Сравнение основных свойств сталей и чугунов.
Таблица 2.2.
Сравнение основных свойств сталей и чугуна.
Свойства | Сталь | Чугун | ||||
определение | Сталь - сплав железа с углеродом (0-2,14 масс % С) содержащий кремний, марганец, вредные примеси серу, фосфор, технологические примеси, а также легирующие добавки. | Чугун – сплав железа с углеродом, содержащий 2,14 – 6,67 масс. % С, вредную примесь серу, технологические примеси, легирующие добавки. | ||||
Предприятия производители | Сталь производят на крупных комбинатах. | Чугун из руды выплавляют на комбинатах, чугун из вторичного сырья может быть получен как на заводах, так и в мелких мастерских. | ||||
Основные отличительные особенности: Пластичность, хрупкость | Для стали характерна пластичность. Сталь подвергается ковке, волочению, обработке давлением, токарной, фрезерной обработке (высокоуглеродистые стали менее пластичны). | Для чугунов характерна хрупкость, особенно от механических воздействий - ударов (хотя имеются ковкие чугуны). | ||||
коррозия (окисление в естественных условиях) | Сталь подвержена коррозии на воздухе, в агрессивной среде особенно в присутствии жидкой и газообразной воды. Нержавеющая сталь легирована хромом, никелем. Оксиды хрома на поверхности препятствуют окислению изделий. | Чугун окисляется поверхностно, но коррозионностоек к объёмной коррозии в массивном изделии, стоек в условиях воздействия влаги и температуры (батареи, реакторы, топочное оборудование, печные плиты). | ||||
свариваемость в электрической дуге | Стальные изделия свариваются в сложные конструкции. Наиболее легко свариваются низкоуглеродистые стали. Металлоконструкции – существенная составляющая промышленных предприятий, строительных сооружений. Для сварки используются электроды разных марок. | Чугунные детали свариваются специальными электродами, часто необходим прогрев места сварки. При сварке электродами, используемыми для изготовления стальных конструкций, чугуны трескаются в месте сварки. | ||||
изготовление детали путем литья. | Стали обладают плохими литейными свойствами. Промышленные стальные изделия изготавливают путем проката. | Чугуны обладают хорошими литейными свойства, большинство изделий изготовляется путем литья. | ||||
Токарная обработка, фрезерование (При токарной обработке деталь вращается, инструмент совершает плоско поступательные движения. При фрезеровании инструмент вращается, деталь неподвижна или совершает плоско параллельные перемещения.) | Детали из стали изготавливают путём токарной обработки (деталь имеет ось симметрии) и фрезерованием. Используются также другие методы: ковка, гнутьё, штамповка, волочение. | Чугуны подвергаются несложным токарным и фрезерным обработкам. Как правило, фрезеруются места сочленения деталей. | ||||
Изменение свойств во времени | Подвержены старению | Подвержены старению | ||||
Общие свойства сталей и чугунов: | · обладают высокими прочностными характеристиками, стабильными во времени;
· способны выдерживать продолжительные циклические нагрузки; · имеют высокую или достаточную твердость, которая сохраняется во времени; · не пропускают газы и жидкости. | |||||
области применения | Среднее и крупное машиностроение, промышленное и гражданское строительство, обрабатывающая промышленность, автомобилестроение, железнодорожный транспорт, рельсы, сельскохозяйственное машиностроение, высокоточная техника, бытовая продукция, военная техника, резервуары для хранения углеводородов, трубопроводы. | Реакторы нефтеперерабатывающих предприятий и химических производств, станины крупного и среднего машиностроения, корпуса механических преобразователей, военная техника, детали автомобилестроения, сельскохозяйственного машиностроения, железнодорожный транспорт, топочные котлы, художественные изделия. |
Превращения сталей в твёрдом состоянии.
|
|
Большинство технологических операций (термическая обработка, обработка давлением и др.) проводят при нахождении железоуглеродистых сплавов в твердом состоянии. Особое значение приобретают фазовые превращения, которые происходят в сталях в твёрдом состоянии, позволяющие получать стали на основе ферритной, аустенитной, перлитной и других видов структур.
Рассмотрим превращения, протекающие в сталях при охлаждении из однофазной аустенитной области (рис. 2.3). Сплавы железа с углеродом, содержащие до 0,02% C (точка P диаграммы), называют техническим железом. Если углерода в железоуглеродистом сплаве содержится меньше 0,0002 % (сплав I, рис. 2.3, а), то при охлаждении от температуры точки 1 до температуры точки 2 происходит перекристаллизация аустенита в феррит. Однофазная ферритная структура сохраняется вплоть до температуры 20-25°С.
а) б)
Рис. 2.3.Часть диаграммы состояния Fe — Fe3C для сплавов, не испытывающих (а) и испытывающих (б) эвтектоидное превращение.
При содержании углерода в техническом железе больше 0,0002%, как в сплаве II, после образования феррита, начиная с температуры точки 5, происходит выделение из феррита кристаллов третичного цементита. Этот процесс вызван уменьшением растворимости углерода в феррите (см. линию PQ, рис. 2.3, а). Конечная структура охлаждённого сплава будет двухфазной и образована зёрнами феррита и третичного цементита. Зёрна цементита располагаются в виде прослоек по границам ферритных зерен (рис. 2.4, б). Третичный цементит ухудшает технологическую пластичность сплавов.
|
|
При температуре 20 – 25 °C третичный цементит имеется во всех железоуглеродистых сплавах, содержащих более 0,0002% C. Однако роль третичного цементита в формировании свойств невелика, так как его содержание мало по сравнению с цементитом, выделившимся при других фазовых превращениях. Обычно при рассмотрении структуры сплавов с содержанием углерода более 0,02 % о третичном цементите не упоминают.
Рис. 2.4. Микроструктура (рисунок с фотографии) технического железа с содержанием углерода:
а - 0,006% C присутствуют зёрна только технического железа (1); б – 0,01% C по границам зёрен технического железа имеются зёрна третичного цементита (2).
Рис. 2.5. Фотографии (слева) и рисунки (справа) микроструктур сталей: а, б – феррито-перлитного типа с увеличение содержания перлита; в – перлит; г – перлит с выделением вторичного цементита (светлая сетка).
Количественное соотношение между структурными составляющими (феррит и перлит) в доэвтектоидных сталях определяется содержанием углерода. Чем ближе содержание углерода к эвтектоидной концентрации, тем больше в структуре перлита. Следовательно, зная содержание углерода в доэвтектоидной стали, можно заранее предвидеть ее зёренную структуру в стабильном состоянии (рис. 2.5).
Сплав II (см. рис. 2.3, б) с содержанием 0,8 % C называется эвтектоидной сталью. В ней при температуре линии PSK происходит эвтектоидное превращение, в результате которого из аустенита выделяются феррит с содержанием 0,02% C и цементит. Такую смесь двух фаз называют перлитом (рис. 2.5, б). Эвтектоидное превращение идет при постоянной температуре и составе фаз, так как в процессе одновременно участвуют три фазы, и число степеней свободы равно нулю. Сплав I (см. рис. 2.3, б) с содержанием углерода менее 0,8 % называют доэвтектоидной сталью. Эвтектоидному превращению в таких сталях предшествует частичное превращение аустенита в феррит в интервале температур точек 1 – 2. При температуре точки b фазовый состав сплава Ас + Фа. Количественное соотношение аустенита и феррита соответственно определяется отношением отрезков ab и bc.
При температуре точки 2 сплав имеет фазовый состав As + Фр с количественным соотношением фаз соответственно Р2 и 2S. В результате эвтектоидного превращения аустенит переходит в перлит, который вместе с выделившимся ранее ферритом образует конечную структуру стали (рис.2.5,а).
Сплав III (рис. 2.3, б) является заэвтектоидной сталью (> 0,8 %С). Эвтектоидному превращению в этих сталях в интервале температур точек 3 – 4 предшествует выделение вторичного цементита (ЦII) из аустенита. Этот процесс вызван уменьшением растворимости углерода в аустените согласно линии ES диаграммы (рис. 2.3).
t , 0С |
t , 0С |
С, % |
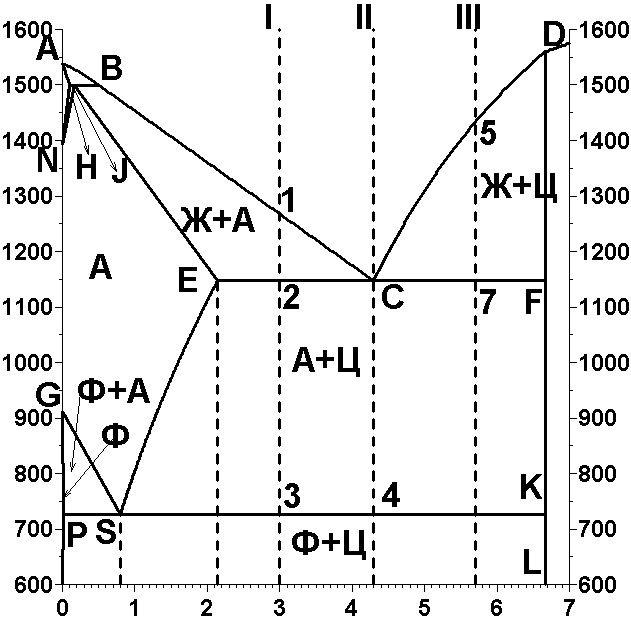
Рис. 2.6. Часть диаграммы состояния системы Fe – Fe3С для высокоуглеродистых сплавов.
В результате при охлаждении до температуры точки 4 аустенит в стали обедняется углеродом до 0,8 % и на линии PSK испытывает эвтектоидное превращение. При медленном охлаждении вторичный цементит выделяется на границах аустенитных зерен, образуя сплошные оболочки, которые на микрофотографиях выглядят светлой сеткой (рис. 2.5, в). Максимальное количество структурно свободного цементита (~ 20 %) будет в сплаве с содержанием углерода 2,14%.
Стали. Классификация сталей.
Сталь – сплав железа с углеродом, содержащий до 2.14 масс. % углерода, а также содержащий марганец и кремний, природные и технологические примеси, вредные примеси фосфор и серу а также вводимые для улучшения физико-химических свойств легирующие добавки.
Сталь является основным металлическим материалов, широко применяемым для изготовления деталей машин, летательных аппаратов, приборов, различных инструментов и строительных конструкций. Широкое использование сталей обусловлено комплексом их механических, физико-химических и технологических свойств. Методы широкого производства стали были открыты в середине XIX в. В это же время были уже проведены и первые металлографические исследования железа и его сплавов.
Стали сочетают высокую жесткость с достаточной статической и циклической прочностью. Эти параметры можно менять в широком диапазоне за счет изменения концентрации углерода, легирующих элементов и технологий термической и химико-термической обработки. Изменяя химический состав, можно получать стали с различными свойствами и использовать их во многих отраслях техники и народного хозяйства.
Углеродистые стали классифицируют по химическому составу, назначению, качеству, степени раскисления, структуре в равновесном состоянии.
Химический состав. В зависимости от химического состава различают: стали углеродистые (ГОСТ 380-88, ГОСТ 1050-88) и легированные (ГОСТ 14959-79).
В свою очередь, углеродистые стали могут быть:
а) малоуглеродистыми, т.е. содержащими углерода менее 0,25 масс. %;
б) среднеуглеродистыми, в которых содержание углерода составляет 0,25 – 0,60 масс. %;
в) высокоуглеродистыми, в которых концентрация углерода превышает 0,60 масс. %.
Легированные стали подразделяются на:
а) низколегированные, содержащие до 2,5 % легирующих элементов;
б) среднелегированные, в их состав входят от 2,5 % до 10,0 % легирующих элементов;
в) высоколегированные, которые содержат свыше 10,0 % легирующих элементов.
Назначение. По назначению стали бывают:
а) конструкционные, предназначенные для изготовления строительных и машиностроительных изделий;
б) инструментальные, из которых изготовляют режущий, мерительный, штамповый и прочий инструмент; эти стали содержат более 0,65 % углерода;
в) с особыми физическими свойствами, например, с определенными магнитными характеристиками или малым коэффициентом линейного расширения: электротехническая сталь, суперинвар;
г) с особыми химическими свойствами, например нержавеющие, жаростойкие или жаропрочные стали.
Конструкционные стали представляют наиболее обширную группу, предназначенную для изготовления строительных сооружений, деталей машин и приборов. К этим сталям относят цементуемые, улучшаемые, высокопрочные и рессорно-пружинные. Инструментальные стали подразделяют на стали для режущего, измерительного инструмента, штампов холодного и горячего (до 200 °С) деформирования.
Качество. Под качеством стали понимается совокупность свойств, определяемых металлургическим процессом ее производства. Однородность химического состава, строения и свойств стали, а также ее технологичность во многом зависят от содержания газов (кислорода, водорода, азота) и вредных примесей серы и фосфора. Газы являются скрытыми, количественно трудно определяемыми примесями, поэтому нормы содержания вредных примесей служат основными показателями для разделения сталей по качеству.
Стали в зависимости от содержания вредных примесей серы и фосфора подразделяют на:
а) стали обыкновенного качества, содержащие до 0,06 % серы и до 0,07 % фосфора; их получают в конвертерах или мартеновских печах;
б) качественные - до 0,035 % серы и фосфора каждого отдельно; стали получают преимущественно в мартеновских печах с соблюдением повышенных требований к составу шихты, технологическим режимам плавки и разливки. В стали одной марки допускается колебание содержания углерода не более 0,08%;
в) высококачественные - до 0,025 % серы и фосфора; сталь получают главным образом в электропечах или кислых мартеновских печах. Колебание содержания углерода в стали одной марки не более 0,07%;
г) особовысококачественные - до 0,025 % фосфора и до 0,015 % серы; выплавляют в электропечах с электрошлаковым переплавом или другими прогрессивными методами. Для таких сталей характерна высокая ударная вязкость, стойкость к пониженным температурам, контактная выносливость.
Сталь обыкновенного качества по поставкам подразделяется на 3 группы:
а) сталь группы А поставляется потребителям по механическим свойствам (такая сталь может иметь повышенное содержание серы и фосфора). Химический состав сталей не регламентируется. Эти стали применяются в конструкциях, узлы которых не подвергаются горячей обработке - ковке, горячей штамповке, термической обработке и т. д. В связи с этим механические свойства горячекатаной стали сохраняются;
б) сталь группы Б поставляется потребителям с определённым регламентированным химическим составом, без гарантии механических свойств. Эти стали применяются в изделиях, подвергаемых горячей обработке, технология которой зависит от их химического состава, а конечные механические свойства определяются самой обработкой;
в) сталь группы В поставляется потребителям с регламентируемыми механическими свойствами и химическим составом. Эти стали применяются для изготовления сварных конструкций. Их свариваемость определяется химическим составом, а механические свойства вне зоны сварки определены в состоянии поставки. Такие стали применяют для более ответственных деталей.
В зависимости от нормируемых показателей (предел прочности sв, относительное удлинение d %, предел текучести sт, изгиб в холодном состоянии) сталь каждой группы делится на категории, которые обозначаются арабскими цифрами.
По степени раскисления и характеру затвердевания стали классифицируют на спокойные, полуспокойные и кипящие. Раскисление — процесс удаления из жидкого металла кислорода, проводимый с целью предотвращения хрупкого разрушения стали при горячей деформации.
а) спокойные стали, т.е. полностью раскисленные; такие стали обозначаются буквами "сп" в конце марки (иногда буквы "сп" опускаются);
б) кипящие стали - слабо раскисленные; маркируются буквами "кп";
в) полуспокойные стали - занимающие промежуточное положение между двумя предыдущими; обозначаются буквами "пс".
Спокойные стали раскисляют марганцем, кремнием и алюминием. Они содержат мало кислорода и затвердевают спокойно без газовыделения. Кипящие стали раскисляют марганцем. Перед разливкой в них содержится повышенное содержание кислорода, который при затвердевании частично взаимодействует с углеродом и удаляется в виде CO. Выделение пузырьков СО создает впечатление кипения стали, с чем и связано ее название. Кипящие стали достаточно дешевые, их производят низкоуглеродистыми и практически без кремния (Si < 0,07%), но с повышенным количеством газовых примесей.
Полуспокойные стали по степени раскисления занимают промежуточное положение между спокойными и кипящими.
Легированные стали производят спокойными, углеродистые – спокойными, полуспокойными и кипящими. Производство кипящих сталей постоянно уменьшается.
Дата добавления: 2019-02-22; просмотров: 1018; Мы поможем в написании вашей работы! |
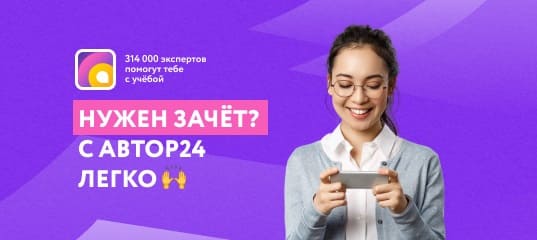
Мы поможем в написании ваших работ!