Подбор и расчет технологических машин подготовительного отделения мукомольного завода
При определении количества технологических машин подготовительного отделения мукомольного завода, расчетную суточную производительность этого отделения принимают на 10…20 % больше суточной производительности размольного отделения. Это необходимо для обеспечения бесперебойной работы размольного отделения. Производительность размольного отделения указана в задании к курсовой работе. Такое увеличение запаса предусматривают также для возможного в дальнейшем повышения производительности мукомольного завода в результате внедрения более совершенного оборудования, средств автоматизации, прогрессивных приемов и способов подготовки зерна к помолу и самого процесса размола. Таким образом, производительность подготовительного отделения определяется по формуле:
(6)
где Q п – суточная производительность подготовительного отделения мукомольного завода, т/сутки;
Q р – суточная производительность размольного отделения мукомольного завода, т/сутки;
k – коэффициент запаса производительности (k = 1,1 ¸ 1,2).
Проверку правильности подбора технологического оборудования проводят согласно коэффициенту его использования , который рассчитывают по формуле:
, (11)
Подбор технологического оборудования проведен правильно, если коэффициент использования ( ) для автоматических весов, концентратов, щеточных и обоечных машин близок к 1 (но не более 1), а для другого технологического оборудования
меньше или равно 1,25. Концентраторы, обоечные и щеточные машины не допускают перегрузки, так как это связано с ухудшением качества очистки зерна и, иногда, приводят к завалам. Поэтому коэффициент использования этих машин должен быть не более 1,0.
|
|
Определение количества расходуемой воды на мойку и увлажнение зерна
После подбора технологических машин для мойки зерна необходимо рассчитать количество расходуемой воды на мойку зерна. Исходят из того, что средний расход воды для мойки зерна составляет 1,5…2,0 л на 1 кг зерна в сутки. Количество расходуемой воды в сутки в м3 для мойки зерна определяется по формуле:
, (14)
где N в – расход воды на мойку зерна в сутки, м3;
Q пл1 – суточная производительность линии подготовки зерна к помолу, т/сутки;
в – расход воды на 1 кг зерна в сутки, л.
Расход воды может быть снижен, если предусмотреть очистку моечных вод и использовать ее для повторной мойки зерна.
Методика подбора и расчета технологического оборудования размольного отделения мукомольного завода
|
|
Подбор и расчет технологического оборудования размольного отделения мукомольного завода основывается на используемой схеме размола или на количественном балансе помола. От правильности подбора и расчета технологического оборудования и его распределения по системам драного, шлифовочного и размольного процессов зависит выход и качество муки, а также расход электроэнергии. На основе используемой схемы размола основное оборудование для размольного отделения мукомольного завода рассчитывается следующим образом. На основе принятых удельных нагрузок для того или иного вида помола определяют:
1) потребную общую длину вальцовой линии;
2) просеивающую поверхность рассевов;
3) ширину сит ситовеечных машин.
Нормы удельных нагрузок на вальцовую линию, просеивающую поверхность рассевов и ширину ситовеечных машин следует принимать из таблицы, представленной в приложении М. Ориентировочные показатели построения схем помолов пшеницы и ржи следует принимать из таблицы, представленной в приложении Н.
Расчет длины вальцовой линии
Удельная нагрузка на вальцы q в принимается в соответствии с нормами для вида помола из таблицы приложения П. Тогда общая длина вальцовой линии в см определяется по формуле:
|
|
, (16)
где Q р – производительность размольного отделения мукомольного завода, т/сутки;
q в – удельная нагрузка на 1 см длины вальцов, кг.
Общая длина вальцовой линии L общ складывается из суммы длин вальцовой линии драного процесса L др, вальцовой линии шлифовочного процесса L шл и вальцовой линии размольного процесса L р, что может быть записано как уравнение баланса в виде формулы:
, (17)
Отношение Кдл длины вальцовой линии шлифовочного и размольного процесса Lшл + Lр к длине вальцовой линии драного процесса Lдр для различных видов помола определяется из таблицы приложения М. Тогда можно записать уравнение баланса в виде формулы
, (18)
Из данного соотношения и уравнения баланса по формуле 19 можно определить длину вальцовой линии драного процесса:
, (19)
Оставшаяся длина от общей длины вальцовой линии за исключением длины вальцовой линии драного процесса приходится на шлифовочный и размольный процесс. Длина вальцовой линии шлифовочного и размольного процесса определяется по формуле:
|
|
, (20)
При многосортных хлебопекарных помолах пшеницы от суммы длин вальцовых линий шлифовочного и размольного процесса на долю шлифовочного процесса приходится 25…30 %. Если принять в этом соотношении долю шлифовочного процесса 27 %, то длину вальцовой линии шлифовочного процесса можно определить по формуле:
, (21)
Соответственно длина вальцовой линии размольного процесса определяется по формуле:
, (22)
В пределах драного, шлифовочного и размольного процесса рассчитанная длина вальцовой линии распределяется по технологическим системам. При выполнении курсовой работы распределение длины вальцовой линии по технологическим системам проводится на примере только драного процесса (по остальным процессам расчеты проводятся аналогично). Так как количество поступающего продукта на каждую драную систему различно, необходимо провести расчет вальцовой линии по каждой драной системе в отдельности. Принимаем, что в схеме многосортного пшеничного хлебопекарного помола предусмотрено пять драных систем. Тогда распределение вальцовой линии по драным системам можно представить в виде таблицы 1.
Таблица 1 – Распределение вальцовой линии по драным системам
Система | Распределение по системам, % | Расчетная длина вальцовой линии по системам, см | |
по нормам | фактическое* | ||
I драная | 12…16 | 16 | ![]() |
II драная | 22…26 | 26 | ![]() |
III драная | 22…26 | 26 | ![]() |
IV драная | 17…22 | 19 | ![]() |
V драная | 8…14 | 13 | ![]() |
Итого | - | 100 | …** |
* Фактическое распределение вальцовой линии по системам драного процесса взято в качестве примера
** Суммарная расчетная длина вальцовой линии систем драного процесса должна быть равна L др.
Вальцовые станки выпускают трех типоразмеров с длиной вальцов 1000, 800 и 600 мм. Необходимо подобрать подходящий типоразмер и определить число вальцовых станков для каждой системы. При определении количества вальцовых станков, которые следует установить на каждую систему, следует иметь в виду, что 1/2 вальцового станка может работать независимо. Длина мелющей линии станка с вальцами размером 1000 Х 250 для 1/2 станка составляет 100 см, а для всего станка 200 см. Такая же закономерность характерна и для других типоразмеров вальцовых станков. Длина мелющей линии станка с вальцами размером 800 Х 250 для 1/2 станка составляет 80 см, а для всего станка 160 см. Для 1/2 станка с вальцами размером 600 Х 250 длина мелющей линии составляет 60 см, а для всего станка 120 см.
Подбор типоразмеров вальцовых станков и определение их количества на мелющей линии драного процесса по системам осуществляется в форме заполнения таблицы 2.
Таблица 2 – Подбор типоразмеров вальцовых станков и определение их количества
Система | Расчетная длина вальцовой линии по системам, см | Размер вальцов, мм | Количество станков | Фактическая длина вальцовой линии, см |
I драная | LI др = … | … | … | L ф I др = … |
II драная | LII др = … | … | … | L ф II др = … |
III драная | LIII др = … | … | … | L ф III др = … |
IV драная | LIV др = … | … | … | L ф IV др = … |
V драная | LV др = … | … | … | L ф V др = … |
Итого | L др = … | … | … | L ф др = … |
В последней графе таблицы 2 записывается фактическая длина мелющей линии по каждой системе, исходя из выбранного типоразмера вальцовых станков и их количества. По каждому этапу и процессу в целом подсчитывается итог. В результате число вальцовых станков каждого типоразмера должно быть выражено целым числом. Желательно, чтобы при оснащении мукомольного завода было использовано не более двух типоразмеров станков.
Дата добавления: 2019-02-26; просмотров: 714; Мы поможем в написании вашей работы! |
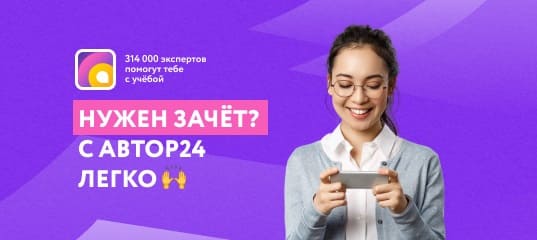
Мы поможем в написании ваших работ!