Термическая обработка и фазовые превращения в сталях.
Под термической обработкой понимают комплекс операций нагрева и охлаждения сплава, осуществляемых по определенному режиму с целью изменения строения сплава и получения заданных свойств во всём объёме детали.
Основу термической обработки составляет изменение структурно-фазового состава и дислокационной структуры сплава, которое может быть достигнуто путем использования таких ключевых факторов, как наличие у фаз сплава полиморфных превращений или зависящей от температуры ограниченной взаимной растворимости компонентов. Термической обработкой обеспечивается заданный уровень свойств во всем объеме детали.
Все существующие виды термообработки, имеющие целью существенно изменить фазовую и дислокационную структуру сплавов и получить оптимальный комплекс эксплуатационных свойств, основаны на использовании одного из упомянутых факторов. При их отсутствии термообработкой можно получить лишь весьма ограниченные результаты.
Существуют две наиболее распространенные разновидности термической обработки. Одна из них основана на использовании специфики превращений в сплавах, обусловленной наличием в них полиморфных превращений, а другая базируется на переменной растворимости компонентов друг в друге при нагреве и охлаждении. В обоих случаях фундаментальной основой технологии термической обработки, гарантирующей получение ожидаемых результатов, является ее режим. Он включает в себя следующие элементы: температуру нагрева, скорость нагрева до заданной температуры, время выдержки при этой температуре и скорость охлаждения. Конкретные величины, характеризующие каждый из элементов режима термообработки, зависят от химического состава обрабатываемого сплава, размера детали и целевого назначения выполняемого вида термообработки. Варьируя эти величины, можно существенно изменять фазовую и дислокационную структуры сплава и придавать ему заданные свойства.
|
|
Термическая обработка стали является наиболее характерным и хорошо изученным процессом, базирующимся на наличии в ней аллотропических превращений, происходящих при нагреве и охлаждении в области определенных критических температур.
Превращения в стали при равновесном нагреве и охлаждении.
На диаграмме состояний железо – углерод стали занимают область до 2,14% С. Для того чтобы при термообработке стали реализовать возможности, предоставляемые аллотропическими превращениями, ее следует нагревать до температур, при которых происходят эти превращения и обусловленные ими очень важные структурно-фазовые изменения.
Сталь нагревают в специальных термических печах с пламенным или электрическим обогревом. Первое превращение стали происходит при температуре около 727°C (рис. 2.7, изотерма PSK). Оно состоит в превращении феррито-цементитной смеси (перлит) в аустенит, являющийся твердым раствором внедрения углерода в γ-Fe, содержащий при этой температуре 0,8 % углерода независимо от количества последнего в обрабатываемой стали.
|
|
Температура превращения перлит – аустенит (П – А) является первой критической точкой (обозначают Ac1). При этой температуре, вследствие аллотропического превращения α-Fe ® γ-Fe, образуется более равновесная, чем перлит, фаза аустенита, обладающая меньшим запасом свободной энергии. В ней растворяется весь находившийся в перлите углерод.
Рис. 2.7. Часть диаграммы состояния железо – цементит вблизи эвтектоидного превращения. (Точка E находится выше рисунка).
Открытие критических точек в стали, осуществленное в 1868г. знаменитым русским ученым-металлургом Д. К. Черновым, создало научную основу термической обработки.
При нагреве стали до точки Ac1 после определенной выдержки (необходимой для протекания приводящих к равновесию диффузионных процессов) сталь приобретает равновесный двухфазный состав соответственно: Ф0,02+ П0,8 ® Ф0,02+ А0,8 (доэвтектоидная сталь) или П0,8 + Ц6,67 ®А0,8 + Ц6,67 (заэвтектоидная сталь). В соответствии с диаграммой состояния в феррите содержится около 0,02 % C (точка Р), в аустените – 0,8 % C (точка S), в цементите – 6,67 % С.
|
|
При дальнейшем повышении температуры поддержание равновесия между образовавшимися фазами обеспечивается диффузионными изменениями их химического состава. Так, в доэвтектоидных сталях составы феррита и аустенита изменяются соответственно по линиям PG и SG, фактически происходит растворение Ф в А.
В заэвтектоидных сталях равновесие между аустенитом и цементитом с ростом температуры поддерживается за счет растворения Ц в A, приводящего к обогащению аустенита углеродом (вплоть до 2,14 % C в точке E, рис. 2.7) и уменьшению количества цементита.
На линиях SG и SE находятся критические температуры, при которых сталь приобретает равновесную однофазную структуру аустенита. Точки, лежащие на линии SG, принято обозначать Ас3, а на линии SE – Acm. При дальнейшем нагреве доэвтектоидных сталей, начиная с температур, равных Ас3 + (30 – 50) °С, наблюдается заметный рост зерна аустенита, приводящий к снижению прочности термически обработанной стали. В заэвтектоидных сталях это неблагоприятное явление происходит, начиная с температур нагрева Acm+ (30—50) °С.
|
|
Температуры нагрева стали при термической обработке обычно ограничиваются вышеуказанными величинами. Хотя в интересах сокращения времени на обработку было бы желательно ускорять диффузионные процессы путем нагрева стали до более высоких температур. В соответствии с режимом термообработки после нагрева и выдержки стали при заданной, зависящей от содержания углерода температуре следует процесс охлаждения аустенита. Вначале рассмотрим, какие структурно-фазовые изменения происходят в аустените доэвтектоидной стали при равновесном, т. е. достаточно медленном, охлаждении.
По достижении определенной температуры (точки на линии SG) аустенит начнет распадаться (А ® Ф + А) и сталь снова будет состоять из двух фаз (Ф + А).
Достигаемая при охлаждении критическая температура, соответствующая началу выпадения феррита из аустенита, обозначается критической точкой Аг3. Ее величина зависит от содержания углерода в стали.
Когда температура достигнет изотермы PSK, равновесный фазовый состав стали будет представлен ферритом и аустенитом, содержащими соответственно 0,02 и 0,8 % С.
При температуре, обозначаемой критической точкой Аг1 аустенит превращается в перлит. Заметим, что феррит и цементит перлита, образующегося при распаде аустенита, имеют форму чередующихся пластинок. Таким образом, при равновесном охлаждении получается исходный равновесный структурно-фазовый состав доэвтектоидной стали: Ф+ П.
Аустенит заэвтектоидной стали после равновесного охлаждения превращается в исходную смесь перлита и цементита (П + Ц). При этом, начиная с температур, лежащих на линии SE, из него будет выделяться избыточный углерод в виде вторичного цементита, а при температуре Ar1 аустенит по уже известной схеме превратится в перлит: А0,8 ®Ф0,02 + Ц6.67. Сталь приобретает свою исходную равновесную заэвтектоидную структуру: П + Ц.
Сплав с равновесной структурой имеет такую плотность дислокаций, которая обеспечивает ему минимальный предел текучести (ρ ≈ 107 см-2). Получению низкой прочности способствует и то обстоятельство, что при равновесном, т. е. достаточно медленном, охлаждении в доэвтектоидной стали формируются довольно крупные зерна избыточного феррита.
Однако термообработка в большинстве случаев производится с целью получения у стали более высоких показателей прочности. В связи с этим режим обработки должен быть построен таким образом, чтобы получающаяся после ее завершения дислокационная структура характеризовалась более высокой плотностью дислокаций и наличием в ней элементов, затрудняющих процесс пластической деформации (дислокационные стенки, атмосферы Коттрелла, стопоры). Кроме того, режим термической обработки должен строиться и с учетом возможности управления прочностью за счет регулирования размера зерен структурных составляющих стали.
Дата добавления: 2019-02-22; просмотров: 1086; Мы поможем в написании вашей работы! |
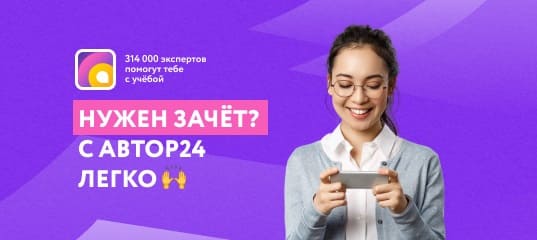
Мы поможем в написании ваших работ!