Мощность машин и её преобразование в механизмах 33 страница
Определение податливости болта
где Е – модуль упругости материала болта; S – площадь сечения болта;
lδ - расчетная длина, равная свободной длине болта между опорными поверхностями, плюс половина длины свинчивания (высоты гайки) (рис. 51.1), т.е.
Для случая ступенчатого болта (рис. 51.2)
где ln - длина n-го участка болта; Sn – площадь сечения n-го участка болта.
D C
Рис.51.1 Рис.51.2
Определение податливости соединяемых деталей.
Для определения коэффициента податливости соединяемых деталей λд пользуются методом профессора И. И. Бобарыкова. Согласно этому методу деформации соединяемых деталей распространяются на так называемые конусы давления, наружный диаметр а меньших оснований которых представляет собой наружный диаметр опорной поверхности гайки (головки болта, пружинной шайбы и т.д.), а образующие наклонены под углом α<45° (рис. 51.3). Рекомендуется принимать tg𝛼 =0,5. Для упрощения расчетов конус заменяют цилиндром, наружный диаметр которого равен среднему диаметру конуса. Коэффициент податливости соединяемых деталей равен
где h1, h2, …, hn – толщина соединяемых деталей;
S1, S2, …, Sn – площади поперечных сечений конусов давлений;
E1, E2, …, En – модули упругости материалов этих деталей.
E
а) б)
|
|
Рис.51.3
Для соединения, показанного на рис. 51.3,а при tga=0,5
Тогда
Для соединения, показанного на рис. 51.3, б, при одинаковых материалах соединяемых деталей
При большом значении λδ и малом значении коэффициента податливости соединяемых деталей λд коэффициент внешней нагрузки х небольшой и почти вся внешняя сила Fвн идет на разгрузку стыка. При малом значении коэффициента податливости болта и большом коэффициента податливости соединяемых деталей, например при применении в стыке упругой прокладки, большая часть внешней силы передается на болт. При наличии упругой прокладки податливостью соединяемых деталей можно пренебречь.
Болтовое соединение нагружено силами в плоскости стыка
Условием надежности соединения является отсутствие сдвига деталей в стыке. Примером может служить соединение двух полумуфт в дисковой муфте. Конструкция может быть собрана по двум вариантам.
Расчет болта, нагруженного поперечной силой Fr при установке его с зазором (рис. 52).
В этом случае болт ставится с зазором в отверстие деталей. Для обеспечения неподвижности соединяемых листов 1, 2, 3 болт затягивают силой затяжки F3. Во избежание работы болта на изгиб его следует затянуть так сильно, чтобы силы трения на стыках деталей были больше сдвигающих сил Fr.
|
|
Основные допущения.
1) Деформация соединяемых деталей не учитывается, то есть детали принимают абсолютно жесткими.
2) Внешние нагрузки передаются от одной детали на другую локально, через зоны, расположенные вокруг болтов.
3) Расчет ведут на предотвращение сдвига деталей по условию неподвижности стыка.
Основным критерием расчета является условие неподвижности стыка.
Рис. 52. К расчету болтов соединения, несущего поперечную нагрузку.
Болт установлен с зазором
Обычно силу трения принимают с запасом: Ff= KFr. (К –коэффициент запаса по сдвигу деталей, К = 1,3 – 1,5 при статической нагрузке, К = 1,8 – 2 при переменной нагрузке).
Найдем требуемую затяжку болта. Учтем, что сила затяжки болта может создавать нормальное давление на i трущихся поверхностях (на рис. 52) или в общем случае
где i – число плоскостей стыка деталей (на рис.52 – i = 2; при соединении только двух деталей i = 1); f – коэффициент трения в стыке (f = 0,15 – 0,2 для сухих чугунных и стальных поверхностей);
Как известно при затяжке болт работает на растяжение и кручение поэтому прочность болта оценивают по эквивалентному напряжению. Так как внешняя нагрузка не передается на болт, его рассчитывают только на статическую прочность по силе затяжки даже при переменной внешней нагрузке. Влияние переменной нагрузки учитывают путем выбора повышенных значений коэффициента запаса.
|
|
Проектировочный расчет болта:
внутренний диаметр резьбы
Расчет болта, нагруженного поперечной силой, с установкой его без зазора (рис. 53).
Основные допущения.
1) Деформации деталей не учитываются, то есть считают детали абсолютно жесткими.
2) Внешние нагрузки передаются с одной детали на другую локально, через зоны, расположенные вокруг болтов.
3) Силы трения, связанные с затяжкой болтов, не учитываются.
4) Основным критерием расчета является условие неподвижности стыка.
5) При установке болта без зазора неподвижность обеспечивается сопротивлением болта срезу и смятию.
Рис. 53. К расчету болтов соединения, несущего поперечную нагрузку.
Болт установлен без зазора
В этом случае отверстие калибруют разверткой, а диаметр стержня болта выполняют с допуском, обеспечивающим беззазорную посадку. При расчете прочности данного соединения не учитывают силы трения в стыке, так как затяжка болта не контролируется. В общем случае болт можно заменить штифтом. Стержень болта рассчитывают по напряжениям среза и смятия.
|
|
Условие прочности
где - расчетное напряжение среза болта; Fr — поперечная сила; dc — диаметр стержня в опасном сечении; [τ]ср — допускаемое напряжение среза для болта; i — число плоскостей среза (на рис. 53 i = 2);
[τ]ср=(0,2÷0,3)σT.
Рис. 54. Варианты конструкций, разгружающие болты от поперечной нагрузки
Проектировочный расчет.
Диаметр стержня из условия среза
Закон распределения напряжений смятия по цилиндрической поверхности контакта болта и детали трудно установить точно. Это зависит от точности размеров и форм деталей соединения. Поэтому расчет на смятие производят по условным напряжениям. Эпюру действительного распределения напряжений заменяют условной с равномерным распределением напряжений (рис.54.1).
E
Рис.54.1
Для средней детали (и при соединении только двух деталей)
для крайних деталей
Формулы (23) и (24) справедливы для болта и деталей. Из двух значений [σ]см в этих формулах расчет прочности выполняют по наибольшему, а допускаемое напряжение определяют по более слабому материалу болта или детали. Сравнивая варианты постановки болтов с зазором и без зазора (рис.52 и 53), следует отметить, что первый вариант дешевле второго, так как не требует точных размеров болта и отверстия. Однако условия работы болта, поставленного с зазором, хуже, чем без зазора. Так, например, приняв коэффициент трения в стыке деталей f= 0,2, К = 1,5 и i = 1, из формулы (20) получим Fзаm = 7,5F. Следовательно, расчетная нагрузка болта с зазором в 7,5 раз превышает внешнюю нагрузку. Кроме того, вследствие нестабильности коэффициент трения и трудности контроля затяжки работа таких соединений при сдвигающей нагрузке недостаточно надежна.
Расчет одиночных болтов при эксцентрической нагрузке
Болты с эксцентрической головкой относятся к специальным болтам. Эксцентричное нагружение болтов возникает при наличии костыльной головки или непараллельности (перекосах) опорных поверхностей деталей и гайки. Такие болты устанавливают в отверстия с зазором и нагружаются отрывающей силой , приложенной c эксцентриситетом а.
Нераскрытие стыка обеспечивается предварительной затяжкой болта.
Fзат = k∙F.
Расчетная сила, растягивающая болт, определяется как для обычного болта:
Fp = 1,3Fзат + 𝜒∙F
Кроме напряжений растяжения расчетная сила вызывает напряжения изгиба. Условие прочности:
𝜎max=𝜎р + 𝜎и≤[𝜎],
где σmax - суммарное максимальное напряжение,
- напряжение растяжения,
- напряжение от изгиба моментом M = Fp∙a.
Следует избегать случайного нагружения болтов эксцентрично приложенной силой, так как даже небольшой эксцентриситет a=d/2, имеющий место при установке обычного болта, если опорные поверхности под гайкой или головкой имеют перекос, вызывает напряжение σmax ≈ 7,5σр. Напряжения изгиба являются самыми опасными для прочности болтов, винтов и шпилек.
Отсюда правила конструирования:
1. Не допускать черновых (необработанных) поверхностей под гайками, головками, шайбами.
2. Несопрягаемые (свободные) поверхности корпусных деталей не обрабатывают. В местах установки крепежа следует предусматривать:
а) на литых деталях – бобышки (местные выступы) под обработку высотой S = 2…3 мм (рис. 54.2, а);
б) на сварных деталях – платики (рис. 54.2, б);
в) на любых деталях – цековки глубиной h = 1,25…1,6 мм (рис. 54.2, в).
3) Использовать сферические, косые шайбы и другие выравнивающие от изгиба устройства.
Рис.54.2
Расчет болтов при внецентренно приложенной силе
Рассмотрим два случая:
1. Поставлен болт с костыльной головкой. В винтах с эксцентричной (костыльной) головкой под действием силы Fзат возникают напряжения растяжения σр и σи (рис. 55).
F
Рис.55. Болт с костыльной головкой
Суммарное напряжение в наиболее опасной точке
Коэффициент 1,3 учитывает напряжения кручения стержня болта от момента трения в резьбе Тр.
Из формулы следует, что с увеличением эксцентриситета е напряжение в болте будет возрастать. При эксцентричном приложении нагрузки суммарные напряжения в болте могут во много раз превышать напряжения растяжения. Например, при эксцентриситете e=0,5dp суммарные напряжения σΣ=5,3σp.
В связи с этим следует избегать применения болтов с эксцентричными головками.
2.Опорные поверхности под гайку и головку болта непараллельны (рис. 55.1).
J
Рис.55.1. Опорные поверхности под гайку и головку болта непараллельны
За напряженное состояние винта в первом приближении принимают чистый изгиб, т.к. изгибные напряжения во много раз превышают напряжения растяжения. По заданному углу наклона упругой линии определяем изгибающий момент на винте
где l – деформируемая длина винта; Е – модуль упругости материала винта; I=πd2/64 – момент инерции сечения стержня винта.
Напряжения изгиба в винте (рис.55.1)
Напряжения изгиба в резьбовой части
Для уменьшения напряжений изгиба повышают точность изготовления (вводят допуски на перекосы опорных поверхностей, на биение торца) или применяют специальные конструкции – сферические или косые шайбы.
Расчет болтов при повышенной температуре
Сборка резьбовых соединений производится при нормальной температуре, однако рабочая температура соединения зачастую существенно превышает нормальную. Пример: крепление с помощью резьбовых шпилек головки к блоку цилиндров двигателя внутреннего сгорания. Во многих случаях, как, например, в большинстве двигателей армейских машин, блок цилиндров и его головка выполняются из лёгких сплавов на основе алюминия, а соединяются между собой посредством стальных шпилек. Но алюминиевые сплавы и стали имеют существенно (примерно в 2 раза) различные коэффициенты линейного термического расширения. Нагревание такого соединения создаёт в его элементах дополнительные нагрузки, которые, суммируясь с усилиями предварительной затяжки, могут привести к разрушению элементов соединения или другим неприятным последствиям (заклинивание резьбы, смятие опорных поверхностей, вытяжение шпилек и т.п.).
Для резьбовых соединений из конструкционной стали при температуре t>300 °С и для легких сплавов при t>150 °С следует учитывать ползучесть и длительную прочность материала.
При t>500 °C для резьбовых соединений применяют специальные жаропрочные стали, например ЭИ643 и др.
Таблица 14. Материалы деталей резьбовых соединений и их максимальные рабочие температуры
Материалы
Рабочие температуры резьбовых соединений, °С, max
Материалы
Рабочие температуры резьбовых соединений, °С, max
Стали
Титановые сплавы
45
<300 °С
BT33-1
<450 °С
30ХГСА
<400 °С
ВТ14
<400 °С,
кратковременно до 500 °С
1Х12НГВМФ
<500 °С
12Х18Н9Т
<600 °С
ВТ16
<350 °С,
кратковременно до 700 °С
Х12Н22ТЗМР
<700 °С
При высоких температурах в резьбовых соединениях часто наблюдается заедание - после некоторого времени работы гайку не удается отвернуть или она отвинчивается с большим трудом. Опасность заедания уменьшается при правильном подборе материалов болта и гайки. С этой целью при температурах до 500 °С и незначительных усилиях применяют гайки из латуни, бронзы и перлитного чугуна, а для более нагруженных соединений - гайки из жаропрочных материалов. При этом материал гайки должен иметь больший коэффициент линейного расширения, чем материал болта.
Заедание в резьбовых соединениях уменьшается при применении покрытий (медное - до 600 °С и серебряное - до 700 °С).
Кадмирование резьбовых соединений при рабочих температурах свыше 200 °С недопустимо, так как кадмий проникает в металл болта и вызывает его разрушение.
При повышении температуры на t°C болт (шпилька) и соединяемые детали в свободном состоянии должны получить удлинение
где δtб и δtд – свободное температурное удлинение болта и соединяемых деталей, соответственно; αб и αi – коэффициенты линейного теплового расширения болта и каждой из соединяемых деталей, соответственно; lб – длина болта; hi – толщина каждой из отдельных деталей, входящих в соединение; причём lб=Σhi.
Но в результате совместной деформации при нагревании в соединении появляется температурная нагрузка (сила), которая сообщает болту дополнительное удлинение, а стягиваемым деталям укорочение (отрицательное удлинение)
где Ft – усилие в соединении, возникшее в связи с его нагреванием; dFб и dFд – дополнительная деформация от действия Ft болта и соединяемых деталей, соответственно; λб и λд – податливость болта и суммарная податливость соединяемых деталей.
Но в силу совместности деформации изменение длины болта и соединяемых деталей одинаковы, то есть δtб+δFб=𝛿tд+δFд, или в развёрнутом виде
Из последнего выражения находим дополнительную нагрузку на соединение, вызванную его нагреванием,
Разделив Ft на площадь поперечного сечения болта, получим величину температурных напряжений, которые суммируются с рабочими напряжениями.
Расчет ведут по рассмотренным выше правилам, но в расчетной формуле учитывают дополнительную силу, появляющуюся при температурной деформации:
Расчетная нагрузка.
Fpt = Fр + Ft, (27)
где Fр – расчетная внешняя нагрузка на болт при нормальной температуре.
Резьбовые соединения, работающие при циклических нагрузках
Примером таких болтов могут служить болты крепления крышки цилиндра двигателя внутреннего сгорания. При циклических нагрузках (чаще всего пульсирующего цикла) большую опасность представляют усталостные явления, которые могут служить причиной аварийных разрушений. Усталостные разрушения начинаются с образования микротрещин, которые возникают в местах наибольшей концентрации напряжений, поэтому в конструкции болтов и винтов большое внимание должно быть уделено целесообразной геометрической их форме. Для оценки концентрации напряжений пользуются гидравлической аналогией, которая выражается так: если контур детали представить как трубу, в которой движется жидкость, то там, где поток турбулентный (вихревой), должны возникнуть местные напряжения, величина которых пропорциональна интенсивности вихрей.
Местные напряжения возникают:
- в местах резкого перехода сечений,
- в канавках с острыми углами,
- при малых радиусах округлений,
- в переходах от стержня к резьбе,
- в переходах к зоне закалки ТВЧ,
- при некруглых отверстиях.
Рассмотрим циклы изменения нагрузок и напряжений (рис. 56).
F
Рис.56. Циклы изменения нагрузок и напряжений
В большинстве случаев переменная внешняя нагрузка изменяется по отнулевому циклу от 0 до Fвн. На болт приходится только часть ее xFвн. Таким образом, если на болт действует сила предварительной затяжки Fзат и переменная внешняя сила, изменяющаяся от 0 до xFвн, то напряжение начальной затяжки , где S1 – площадь поперечного сечения болта по внутреннему диаметру резьбы.
Максимальное напряжение цикла σmax=σm+σa=σзат+2σa,
где - амплитуда напряжения цикла;
σm=σзат+σa - среднее напряжение цикла.
Расчет на усталость болтов производится как проверочный по коэффициенту запаса прочности
где σ-1 - предел выносливости болта (σ-1=0,35σв);
Дата добавления: 2019-01-14; просмотров: 187; Мы поможем в написании вашей работы! |
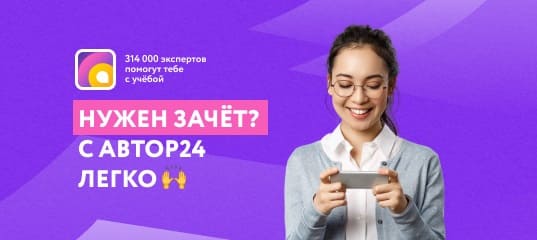
Мы поможем в написании ваших работ!