Примечание. Внутренний диаметр матрицы 406 мм, а ее ширина 165 мм.
Зазор между матрицей и роликами изменяют при помощи винтов, которые специальными рычагами поворачивают ось роликов. На рычагах нанесены стрелки, указывающие направление поворота этих рычагов для приближения роликов к матрице.
Два ножа, установлены с наружной стороны матрицы, срезают выходящие из нее отверстий гранулы. Положение ножей по отношению к матрице регулируют вращением специальных маховиков. При перегрузке или заклинивании матрицы срезаются предохранительные штифты, неподвижная ось вместе с фланцем поворачивается и воздействует на ролик конечного включателя, который выключает электродвигатели.
Матрица и вся зона прессования закрывается дверкой. Конечный выключатель на корпуса редуктора связаны с дверкой, отключает прессующую секцию при открытии дверки. Для получения гранул большой длины ножи снимают. За работой гранулятора наблюдают через смотровое окно. Два патрубка верхней части пресса предназначены для подсоединения его к аспирационной сети.
Прессующие ролики состоят из рабочей обечайки с рифлями на наружной поверхности, вращающихся на оси. Зазор в конических подшипниках регулируют при помощи гаек. С обоих концов ролика установлены уплотнительные сальники.
При гранулировании пар в смеситель подают через вентиль, после которого установлен и редукционный клапан, снижающий давление пара до (3,5…4,0)*105 Па. При давлении ниже 3,0*105 Па электроконтактный манометр автоматически перекрывает клапан и отключает электродвигатель пресса. Кроме того, в системе подачи пара для отделения воды установлен сепаратор пара и конденсатоотводчик. Для контроля давления пара установлен манометр.
|
|
Техническая характеристика пресс-гранулятора ДГ- I приведена в таблице 8.
Электродвигатели пресса сблокированы между собой. Всё электрооборудование смонтировано на панели управления. Непосредственно около пресса установлен щит управления с аппаратурой контроля и управления. Электрической схемой предусмотрено блокировка электродвигателя пресса.
Таблица 8-Техническая характеристика пресс-гранулятора ДГ-I
№ п/п | Наименование показателя | Значение показателя |
1 | Производительность, т/час | 7,0…10,0 |
2 | Расход пара, кг/с | 0,167 |
3 | Давление пара, МПа | 0,35…0,40 |
4 | Влажность гранул, % | 13…17 |
5 | Температура гранул после пресса, 0С | 50…80 |
6 | Мощность электродвигателей, кВт | 78 |
7 | Габаритные размеры, мм | 2200*1130*2250 |
8 | Масса, кг | 3230 |
Охладитель ДГ- II предназначен для охлаждения гранул. Состоит из колонки, разгрузочного устройства и вентилятора. Внутренние полости 1 колонки образованы двумя торцовыми стенками, внутри которых посекционно установлены сетки 2 и жалюзи 3 (Рисунок 20). Снаружи колонки проходят воздушные каналы 4 со специальными отверстиями для забора воздуха. Для приема и направления гранул в охладительную колонку в верхней ее части бункер 8 с крышкой, в которой имеются загрузочный 9 и аспирационный 10 патрубки. На стенке бункера установлены датчики уровня 11: нижний управляющий разгрузочным устройством; верхний - аварийный. В одной из торцовых стенок предусмотрено отверстие с диффузором для присоединения охладительной колонки к вентилятору, а в другой - отверстия для очистки закрытые дверками.
|
|
Рисунок 20-Охладительная колонка ДГ- II : 1 – полости; 2 – сетка; 3 – жалюзи; 4 – воздушные каналы; 5 – основание; 6 – крыльчатка; 7 – заслонки; 8 – бункер; 9,10 – патрубки; 11 – датчики уровня.
Колонка установлена на основании, в котором находится разгрузочное устройство, состоящее из двух вращающихся навстречу один другому валов с крыльчатками 6. На каждом валу расположена заслонка 7, с помощью которой регулируют производительность колонки. Привод разгрузочного устройства аналогичен приводу питателя пресса ДГ- I.
|
|
Измельчитель ДГ-III предназначен для измельчения гранул диаметром до 10 мм в крупку. Состоит из корпуса, установленных в нем двух вращающихся навстречу один другому валков (ведущего и ведомого), механизма регулирования валков и их привода. Гранулы поступают в приемное устройство, измельчаются валками, и полученная крупка удаляется через выпускное устройство. В корпусе расположены окна, закрытые крышками с предохранительными решетками, предназначенные для замера зазоров между валками и отбора проб после измельчения. В торцовых стенках корпуса предусмотрены предназначенные для установки валков продольные пазы. Привод валков состоит из электродвигателя, смонтированного на плите и расположенного на задней стенке корпуса, и клиноременной передаче. Перекидная заслонка, установленная внутри корпуса, позволяет при необходимости направлять поток мимо валков. Для регулирования зазора между валками предусмотрен для каждого валка механизм настройки, шпилька, шарнирно связанный с корпусом подшипника. При вращении маховика увеличивается или уменьшается зазор между валками. Амортизационные пружины, установленные между корпусами подшипников подпружиненного ведомого валка и опорой, рассчитаны на усилия необходимые для дробления гранул. Они одновременно предохраняют от поломки измельчитель при попадании между валками посторонних предметов. Валки рифленные: на ведущем рифли нарезаны по винтовой линии с наклоном к оси 20, а на ведомом – 870.
|
|
Ведущий валок через клиноременную передачу приводится во вращение от электродвигателя, а ведомый - через клиноременную передачу от ведущего. Ремни натягивают при помощи специального устройства.
6.2 Общее устройство оборудования ОПК-2
Оборудование для прессования кормов ОПК-2 предназначено для гранулирования комбикормов (см. Таблицу 9). Кроме того, на сушильных агрегатах травяной сечки можно получать гранулы из травяной муки или брикеты из травяной сечки (производительность оборудования – до 1,5 т/ч), а также брикеты из смесей сечки высушенных естественных и сеяных трав, соломы, балансирующих добавок и комбикормов (производительность до 2,5 т/ч).
Таблица 9-Техническая характеристика оборудования ОПК-2,0
№ п/п | Наименование показателя | Значение показателя |
1 | Производительность, кг | 6000 |
2 | Мощность электродвигателей, кВт | 143,8 |
3 | Влажность кормов, % | 15…17 |
4 | Габаритные размеры, мм | 11415* 6043* 8744 |
5 | Масса, кг | 11321 |
Оборудование ОПК-2 поставляется в следующих исполнениях: ОПК-2,0- универсальное – для брикетирования и гранулирования кормов: ОПК-2,0-1- для гранулирования комбикормов и травяной муки: ОПК-2,0-2- для брикетирования смесей.
ОПК-2,0 включает (Рисунок 21) пресс-гранулятор, смеситель-питатель, системы подачи кормов, накопления и дозирования, охлаждения и сортирования. Управление электроприводом осуществляется от двух электрошкафов.
Пресс - основная составная часть оборудования. Предназначен для осуществления основных технологических операций – гранулирования и
Рисунок 21-Технологическая схема оборудования ОПК-2,0: 1- загрузочный транспортер; 2-дозатор; 3- накопительный бункер; 4-транспортер крошки; 5, 8- вентиляторы; 6-циклон; 7-транспортер сечки; 9- камера предварительного сортирования; 10- охладительная колонка; 11-камера окончательного сортирования; 12- вибровыгружатель; 13- нория; 14- ленточный транспортер; 15- пресс; 16- система ввода пара; 17- смеситель-питатель; 18- система ввода воды.
брикетирования кормов. Состоит из редуктора, сменных прессующих сборочных единиц (для гранулирования и брикетирования), подъемника и электродвигателя. Редуктор и электродвигатель смонтированы на общей плите, их валы соединены муфтой.
Для перехода от гранулирования к брикетированию (или наоборот) нужно только заменить прессующие узлы.
Сборочная единица для гранулирования служит для приготовления гранул из комбикормов или травяной муки. Основные части: кольцевая матрица с радиальным отверстием, два прессующих вальца, блок направляющих лопаток, плита с муфтой для привода рабочих органов смесителя-питателя и приемник.
Матрица для брикетирования состоит из 44 отдельных сегментов, закрепленных между двумя дисками. В собранном виде сегменты образуют прессующие каналы, у которых три стенки имеют постоянную длину, а одна – переменную. Продолжением этой стенки служит металлическая пластинчатая пружина, позволяющая регулировать сопротивление продавливанию прессуемого корма через каналы и, тем самым, регулировать плотность приготавливаемых брикетов. Прижатие пружин к каналам осуществляется пружинным механизмом через специальный диск. При нажатии диском на концы пружин последние выправляются и образуют закрытое продолжение трапециевидных каналов.
Смеситель-питатель предназначен для непрерывного перемешивания увлажненного корма и принудительной подачи его в камеру прессования. Состоит из цилиндрического корпуса с открытием выводным концом и двумя загрузочными горловинами, консольного шнека и мешалки коллектора для подвода пара. Смеситель может перемешаться на опорных роликах по направляющим и в рабочем положении крепится к прессу фиксаторами.
Система накопления и дозирования состоит из шнековых транспортеров, накопительного бункера и шнекового дозатора, подающего, корм из бункера в выгрузной или возвратный шнек.
Система забора сечки предназначена для приема травяной и соломенной сечки и транспортирования ее в смеситель-питатель. Состоит из пневмотрубопроводов, заборника травяной сечки, вентилятора, циклона со шлюзовым затвором и цепочно-планчатого транспортера. Соломенная сечка загружается в пневмотрубопровод через шлюзовый затвор, а травяная сечка из сушильного агрегата – в заборник сечки. Оборудование в исполнении ОПК-2,0-1 системой забора сечки не комплектуется.
Системы подвода пара и охлаждения гранул аналогичны гранулятору ДГ.
Дата добавления: 2019-02-13; просмотров: 366; Мы поможем в написании вашей работы! |
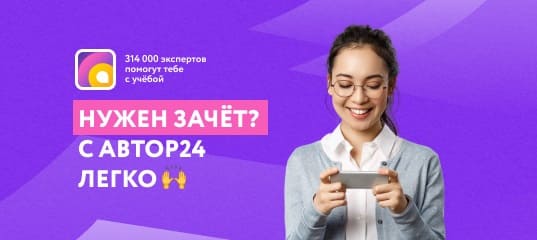
Мы поможем в написании ваших работ!