Высокоскоростная механообработка
В современных машинах увеличивается процент деталей с пространственно-сложными поверхностями. Это связано с развитием сложной формообразующей оснастки, с оптимизацией массогабаритных показателей в авиационной и космической технике, в гоночных автомобилях. Обработка таких элементов оснастки и сложных деталей с обычными режимами резания длится несколько десяткой часов. Значительно сократить время обработки позволяет метод высокоскоростной обработки (ВСО).
Развитию этого метода послужили высокие достижения информационных технологий, и в частности создание высоко-технологичных наукоемких CAD/CAM-систем. Внедре-нию метода ВСО способст-вовали теоретические пред-
посылки теории резания:
1. При повышении ско-рости резания происходит перераспределение тепла, образующегося при резании, в сторону тепла, уносимого стружкой (рис. 3.53). Доля тепла, передаваемого заго-товке, понижается так, что заготовка практически не нагревается. Именно это позволяет производить обработку даже закаленных сталей, не опасаясь отпуска поверхностного слоя.
2. При анализе зависимости силы резания от скорости резания (рис. 3.54) было отмечено, что в определенном интервале скоростей резания наблюдается значительный спад сил резания (такие зависимости за рубежом называют кривыми Соломона).
Проведенные исследования показали, что высокоскоростная обработка возможна на станках с ЧПУ при определенных условиях:
|
|
· небольшие сечения среза;
· малые динамические нагрузки при изменении направления движения инструмента;
· равномерная нагрузка на инструмент во время всего цикла обработки заготовки.
Из всех методов механообработки наибольший эффект дает высокоскоростное фрезерование. Для проведения высокоскоростной обработки разработаны специальные фрезерные станки с ЧПУ с частотой вращения шпинделя 60…80 тыс. оборотов в минуту. К имеющемуся оборудованию разрабатываются специальные приспособления, реализующие новые кинематические схемы высокоскоростной обработки.
Изменился и режущий инструмент, работающий в новых условиях. Разработаны новые типы твердосплавного инструмента с многослойными покрытиями.
Применение высокоскоростного фрезерования позволяет упростить управление процессом достижения размера и качества поверхности, обеспечить обработку тонкостенных деталей. Так, при высокоскоростном фрезеровании высота микронеровностей обрабатываемой поверхности уменьшается с 2 мкм при 700 м/мин до 0,5 мкм при 1750 м/мин.
При обработке нетрадиционных материалов также эффективно применение скоростного фрезерования (скорость резания до 10 000 м/мин и подача до 30 м/мин). Имея возможность вести лезвийную обработку закаленных сталей, можно обеспечить качество поверхности, соизмеримое с электроэрозионной обработкой. Это позволяет пересмотреть структуру производственного процесса изготовления формообразующих элементов пресс-форм и штампов (рис. 3.55). Режимы резания для обработки штампа без дальнейшей полировки твердостью 51 HRC и размерами 300х145 мм составляли: подача 5 м/мин, обороты шпинделя 35 тыс. об/мин, время обработки 95 мин, минимальный диаметр фрезы 2 мм.
|
|
У истоков высокоскоростной обработки стояла фирма Delcam plc, которая одной из первых использовала эту технологию при изготовлении пресс-форм и штампов.
Высокоскоростное резание производят с малой подачей в зоне небольших сил резания, поэтому основополагающими факторами, влияющими на процесс резания, является биение инструмента и возникающие при этом вибрации. С увеличением биения инструмента резко возрастает износ инструмента (рис. 3.56). Таким образом, ВСО требует особого внимания к балансировке инструмента. Для этого могут использоваться специальные патроны с возможностью балансировки или балансированные оправки для термозажима.
|
|
Высокоскоростная обработка позволяет получить поверхности с малой шероховатостью. Но практически для каждой комбинации системы СПИД существует своя зона стабильной (безвибрационной) работы инструмента (рис. 3.57). В связи с отсутствием отработанных рекомендаций стабильные зоны работы инструмента определяются экспериментальным путем. Для уменьшения вибраций следует выбирать фрезы с закругленной режущей кромкой.
При сравнении способов охлаждения в процессе резания экспериментально отмечено, что наилучший эффект достигается при обдуве зоны резания (рис 3.58). Низкая стойкость инструмента при охлаждении СОЖ объясняется главным образом выкрашиванием режущих кромок, что обусловлено циклическими термическими нагрузками на режущую кромку инструмента.
Внедрение высокоскоростной обработки потребовало пересмотра многих позиций подготовки процесса резания с целью гарантированного обеспечения минимальных динамических нагрузок на инструмент в течение всего процесса резания. В первую очередь необходимо построить траекторию движения инструмента таким образом, чтобы всегда был равномерный съем металла (постоянная толщина резания). Вручную это можно сделать для деталей простой конфигурации. Для деталей сложной формы, штампов, пресс-форм применяют CAD/CAM-системы со специальными модулями, реализующими особенности построения траектории движения инструмента для высокоскоростной обработки. В том числе: небольшая толщина съема металла (рис.3.59, а), движение по дуге окружности в углах (рис. 3.59, в) вместо резкого поворота (рис.
![]() |
3.59, б). Данные условия проще реализовать на станках с ЧПУ с подготовкой производства в CAD/CAM-системах. Во всех случаях должно быть исключено лобовое фрезерование с шириной резания равной диаметру фрезы. Даже при фрезеровании шпоночных пазов или аналогич

ных им узких пазов (рис. 3.60, а) вместо одного прохода, с помощью CAM-систем, строят траекторию сложного трохоидального движения (рис. 3.60, б). Такой режим обработки возможен только на станках с ЧПУ. Обработка колодцев или понижений со сложным контуром также строится с учетом равномерности снимаемого припуска (рис. 3.60, в). Часто применяющаяся строчная обработка при обычном фрезеровании неприменима при высокоскоростной обработке. При высокоскоростной обработке предпочтение отдается спиральным стратегиям, когда инструмент, однажды врезавшись, сохраняет непрерывный и равномерный контакт инструмента с заготовкой, с одним заходом и выходом (рис. 3.60, в).
|
|
Высокоскоростная обработка трехмерных поверхностей с резкими переходами связана с определенными трудностями. В таких случаях заготовка разбивается на определенные зоны, в которых применяется наиболее оптимальный способ движения инструмента.
Оптимизация траектории движения инструмента при ВСО по минимуму действующих сил реализуется в модуле CAM или в специальном модуле при расчете траектории. Кроме того, CAD/CAM-система должна иметь специальные функции [10]:
· широкий набор вариантов гладкого подвода-отвода и связок между проходами;
· набор стратегий спиральной и эквидистантной обработки зон как на чистовой, так и на черновой обработке, и поиск оптимальной стратегии в различных зонах обработки;
· автоматическое сглаживание траекторий в углах;
· использование в УП специальных технологических приемов (врезание сверху, трохоидальная обработка, специальные виды интерполяции);
· исключение проходов полной шириной фрезы и автоматическое применение трохоидального врезания в этих местах;
· широкое использование петель и различных криволинейных траекторий для уменьшения инерционных сил;
· оптимизацию подач для сглаживания нагрузки на инструмент.
Более широкие возможности имеют CAD/CAM-системы и станки с ЧПУ, поддерживающие 5-координатную обработку. В этом случае имеется набор возможностей по управлению вектором фрезы. Инструмент можно поставить по нормали к обрабатываемой поверхности или боком. При фрезеровании боком есть возможность управлять углом отклонения фрезы от поверхности. Часто при обработке сложных поверхностей создается набор макропрограмм, генерирующих проходы фрезы. Построив ограничивающие кривые, создают область действия оптимальной для данного участка поверхности макропрограммы. Полученная таким образом управляющая программа позволит получить эффективную обработку детали. Так при фрезеровании колеса турбины выделяют две основные задачи: выборка межлопаточного пространства и фрезерование лопаток (рис. 3.61), каждая из которых получается по своему алгоритму.
Внедрение высокоскоростной обработки связано с определенными трудностями: покупка дорогостоящего инструмента и оборудования для высокоскоростной обработки с быстродействующими устройствами ЧПУ, наличие CAD/CAM-систем, позволяющих выполнять подготовку производства для высокоскоростной обработки, подготовка кадров для выполнения операций высокоскоростной механообработки, наличие достаточного портфеля заказов.
Освоение технологий высокоскоростной обработки обеспечит такое качество обработки, которое позволит исключить финишные операции ручной полировки. Внедрение в обычную обработку новых подходов и стратегий, разработанных для ВСО, благоприятно скажется на качестве обработки и снизит вероятность поломки инструмента.
Дата добавления: 2019-02-12; просмотров: 194; Мы поможем в написании вашей работы! |
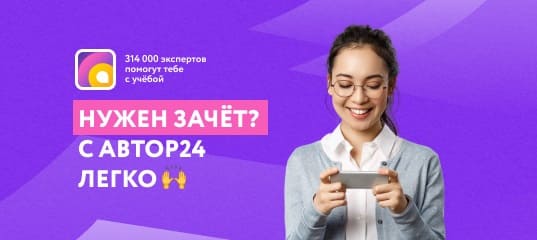
Мы поможем в написании ваших работ!