
Таким образом, простейшим способом за 2 – 3 мин обычный чугун превращается в новый конструкционный материал, благоприятно сочетающий в себе свойства чугуна и стали.
Дата добавления: 2019-02-22; просмотров: 1721; Мы поможем в написании вашей работы! |
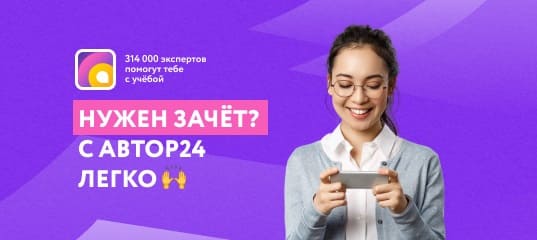
Мы поможем в написании ваших работ!