Общие сведения о процессе смешивания
Под смешиванием понимают процесс равномерного распределения частиц компонентов корма в общем его объеме, в результате чего получают однородную кормовую смесь. В технологических процессах приготовления кормов применяют, в подавляющем большинстве случаев, механическое смешивание. Устройства, с помощью которых осуществляется процесс смешивания, называют смесителями, а их рабочие органы мешалками.
Смесители кормов классифицируют по следующим основным признакам: по характеру и организации рабочего процесса, по основному назначению конструкции рабочих органов и частоте вращения.
По характеру процесса различают смесители порционного (периодического) и непрерывного действия. В зависимости от вида смешиваемых кормов смесители могут быть предназначены для приготовления сухих сыпучих (комбикормов), рассыпных влажных и жидких (консистентных) кормов. По организации рабочего процесса все смесители делятся на две большие группы: с вращающейся камерой и с неподвижной камерой, или транспортирующие.
К первой группе относятся барабанные, горизонтальные, вертикальные или наклонные смесители различного конструктивного исполнения.
Ко второй группе относятся мешалочные смесители. По конструкции рабочих органов – мешалок применяют смесители: для сыпучих кормов – шнековые, лопастные и ленточные; для жидких – турбинные, пропеллерные и лопастные; для рассыпных влажных (стебельных) кормов – шнековые и лопастные.
|
|
В зависимости от частоты вращения мешалок смесители делят на тихоходные и быстроходные. К тихоходным относятся смесители, у которых показатель кинематического режима меньше 30, а к быстроходным – у которых этот показатель больше 30. Мешалочные смесители по числу мешалок делят на одно – и двухвальные. Наиболее распространенными являются шнековые. Смесители последнего типа выполняют горизонтальными и применяют для смешивания всех видов сухих и влажных компонентов, за исключением жидких кормосмесей. В процессе работы компоненты кормов непрерывно загружаются в приемный бункер смесителя, интенсивно пермешиваются вращающимися внутри корытообразного корпуса шнеком или валом с лопастями, которые расположены по винтовой линии. При этом, слои корма, перемещаясь один относительно другого с различными окружными скоростями, проталкиваются к разгрузочному окну.
Смесители – запарники периодического действия С-12, С-7, С-2 предназначены для приготовления кормовых смесей влажностью (65…80)% из концентрированных, грубых кормов, корнеклубнеплодов, зеленой массы или силоса, травяной муки и различных добавок (см. Таблицу 1). В них можно проводить и запаривание кормов. Базовой моделью является смеситель-запарник С-12.
|
|
Смесители С-12 и С-7 выпускаются в двух исполнениях: для использования в кормоцехах (например, С-12-І) и для самостоятельного использования – С-12-ІІ (с загрузочным и выгрузным транспортерами (Рисунок 3).
2.2 Общее устройство смесителя С-12
Смеситель С-12 предназначен для приготовления сырых или запаренных кормовых смесей влажностью 65... 75% из предварительно измельченных кормов.
Таблица 1-Техническая характеристика смесителей-запарников типа С
№ п/п | Наименование показателя | С-12 | С-7-І | С-7-ІІ | С-2 |
1 | Производительность, т/ч без запаривания с запариванием | 10 5 | 9 2.9 | 9 2.9 | 4 2 |
2 | Производительность при выгрузке кормовых смесей, м3/ч | 40 | 35 | 35 | - |
3 | Продолжительность смешивания, мин | 15…20 | 15…20 | 15…20 | 15…20 |
4 | Продолжительность запаривания, мин | 60…70 | 50…65 | 50…65 | - |
5 | Вместительность смесительной камеры, м3 | 14 | 8 | 8 | 2.9 |
6 | Полезный объем, м3 | 12 | 7 | 7 | 2.5 |
7 | Установленная мощность электродвигателей, кВт | 13.37 | 11.37 | 15.57 | 8.5 |
8 | Частота вращения лопастей, мин-1 | 3.7 | 4.7 | 4.7 | 6 |
9 | Расход пара, кг/т | 160…200 | 160…200 | 160…200 | 160…200 |
10 | Неравномерность смешивания, % | 5…12 | 5…12 | 5…12 | 5…12 |
11 | Габариты, м | 4.2*2.9*2.4 | 3.6*2.4*2.8 | 3.9*8.7*3.4 | 3.4*4.4*1.6 |
12 | Масса, кг | 5200 | 3720 | 4670 | 2790 |
|
|
Рисунок 3-Принципиальн-технологическая схема работы смесителей-запарников: 1-загрузочный транспортер; 2-выгрузной шнек; 3-мешалка; 4-трубки-оросители; 5-выгрузной транспортер.
Он состоит (Рисунок 4) из следующих узлов: корпуса, парораспределителя 11, лопастных валов с мешалками 8 и 9, выгрузного шнека 10, выгрузной горловины с клиновой задвижкой, привода 5 и системы управления выгрузного шнека и задвижки.
Рисунок 4-Запарник-сместель кормов С-12: 1-крышка смесителя; 2-щит; 3-система управления шнеком и задвижкой; 4-зубчатые колеса; 5-редуктор привода; 6-натяжное устройство цепной передачи; 7-натяжное устройство; 8-лопастной вал левый; 9-лопастной вал правый; 10-выгрузной шнек; 11-парораспределитель; 12-система управления парораспределителями.
Корпус смесителя сварной конструкции. В нем размещаются две лопастные мешалки, вращающиеся навстречу друг другу. Каждая мешалка состоит из вала, на котором закреплено по восемь лопастей. Валы мешалок вращаются в подшипниках, закрепленных на торцевых стенках корпуса. На концах валов мешалок, с наружной стороны корпуса, насажены приводные цилиндрические зубчатые колеса 4, входящие в зацепление друг с другом. В нижней части корпуса под мешалками расположен выгрузной шнек 10. Лопастные мешалки и выгрузной шнек работают от одного привода, состоящего из электродвигателя и цилиндрического редуктора. На валу электродвигателя установлен четырехручьевой шкив, который приводит во вращение быстроходный вал редуктора.
|
|
Коллектор парораспределителя 11 снабжает паром две распределительные трубы, расположенные внизу, снаружи, вдоль обеих боковых стенок корпуса смесителя. Каждая распределительная труба пятью муфтовыми кранами соединена с пароподводящими патрубками. Один конец патрубков вварен в днище корпуса, а второй конец закрыт заглушкой, снимаемой только при очистке системы. Включение и выключение подачи пара производится переключателем. В верхней части корпуса приварены решетки для установки съемных щитов 2 и крышки 1. В крышке имеется смотровой люк с предохранительной сеткой для наблюдения за смешиванием кормов и люк для загрузки кормов. Этот люк имеет шиберную задвижку с тягой.
Система управления выгрузкой кормов служит для синхронного включения и выключения выгрузного шнека и подъема или опускания клиновой задвижки.
Она состоит (Рисунок 5) из электродвигателя 17 с редуктором 16, винта
Рисунок 5-Кинематическая схема смесителя С-12: 1,17-электродвигатели; 2,3-ведущий и ведомый шкивы; 4,16-редукторы; 5,8,9,-звездочки; 6,7-шестерни;10-полумуфта; 11-пружина; 12,22-рычаги; 13-стальной трос; 14-шнек; 15-мешалки; 18-винт; 19-шток; 20-выключатель; 21-копир; 23-задвижка.
18, связанного со штоком 19 и копиром 21, стального троса 13 с обводными роликами, рычагов управления 12 и 22, трех концевых выключателей 20 и кулачковой полумуфты 10 с вилкой включения выгрузного шнека 14, Один конец вилки включения двумя пальцами шарнирно соединен со шлицевой кулачковой полумуфтой, находящейся на приводном валу шнека, другой шарнирно связан с опорой. Вилка перемещается при помощи троса 13, который одним концом прикреплен к ее рычагу 12, а вторым через обводные ролики - к рычагу управления 22.
Для контроля температуры нагрева запариваемой массы на корпусе смесителя установлен специальный аэротермометр УТ-200Е. Шкала термометра имеет три интервала: от 0 до 750С (белого цвета); от 75 до 950С (зеленого цвета); от 95 до 1200С (красного цвета).
2.3 Работа смесителя С-12
Кормосмесь разгружают следующим образом. При работающих мешалках включают электродвигатель 17 управления задвижкой 23. Шток 19 поднимается вверх, тянет за собой задвижку и открывает разгрузочную горловину шнека. Одновременно рычаг 22 освобождает трос и рычаг 12.
Электрическая схема смесителя выполнена таким образом, что во время прохождения копира 21 около среднего конечного выключателя главный привод смесителя останавливается и зубчатая полумуфта 10 под действием освобожденной пружины 11 плавно входит в зацепление второй полумуфтой и звездочкой 9 включает шнек. После зацепления полумуфт копир освобождает средний выключатель, при этом включается снова привод мешалок, но уже с включенным разгрузочным шнеком. Начинается процесс разгрузки корма, а копир, дойдя до верхнего конечного выключателя, останавливает электродвигатель системы управления. Затем копир переводят в первоначальное положение.
Технологический процесс смешивания кормов без запаривания. Для получения кормосмеси заданной влажности в смеситель сначала заливают воду по подведенному заранее водопроводу. Количество воды определяется расчетным путем. Измельченные компоненты корма в соответствии с заданным рационом загружают из кормоприготовительных машин в смеситель через загрузной люк. Все компоненты кормосмеси можно загружать одновременно. Заполнив емкость смесителя на 30%, включают в работу мешалки. Остальную часть кормов загружают при работающих мешалках. Если готовят кормовые смеси, в которые входят солома и силос, коэффициент заполнения смесителя составляет 0,6, для других смесей — 0,8.
При смешивании кормосмеси лопасти одной мешалки начинают перемещать корм в одну сторону, а лопасти другой мешалки в другую сторону, т. е. создаются два встречных потока. Кроме того, масса перемещается и в плоскости лопастей. В результате многократных перемещений происходит хорошее смешивание кормов. После окончания загрузки смешивание длится (10...15) мин. Приготовленную смесь выгружают в кормораздатчик или транспортные средства. Хранить приготовленные корма в смесителе не рекомендуется.
Технологический процесс смешивания кормов с запариванием. При запаривании картофеля и концентратов в смеситель сначала заливают (60... 70)% воды от общего расчетного количества. Включают подачу пара. Вода нагревается до температуры 90°С. В нагретую воду загружают все компоненты, которые должны быть запарены. Во время запаривания мешалки должны работать, так как находящийся в движении корм быстрее запаривается.
Продолжительность запаривания зависит от вида и объема корма, степени его измельчения, температуры пара, производительности парового котла и других условий. В каждом конкретном случае продолжительность запаривания надо определять расчетным или опытным путем. В среднем продолжительность запаривания в смесителе С-12 составляет (1...3) ч. При запаривании грубых кормов их предварительно измельчают до (20...30) мм и при загрузке смачивают водой из расчета (80...100) л воды на 100 кг корма.
Для запаривания грубых кормов в смеситель подают пар (250...300) кг/ч при давлении (0,025...0,035) МПа. Запаривание длится (1...2) ч. По окончании запаривания необходимо перекрыть муфтовые краны и вентили на паропроводе и выдержать кормосмесь в течение (40...60) мин для дозапаривания. После этого доливают основную воду для охлаждения корма и добавляют другие компоненты в соответствии с заданным рационом.
2.4 Техническое обслуживание смесителя С-12
При ежедневном техническом обслуживании очищают, проверяют и подтягивают все болтовые крепления, устраняют течь, смазывают узлы и детали в соответствии с картой смазки, промывают емкости бункера и мешалок, а также убеждаются в правильности натяжения приводных ремней, проверяют состояние смесителя и устраняют, в случае необходимости, дефекты.
Периодическое техническое обслуживание смесителя-запарника проводят через 300 часов работы. Оно включает подготовку обслуживающим персоналом машины к техническому осмотру, проведение очередного технического обслуживания и настройку машины на эксплуатационный режим работы. Периодическое техническое обслуживание включает операции ежедневного технического обслуживания, а также дополнительные операции по смене масла, проверке, регулировке и настройке механизмов и узлов на нормальную работу, выявление и устранение дефектов в работе машины.
Регулировки. Зазор между вершинами кулачковых полумуфт проверяют ежедневно. В выключенном положении он должен составлять 48 мм. Зацепление регулируют винтом натяжения троса. Зазор между роликами вилки включения и буртиком кулачковой полумуфты, когда муфта включена, должен быть в пределах (5...10) мм. Натяжение клиноременной передачи регулируют так, что при нажатии в средней части ремня с усилием (0,10...0,15) кН прогиб был (20...30) мм.
2.5 Общее устройство и работа смесителя С-30
К смесителям непрерывного действия относится, в частности, высокопроизводительныйдвухвальный лопастной смеситель С-30 (см. Таблицу 2). Он предназначен для получения однородной кормовой смеси из предварительно измельченных грубых, сочных и концентрированных кормов с добавлением жидких питательных растворов (мелассы, карбамида и других). Допустимая максимальная длина частиц: грубых кормов – до 50 мм; силоса и сенажа – до 30 мм; корнеклубнеплодов – до 15 мм.
Таблица2 -Техническая характеристика С-30
№ п/п | Наименование показателя | Значение показателя |
1 | Производительность, т/ч | 15…28 |
2 | Мощность электродвигателя, кВт | 5,5/7,5 |
3 | Рабочий орган смесителя: диаметр вала, мм длина, мм максимальная частота вращения, мин-1 | 400 2000 285 |
4 | Полезная емкость бункера, м3 | 1,03 |
5 | Габариты, мм | 2340*930*1740 |
6 | Масса, кг | 580/877 |
Смеситель (Рисунок 6) состоит из корпуса 1, двух лопастных мешалок 2 и системы привода (электродвигатель 5 с редуктором 6 и ременной передачей).
Рисунок 6 -Двухвальный лопастной смеситель С-30: 1-корпус; 2-лопастная мешалка; 3-загрузочный бункер; 4-крышка; 5-электродвигатель; 6-шестеренчатый редуктор; 7-выгрузная горловина.
Корпус корытообразного типа, в котором расположены два лопастных вала. Лопасти мешалок на каждом валу расположены по винтовой линии под углом 450 по направлению к выгрузной горловине 7 и повернуты друг относительно друга на 1800. Угол поворота лопасти относительно вала можно регулировать. Лопасти перекрывают друг друга на 110 мм. Спаренные лопастные мешалки связаны между собой зубчатым зацеплением, обеспечивающим синхронное вращение их во встречном направлении с частотой (270…285) мин-1. Для изменения частоты вращения валов предусмотрены сменные венцы шестерен.
Корма, подлежащие смешиванию, поступают в приемную часть корпуса с транспортеров, которые подают их непрерывным потоком на две лопастные мешалки. Последние интенсивно перемешивают кормовые компоненты и подают готовую смесь к выгрузной горловине 7 и далее на скребковый или шнековый транспортер кормоцеха.
Контрольные вопросы
1. Каково назначение и устройство смесителя С-12?
2. Как обеспечивается синхронность работы выгрузного шнека и клиновой задвижки?
3. Как осуществляется технологический процесс смешивания и запаривания кормовых смесей?
4. Какие различия смесителей С-12, С-7 и С-2?
5. Почему производительность с запариванием меньше, чем без запаривания?
АГРЕГАТ ДЛЯ ПРИГОТОВЛЕНИЯ
ЗАМЕНИТЕЛЯ МОЛОКА АЗМ-0,8
Цель: Изучение устройства и работы агрегата для приготовления заменителя молока АЗМ-0,8.
ПРОГРАММА РАБОТЫ
1. Изучить устройство и работу агрегата для приготовления заменителя молока АЗМ-0,8 и его основных сборочных единиц.
2. Сравнить типы рабочих органов
3. Изучить какие компоненты включает в себя заменитель молока.
4. Проанализировать техническую характеристику агрегата.
Общие сведения
Агрегат АЗМ-0,8 предназначен смешивания жидких порошкообразных компонентов для приготовления заменителя молока телятам и рассчитан на обслуживание телятника на 200...300 голов (см. Таблицу 3).
Агрегат может быть использован для приготовления различных высокодисперсных пищевых эмульсий и как нагреватель воды для технических нужд.
Приготовленный в агрегате высококачественный заменитель молока дает возможность высвободить большое количество цельного молока. Простота обслуживания, низкие энергоемкость и трудоемкость, стерильность продукта - все это способствует значительному экономическому эффекту при использовании агрегата АЗМ-0,8 в хозяйствах. Агрегат может работать с установкой для выпойки телят УВТ-20 или с любыми другими средствами, предназначенными для выпойки молодняка сельскохозяйственных животных.
Общее устройство и работа
Агрегат для приготовления заменителя молока АЗМ-0,8 (Рисунок 7) состоит из смесителя 6,шнека 7, установки насоса-эмульсатора 15,фильтра 18,бачка 9,трубопроводов и соединительной арматуры для заменителя молока, трубопроводов и соединительной арматуры для воды и пара, электрооборудования.
Таблица 3-Техническая характеристика АЗМ-0,8
№ п/п | Наименование показателя | Значение показателя |
1 | Количество продукта в одной порции, кг | 800±20 |
2 | Продолжительность полного цикла приготов ления продукта, не более, ч | 3,5 |
3 | Масса, кг | 800 |
4 | Рабочая вместимость смесителя, не менее, л | 820 |
5 | Расход пара для приготовления порции про дукта, не более, кг | 100 |
6 | Температура нагрева продукта, не более, 0С | 90 |
7 | Давление пара при запаривании кормов, не более, кПа | 68,6 |
8 | Температура нагрева 400 л воды для технических нужд, не более, 0 С | 90 |
9 | Расход пара для нагрева 400 л воды, не более, кг | 80 |
10 | Расход проточной воды при охлаждении пор ции продукта, не более, л | 1500 |
11 | Расход воды для мойки и чистки агрегата, не более, л | 600 |
12 | Температура нагрева 600 л воды для мойки и чистки агрегата, не более, 0 С | 70 |
13 | Расход пара для нагрева 600 л воды, не бо лее, кг | 80 |
14 | Установленная мощность, кВт | 5,65 |
15 | Габаритные размеры, мм | 2360*1295*2630 |
16 | Характеристика рабочих узлов, органов агрегата: подача насоса-эмульсатора, л/ч частота вращения насоса-эмульсатора, с-1 подача шнека, кг/ч частота вращения шнека, мин -1 частота вращения мешалки смеситетеля, с-1 | Не менее 2500 25 Не менее 1000 432 0,9...0,97 |
Смеситель 6состоит из двух цилиндрических обечаек - наружной и внутренней; воздушная рубашка между ними служит термоизолятором во время запаривания. При охлаждении содержащегося в смесителе продукта через рубашку проходит холодная вода. Внутри емкости смесителя установлена мешалка 3,верхний конец которой соединен с валом редуктора. Вращение мешалки осуществляется от привода, смонтированного на раме. На внутренней поверхности смесителя при помощи кронштейнов 33закреплены две неподвижные лопасти 4.Смеситель закрывается двумя крышками. Первая крышка предназначена для наблюдения за процессом приготовления заменителя молока, закреплена шарнирно и фиксируется в открытом положении специальным устройством. На второй крышке размещены корпус подшипника для крепления вала мешалки, рама для крепления привода мешалки и приемная горловина для загрузки шнеком растительных компонентов комбикорма. Загрузочная горловина после окончания загрузки закрывается заслонкой. На наружной обечайке смесителя установлены
Рисунок 7-Агрегат для приготовления заменителя молока АЗМ-0,8
Бункер загрузочный; 2-вентиль слива воды из кольцевой ёмкости; 3-мешалка лопастная; 4-мешалка неподвижная; 5-кожух; 6-смеситель-запарник; 7-шнек загрузочный; 8-труба для отвода избыточных паров; 9- бачок для жиров; 10-труба; 11- указатель уровня; 12- термометр; 13- вентиль; 14-кран; 15-насос-эмульсатор; 16-рукав выдачи; 17-кран трёхходовой; 18-фильтр; 19-вентиль; 20-кран трёхходовой; 21-клапан обратный; 22рукав для обрата; 23-шнек; 24-вентиль; 25-мешалка.
термометр 12 и указатель уровня 11.В нижней части смесителя приварена рама для крепления насоса-эмульсатора и шнека.
Привод, предназначенный для передачи крутящего момента мешалке, устанавливается вертикально в верхней части смесителя и состоит из электродвигателя и редуктора. Редуктор представляет собой трехосную двухступенчатую цилиндрическую передачу. В корпусе и крышке редуктора имеются отверстия для заливки и слива масла, закрываемые резьбовой пробкой и сапуном, в котором имеется отверстие для сообщения внутренней полости редуктора с атмосферой. Уровень масла в редукторе определяется посредством контрольного отверстия, закрытого резьбовой пробкой.
Шнек предназначен для загрузки в смеситель комбикормов и состоит из загрузочного бункера 1, мешалки 25, расположенной в бункере, кожуха шнека 5и шнека 23. Внутри бункера установлена сетка, предотвращающая попадание в бункер инородных предметов. Шнек установлен вертикально. Привод шнека осуществляется от электродвигателя через клиноременную передачу. Привод мешалки осуществляется от вала шнека через одноступенчатую цилиндрическую зубчатую передачу. На кожухе шнека имеется крышка, открыв которую можно очистить кожух от комбикорма. Для регулирования подачи корма из бункера служит заслонка.
Установка насоса-эмульсатора 15 предназначена для эмульсирования смеси, подачи обрата в смеситель, перекачивания, выдачи готового продукта и для циркуляционной промывки составных частей агрегата.
Установка насоса-эмульсатора состоит из рамы насоса-эмульсатора, электродвигателя, соединительной муфты, щитка и соединительного патрубка. Насос-эмульсатор состоит из корпуса, вала, крыльчатки, диска неподвижного, диска подвижного, пальцев и рассекателей. Корпус эмульсатора и крышка эмульсатора образуют полость, разделенную неподвижным диском на две камеры. В первой камере вращается крыльчатка, создающая напор, необходимый для проталкивания смеси через рабочую камеру. На одном диске укреплены рассекатели, на другом — пальцы. Подвергаясь интенсивным ударам и перемешиванию, первичная эмульсия дробится на мельчайшие частицы. Вторичная тонкодисперсная эмульсия выходит через отверстие в крышке по трубопроводу. Подвижный диск и крыльчатка посажены на шлицевый вал и крепятся на нем гайкой. Выходной конец вала установлен в корпусе на конических подшипниках, которые с наружной стороны закрываются крышками с прокладками. Уплотнение вала осуществляется резиновыми манжетами.
Фильтр 18предназначен для предотвращения попадания в насос-эмульсатор и трубопроводы инородных тел. Фильтр состоит из корпуса, фильтрующего элемента, крышки, которая крепится к корпусу при помощи скобы. Уплотнение корпуса и крышки осуществляется прокладкой. Фильтр крепится к насосу-эмульсатору и трубопроводам при помощи гаек.
Бачок 9 предназначен для заливки в него смеси растительных и животных жиров, биостимуляторов (микроэлементов и антибиотиков). Бачок при помощи кронштейнов крепится к смесителю. Патрубок в нижней части бачка служит для соединения с всасывающей полостью насоса-эмульсатора посредством трубопровода, на котором установлен кран, регулирующий подачу смеси из бачка.
Трубопроводы и соединительная арматура предназначены для соединения составных частей агрегата в единую технологическую линию, по которой циркулирует заменитель молока, и состоят из трехходовых кранов, гаек, конусов, штуцеров, колен, разводки и рукава. Трубопроводы и соединительная арматура для воды и пара предназначены для подключения агрегата к водопроводной и паропроводной системам и состоят из тройников, сгонов, муфт, труб, вентилей, контргаек и угольников. Обратный клапан служит для предотвращения забивания паропроводящей системы кормовой смесью в случае падения давления пара, подаваемого в смеситель. Состоит из корпуса, прокладки, золотника и крышки. Обратный клапан должен быть установлен так, чтобы золотник при прохождении пара срабатывал в вертикальной плоскости. Стрелка на корпусе указывает направление подачи пара.
Электрооборудование агрегата АЗМ-0,8 подключается к сети переменного тока напряжением 380/220 В. В состав электрооборудования агрегата входят шкаф управления, электродвигатель насоса-эмульсатора мощностью 4,0 кВт, электродвигатель мешалки мощностью 1,1 кВт, электродвигатель шнека мощностью 0,55 кВт. Шкаф управления сварной конструкции, пылевлагозащищенного исполнения, устанавливается на стене внутри помещения на расстоянии (1,5…2) м от агрегата. На боковой стенке шкафа управления установлены пакетный выключатель ПВМЗ-25, предназначенный для подачи и отключения питания, посты управления ПКЕ122-2 и ПКЕ122-3, предназначенные для пуска и остановки механизмов агрегата. Внутри шкафа управления на панели установлены: автоматические выключатели АП50-ЗМ для защиты электродвигателей от токов короткого замыкания; магнитные пускатели ПМЕ-112 и ПМЕ-114 для пуска и защиты электродвигателей от перегрузок; предохранитель ПРС-6-П для защиты цепей управления оттоков короткого замыкания; набор зажимов малогабаритный КМ-1-10-12.
Технологический процесс (Рисунок 8). Агрегат для приготовления заменителя молока АЗМ-0,8 смешивает комбикормовые смеси с водой, запаривает полученную смесь, осолаживает ее, смешивает смесь с обратом, растительными и животными жирами, биостимуляторами (микроэлементами, витаминами и антибиотиками), эмульсирует грубодисперсную смесь и выдает готовый продукт.
Заменитель молока готовят по установленной рецептуре из расчета на одно кормление телят. Рецептура кормовых компонентов заменителей молока может быть разнообразной, в зависимости от наличия компонентов кормов в хозяйстве. Однако подбор компонентов должен отвечать требованиям, предъявленным к заменителям молока. В состав заменителя молока входят сухие кормовые смеси, «снятое молоко» (обрат), биостимуляторы (микроэлементы, витамины, антибиотики), сахар, соль, мел, рыбий жир и другие.
Сухие комбинированные смеси из загрузочного бункера 6направляются шнеком 7в смеситель-запарник 9. «Снятое молоко» (обрат) закачивается в смеситель-запарник насосом-эмульсатором 14при помощи гибкого рукава. Вода подводится в нижнюю часть смесителя из водопроводной сети. Смесь нагревают паром, подводимым в нижнюю часть смесителя. Эмульсирование, выдача готового продукта и циркуляционная промывка трубопроводов для заменителя молока производятся насосом-эмульсатором, имеющим индивидуальный привод от электродвигателя. Смесь растительных и животных жиров, биостимуляторов (микроэлементов и антибиотиков) и других компонентов, предусмотренных рецептом заменителя молока, заливается в бачок 10и подается в смеситель 9через фильтр 17.
Рисунок 8-Принципиально-технологическая схема агрегата для приготовления заменителя молока АЗМ-0,8: 1-воронка; 2,11-трубопроводы; 3,4,13,15,18,19,20-вентили; 5-загрузочный ковш; 6-бункер; 7-шнек; 8-указатель уровня; 9-запарник-смеситель; 10-бачок; 11-трубопровод; 12-термометр; 14-насос-эмульгатор; 16-выпускной шланг; 17-фильтр; 21-мешалка.
Подготовка агрегата к работе
Открывают вентиль и заполняют емкость смесителя холодной водой в количестве 400 л, после чего вентиль закрывают. Количество залитой в смеситель воды определяют по указателю уровня. Запускают электродвигатель мешалки, открывают заслонку, нажатием кнопки запускают электродвигатель загрузочного шнека и постепенно засыпают комбикорм в бункер. Из бункера комбикорм шнеком подается в смеситель. После окончания загрузки комбикормов в смеситель отключают электродвигатель привода шнека, закрывают заслонку. При этом мешалка остается включенной. При вращении мешалки происходит смешивание комбикормов с водой и образование равномерной по консистенции смеси. Для подогрева смеси открывают вентиль, пар поступает в смеситель и нагревает смесь до температуры (85...90)0С. Контроль за температурой нагрева смеси ведут по термометру 12. После окончания подогрева смеси закрывают вентиль, прекращают подачу пара в смеситель. Следующий процесс обработки — осолаживание (пропаривание) растительных компонентов комбикормов - начинается при достижении смесью температуры 700С и продолжается при дальнейшем ее нагревании до (85...90)0С. Осолаживание длится не менее 1 ч после достижения смесью температуры 900С.
Во время осолаживания каждые (10...15) мин нажатием кнопки включают электродвигатель привода мешалки в работу на (4...5) мин. После окончания процесса осолаживания заливают в смеситель обрат («снятое молоко»). При наличии в хозяйстве свежего, качественного, непастеризованного обрата кормовую смесь после осолаживания сразу охлаждают холодной водой, открыв вентиль 13. Обрат в смеситель закачивают насосом-эмульсатором 15в такой последовательности: рукав 22 опускают в емкость с обратом; трехходовые краны 20и 17устанавливают в положение «смеситель-насос-эмульсатор-смеситель»; нажимают кнопку и запускают электродвигатель насоса-эмульсатора. Агрегат при этом работает по замкнутому циклу. При достижении насосом-эмульсатором полной производительности (контролируют по истечению смеси из патрубка внутри емкости) трехходовой кран 20 переключают в положение «емкость для обрата-насос-эмульсатор». Насос-эмульсатор начинает подавать обрат, агрегат работает по циклу «емкость для обрата-насос-эмульсатор-смеситель». Таким образом, подают в смеситель обрат в количестве, соответствующем установленной рецептуре. Контроль ведут по указателю уровня 11. После окончания заливки обрата нажимают кнопку и выключают электродвигатель насоса-эмульсатора. После этого охлаждают кормовую смесь до температуры (50...55)0С. Для этого открывают вентиль 19 и направляют холодную воду в рубашку смесителя. Остальные вентили оставляют закрытыми. При охлаждении смеси до температуры (50...55)0С вентиль 18закрывают.
Во вспомогательной емкости (ведре) приготовляют в соответствии с рецептом смесь растительных и животных жиров, витаминов, микроэлементов и антибиотиков на подогретом обрате или кипяченой воде и заливают в бачок 9.Для подачи смеси из бачка 9в смесителе устанавливают трехходовые краны 20и 17в положение «смеситель-эмульсатор-смеситель», кран 18 устанавливают в положение «для выдачи» и, нажав кнопку, включают электродвигатель насоса-эмульсатора. При этом агрегат будет работать по замкнутому циклу («смеситель-эмульсатор-смеситель»). Смесь из емкости будет засасываться насосом-эмульсатором и подаваться обратно в емкость с одновременным засасыванием смеси из бачка. Одновременно с подачей жировой смеси в смеситель проводится эмульсирование смеси, т. е. дробление жировой смеси на мелкие частицы и равномерное распределение их по всему объему продукта. Эмульсирование должно длиться (15...20) мин до полного выхода жировой смеси из бачка. После окончания эмульсирования нажатием кнопки выключают электродвигатель насоса-эмульсатора, закрывают кран 14(см. рисунок 7), затем, не выключая электродвигатель мешалки, открывают вентиль впуска холодной воды в рубашку и охлаждают смесь до температуры (35…38)0С. После охлаждения нажимают на кнопку и выключают электродвигатель мешалки.
Выдачу готового продукта при ручной выпойке производят через гибкий рукав во фляги или другие емкости. При механизированной выпойке гибкий рукав подключают к трубопроводу для забора продукта. Для выдачи готового продукта устанавливают трехходовой кран 17в положение «эмульсатор- выдача», а трехходовой кран 20— в положение «смеситель-эмульсатор» и, нажав на кнопки, включают электродвигатели мешалки и насоса-эмульсатора. Приготовленный заменитель молока выдается по потребности. После окончания выдачи готового продукта, нажав на кнопки, выключают электродвигатели приводов мешалки и насоса-эмульсатора, тщательно промывают агрегат. Для этого открывают вентили 13 и 19 (см. рисунок 8) и заполняют смеситель холодной водой. После заполнения смесителя водой закрывают вентили 13 и 19 испускают воду из рубашки смесителя. Затем открывают паровой вентиль 24и подогревают воду в смесителе до температуры 700С. Температуру нагрева воды контролируют термометром 12.
Агрегат промывают по двум циклам: 1-й цикл — трехходовые краны 17и 20 устанавливают в положение для перекачивания воды из смесителя в эмульсатор и снова в смеситель и, нажав кнопку, запускают электродвигатель насоса-эмульсатора. Продолжают промывку таким образом в течение трех минут. При этом промываются трубопроводная арматура, смеситель, фильтр, Насос-эмульсатор; 2-й цикл — устанавливают трехходовые краны 17 и 20в положение для выдачи продукта и сливают воду в канализацию. После промывки агрегата промывают бачок 9 (см. рисунок 8), снимают крышку фильтра, извлекают сетку, промывают, после чего фильтр собирают.
После этого заливают в смеситель горячий щелочной раствор и промывают им агрегат по двум циклам, изложенным выше, затем сливают раствор и окончательно промывают агрегат горячей водой. При механизированной промывке агрегата АЗМ-0,8 используется насос-эмульсатор и емкость смесителя. Для этого в емкость смесителя заливают щелочной раствор в количестве 600л и подогревают его паром до температуры 700С. Для подачи пара в емкость смесителя необходимо закрыть вентиль 19 и трехходовой кран 20, вентиль 24 — открыть. Верхнюю часть внутренней поверхности смесителя промывают специальной щеткой, прикладываемой к агрегату. Возможна механизированная промывка верхней части внутренней поверхности смесителя. Для этого щетку присоединяют посредством переходного элемента к рукаву 16. При перекачивании обеспечивают одновременную подачу жидкости в колено 10и рукав со щеткой установкой рукоятки крана 17в нужное положение.
Техническое обслуживание
При ежедневном техническом обслуживании (ЕТО) очищают наружные и внутренние поверхности агрегата от остатков корма; проверяют состояние затяжки резьбовых соединений, исправность заземления, убеждаются в отсутствии посторонних предметов на агрегате, наличии подтеканий смазки через уплотнения, посторонних шумов и стуков при работе агрегата, смазки в редукторе привода мешалки.
При первом техническом обслуживании (ТО- 1) через 60 ч работы выполняют все работы ежедневного технического обслуживания. Кроме этого, смазывают подшипники в соответствии со схемой смазки, проверяют натяжение ремней клиноременной передачи шнека, надежность крепления лопастей мешалки смесителя и шнека, крепления пальцев и рассекателей насоса-эмульсатора, крепления электроаппаратов, состояние контактов магнитных пускателей.
При втором техническом обслуживании через 240 ч работы выполняют все работы ежедневного и технического обслуживания ТО-1. Кроме этого, дополнительно проверяют состояние изоляции электродвигателей привода мешалки, шнека, насоса-эмульсатора, состояние подшипников электродвигателей привода мешалки, шнека, насоса-эмульсатора; заземление электродвигателей и агрегата, состояние покраски агрегата.
Контрольные вопросы
1. Объясните принцип действия и технологический процесс агрегата для приготовления заменителя молока АЗМ-0,8.
2. Назовите основные сборочные единицы агрегата и объясните их устройство.
3. Расскажите о порядке подготовки агрегата к работе.
4. Перечислите основные операции ежедневного и периодического технических обслуживаний агрегата.
4 ИЗМЕЛЬЧИТЕЛЬ-СМЕСИТЕЛЬ ИСК-3.
КОМПЛЕКТ ОБОРУДОВАНИЯ КОРК-15
Цель: Изучить назначение, устройство и технологический процесс измельчителя-смесителя ИСК-3 и использования в комплекте оборудования КОРК-15".
Программа работы.
1. Изучить назначение, устройство, отличительные особенности и компоновки узлов, рабочих органов различного исполнения ИСК-3.
2. Ознакомиться с технической характеристикой, порядком работы ИСК-3.
3. Разобраться с применением измельчителя-смесителя в линии ЛИС-3 и комплекте оборудования КОРК-15.
4. Ответить на контрольные вопросы.
4.1 Общие сведения о смесителе-измельчителе
Измельчитель-смеситель (см. Таблицу 4) предназначен для измельчения
соломы и других грубых кормов, а также для смешивания кормов в технологических линиях, оснащенных питателем соломы. Измельчители-смесители могут применяться как самостоятельные машины, а также в технологических линиях кормоцехов.
Таблица 4 -Техническая характеристика ИСК – 3
№ п/п | Наименование показателя | Значение показателя |
1 | Производительность, т/ч: при измельчении соломы при смешивании кормов | 4,0 – 5,0 20,0 |
2 | Масса, кг | 1295 - 2910 |
3 | Мощность, кВт | 37,0 – 41,4 |
4 | Удельный расход электроэнергии, кВт/ч: при измельчении при смешивании | 9,2 – 10,3 1,8 – 2,1 |
5 | Частота вращения ротора, мин-1 | 930 - 980 |
6 | Габаритные размеры, мм | 7430*1750*1620 |
В исходном сырье, поступающем в измельчители-смесители должны отсутствовать посторонние предметы (камни, стекло, металлические части, куски древесины и т. п.), которые смогут вызвать поломку или остановку измельчителей-смесителей.
В грубом корме, идущем на измельчение, частицы длиной до 200 мм, должны составлять не менее 80% всей массы. Подготовка отдельных кормов, предназначенных для образования кормосмесей, должны удовлетворять следующим требованиям:
Грубые корма для КРС - должны быть измельчены на длину частиц (30-50) мм, для овец - на длину до 30 мм, в количестве не менее 80% от общей массы.
Корнеклубнеплоды должны быть очищены от загрязнений и измельчены. Остаточная загрязненность не более 3%. Размеры частиц измельченных корнеклубнеплодов - не более 15 мм.
Сенаж и силос должны соответствовать требованиям ГОСТ 23637-79 и ГОСТ 23638-79.
Измельчители-смесители разработаны в шести исполнениях (см. Таблицу 5).
Таблица 5-Характеристика исполнений
Исполнение | Характеристика | Назначение |
ИСК-3 ИСК-3-1 ИСК-3-2 ИСК-3-3 ИСК-3-4 ИСК-3-5 | Измельчитель-смеситель с выгрузным транспортером и блоками РУС. Измельчитель-смеситель без транспортеров и блоков РУС. Смесители с выгрузным транспортером, без блоков РУС. Измельчитель-смеситель с выгрузными и загрузочными транспортерами и блоками РУС. Измельчитель-смеситель с выгрузным транспортером, без блоков РУС. Измельчитель-смеситель с выгрузным и разгрузочным транспортерами, без блоков РУС. | Измельчение, смешивание и выгрузка, самостоятельное изделие. Измельчение, смешивание для технологических линий кормоцехов. Смешивание и выгрузка для технологических линии кормоцехов. Прием, измельчение, смешивание и выгрузка, самостоятельное изделие. Измельчение, смешивание и выгрузка для технологических линий кормоцехов. Прием, измельчение, смешивание и выгрузка для технологических линии, кормоцехов. |
Устройство и работа
Измельчитель-смеситель ИСК-3 состоит из следующих составных частей: измельчителя-смесителя кормов; разгрузочного транспортера со стойкой; комплектных устройств управления типа блоков РУС-3.
Измельчитель-смеситель ИСК-3-1 состоит из измельчителя-смесителя кормов. Измельчитель-смеситель ИСК-3-2 состоит из следующих составных частей: измельчителя-смесителя кормов (поставляемого в режиме смешивания) разгрузочного транспортера со стойкой.
Измельчитель-смеситель ИСК-3-3 состоит из следующих составных частей: измельчителя-смесителя кормов; разгрузочного транспортера со стойкой; загрузочного транспортера со стойкой; загрузочного транспортера со стойкой; комплектных устройств управления типа блоков РУС 3.
Измельчитель-смеситель ИСК-3-4 состоит из следующих составных частей: измельчителя-смесителя кормов; разгрузочного транспортера со стойкой.
Измельчитель-смеситель ИСК-3-5 состоит из следующих составных частей: измельчителя-смесителя кормов; разгрузочного транспортера со стойкой; загрузочного транспортера со стойкой.
Технологический процесс (Рисунок 9) для различных исполнений отличается друг от друга.
Для исполнений ИСК-3; ИСК-3-2; ИСК-3-4.
Грубый корм в измельчитель-смеситель подается транспортером. Для подачи грубого корма на загрузочный транспортер может быть использован
питатель соломы ПС-Ф-6.
В измельчителе-смесителе 2 корм измельчается посредством ножей и противорезов, а затем крыльчаткой выбрасывается на выгрузной транспортер.
Для исполнения ИСК-3-1 подача и выгрузка корма производится имеющимися в хозяйстве транспортерами.
Для исполнений ИСК-3-3, ИСК-3-5.
Грубый корм транспортером 1 подается в рабочую камеру измельчителя-смесителя 2, где измельчаются посредством ножей и противорезов, а затем крыльчаткой выбрасывается на выгрузной транспортер 5. Для подачи грубого корма на транспортер 1 может быть использован питатель соломы ПС-Ф-6. Отделение твердых включений (камни, металлические части и т. п.) происходит в головке транспортера 1 за счет сил инерции.
Твердые включения падают на подпружиненную заслонку 3 и удаляются наружу, очистка подпружиненной заслонки осуществляется подачей воздуха крыльчатки. Подача воздуха регулируется при помощи заслонки 4.
Рисунок 9-Технологическая схема измельчителя-смесителя (обозначения в тексте).
Для получения различных кормовых смесей (во всех исполнениях) компоненты корма в соответствующих порциях одновременно подают в рабочую камеру. При работе в режиме смешивания на рабочую камеру вместо противорезов устанавливаются деки.
Для исполнителей ИСК-3-3, ИСК-3-5 заслонка 5 фиксируется двумя болтами расположенными на головке транспортера, а заслонка 4 устанавливается в положение "закрыто" (ручка в нижнем положении). Ввод мелассы, карбамида в корм для всех исполнений производится через форсунку 6.
К основным достоинствам машины относится хорошее качество измельчения грубых кормов даже с высокой влажностью, универсальность, защищенность рабочих органов от поломок.
Пуск и остановка измельчителей-смесителей ИСК-3, ИСК-З-З. осуществляется от блоков управления (типа РУС).
Измельчитель-смеситель (Рисунок 10) состоит из рамы 1, приемного бункера 2, рабочей камеры 3, ротора 4, выгрузной камеры 5, шести противорезов или шести дек в зависимости от назначения измельчителя-смесителя. Привод ротора осуществляется от электродвигателя 6, через клиноременную передачу 7. Регулировка клиноременной передачи осуществляется натяжным болтом 8, путем перемещения опорной плиты 9. На приемном бункере крепятся форсунки 10 и 11 для ввода в кормосмесь карбамида и мелассы. На выгрузной камере крепится стопор ротора 12, который фиксирует ротор от самопроизвольного проворачивания при транспортировке, ремонте или техобслуживании. Приемный бункер 2 представляет собой сварную конструкцию и предназначен для приема кормов из загрузочных средств. Рабочая камера 3 представляет собой сварной цилиндр, в котором происходит измельчение или смешивание кормов. В ней монтируется противорезы или деки.
Рисунок 10-Общий вид измельчителя-смесителя (обозначения в тексте).
Противорежущие ножи под действием сил резания постоянно меняют угол поворота, благодаря этому автоматически поддерживают оптимальные условия измельчения и равномерный износ режущих кромок. При попадании в рабочую камеру камней и металлических предметов противорежущие ножи выходят из рабочей камеры, поворачиваясь вокруг своих осей, что предотвращает их поломку.
Выгрузная камера 5 выполнена в виде цилиндра и предназначена для выгрузки готового корма в транспортер через наружный патрубок 13. Для изменения степени измельчения или равномерности смешивания на выгрузной камере установлена заслонка 14. При уменьшении заслонкой сечения выгрузного патрубка, увеличивается степень измельчения или равномерность смешивания.
Рама 1 представляет собой сварную конструкцию, на которой устанавливается выгрузная камера и электродвигатель. На раме имеются люки для установки и обслуживания клиновых ремней. Подушками 17 рама устанавливается на фундамент и крепится к нему фундаментными болтами.
Ротор является основным рабочим органом и предназначен для крепления ножей и крыльчатки. В настоящее время изготавливаются два типа роторов: ИСК –3.01.05.000 и ИСК-3,01.06.000.
Ротор ИСК-3.01.05.000 (Рисунок 11) состоит из вала ротора 1, на который одевается крыльчатка 2 и поярусно фланцы 3 с ножами 4, фланцы и крыльчатка шпонкой 5 фиксируется на валу.
Рисунок 11-Ротор измельчителя ИСК-3 и расположение ножей по ярусам (обозначения в тексте)
Фланцы, ножи и крыльчатка соединяются между собой четырьмя пальцами 3 и четырьмя шпильками 9. Шпильки нижним концом вкручиваются в крыльчатку, а сверху зажимаются гайками. Верхний фланец ротора с зажимными гайками защищен от попадания корма прижимами 6.
Ротор ИСК-3.01.06.000 отличается от ротора ИСК-3.01.05.000 тем, что ножи и фланцы и крыльчатка соединяются между собой четырьмя шпильками и двенадцатью пальцами. Между ярусами ножей ротора ИСК-3.01.05.000 устанавливается один фланец с пазами для установки ножей, а между ярусами ножей ротора ИСК-3.01.06.000 устанавливается четыре фланца и по одной пластине под каждый нож. На крыльчатках обоих роторов крепятся защитные накладки. При износе их следует менять.
Противорезы выпускаются двух исполнений:
- с установкой противорезов на вал при помощи шпонки;
- с установкой противорезов без шпонки с возможностью установки зубчатой деки на плиту.
Они состоят из плиты, на которой в опорах крепится вал. На валу установлены противорезы и две втулки. Не снимая пружины, можно вывести противорезы из рабочей камеры, предварительно вынув палец. Рычаг для крепления пружины приварен к кронштейну, который свободно установлен на валу. Кронштейн для крепления пружин свободно установлен на шейке втулки. Вал ротора состоит из корпуса, вала, двух подшипников и гайки. На верхнюю часть вала устанавливается ротор, на нижнюю – шкив. Упорные подшипники зажимаются гайкой, которая фиксируется отгибочной шайбой.
Загрузочный и разгрузочный транспортеры имеют одинаковую конструкцию и отличаются приемным узлом и головкой. Транспортер состоит из корпуса, головки, полотна транспортера, устройства натяжения полотна транспортера, мотор-редуктора. Мотор-редуктор через цепную передачу приводит в движение полотно транспортера. Натяжное устройство предназначено для натяжения цепи. На корпусе приварены кронштейны для крепления опоры транспортера – стойки. Разгрузочный транспортер имеет приемную горловину с крышкой для исполнений ИСК-3; ИСК-3-4; а для ИСК-3-5 приемную горловину с крышкой, на который имеется заслонка для изменения подачи воздуха в головку. В верхнем положении рукоятки заслонка открыта, а в нижнем закрыта. Загрузочный транспортер имеет бункер для приема кормов, а также головку, в которой камни, металлические примеси и другие твердые включения отделяются от корма и через подпружиненную заслонку удаляются. При работе измельчителя-смесителя в режиме смешивания заслонка фиксируется болтами. Полотно транспортеров состоит из двух втулочно-роликовых цепей, к которым прикреплены металлические скребки. Полотно натягивается при помощи двух болтов натяжного устройства. Крышки служат для очистки транспортера от остатков корма.
Блоки управления типа РУС служат для запуска, остановки и управления электропроводами измельчителя-смесителя кормов.
Для подготовки рабочего места следует убедиться в исправности всех узлов, проверить отсутствие посторонних предметов на поверхности узлов.
Режимы работ
Измельчитель-смеситель может работать в одном из трех режимов: измельчение, смешивание и смешивание с доизмельчением.
В режиме измельчения измельчитель-смеситель комплектуется шестью комплектами противорежущих ножей на рабочей камере. На роторе устанавливаются четыре ножа в первом ярусе, два или четыре длинных ножа во втором ярусе, два или четыре зубчатых ножа в третьем и четвертом ярусах. Количество ножей во втором и третьем, четвертом ярусах зависит от требуемой степени измельчения. Для увеличения степени измельчения следует увеличить количество ножей на ярусах.
В режиме смешивания измельчитель-смеситель комплектуется шестью деками вместо пакетов противорезов. На роторе устанавливаются четыре укороченных ножа в первом ярусе, два длинных ножа в третьем ярусе и два зубчатых ножа в четвертом ярусе.
В режиме смешивания с доизмельчением измельчитель-смеситель коплектуется тремя пакетами противорезов и тремя деками на рабочей камере. Количество ножей аналогично режиму смешивания.
Предприятие - изготовитель поставляет измельчители в режиме измельчения, за исключением исполнения ИСК-3-2, поставляемого в режиме смешивания с доизмельчением.
Последовательность выполнения операции при работе.
1.Рубильный блоков РУС поставьте в положение «Вкл.».
2.Откройте заслонку выгрузной горловины измельчителя-смесителя.
3.Включите привод разгрузочного транспортера нажатием кнопки «Пуск».
4.Включите электродвигатель измельчителя-смесителя нажатием кнопки «Пуск».
5.Включите привод загрузочного транспортера нажатием кнопки «Пуск», для исполнения ИСК-3-3.
6.Подайте корм в приемный бункер измельчителя-смесителя или в приемный бункер загрузочного транспортера для исполнения ИСК-3-3, ИСК-3-5.
7.Подайте карбамид и мелассу в приемный бункер.
8.В процессе работы необходимо следить за выполнением технологического процесса не допускать забивания транспортеров.
После окончания работы необходимо провести следующие операции:
1.Прекратить подачу карбамида и мелассы.
2.Отключить привод транспортеров и двигатель измельчителя-смесителя в последовательности обратной включительно.
3.Очистить транспортеры и измельчитель-смеситель от остатков корма.
4.Закрыть заслонку камеры-выгрузной измельчителя-смесителя.
Дата добавления: 2019-02-13; просмотров: 2945; Мы поможем в написании вашей работы! |
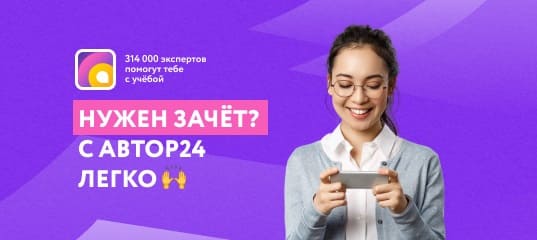
Мы поможем в написании ваших работ!