Форма отчета к выполненной лабораторной работе
«Физико-химический анализ моторных масел»
ФИО студентов_____________________________________группа_________
Руководитель занятий_______________________________Дата____________
Применяемое оборудование___________________________________________
____________________________________________________________________
Показатели качества | Данные | Имеющиеся | |
НД | Испытаний | отклонения | |
Кинематическая вязкость, мм2/с при 20оС 40оС 75оС 100оС | |||
Индекс вязкости | |||
Отношение вязкости n50/n100 | |||
Содержание воды: Качественное Количественное, % | |||
Кислотное число, мг КОН/г |
График вязкостно-температурной характеристики
Заключение:
Отметка о защите:
6 Физико-химический анализ консистентных смазок
Теоретическая часть
Основное назначение пластических смазок уменьшать износ деталей, снижать коэффициент трения, защищать детали от коррозии. Их применяют там, где жидкие смазки вытекают, а также для герметизации подвижных соединений и защиты деталей, подвергающихся сильному воздействию грязи и пыли.
Консистентные смазки представляют собой жидкие масла, специальным образом защищенные для того, чтобы предать им ряд эксплутационных свойств не обеспечиваемых маслами. Консистентные смазки состоят из смеси масел 80-90%, загустителя 9-20%, наполнителя, стабилизатора и присадок. По физической структуре смазки представляют неоднородную среду состоящею из двух фаз твердой и жидкой. Грубой моделью может служить кусочек поролона, пропитанный водой (каркас - поролон, загущаемое масло- вода). Свойство твердого тела придает смазки наличие твердого каркаса. Прочность каркаса зависит от природы и процентного содержания в смазке загустителя.
|
|
Загустители могут быть мыльными и немыльными. К мыльным загустителям относятся соли натуральных и жирных синтетических кислот, т.е. мыла. Широко распространены калиевые, литиевые, натриевые, бариевые, алюминиевые, цинковые, свинцовые. К немыльным загустителям относятся твердые углеводороды-парафины, церазин, воск, озокериты и т.д. Смазки на немыльном загустителе влагостойкие.
В качестве масленой основы используют различные нефтяные и синтетические масла. От вязкости масла зависит вязкостные и низко температурные свойства масел.
Присадки вводят в состав смазок с целью улучшения противоизносных, противокоррозионных свойств, повышения термостойкости и химической стабильности. Присадки вводят до 5% по массе. Применяют, как правило, те же присадки что и в производстве масел.
Стабилизаторы вводят в смазки для повышения колодной стабильности.
|
|
В смазках специального назначения (уплотнительные, резьбовые, рессорные) применяют наполнители. Наполнителями называют различные твердые порошкообразные вещества, вводимые в смазки для придания им дополнительных свойств. В отличие от присадок наполнители нерастворимы в маслах и находятся в смазках во взвешенном состоянии. Наполнители могут уменьшать или увеличивать коэффициент трения, увеличивать прочность смазки, повышать ее термостойкость. В качестве наполнителя применяют: графиты, дисульфид молибдена, слюду.
Консистентные смазки классифицируются следующим образом:
- по термостойкости смазки делятся на: низкоплавкие до 40-65°С; среднеплавкие до 100°С; тугоплавкие более 100°С;
- по назначению консистентные смазки делятся на: универсальные и специальные (антифрикционные, консервационные, уплотнительные);
- по области применения: автомобильные, самолетные, тепловозные;
- по основе загустителя: мыльные, углеводородные, селикагелевые;
- по прочности каркаса: пластичные, полужидкие, жидкие.
Консистентные смазки должны отвечать следующим требованиям: сохранять однородность и стабильность в процессе работы, обеспечивать заданные механические свойства, снижать коэффициент трения и механический и коррозионный износ металлов, не разрушать резинотехнические изделия быть влаго и термостойкими.
|
|
В маркировку смазок входят: назначение и область применения данной смазки, основа загустителя, рекомендуемый температурный диапазон применения, дисперсная среда, число пенетрации.
Назначение и область применения смазки обозначается первой буквой:
С- общего назначения для обычных температур, солидолы;
О- смазки для работы при повышенных температурах до 100°С;
М- многоцелевые, рабочая температура от 30-130°С;
Ж- термостойкие, рабочая температура выше 150°С;
Н- морозостойкие, рабочая температура ниже -40°С;
И- противозадирные и противоизностные;
П- приборные;
Д- приработочные;
Х- химически стойкие;
З- защитные, консервационные;
А- арматурные;
Р- резьбовые;
В- вакуумные;
К- канатные.
Следующие буквы в маркировке обозначают основу загустителя:
Ли- литиевое мыло;
Ка- калиевое мыло;
На- натриевое мыло;
Ли-Ка смесь литиевого и калиевого мыла и т.д.
|
|
Цифры в маркировке обозначают диапазон рабочих температур, уменьшенный в 10 раз, например 2/10 – рабочая температура от -20 до +100°С.
Тип дисперсной среды или добавки обозначают строчной буквой:
у- синтетические углеводороды (синтетические масла);
к- кремнеорганические жидкости;
г – графит;
д - дисульфид молибдена;
Если нет индекса, в качестве жидкой фазы использованы нефтяные масла.
Индекс консистенции обозначается цифрой и стоит последним в маркировке.
Пример: Мли3/14-3, Смазка «Литол 24» - многоцелевая в качестве загустителя использовано литиевое мыло, рабочая температура от -30 до 140°С, загущено нефтяное масло, добавок нет, класс густоты 3.
Основные характеристики наиболее часто употребляемых смазок приведены в таблице 6.1
Таблица 6.1- Основные характеристики смазок
Товарное наименование | Температура каплепадения, оС, не менее | Пенетрация при 25оС, 10-4мм | Предел прочности при 20оС, Па | Вязкость при 0оС и скорости деформации 10 с-1, Па×с | Коллоидная стабильность, %, не более |
Солидол С | 85 …105 | 260…310 | 200…500 при 50ос | ≤ 190 | 1…5 |
Пресс-солидол С | 85…95 | 310…350 | 100…400 при 50ос | ≤ 90 | 2…10 |
Солидол Ж | 78 | 230…290 | 196 при 50ос | ≤ 250 | - |
Графитная | 77 | 250 | 100 при 50ос | ≤ 100 | 5 |
1-13 | 120 | 180…250 | 500…1000 | ≤ 500 | 20 |
Консталин | 130 | 225…275 | 150…300 | 250…500 | 8…20 |
Литол -24 | 185 | 220…250 | 500…1000 | ≤ 280 | 12 |
Фиол-1 | 185 | 310…340 | ≥ 250 | ≤ 200 | 25 |
Фиол-2 | 188 | 265…295 | 300 | ≤ 250 | 16 |
Фиол-2м | 180 | 265…295 | 300 | ≤ 250 | 15 |
Циатим 221 | 200 | 280…160 | 250…450 | 80…200 | 7 |
Экспериментальная часть
6.2.1 Оборудование, инструменты, реактивы:
Прибор для определения температуры каплепадения;
Пластомер К - 2;
Прибор КСА;
Пробирки химические;
Цилиндр мерный на 50 мл;
Колба КН-2-250-34 ТХС;
Пинцет никелированный;
Штатив химический;
Пенетрометр;
Плитка электрическая закрытого типа;
Бензин Б-70;
Стеклянные пластинки.
6.2.2 Определение цвета и внешнего вида смазок
Цвет смазки зависит в основном от рода загустителя. Кальциевые смазки имеют цвет от светло-коричневого до темно-коричневого. Натриевые и кальце-натриевые от светло-желтого до ярко-желтого цвета. Литиевые смазки светло-коричневые, литиевая смазка №158- синего цвета. Графитная смазка - черного цвета. Определить цвет смазки визуально.
Однородность и механические примеси. Каждая смазка должна быть однородной. Не допускается вкрапление частиц загустителя, выделения масла, присутствие механических примесей. Смазку нанести на лабораторное стекло толщиной 1...2 мм и прижать вторым стеклом. Рассматреть в проходящем свете. Если в смазке находятся механические примеси, то при растирании смазки слышится характерный скрежет. При обнаружении механических примесей нужно провести анализ на растворимость в спиртобензольной смеси и воде и нерастворимость в соляной кислоте. Механические примеси нерастворимые в соляной кислоте очень опасны, т.к. вызывают абразивный износ трущихся поверхностей
Определение основы загустителя по растворимости в воде и бензине. Кальциевые и литиевые смазки нерастворимы в бензине и воде, образуют текучие непрозрачные системы. Натриевые и кальце-натриевые смазки на немыльном загустителе растворимы в бензине, не растворимы в воде.
Для определения рода загустителя испытуемый образец смазки, в объеме приблизительно по 1 см3, внести стеклянной палочкой в самый низ двух пробирок, стараясь при этом не задеть их стенок.
Затем добавить четырехкратное количество дистиллированной воды в первую и столько же бензина во вторую пробирку.
Первую пробирку нагреть над спиртовкой и довести воду до кипения. Чтобы не было выброшено содержимое пробирки, необходимо при нагревании вращать пробирку вокруг своей оси. Полное растворение загустителя и образования мыльного раствора с плавающим на ее поверхности маслом свидетельствует о принадлежности испытуемого образца к натриевым смазкам.
Если же после охлаждения пробирки вода остается прозрачной или слегка мутной, а ее поверхность покрыта слоем смазки, следует проводить испытание на растворимость в бензине.
Подогреть вторую пробирку на водяной бане до 60°С (степень нагрева определяют на ощупь). Смазка считается растворимой, если образуется совершенно прозрачный раствор.
6.2.3 Определение температуры каплепадения
Для проведения испытания необходим специальный термометр типа ТН-4 в комплекте с гильзами и чашечками из латуни рисунок 6.1.
Нужно вынуть капсюль 4 из гильзы термометра и с помощью шпателя наполнить его испытуемой смазкой, следя за тем, чтобы в месте с ней не попадали пузырьки воздуха. Излишек смазки срезать с верхней части капсюля шпателем, вставить капсюль в гильзу термометра до упора о внутренний бортик. Излишек смазки, выдавленный шариком термометра, срезать шпателем.
На дно пробирки 3 поместить кружок бумаги, который необходимо менять после каждого определения.
Термометр с капсюлем вставить в пробирку так, чтобы нижний край капсюля находился на расстоянии 25 мм от дна пробирки. Вертикально поместить пробирку в коническую колбу, заполненную водой или глицерином, закрепить в штативе.
1- стакан с водой или глицерином; 2 - специальный термометр; 3 - пробирка; 4- мешалка; 5 - нагревательный элемент
Рисунок 6.1 - Прибор для определения температуры каплепадения
Нагрев жидкости вести в два этапа. На первом этапе, где скорость нагрева не нормирована, интервал температур составляет от комнатной до 20°С для низкоплавких, до 60°С для среднеплавких, до 130°С для натриевых и литиевых. На втором этапе темп повышения температуры в приборе должен составить 1°С в минуту. На обоих этапах жидкость в колбе должна помешиваться специальной мешалкой 4.
Температуру, при которой в процессе нагревания падает из нижнего отверстия капсюля первая капля испытуемой смазки, считать температурой каплепадения. Если смазка не образует капли, а вытягивается из капсюля в виде цилиндра, то за температуру каплепадения принимают ту, при которой выходящий столбик смазки коснется дна пробирки.
6.2.4 Определение предела прочности
Испытание проводят на пластометре К-2 рисунок 6.2, который должен быть разобран, тщательно промыт и высушен.
Прибор состоит из основания со стойкой, по которой вертикально перемещается электропечь 8. Электропечь нагревает резервуар 7 с маслом для повышения давления, которое контролируется по манометру 5. Воронка 6 служит для добавления масла в прибор, кран 4 для сообщения воронки с внутренней полостью прибора. Корпус 1 трубкой соединен с внутренней полостью прибора. Внутри оправки 2 находится капилляр 3. В комплект прибора входят два капилляра, один длинной 100 мм, другой длиной 50 мм. Короткий капилляр применяется в том случае, когда при испытании на длинном капилляре давление превышает допустимое для манометра. На внутренней полости капилляра нанесена резьба. Все внутренние полости прибора К-2, включая манометр, заполнены маловязким маслом, с целью полного вытеснения воздуха.
1-корпус; 2- оправка; 3- капилляр; 4- кран; 5- манометр; 6- воронка; 7 резервуар с маслом; 8- электропечь
Рисунок 6.2 - Прибор пластометр К-2 для определения предела прочности смазок
Перемешанной смазкой заполнить обе половинки желоба капилляра, следя за тем, чтобы не было пузырьков воздуха и пропусков смазки в резьбе. Осторожно, чтобы не вызвать сдвига смазки, соединить их и надеть кольцо.
Смазать испытуемой смазкой наружную поверхность капилляра и вставить в оправку. На нижний обрез бортика оправки надеть резиновую прокладку на выступ в корпусе пластометра.
Пластометр заполнить маслом, для чего открыть кран воронки с маслом и держать его открытым до тех пор, пока уровень масла в корпусе не достигнет верхнего обреза бортика оправки.
Закрепить оправку в корпусе гайкой. На верхней части корпуса установить защитное стекло. Закрыть кран. Включить электропечь, обогревающую резервуар с маслом, и наблюдать за манометром.
Скорость повышения давления в системе должна быть не более 5 кПа в 1 мин при использовании длинного капилляра и 5 кПа при использовании короткого. Скорость повышения давления регулировать, поднимая и опуская вдоль резервуара с маслом электропечь. Это соответственно увеличивает или уменьшает площадь нагрева.
После того как давление в системе достигнет максимума, произойдет выдавливание смазки, что можно наблюдать через защитное стекло, и давление начнет снижаться. Необходимо записать максимальное давление, отключить прибор и обработать результаты.
Предел прочности t (Па) испытуемой пластичной смазки вычислить по формуле:
, (6.1)
где Р- максимальное давление, кгс/см2; r, l- радиус и длина капилляра, r = 2мм и l = 50мм или 100мм.
6.2.5 Определение коллоидной стабильности
Для определения коллоидной стабильности используют прибор КСА рисунок 6.3.
1-смазка; 2-чашка; 3-шток; 4-груз; 5-пусковая кнопка; 6-шарик; 7-поршень; 8-бумажные фильтры; 9-столик.
Рисунок 6.3 - Прибор КСА для определения коллоидной стабильности смазок
Прибор состоит из штатива с плиткой, на которой установлен круглый уровень и столик 9. На стойке штатива укреплен кронштейн, в котором помещен шток 3 с двумя выемками для крепления груза 4. Металлический шарик 6 служит для передачи давления на хвостик поршня. На столик устанавливают чашечку 2 для испытуемой смазки, в которую вставлен поршень 7. Чашечка снабжена втулкой для вывода хвостовика поршня. Масса штока, шарика, поршня и груза составляет 1 кг.
Чашечку с поршнем промыть в бензине и высушить.
Один кружок фильтровальной бумаги смочить маслом, отжать между листами фильтровальной бумаги.
Чистую чашечку с поршнем и промасленной фильтровальной бумагой взвесить на аналитических весах.
Затем в чашечку шпателем вмазать смазку, не допуская образования пузырьков воздуха и пустот, и опять взвесить с промасленной фильтровальной бумажкой.
На столик установить стопку фильтровальных бумажек 7-9 шт. Сверху положить промасленный кружек фильтровальной бумаги и чашечку со смазкой. В лунку хвостовика поршня поместить шарик.
Нажать пусковую кнопку 5, освободить шток и опустить его до соприкосновения с шариком.
На шток надеть груз, нажать пусковую кнопку, закрепить ее скобой и отметить время начала испытания.
По истечению 30 мин. Взвесить чашечку со смазкой и кружком фильтровальной бумаги.
Массовая доля масла X(%), выделившегося после прессования пластичной смазки, вычислить по формуле:
, (6.2)
где G1- масса чашечки с поршнем и фильтровальной бумагой без смазки, г; G2 -масса чашечки со смазкой и пропитанным маслом кружочком фильтрованной бумаги до испытания, г; G3 - масса чашечки со смазкой и пропитанным маслом кружочком фильтровальной бумаги после испытания, г.
Смазка считается пригодной, если массовая доля выделившегося масла меньше 20%.
6.2.6 Определение содержания воды
Содержание воды в разных смазках сказывается по-разному. Так в кальциевых и кальциево-натриевых смазках присутствие воды обязательно, так как вода для них является стабилизатором. Удаление воды из этих смазок приводит к полному разрушению смазок.
В составе литиевых, углеводородных смазок наличие воды не допускается. В некоторых смазках допустимо незначительное количество воды (в некоторых бариевых, алюминиевых).
В пробирку, предварительно тщательно промытую и высушенную, поместить смазку до высоты 40-60 мм. Для облегчения введения смазок края пробирки слегка подогреть, после чего комки смазки, частично расплавляясь, опускаются на дно пробирки.
Пробирку закрыть пробкой, в отверстие которой вставить сухой термометр. Термометр поместить в смазке таким образом, чтобы ртутный шарик находился в центре и на 20 мм ниже уровня смазки.
Пробирку со смазкой нагреть, перемещая ее в наклонном положении над пламенем спиртовки. Скорость повышения температуры до полного расплавления смазки поддерживать 10°-20 °С в мин.
После того, как смазка расплавилась, нагрев ускорить до 70°С. Появление толчков, треск, пузырьков, указывает на наличие воды в смазке.
6.2.7 Определение числа пенетрации
Определение числа пенетрации проводят на стандартном приборе пенетрометр.
Пенетрометр рисунок 6.4 состоит из массивного штатива 1, в который укреплен конус 6 стандартной массы. При нажиме кнопки 5 конус начинает свободно падать и погружается в смазку, которая помещается в металлический толстостенный стакан 7, установленный на столике прибора 8.
1-штатив; 2- зубчатая рейка; 3- шкала; 4-шток; 5- пусковая кнопка; 6- конус; 7- стакан; 8- столик прибора.
Рисунок 6.4 - Прибор для определения числа пенетрации
Анализ проводится следующим образом. Металлический стакан заполнить смазкой, завинтить крышку с мешалкой и поместить в водяную баню, где выдержать при 25°С в течение 1 часа. Стакан 7 с разогретой смазкой перенести на площадку мешалки, закрепить ручку мешалки и размешивать смазку поднятием и опусканием ручки мешалки 60 раз.
Стакан с испытуемой смазкой поместить на стол пенетрометра и выровнять поверхность смазки шпателем вровень с краями стакана, полностью удалив ее избыток.
Поддерживая одной рукой шток 4 и нажимая на кнопку, осторожно опустить конус 6, стараясь возможно точнее (с точностью до 0,1 мм) совместить его острие с поверхностью смазки. Как только это будет выполнено, кнопку 5 опустить, благодаря чему зафиксируется достигнутое положение.
Затем привести в исходное положение отсчетный механизм пенетрометра, для чего, плавно нажимая на верхний конец зубчатой рейки 2, опустить ее до упора в верхний обрез штока 4, а стрелку на шкале 3 поворотом в любом направлении установить против нуля.
Нажать кнопку и, придерживая ее в таком положении в течение 5 с, наблюдать за погружением конуса вместе со связанным с ним штоком (см. рис 6.4) в смазку.
По истечению 5 с кнопку опустить, и плавно снизить до упора в шток рейку измерительной шкалы.
Одновременно с опусканием рейки будет поворачиваться соединенная с ней шестеренка стрелки по шкале 3. Число делений, на которое повернется стрелка по шкале, и будет представлять собой выраженную в десятых долях миллиметра глубину погружения стандартного конуса, т.е. пенетрацию смазки.
Испытание проделать 5 раз, каждый раз, тщательно очищая конус от налипшей смазки, выравнивая ее поверхность и изменяя перемещением стакана место погружения конуса.
Максимальное расхождение между отдельными замерами не должны превышать 6%.
Контрольные вопросы
Назначение консистентных смазок?
Состав консистентных смазок?
Классификация консистентных смазок?
Что характеризует число пенетрации смазки?
Что такое предел прочности консистентных смазок?
Что такое коллоидная стабильность консистентных смазок?
Как маркируют консистентные смазки?
Что характеризует температура каплепадения консистентной смазки.
Дата добавления: 2019-02-26; просмотров: 167; Мы поможем в написании вашей работы! |
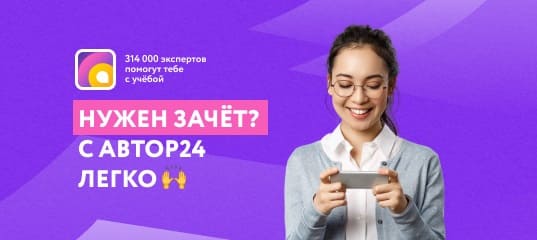
Мы поможем в написании ваших работ!