Мощность машин и её преобразование в механизмах 31 страница
d0 – диаметр отверстия под крепежную деталь, мм;
Р – шаг резьбы, мм;
d2 – средний диаметр резьбы, мм.
Наибольшее влияние на затяжку соединений оказывают условия контактного трения в резьбе и на опорной поверхности, зависящие от состояния контактных поверхностей, вида покрытия, наличия смазочного материала, отклонение от перпендикулярности опорного торца и оси резьбы, скорости завинчивания и др. Значения коэффициента трения в реальных условиях сборки можно лишь прогнозировать. Как показывают многочисленные эксперименты, они не стабильны. Для понимания и правильного назначения режимов сборки резьбовых соединений важно знать, на что расходуется Мкр. Три составляющие момента затяжки (согласно формуле) отражают их доли, идущие на создание усилия затяжки (12…15%), на преодоление сил трения в резьбе (32…39%) и на преодоление сил трения под головкой болта или под гайкой (47…54%). Как видим, на создание усилия затяжки расходуется меньшая доля от Мкр. В расчётах обычно принимают, что коэффициенты трения в резьбе и на опорном торце примерно равны.
При применении соединений с фланцевыми болтами и гайками важно учитывать влияние на момент затяжки увеличенной опорной поверхности под головкой. Момент требуется на 10-15% выше, чем без фланца.
Способ затяжки по моменту из-за сильного влияния условий трения не обеспечивает достижения необходимого усилия затяжки.
|
|
Рассмотрим пример соединения болт-гайка М8 класса прочности 8.8-8, покрытие цинковое с хроматированием без смазочного материала, номинальное усилие затяжки Q = 15900 Н, Мкр max = 24,4 Нм. Построим диаграмму в координатах Q – Мкр (рис. 43) при значениях коэффициентов трения 0,3, 0,14 и 0,10 для соединений 1I и III классов. Виден весьма существенный разброс достигаемых значений усилия затяжки (заштрихованная четырехугольная зона) при заданных крутящих моментах. Для соединений II класса это А2ВСD2, а III класса – А3ВСD3.
img072
Рис. 43
Минимально достигаемое усилие затяжки Qmin получается при приложении минимального крутящего момента затяжки Мкр. min при максимальном коэффициенте трения μmax (точки А2 и А3 на диаграмме).
Максимальное усилие затяжки Qmax достигается при приложении максимального крутящего момента Мкр. max при наименьшем коэффициенте трения μmin (точка С на диаграмме). Подобные графические изображения могут быть построены для каждого конкретного резьбового соединения.
Точка соответствующего соотношения Мкр. – Q находится внутри четырёхугольника. Показано, что способ затяжки с контролем момента даже при его точной фиксации не обладает необходимой надежностью, далеко не всегда обеспечивает нужное усилие затяжки.
|
|
Предлагаемые методы контроля основаны на замере не усилия затяжки, а момента страгивания затянутой крепёжной детали в направлении затяжки, то есть базируются на косвенных методах – приложением вращающего момента.
В мировой практике имеется опыт применения методов и инструментов, которые непосредственно контролируют усилие затяжки в ходе сборки. Исследования показывают, что наибольшая точность обеспечения усилий затяжки (в том числе в производственных условиях) возможна лишь при затяжке до предела текучести. Система автоматического регулирования сборки позволяет уловить момент, когда малое приращение усилия происходит при значительном угле поворота инструмента. Однако эти методы и инструменты сложны и дороги.
Поэтому особо следует остановиться на контроле качества коррозионных и декоративных покрытий резьбовых крепёжных деталей. По нормам крупнейших автопроизводителей величина коэффициента трения в резьбе и на опорных торцах деталей может лишь незначительно отличаться от μ= 0,1. Разработаны фирменные стандарты на определение коэффициента трения путём соответствующих испытаний. Сборка с контролем усилия затяжки требует значительно больших затрат, чем обеспечение стабильности коэффициента трения, поэтому ему и отдано предпочтение.
|
|
В конструкторской и технологической документации необходимо указывать усилие предварительной затяжки как основное требование, а момент затяжки использовать только как справочную величину. В стандартах и руководящих документах на затяжку резьбовых соединений следует иметь оба этих показателя, а не только моменты.
Зависимость между моментом, приложенным к гайке, и осевой силой
Подавляющее большинство резьбовых соединений с предварительной затяжкой. Затяжка создается при сборке с целью, чтобы после приложения рабочей нагрузки не происходило раскрытия стыка или сдвига соединяемых деталей.
При завинчивании гайки (рис.44) к ключу прикладывают вращающий момент
Tкл=Fкл∙Lр, (1)
где Fкл — усилие на конце ключа; Lp — расчетная длина ручки ключа.
Рис.44. К расчету момента на ключе
Момент движущих сил равен сумме моментов сил сопротивления, т. е.
|
|
Tкл=T+TT, (2)
где Т — момент в резьбе; ТT — момент сил трения на опорном торце гайки. Момент в резьбе определяют по формуле
где F3 — сила затяжки болта (осевая сила, растягивающая болт); Ψ— угол подъема винтовой линии; d2 — средний диаметр резьбы; φ’ — приведенный (с учетом влияния угла профиля α) угол трения в резьбе: φ’ = φ/cos(α/2), φ – угол трения материалов пары винт – гайка.
Момент сил трения на опорной поверхности
Здесь f≈0,15- коэффициент трения между поверхностью гайки (головки) и детали; D — диаметр захвата гаечного ключа (опорного торца гайки); d0=d1+(1÷1,5) мм — диаметр отверстия в детали под болт.
Подставляя полученные выражения Т и ТT в формулы (1) и (2) для момента завинчивания, получим момент на ключе
Длина стандартных ключей: L = 15d при f≈0,15; Fз/Fкл=70÷80, где Fкл – усилие рабочего.
Распределение осевой нагрузки по виткам резьбы
При нагружении осевая сила распределяется между витками неравномерно. Неравномерность распределения сил по виткам усугубляется тем, что витки на наиболее растянутой части винта сопрягаются с витками, расположенными в наиболее сжатой части гайки. Задача о распределении нагрузки по виткам статически неопределима. Распределение сил между витками резьбы, полученное Н.Е. Жуковским в 1902г. для гайки с десятью витками, показано на рис.45,а. В дальнейшем это решение неоднократно подтверждалось экспериментальными исследованиями. Установлено, например, что при стандартной крепежной гайке с шестью витками, первый виток резьбы воспринимает 52% нагрузки, второй 25%, третий 12% и последний шестой – только 2% нагрузки.
При столь неравномерном распределении нагрузки по виткам резьбы большое увеличение высоты гайки оказывается бесполезным в связи с опасностью последовательного «цепного» разрушения витков. Приближенно – равномерное распределение нагрузки по виткам резьбы можно получать, только применяя гайки специальной формы, выравнивающие распределение нагрузки в резьбе. Специальные гайки желательно применять при действии переменных и динамических нагрузок, где разрушение носит усталостный характер.
Висячая гайка. Выравнивание нагрузки в резьбе здесь достигается благодаря тому, что винт и гайка имеют однозначные деформации растяжения (рис. 45,б). Кроме того, в наиболее нагруженной зоне (внизу) висячая гайка обладает повышенной податливостью, что также способствует выравниванию нагрузки в резьбе.
Гайка со срезанными витками. У такой конструкции резьбовой пары увеличена податливость нижних витков винта, так как они соприкасаются с гайкой не всей поверхностью, а только своими вершинами (рис. 45,в). Увеличение податливых витков в наиболее нагруженной зоне снижает нагрузку этих витков.
а)
б) в)
Рис.45. Схема распределения нагрузки между витками резьбы по Н.Е. Жуковскому
Условие самоторможения в резьбе
Условие самоторможения можно записать в виде Тотв > 0. Рассматривая самоторможение только в резьбе без учета трения на торце гайки, получим tg(φ1-Ψ)>0 или
Ψ<φ1. (6)
Для крепежных резьб значение угла подъема Ψ лежит в пределах 2°30' – 3°30', а угол трения φ изменяется в пределах 6° (при f≈0,1) – 16º (при f≈0,3). Таким образом, все крепежные резьбы – самотормозящие. Резьбы для ходовых винтов выполняют как самотормозящие, так и несамотормозящие.
Приведенные выше значения коэффициента трения, свидетельствующие о существенных запасах самоторможения, справедливы только при статических нагрузках. При динамических и вибрационных нагрузках вследствие взаимных микросмещений поверхностей трения коэффициент трения существенно снижается и условие самоторможения нарушается. Происходит самоотвинчивание во избежание которого применяют специальные стопорные устройства (см. способы стопорения резьбовых соединений).
КПД винтовой пары
КПД винтовой пары η определяется отношением работы, затраченной на завинчивание гайки без учета трения, к той же работе с учетом трения. Работа завинчивания равна произведению момента завинчивания на угол поворота гайки. Так как углы поворота равны и в том и в другом случае, то отношение работ равно отношению моментов , в котором Tзав определяется по формуле, а – по той же формуле, но при f=0 и φ=0:
В винтовой паре основной критерий качества передачи энергии - коэффициент полезного действия (КПД) в отличие от большинства передач различается в зависимости от того, какое движение является ведущим. Так, если ведущим является вращательное движение – вращающийся винт сообщает поступательное движение невращающейся гайке, или, например, вращением гайки при затяжке соединения ей сообщается поступательное движение, КПД определяется соотношением (учитывая потери только в резьбе (fТ = 0)):
Формула (8) позволяет сделать вывод, что η возрастает с увеличением Ψ и уменьшением φ. В самотормозящей паре Ψ< 𝜑 и η< 0,5. КПД винтовой пары представляет интерес главным образом для винтовых механизмов. Максимальное значение η можно определить из выражения (8), приравняв нулю производную . Получим ηmax при Ψ=45°-φ/2. Для увеличения угла подъема резьбы применяются в винтовых механизмах многозаходные резьбы. Обычно Ψ не превышает 250, так как дальнейший прирост КПД незначителен, а изготовление резьбы затруднено.
Если же ведущим становится поступательное движение, например, при попытке вращать винт посредством перемещения вдоль его оси, закреплённой от проворота гайки (как в механизме самовращающей отвёртки), то КПД
В этом выражении (8.1) при углах подъёма равных или меньших чем приведённый угол трения числитель становится равным нулю или даже отрицательным, что является сигналом невозможности передачи энергии, а, значит, и движения в данном направлении. Следовательно, крепёжные резьбы с точки зрения стопорения от самоотвинчивания предпочтительно выполнять с мелкими шагами, обеспечивая тем самым наименьший угол подъёма резьбы.
Для повышения КПД винтовых механизмов применяют средства, снижающие трение в резьбе: антифрикционные материалы, смазку поверхностей, применение шариковых винтовых пар.
Расчет резьбы на прочность
При расчете резьбы на прочность принимают следующее допущение: все витки резьбы нагружаются равномерно (хотя теоретическими и экспериментальными исследованиями установлено, что для гайки с шестью витками первый виток резьбы воспринимает 52% всей осевой нагрузки, второй — 25%, третий — 12%, шестой — только 2%). Действительный характер распределения нагрузки по виткам зависит от ошибок изготовления и степени износа резьбы, что затрудняет определение истинных напряжений. В практике расчет резьбы на прочность производится не по истинным, а по условным напряжениям, которые сравнивают с допускаемыми напряжениями, установленными на основании опыта. Полагая нагружение витков равномерным, резьбу принято рассчитывать по напряжениям смятия и среза.
Рис. 46. К расчету резьбы на срез
Расчет резьбы по напряжению смятия.
Условие прочности витка резьбы по смятию:
а) для гайки
б) для винта
где F - осевая сила, действующая на болт, d2 - средний диаметр резьбы, h - высота витка, z - число витков резьбы в гайке, [σ]смв - допускаемое напряжение смятия материала винта, [σ]смг - допускаемое напряжение смятия материала гайки.
Расчет резьбы по напряжению среза.
Проверочный расчет. Условие прочности
τср≤[τ]ср,
где τср — расчетное напряжение среза в резьбе; [τ]ср — допускаемое напряжение среза в резьбе.
Для винта:
для гайки
здесь F — осевое усилие, действующее на болт; d1 — внутренний диаметр резьбы; d — наружный диаметр резьбы; Н — высота гайки; K=cd/P — коэффициент, учитывающий тип резьбы (K=0,8 — для треугольной резьбы; К= 0,5 — для прямоугольной и К= 0,65 — для трапецеидальной резьбы).
Проектировочный расчет (рассматривается случай, когда материал гайки и винта одинаков). Задавшись типом резьбы и определив диаметр при проектном расчете, можно определить высоту гайки:
Стандартные крепежные изделия на прочность резьбы не рассчитывают.
Из условия равнопрочности резьбы и стержня винта определяются высота гайки, нормы на глубину завинчивания винтов и шпилек в деталь и прочие размеры. Учитывая сложность напряженного состояния резьбы, а, также предусматривая ослабление резьбы от истирания и возможных повреждений при завинчивании, высоту стандартных гаек крепежных изделий принимают H≈0,8d1. По тем же соображениям устанавливают нормы завинчивания винтов и шпилек в детали H=d1 – в стальные детали, H=1,5d1 – в чугунные и силуминовые детали.
Выбор стандартных крепежных изделий
Стандартизация резьб проведена с учетом условия равнопрочности всех элементов соединения. Поэтому можно ограничиться расчетом по одному, основному критерию - прочности нарезанной части, а размеры винтов, болтов и гаек принимать по таблицам стандартов в зависимости от рассчитанного диаметра резьбы.
Выбор производят по наружному диаметру резьбы по стандартам на крепежные изделия.
Таблица 10. Основные размеры метрической резьбы с крупным шагом
Стандартный наружный диаметр резьбы d, мм
М10
М12
М16
М18
М20
М24
М27
Крупный шаг резьбы S, мм
1,5
1,75
2
2,5
2,5
3
3
Внутренний диаметр резьбы d1, мм
8,37
10,1
13,83
15,29
17,29
20,75
23,75
Размер под «ключ» головки болта
17
19
24
27
30
36
41
Диаметр отверстия при установке с зазором d0, мм
10,5
13
17
19
21
25
28
Длины болтов
от 20
от 20
от 25
от 30
от 30
от 35
от 45
Ряд стандартных длин болтов: 20, 25, 30, 32, 35, 40, 45, 50, 55, 60, 65, 70, 75, 80, 90, 100, 110…
Стандарты приведены в справочниках конструктора (см. литературу).
Материалы резьбовых изделий и допускаемые напряжения
При выборе материала для резьбовых деталей учитывают величину и характер нагрузки (статическая или переменная), условия работы (температуру, коррозию и т. д.), способ изготовления.
Для изготовления крепёжных резьбовых деталей используются самые различные материалы, чаще всего цветные (алюминий, медь, титан и их сплавы) и чёрные металлы (углеродистые и легированные стали). Тем не менее, основная масса потребляемых промышленностью резьбовых изделий изготавливается из сталей. Стандартные крепежные изделия общего назначения изготовляют из углеродистых сталей типа сталь 10 - сталь 35. Эти стали, позволяют изготовить большие партии болтов, винтов, гаек методом холодной высадки с последующей накаткой резьбы. Легированные стали 35Х, 30ХГСА применяют для высоконагруженных деталей при переменных и ударных нагрузках. Механические свойства крепежных изделий определяются как материалом, так и технологией изготовления. Декоративные винты и гайки выполняются из цветных металлов и пластмасс. Выбор материалов, как и всех параметров резьбовых соединений, определяется расчётом на прочность.
При этом крепёж, изготовленный из разных сталей, может иметь одинаковые прочностные характеристики, а детали, изготовленные из одной и той же стали, но получившие разную термообработку, могут значительно различаться по своим прочностным характеристикам. Отсюда следует, что при заказе стандартных резьбовых деталей недостаточно указать материал, из которого они должны быть изготовлены, но ещё необходимо показать требуемые прочностные характеристики материала заказываемых деталей. Обозначение прочностных характеристик крепёжных резьбовых деталей стандартизовано (стальные винты и шпильки по ГОСТ 1759-82) и представлено 12-ю классами прочности. Оно состоит из двух цифр, разделённых точкой (в некоторых документах точка не ставится): первая цифра представляет предел прочности материала, выраженный в МПа и поделённый на 100; вторая цифра (стоящая после точки) равна отношению предела текучести материала к его пределу прочности умноженному на 10. В стандарте представлены следующие классы прочности: 3.6; 4.6; 4.8; 5.6; 5.8; 6.6; 6.8; 6.9; 8.8; 10.9; 12.9; 14.9.
Класс 4.6 – предел прочности σв=400 МПа и предел текучести σт=240 МПа. Выдержка из ГОСТ 1759-82 «Изделия крепёжные. Общие технические требования» приведена в таблице 3.
Дата добавления: 2019-01-14; просмотров: 203; Мы поможем в написании вашей работы! |
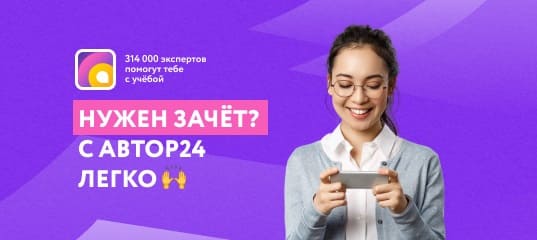
Мы поможем в написании ваших работ!