Выбор маршрута обработки в зависимости
От возможностей оборудования и инструмента
На предприятии имеется определенный парк станочного оборудования. Выбор маршрута обработка зависит от многих факторов, в том числе и от имеющегося в наличии оборудования. Если имеется не-сколько вариантов построения мар-шрута, то оптимальный выбор определяется производительностью имеющегося оборудования, разме-ром изготавливаемой партии дета-лей и сроками изготовления. Наи-более подходящий вариант опреде-лится экономическими расчетами.
Например, для изготовления винта (рис. 3.33) на данном пред-приятии возможно применение 3-х вариантов маршрутов обработки (табл. 3.30).
Таблица 3.30
Сравнительные характеристики вариантов технологических процессов
Вариант № 1 | Вариант № 2 | Вариант № 3 | |||
Операции | Q, шт/ час | Операции | Q, шт/ час | Операции | Q, шт/ час |
1 | 2 | 3 | 4 | 5 | 6 |
1. Заготови- тельная Распаковать бухту с проволокой | 1. Заготови- тельная Отрезать заготовку длиной 2 м | 1. Заготови- тельная Отрезать заготовку длиной 1 м |
Продолжение табл. 3.30
1 | 2 | 3 | 4 | 5 | 6 |
2. Холодно- высадочная Изготовить деталь с диа-метром под резьбу, головкой и шлицом | 1000 | 2. Автоматная Проточить заготовку, нарезать резьбу, отрезать готовую деталь | 30 | 2. Токарная Проточить заготовку, нарезать резьбу, отрезать готовую деталь | 30 |
3. Галтовочная Притупить острые кромки | 2000 | 3. Фрезерная Фрезеровать шлиц согласно чертежу | 100 | 3. Фрезерная Фрезеровать шлиц согласно чертежу | 100 |
4. Резьбо-накатная Накатать резьбу согласно чертежу | 1500 | 4. Слесарная Снять заусенцы, притупить острые кромки | 100 | 4. Слесарная Снять заусенцы, притупить острые кромки | 100 |
5. Промы-вочная Промыть детали согласно ТТП | 2000 | 5. Промы-вочная Промыть детали согласно ТТП | 2000 | 5. Промы-вочная Промыть детали согласно ТТП | 2000 |
6. Консерва-ция Консервировать детали согласно ТТП | 2000 | 6. Консерва- ция Консервировать детали согласно ТТП | 2000 | 6. Консервация Консервировать детали согласно ТТП | 2000 |
|
|
Наиболее производительным является первый вариант, наименее производительным – третий. В разных вариантах используется различное оборудование и различные заготовки. Техпроцессы отличаются количеством операций и качеством изготовленной продукции. Так, винт, изготовленный по первому варианту, имеет большую прочность резьбового соединения потому, что при накатке резьбы текстура волокон заготовки не перерезается, а деформируется.
3.14. Последовательность обработки поверхностей
при наличии допусков их взаимного расположения
|
|
![]() |
При наличии допусков взаимного расположения поверхностей проектирование технологического процесса механической обработки вызывает определенные трудности. Выход из этой ситуации может быть таким. Сначала определяется последняя, заключительная операция технологического процесса механической обработки. А затем, обрабатывая базовые поверхности на этой операции, получим предпоследнюю операцию и т.д., пока не определится заготовительная операция. Такая же последовательность была использована при расчете минимального припуска. Если обозначить заключительную операцию как n, то предпоследняя операция обозначится n–1, предпредпоследняя – n–2, и т.д., а заготовительная – как n–m. На заключительной операции механообработки обрабатывается самая точная поверхность, а базой для нее служит обычно поверхность на 1…2 квалитета грубее. При наличии допуска взаимного расположения между этими поверхностями как более точного, чем допуски на размеры этих поверхностей, базой выбирается поверхность, связанная допуском взаимного расположения. Все допуски взаимного расположения поверхностей формируются на последних операциях технологического маршрута. На рис. 3.34 представлен чертеж детали, на котором имеется 4 допуска взаимного расположения поверхностей. Из анализа чертежа видно, что самый точный размер – ø50h6. Согласно правилам разработки технологических процессов этот размер должен обрабатываться на последней формообразующей операции. По Матвееву В.В. [46], 6 квалитет точности для незакаленных сталей можно получить следующей последовательностью операций: точение, шлифование предварительное, шлифование тонкое, полирование. Данная последовательность операций является экономически обоснованной и применяется при больших партиях деталей. Для мелкосерийного производства допускается применение технически достижимой обработки. С учетом того, что токарная обработка будет производиться на станках с ЧПУ повышенной точности (СТП220АП), предлагается следующая последовательность обработки: токарная с ЧПУ, шлифование чистовое. Для повышения точности обработки увеличивают время выхаживания. При этом съем металла производится за счет упругого восстановления обработанной поверхности. Но данный способ является неэкономичным. Поверхность ø50h6 связана с другими поверхностями 4-мя допусками взаимного расположения. Причем все связанные поверхности имеют нежесткие допуски на размеры.
|
|
При обработке поверхности ø50h6 в качестве базовой желательно взять поверхность по 7 квалитету и связанную с ней допуском взаимного расположения. Но по чертежу детали нет 7 квалитета, а наиболее точная поверхность (после ø50h6) ø100h8 не связана с ø50h6 допуском взаимного расположения. Допуском взаимного расположения с ø50h6 связана внутренняя поверхность ø70H9. Поверхность ø70H9 могла обрабатываться последней, если бы имела 6 или 7 квалитет точности, так как при шлифовании принято обрабатывать вначале наружную цилиндрическую, а затем внутреннюю цилиндрическую поверхность.
|
|
Если бы торец ø70H9 не был бы связан с обрабатываемой поверхностью допуском взаимного расположения, то наилучшим вариантом для базирования при обработке ø50h6 была бы наружная цилиндрическая поверхность ø100h8. Эта поверхность имеет точный допуск h8, большую протяженность (хорошее базирование) и наибольшую жесткость. При таком базировании цилиндр необходимо лишить 4-х степеней свободы. В этом случае шлифуемая поверхность ø50h6 была бы параллельна цилиндрической поверхности ø100h8 с минимальной погрешностью.
Базовой поверхностью для обработки ø50h6 принята поверхность ø70H9, так как она связана допусками взаимного расположения со шлифуемой поверхностью. При базировании по внутреннему цилиндру может быть несколько вариантов (рис. 3.35, а, б, в). Необходимо отметить, что при назначении допусков взаимного расположения конструктором была допущена неточность: задано радиальное биение и по торцу, и по цилиндру ø70H9. Это вызывает определенные трудности при базировании по ø70H9. Если отдать предпочтение базированию по торцу, то его необходимо лишить 3-х степеней свободы (рис. 3.35, б). При этом цилиндр ø50h6 будет не перпендикулярен к торцу ø70H9 с меньшей погрешностью и будет выдержано радиальное биение торца относительно ø50h6. Если цилиндр ø70H9 лишить 4-х степеней свободы, то ø50h6 будет параллелен ø70H9 с меньшей погрешностью и будет выдержано радиальное биение цилиндра ø70H9 относительно ø50h6 (рис. 3.35, а). Выбор одного из перечисленных вариантов возможен при детальном рассмотрении конструкции изделия, в которой установлена данная деталь. Если конструкция сборочного изделия неизвестна, то выбирается вариант базирования (по рис. 3.35, а), с тем чтобы обеспечить параллельность осей ø50h6 и ø70H9.
Наружное шлифование цилиндрических поверхностей производится на круглошлифовальных станках. Для экономичности обработки на обрабатываемой цилиндрической поверхности делают кольцевую проточку для выхода шлифовального круга. Шлифовальный круг при этом по торцу не изнашивается. В противном случае нужна частая переточка шлифовального круга. Ряд круглошлифовальных станков предназначен для обработки не только цилиндрических поверхностей, но и торцевых. В этом случае возможно два варианта получения ø50h6.
В первом варианте (рис. 3.36, а) размер 40±0,1 получен на предыдущей операции, и в данном случае не выдерживается. Во втором варианте (рис.3.36, б) обрабатывается торец детали и выдерживается размер 120–0,1. Затем, используя обработанный торец как базу, обрабатывают
ø50h6 и выдерживают размер 40±0,1. Так как шлифовальный станок предназначен для точной обработки, то за счет обработки за одну установку выдерживается биение торца ø50h6 к цилиндрической поверхности, а за счет базирования по цилиндру ø70H9 обеспечивается радиальное биение цилиндра ø70H9 к цилиндру ø50h6.
Предпоследняя (n– 1) операция может быть плоскошлифовальная (рис. 3.37), если на последней операции не обрабатывается торец ø50h6. Чтобы обеспечить минимальную погрешность радиального биения на последней операции, на плоскошлифовальной операции необходимо базироваться по ø50,4h8 (условно принят припуск на шлифование 0,2 мм на сторону). Однако практически это нереально. Поэтому в качестве базы будет использоваться цилиндрическая поверхность ø70H9. Эта же поверхность будет использована как базовая и на последней операции. Принцип постоянства баз будет соблюден и погрешность обработки будет минимальной.
На последней операции в качестве базы использована цилиндрическая поверхность ø70H9. Данная поверхность имеет шероховатость Ra 1,6 мкм. Она будет получена внутренним шлифованием на n–2 операции. В качестве базы желательно использовать ø100h8. Эта поверхность точна, достаточно протяженна, имеет повышенную жесткость. Но она никак не связана с внутренней поверхностью.
Поэтому за базу будет принята поверхность ø50,4h8 (рис. 3.38), так как она по чертежу детали связана допуском взаимного расположения с обрабатываемой поверхностью.
Отверстие ø10 можно было бы получить на сверлильном станке по кондуктору, используя следующий набор инструментов: сверло, зенкер, развертка. При небольшой глубине отверстия, при d ≈ l, и небольшом диаметре отверстия, можно сразу после сверла использовать развертку, чтобы получить необходимую шероховатость.
Для данной детали кроме ø10 необходимо выдержать размер 35±0,05 до оси отверстия и отклонение от перпендикулярности к поверхности ø50h6. Указанные требования можно выполнить только на координатно-расточном станке, используя следующий набор инструментов: сверло, расточной резец. Так как на координатно-расточных станках кондукторы обычно не используются, то для направления сверла вначале необходимо зацентровать отверстие центровочным сверлом. Базой будет цилиндрическая поверхность ø50h6 и торец ø100h8 (рис. 3.39). По цилиндрической поверхности деталь должна быть лишена 4-х степеней свободы, так как относительно нее определяется отклонение от перпендикулярности. По торцу деталь может быть лишена одной степени, потому что от торца выдерживается всего один размер 35±0,05. Размер этот точен, поэтому должен быть выдержан от окончательно обработанного торца. Отсюда следует, что на заключительной ( n- й) операции должно обрабатываться отверстие ø10. Предпоследняя (n– 1) операция – получение ø50h6 и размера 40±0,1. На операции n– 2 – обработка отверстия ø70H9. На этих операциях сформировались все четыре допуска взаимного расположения поверхностей. В дальнейшем ход рассуждений остается таким же – от обработанной поверхности к базирующей и т.д.
Определена связь между поверхностями ø50h6 и ø70H9 (по чертежу) на точных чистовых операциях. Эту связь необходимо соблюдать и на получистовых и черновых операциях. Поверхность ø100h8 стоит в стороне от вышеперечисленных поверхностей, но она является довольно точной, поэтому ее можно получить на n–3 операции. Базой может являться поверхность как ø50,4h8, так и ø70H9. Проанализируем их. Обычно, если есть очень точная радиальная поверхность, в нашем случае это ø50h6, то желательно и другие поверхности выполнять соосными с ней. С этой точки зрения в качестве базовой необходимо взять поверхность ø50,4h8. Но эта поверхность в осевом направлении недостаточно протяженна, чтобы лишить ее 4-х степеней свободы. С этой точки зрения более предпочтительной является поверхность ø70H9. К тому же она является базовой для получения поверхности ø50h6. Поэтому, для обработки наружной поверхности ø100h8, в качестве базовой выбираем поверхность ø70H9 (рис. 3.40).
![]() |

![]() |
Станки с ЧПУ предназначены для получистовой, а в некоторых случаях и для чистовой обработки. Поэтому, прежде чем деталь обрабатывать на станке с ЧПУ, необходимо подготовить базы. Обычно подготовку баз производят на станках, предназначенных для черновых операций. В нашем случае – это станок с ручным управлением типа 16К20, а операция n– 6 (рис. 3.42, б).
На заготовительной операции ( n– 7) из круга или прутка отрезается заготовка для одной детали (рис. 3.42, а).
Выстроив номера операций по возрастающей, получим маршрутный технологический процесс для механической обработки заданной детали. После того как в маршрут добавятся все сопутствующие операции – слесарная, контрольная, промывочная, термическая, гальваническая, консервация и другие – получим законченный технологический процесс.
Дата добавления: 2019-02-12; просмотров: 286; Мы поможем в написании вашей работы! |
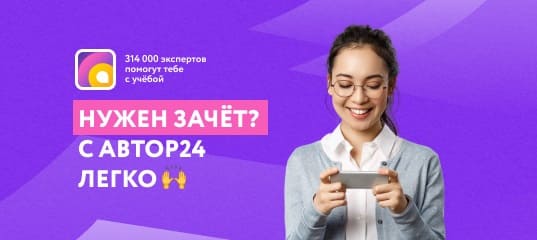
Мы поможем в написании ваших работ!