Мощность машин и её преобразование в механизмах 35 страница
б) Предполагаем, что под действием внешнего момента Му стык будет поворачиваться относительно оси симметрии стыка. Если затяжка отсутствует, то осью поворота будет нижняя кромка основания (см. рис. 60,а). Пока давление между основанием и фундаментом обеспечено, то есть в стыке — напряжения сжатия, то стык затянут, и основание и фундамент можно считать единым целым. Испытания подтверждают это предположение.
в) Из предыдущего пункта понятно, почему основным критерием расчета таких соединений является условие нераскрытия стыка.
г) Пренебрегая величиной χ при расчете фундаментных болтов, найдём напряжение в стыке от изгиба:
где Wcmy – осевой момент сопротивления стыка; зависит от формы стыка.
д) Эпюра напряжений в стыке от изгиба приведена на рис. 60,г.
4.7) Для выполнения условия нераскрытия стыка напряжения в нем должны быть сжимающими. На рис. 60,д приведены варианты эпюры суммарных напряжений в стыке.
а) 2, 3 – стык раскрыт σΣ≥0;
б) 1– стык не раскрыт σΣ<0, то есть сжимающее;
4.8) Из условия нераскрытия стыка напряжение в нем может быть определено:
где S=1,3÷2 – коэффициент запаса по нераскрытию стыка. Знак «–» берется при сжимающей силе Fx.
4.9) Требуемая сила затяжки болтов из условия нераскрытия стыка.
а) Из формулы для определения Fзат видно, что уменьшение площади стыка A уменьшает требуемую силу затяжки.
|
|
б) Целесообразно делать стыки не сплошными, а — как показано на рис. 59, 60.
в) Целесообразность делать стыки несплошными подтверждается следующим: если уменьшить площадь А до А1 вдвое А1=0,5∙А, то σмy возрастет на 12%, а усилие затяжки уменьшится на 38%.
4.10) Проверяем и максимальное напряжение смятия фундамента:
σсм = σΣmax ≤ [σ]см.
Величина допускаемого напряжения для разных материалов приведена в справочных данных.
Технико-экономические преимущества применения прогрессивного крепежа
Принципы унификации крепёжных деталей
Важным и эффективным средством совершенствования крепёжных соединений следует считать унификацию применяемых конструкций изделий, в том числе за счёт использования международных стандартов. Одним из возможных и наиболее перспективных вариантов рассмотрим повсеместное применение винтов и болтов со звездообразным приводом, получающим всё большее распространение в мировой практике. На рис. 11 показаны возможные варианты унификации винтов и болтов.
Применение звездообразного привода выгодно как с технической, так и с экономической стороны. Хорошие перспективы имеются также по унификации самонарезающих винтов, гаек и других видов крепёжных деталей.
|
|
Об экономике современного крепежа. «Цена на месте»
Крепёжные детали новых прогрессивных конструкций выполняют большее число функций и поэтому обычно дороже традиционных. Это вполне обосновано. Отказ от деталей устаревших видов и вспомогательных деталей в соединениях уменьшит и упростит транспортные операции, комплектацию рабочих мест сборщиков и другие процедуры.
В 40-х годах прошедшего века в США была выдвинута концепция по подсчету расходов и снижению затрат при производстве, продаже и применении новых изделий, в том числе и крепежных деталей. Она получила название «In Place Cost» (IPC), что в переводе означает «Цена на месте», и позднее была усовершенствована в Европе и Японии. Концепция позволяет учитывать затраты, возникающие начиная с оформления заказа на закупку деталей и кончая установкой на место их применения в рабочий узел машины. Одним из объектов снижения затрат со временем стало и последующее сервисное обслуживание данной сборочной единицы в машине.
Однако в отечественной практике не принято обращать внимание на расходы, связанные с крепёжными деталями устаревших конструкций, а также «лишними» деталями в соединениях, хотя их надо заказать, доставить к потребителю, организовать хранение и учёт, перевезти в сборочные цехи, разместить там на складах, разложить в специальную тару на каждую смену, доставить к рабочим местам всех сборщиков и т.д. Всё это: рабочие кадры, трудозатраты, зарплата, весовая и учётная техника, тара, спецодежда, инвентарь, помещения, транспортные средства и много ещё того, что относят к накладным расходам, сильно увеличивает стоимость крепёжных деталей, установленных на своё место в узле автомобиля. В опубликованных специалистами США и Великобритании данных приведены следующие оценки:
|
|
- стоимость крепёжных деталей, установленных в собранном изделии, увеличивается в 3…10 раз по сравнению со стоимостью их закупки;
- на соединение конструктивных элементов машины приходится от 20 до 40% общих расходов на её изготовление;
- любая промышленная фирма, расходующая 1 млн долларов в год на крепёжные детали, может сэкономить 15% от этой суммы только за счёт применения более рациональных конструкций и т.д.
Зная средства, которые расходуют отечественные производители машиностроительной продукции на закупку крепёжных деталей, можно обнаружить значительные резервы экономии только за счёт наведения порядка в применении крепежа.
|
|
Требования к качеству крепёжных изделий и их обеспечение
В мировой практике машиностроения с каждым годом возрастают требования к качеству крепёжных деталей, поступающих на сборку. Такова общая тенденции развития техники. Это происходит вследствие применения автоматизированных устройств и систем сборки (например, автомобилей, приборов). Производители увеличивают гарантийные сроки эксплуатации товара как средства конкурентной борьбы за покупателя. Известно, что до 50% дефектов и поломок автомобилей связано с ослаблением или другими дефектами крепёжных соединений. Контроль качества крепёжных деталей должен сопровождать все операции их изготовления:
а) исходный металл – химический состав, механические свойства, качество поверхности и нанесённого подсмазочного покрытия, например, фосфатного;
б) автоматизированный контроль процессов на автоматах высадки, обточки заходной части, накатки или нарезки резьбы. Оборудование для производства крепёжных деталей оснащают программируемыми средствами активного контроля. Например, на холодновысадочных автоматах измеряется усилие на каждой позиции штамповки. И если нагрузка не соответствует эталонному значению, станок останавливается, причину сбоя устраняют;
в) статистический контроль – систематическое контролирование наладчиком размеров, определяемых технологией и характеризующих устойчивость процесса (например, длины изделия, диаметра стержня под накатку резьбы, соосности головки и стержня, глубины шлица и др.). Все проверенные параметры вводят в специальную форму на компьютере со строго заданной периодичностью (например, каждые 15…20 минут работы). Программные средства исключают возможность исправления введённых данных, по ним строятся кривые стабильности процесса. Статистический контроль осуществляется на всех операциях;
д) завершающий этап: контроль готовых деталей. Нормой становится применение автоматизированных контрольных систем и оборудования для контроля практически всех важнейших параметров деталей. Принцип действия контролирующих устройств основан на использовании лазеров, ультразвука, электромагнитных и других свойств. Автоматические установки включают системы проверки размеров самых разных элементов деталей (резьба, шлицы в головке, прямолинейность и др.). Может проверяться твёрдость, вид и толщина покрытия, усилие закручивания и т.д. Производи-тельность контроля: резьбы, размеров и глубины шлицев – 150 шт./мин, обнаружение трещин – 220 шт./мин, наружные геометрические размеры – 300…500 шт./мин. Из нескольких контрольных автоматов формируют линии контроля. Подача деталей производится из бункеров, дефектные детали удаляют в специальную тару. Контроль 100% деталей особенно важен при поставке крепёжных деталей на автоматические линии сборочных предприятий.
Европейскими нормами ЕН ИСО рекомендован максимальный уровень дефектности для машиностроения ppm 50 (50 дефектных деталей на 1 млн штук). Достичь его без применения автоматизированных контрольных средств при производстве крепёжных изделий невозможно. Известно, что производители автомобилей таких фирм, как Мерседес, БМВ, и некоторые другие, ставят перед поставщиками крепежа задачу довести уровень дефектности до ppm 1. Таким образом, контрольная техника постепенно становится неотъемлемой составляющей производственного цикла. С этим нельзя не считаться.
О маркетинговых исследованиях в области крепёжных изделий
Роль маркетинга в развитии производства и применения новых видов изделий во всех отраслях – несомненна. Поэтому важно уметь пользоваться его приёмами в повседневной деятельности при определении верных направлений развития бизнеса. «Важно своевременно и правильно оценивать жизнеспособность основных видов продукции предприятия. Опасно рассчитывать на «вчерашних кормильцев» и не уделять внимания «кормильцам завтрашним», надо вовремя выявлять продукцию, приближающуюся или вступающую в стадию упадка, готовить ей замену». (Ф.Котлер. Основы маркетинга. Пер. с англ. / М.: Прогресс, 1990).
В теории и практике маркетинговых исследований рынка и продвижения на него новых видов продукции широко используется методика анализа продукции на основе рассмотрения её «жизненного цикла» (рис. 61). Покажем, на каких этапах жизненного цикла находятся основные группы крепёжных деталей, выпускаемых в РФ и применяемых отечественными автозаводами в автотранспортных средствах (АТС).
Этап 1. Выход (выведение товара на рынок). Рынок имеется, формируется, но ещё не подготовлен, хотя интерес к новому продукту несомненно проявляет. Начинается сбыт наиболее подготовленным потребителям.
Этап 2. Рост. Потребители и рынок положительно реагируют на новую продукцию, если её качество и технический уровень приносят выгоды потребителям. Появляются новые сегменты рынка, с увеличением объемов производства снижается цена продукции. Характеристики и преимущества крепёжных деталей, отнесённых к этому этапу, приведены ранее. В АТС находят место всё большее количество болтов и гаек с фланцем, гаек самостопорящихся, болтов и винтов со звездообразным приводом, винтов и болтов резьбовыдавливающих. Это позволяет заменять устаревшие конструкции, в том числе избавляться от шайб, как от лишних деталей. Однако, несмотря на то, что производство и применение многих прогрессивных крепёжных деталей в РФ ежегодно увеличивается, использование их по сравнению с изделиями из этапа «Зрелость» остаётся недостаточным.
Этап 3. Зрелость. Это самый продолжительный и стабильный этап, в том числе по прибыли, хотя темпы роста сбыта постепенно снижаются. Группы стандартных крепёжных деталей, находящихся на этом этапе, казалось бы, имеют относительно устойчивый спрос на рынке. Однако следует иметь в виду, что не менее 70% гаек шестигранных и большинство прорезных надо заменять на гайки с фланцем и гайки самостопорящиеся. У приварных, неподвижных и закладных квадратных гаек тоже имеется хорошая замена: приклёпываемые гайки. Аналогичная замена по приварным болтам и шпилькам – это приклёпываемые шпильки. Болты с шестигранной нормальной головкой и винты с внутренним шестигранником наверняка уступят место болтам с наружным и винтам с внутренним звездообразным приводом. Винты и винты самонарезающие прямой и крестообразный шлицы тоже сменят на звездообразный привод. Везде, где под головки болтов и винтов и под гайки устанавливают плоские шайбы, должен появиться фланцевый крепёж. Таким образом, можно утверждать, что значительная часть крепёжных деталей, находящихся на этапе «Зрелость», приближается к «Упадку».
img011
Рис. 61. Диаграмма «жизненного цикла» крепежных изделий для АТС
Этап 4. Упадок. Качество и технический уровень товара перестаёт удовлетворять потребителей, он постепенно теряет применяемость, приходится снижать цены, падает рентабельность. Большие резервы повышения технического уровня крепёжных соединений, экономии средств, снижения трудоёмкости сборки остаются нереализованными. Имеется три определяющих причины медленного перехода на новые, прогрессивные крепёжные детали в машиностроении: а) основной массив российских стандартов на крепёжные изделия не гармонизирован со стандартами ИСО, у нас нет стандартов на большинство современных конструкций; б) экономические службы предприятий-потребителей крепежа не проводят объективного технико-экономического анализа в области крепёжных соединений; в) уровень знаний и квалификация специалистов по крепёжным деталям и соединениям недостаточны (настоящий материал имеет целью эту причину постепенно исправить).
Стареющий товар мешает началу энергичных действий по его замене. Например, автозаводы продолжают применять огромное количество шайб и болтов с шестигранной уменьшенной головкой. Если с шайбами всё ясно, то по болтам с шестигранной уменьшенной головкой обстановка сложнее. Показано, что применение этих болтов классами прочности выше, чем 6.8 – недопустимо. Но уменьшенный шестигранник изготавливают методом безотходной формовки, а не обрезкой граней, как у нормальных головок. Болты с уменьшенной головкой проще в изготовлении (3 перехода), имеют ниже норму расхода металла. Невысокая цена сдерживает принятие решений об отказе от них. Однако выход из положения застоя по этой конструкции имеется. Он состоит в переходе на прогрессивные винты с цилиндрической головкой, сферой и внутренним звездообразным приводом. Головки винтов тоже изготавливаются без отходов, но при этом опорная поверхность под головкой такая же, как у болтов с нормальным шестигранником. Применение винтов с прямым шлицем с каждым годом уменьшается из-за низких потребительских свойств: при сборке отвертка часто соскальзывает из шлица, портит присоединяемую деталь.
Рассмотренная диаграмма наглядно показывает, что и какого технического уровня мы выпускаем и используем в сборке АТС и что должны выпускать и применять, в том числе не только в автомобилях. Приведённые качественные характеристики выпускаемых крепёжных деталей позволяют их производителям и потребителям объективно оценивать перспективы своего развития.
Вопросы для самопроверки
- В чём различие между разъёмными и неразъёмными соединениями?
- В чём состоит принцип конструкции резьбовых соединений?
- Каковы области применения основных типов резьб?
- Каковы достоинства и недостатки резьбовых соединений?
- Для чего необходимо стопорение резьбовых соединений?
- Какие конструкции применяются для стопорения резьбовых соединений?
- Как распределяется нагрузка по виткам при затяжке резьбы?
- В чем различия к требованиям для крепежных и ходовых резьб?
- Каковы основные типы резьб?
- Каковы основные виды резьбовых соединений и их особенности?
- Каковы основные детали резьбовых соединений и их типы?
- Каковы основные способы стопорения резьбовых соединений?
- Как определить осевую силу в резьбовом соединении? Как определить эту силу, если коэффициенты трения неизвестны?
- Каковы основные случаи расчета резьбовых соединений?
- Почему болты, поставленные без зазора, обеспечивают при тех же диаметрах большую несущую способность соединения, чем поставленные с зазором?
- Каково влияние податливости в затянутых болтовых соединениях, нагруженных внешней силой?
- Чем вызвана неравномерность распределения нагрузки по виткам резьбы и как ее уменьшить?
- Как учитывается податливость деталей при расчёте резьбового соединения?
- Какой диаметр резьбы находят из прочностного расчёта?
- Какой диаметр резьбы служит для обозначения резьбы?
- Как происходит образование винтовой линии?
- Что такое профиль резьбы, шаг резьбы, угол профиля и угол подъема резьбы?
- Какие различают типы резьбы по назначению, по геометрической форме и какие из них стандартизованы? Основные параметры резьбы.
- Почему метрическая резьба с крупным шагом имеет преимущественное применение? Когда применяются резьбы с мелким шагом?
- Как повысить к.п.д. винтовой пары?
- Как рассчитывают болты (винты и шпильки) при действии на них постоянных нагрузок в следующих случаях: предварительно затянутый болт дополнительно нагружен осевой растягивающей силой; болт, установленный в отверстие с зазором и без зазора, нагружен поперечной силой?
- Опишите конструкции, разгружающие болт от восприятия поперечных сил.
- Если рассчитан диаметр болта d1, как определяют остальные (какие?) размеры болта? В каком случае применяют проверочный и проектировочный расчеты?
- Опишите работу пружинной шайбы. Предохраняют ли эти шайбы детали от задиров, увеличивают ли опорную поверхность?
- В какой резьбе, в треугольной или трапецеидальной, меньше потери на трение?
- Можно ли применять дюймовую резьбу при проектировании новых машин? Почему? Запишите обозначение этой резьбы на чертеже, если диаметр нарезаемой части винта равен одному дюйму.
- Перечислите резьбы для крепления деталей и для передачи движения.
- По сравнению с трапецеидальной резьбой упорная передает осевую силу (большую или меньшую). Почему?
- Назовите характеристики приводов: крестообразного шлица и внутреннего звездообразного. Дайте оценки их характеристикам по 10- балльной системе.
- Дайте характеристики функций в соединениях: болт с шестигранной уменьшенной головкой и болт со звездообразной головкой, малым фланцем и цилиндрическим направляющим концом.
- Для соединения пластмассовой крышки к корпусу из стального листа с отбортованными отверстиями можно применить винты самонарезающие с концом типа С или R и резьбовыдавливающие винты. Оба с фасонной головкой и фланцем, первый имеет крестообразный шлиц типа Н, второй – звездообразный. Какую конструкцию Вы предпочтёте? Почему?
- Предложите несколько альтернатив приварной гайке. Какому варианту Вы отдадите предпочтение и почему?
- Вам надо заменить болт с шестигранной уменьшенной головкой М8х25 классом прочности 6.8 с плоской и пружинной шайбами на крепёжную деталь класса прочности 8.8. Предложите не менее двух решений (болт, винт, др.).
- Каким равноценным болтом можно заменить Болт М10х50 классом прочности 6.8? Почему?
- Какие отличия имеют крестообразные шлицы типов Н и Z? Можно ли использовать для них общую отвёртку?
Дата добавления: 2019-01-14; просмотров: 199; Мы поможем в написании вашей работы! |
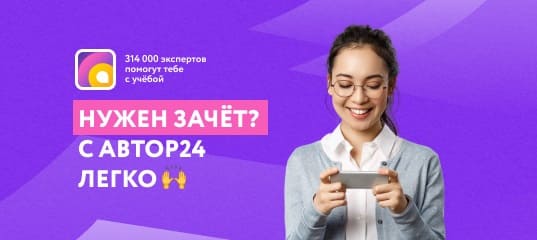
Мы поможем в написании ваших работ!