Мощность машин и её преобразование в механизмах 28 страница
Рис.19. Примеры специальных болтов
Шпильки
На рис. 14, в, г показана шпилька. Шпильки применяют, когда по конструктивным особенностям соединений установить болт или винт нельзя и когда по условию эксплуатации требуется частая разборка и сборка соединения деталей, одна из которых имеет большую толщину. Применение винтов в этом случае привело бы к преждевременному износу резьбы детали при многократном отвинчивании и завинчивании. При динамических нагрузках прочность шпилек выше, чем прочность болтов. Шпильку ввинчивают в деталь при помощи гайки, навинченной поверх другой гайки или при помощи специального шпильковерта.
Шпилька — резьбовое изделие цилиндрической формы, имеющее с обоих концов резьбы, один конец которой (головка) ввинчивается в деталь, для чего имеет с этой стороны тугую нарезку, а на другой навинчивается гайка. Резьбовое изделие, показанное на рис. 14, г, можно назвать болтом-шпилькой.
При разборке свинчивается только гайка и тугая резьба в корпусе не повреждается. Шпильки рекомендуется применять при чугунных или алюминиевых корпусах.
Шпильки делят на два типа по ГОСТ 11765-81: с проточкой (рис. 20, а); без проточки, со сбегом резьбы на посадочном конце (рис. 20, б). Один конец шпильки ввинчивается в тело детали до отказа с затяжкой на сбег резьбы (шпилька ввинчивается, например, с помощью двух гаек, рис. 37, а). Диаметр резьбы на обоих концах шпильки, как правило, одинаков. Глубина ввинчивания lш зависит от материала детали, определяется по табл. 5.
|
|
Рис. 20. Конструкции шпилек
Таблица 5. Минимальная относительная длина завинчивания lш в корпус шпилек (винтов),
изготовленных из различных материалов
σв стальной шпильки (винта), МПа
lw/d при материале корпуса (σв, МПа)
Сталь
(300-400)
Дюралюминий (360-400)
Бронза
(250-200)
Чугун (180-250)
Силумин (160-200)
400-500
0,8-0,9
0,8-0,9
1,2-1,3
1,3-1,4
1,4-2,0
900-1000
1,6-2,0
1,6-2,0
1,8-2,2
1,8-2,2
2,0-2,5
Гайки
Болты и шпильки снабжены гайками.
Гайки имеют различную форму. Наиболее распространены шестигранные гайки. На рис. 21 показаны шестигранные гайки, применяемые в машиностроении: а — с одной фаской; б — с одной фаской и проточкой; в — прорезные; г — корончатые. У корончатых гаек для установки стопорных шплинтов выполнены прорези. Имеются и другие конструктивные разновидности шестигранных гаек. В зависимости от высоты шестигранные гайки бывают нормальные, высокие и низкие. Высокие гайки применяют при частых разборках и сборках для уменьшения износа резьбы. Прорезные и корончатые гайки также выполняют высокими. В зависимости от точности изготовления шестигранные гайки, аналогично болтам, бывают нормальной и повышенной точности. Для крепления подшипников качения, рулевого устройства в велосипедах, мотоциклах и других машинах применяют круглые гайки со шлицами (рис. 21, д). При частом отвинчивании и завинчивании с небольшой силой затяжки применяют гайки-барашки (рис. 21, е, ж).
|
|
Рис. 21. Конструктивные формы гаек
Рис. 22. Гайки
На рис. 22: в — шестигранная гайка с двумя фасками для больших осевых нагрузок; г — шестигранная гайка с одной фаской для незначительных осевых нагрузок; ж — шестигранная гайка с глухим резьбовым отверстием; з — шестигранная гайка с буртиком; и — круглая гайка с накаткой и углублением под ключ; к — круглая гайка с отверстиями на торце под ключ.
Резьбовое соединение нестандартными деталями
Помимо резьбовых соединений, осуществляемых при помощи стандартных крепежных деталей, находят широкое применение резьбовые соединения, в которых резьба выполняется непосредственно на деталях, входящих в соединение.
На рис.23 представлено соединение трубы 1 со штуцером 2, осуществляемые при помощи накидной гайки 3 и втулки 4, прижимающей коническую развальцованную часть трубы к штуцеру.
|
|
Рис.23
Крепёжные детали с фланцем
В США в 60-х годах прошедшего столетия шайбы соединили с головками болтов и гайками. Диаметр фланцев примерно равен наружному диаметру нормальных шайб и выбран неслучайно – было установлено, что оптимально контактные напряжения под головками болтов класса прочности 8.8 должны быть в пределах 170…180 МПа. В соединениях стало меньше деталей, снизилась трудоёмкость сборки узлов, стали возможными переход на крепёжные детали более высокого класса прочности и уменьшение их размеров. Расчёты и испытания показывают, что при использовании фланцевого крепежа существенно повышается надёжность резьбового соединения, так как под головкой от прилагаемых усилий затяжки и рабочих нагрузок не возникают пластические деформации в соединяемой детали. Увеличение площади опорной поверхности обеспечивает ещё и значительно лучшие стопорящие свойства.
Имеются: ГОСТ Р 50592-93 Гайки шестигранные с фланцем класса точности А. Технические условия; ГОСТ Р 50274-92 Болты с шестигранной уменьшенной головкой и фланцем. Технические условия. На болты с шестигранной (нормальной) головкой и фланцем российского стандарта пока нет, можно пользоваться стандартом ДИН 6921.
|
|
На болтах и гайках с фланцем классов прочности 8.8 – 8 и выше часто применяют конструкцию опорной поверхности фланца с поднутрением, направленным от наружной части в сторону стержня. Это повышает стопорящие свойства.
На рис. 24 приведена диаграмма контактных напряжений под головками болтов класса прочности 8.8. При затяжке соединения контактные напряжения σН под головкой болтов с шестигранной уменьшенной головкой существенно превышают напряжения течения σт материала соединяемых деталей (пунктирные линии). Усилие затяжки при переходе с болтов класса прочности 6.8 на 8.8 возрастают в 1,6…3,2 раза. Это в большинстве случаев приводит к местным деформациям на соединяемых деталях и в результате ускоряет ослабление соединения.
img078
Рис. 24
В зарубежном машиностроении (автомобили и двигатели, тракторы и сельхозмашины, станки и другая техника) применяют болты и винты повышенных классов прочности – не ниже 8.8, мелкие винты и неответственные детали могут иметь классы 4.8, 5.6, 6.8. Например, структура болтов по прочности в автомобилях Западной Европы такова: размеры М6 – М10: 8.8 – 90%, 10.9 – 8%, 12.9 – 1%, а размеры М12 и выше: 8.8 – 31%, 10.9 – 61%, 12.9 – 2%. Болтов с прочностью ниже 8.8 очень мало. Таковы же характеристики болтов в автомобилях АвтоВАЗа.
Казалось бы, что вместо болтов с шестигранной уменьшенной головкой можно применять болты с нормальной головкой по ГОСТ 7805. Но это почти всегда сопряжено с отсутствием места для размещения монтажного инструмента. Можно под уменьшенную головку болта повышенной прочности поставить закалённую плоскую шайбу. Но такое соединение дороже, трудоёмкость сборки выше. Повышение класса прочности крепежной детали требует изменять конструкцию соединения.
Резьбовыдавливающие крепёжные детали
Общепринятый способ соединения деталей и узлов, осуществляемый обычными болтами, винтами и шпильками, связан с необходимостью использования гаек или нарезания резьбы в отверстии, и для этого нужен резьбонарезной и контрольный инструмент, трудовые и иные затраты. Это обстоятельство способствовало изобретению крепёжных деталей, способных во время сборки выдавливать резьбу в гладком отверстии и при этом обеспечивать стопорение соединений. Отверстия под резьбовыдавливающие детали можно получать сверлением, пробивкой или при отливке. Эффективно применение резьбовыдавливающих винтов в отбортованных отверстиях листовых деталей: прочность соединения по сравнению с нарезкой резьбы увеличивается на 20-30%. Диаметр отверстия под винт делают несколько больше среднего диаметра резьбы (≈1,03dср). Он зависит от материала и глубины ввинчивания в отверстие. Установка в гладкое отверстие осуществляется теми же винтовёртами, что и обычные винты, так как вращающий момент формообразования резьбы всегда меньше момента затяжки резьбового соединения.
Резьбовыдавливающие крепёжные детали подлежат термообработке. Минимальное требование – нитроцементация на глубину 0,08…0,28 мм (зависит от диаметра винта), твёрдость не менее 450 НV.
Наиболее применяемая конструкция резьбовыдавливающих винтов и болтов имеет метрическую резьбу на стержне трёхгранной (лобулярной) формы. В мировой практике такой вид крепёжных деталей называют «Taptite» (Тептайт). На рис. 25 показано поперечное сечение стержня и заходная часть на его конце, где D – диаметр окружности, описывающей профиль, равный номинальному диаметру резьбы и имеющий допуск близкий к полю допуска гайки – 6Н; C – размер трёхгранного профиля сечения стержня, замеренный по любой произвольной оси, равен сумме радиусов, образующих профиль: C = R1+R2 ( R1 – радиус вершины профиля, R2 – радиус основания профиля); k – некруглость профиля, характеризующая отклонение профиля от круга. Большей величине k соответствуют меньшие вращающие моменты образования резьбы и, наоборот, чем больше отклонение профиля от круга, тем меньше поверхность контакта резьбы винта с резьбой, сформированной в изделии, и ниже прочностные характеристики соединения.
img001
Рис. 25
Важным элементом резьбовыдавливающих крепёжных деталей является заходная часть с плавным сбегом резьбы. Она может иметь разные исполнения. На рис. 25 приведено сечение наиболее применяемого вида с постепенным уменьшением высоты вершин резьбы, где D1 – внутренний, а D2 – средний диаметр резьбы. Такой заход обеспечивает меньший момент образования резьбы.
В отечественной промышленности такие крепёжные детали начали выпускать и применять в конце 80-х годов в автомобильной промышленности, было выпущено 7 стандартов ОСТ 37.001.315…321-88 на болты, винты и шпильки резьбовыдавливающие. Их приёмка производится в соответствии с ТУ 37.103.040-96 «Резьбовыдавливающие крепёжные изделия». Международные стандарты: ДИН ЕН ИСО 887, 7046…7048.
Резьбовыдавливающий крепёж многофункционален – его применяют в автомобилях, в автокомпонентах, в том числе для крепления к деталям из алюминиевых сплавов, нарезка резьбы в которых – очень трудоёмкая операция. Этот вид крепёжных деталей применяют в других отраслях, они удобны в быту: могут быть применены вместо метчика, исправляют испорченную резьбу в отверстии, зачищают в ней краску и т. д.
Болты и винты со звездообразным приводом
Звездообразный привод, известный под товарным названием «TORX», в РФ начали применять в начале 90-х годов. Надёжность и прочность резьбовых соединений в значительной степени зависит от обеспечения требуемого усилия затяжки при сборке узла. Большое значение для передачи вращающего момента имеет величина площади контакта рабочей части монтажного инструмента и привода крепёжной детали. Наибольшую поверхность контакта имеет звездообразный привод (рис. 26), он реже выходит из строя по сравнению с другими формами и способен передавать наибольший крутящий момент. Несомненными преимуществами такого привода в сравнении с шестигранной головкой являются экономия металла и снижение веса головок (рис. 27), существенное уменьшение габаритов конструкции для размещения головки болта и монтажного инструмента (рис. 28). Применение звездообразного привода открывает наилучшие возможности для унификации конструкций резьбовых соединений.
Наибольшее распространение болты и винты со звездообразным приводом получили для соединений повышенной прочности и высокими усилиями затяжки, например, в автомобильной технике: в креплениях головки к блоку цилиндров двигателей, крышек подшипников распределительного и коленчатого валов, замков и петель дверей, автокомпонентах – в приборах, фарах и многих других узлах. Много таких винтов в зарубежной бытовой технике – в газовых и электрических плитах, холодильниках, стиральных машинах. Только такой привод специальных винтов обеспечивает надёжное крепление твёрдосплавных пластин сборных фрез и резцов.
В РФ введены три стандарта. ГОСТ Р ИСО 10664-2007 Звездообразное углубление под ключ для винтов. Конструкция и размеры. Методы контроля. Винты с таким шлицем могут иметь любую из применяемых головок. ГОСТ Р 52854-2007 Болты со звездообразной головкой и малым фланцем. Технические условия. Эти болты имеют площадь опорной поверхности как болт с шестигранной нормальной головкой. ГОСТ Р 52855-2007 Болты со звездообразной головкой и большим фланцем. Технические условия.
img003img074
Рис. 26 Рис. 27
img010
Рис. 28
Сравним разные формы приводов по следующим показателям:
- вращающий момент, передаваемый от отвёртки или ключа;
- площадь поверхности контакта инструмента с головкой и связанная с ней долговечность привода и инструмента при многократных сборках-разборках;
- величина пространства, требующегося для расположения монтажного инструмента на головке крепёжной детали;
- технологичность и экономичность изготовления головки;
- обеспечение возможности контроля качества затяжки по моменту страгивания при отвинчивании;
- осевые нагрузки на инструмент при сборке и разборке и др.
Итоговая оценка приводов позволяет расположить их по возрастанию надёжности и выгодности применения. По 10-балльной системе имеем: прямой шлиц – 1 балл, крестообразные шлицы типа Н и Z – 1,5…2 балла соответственно, внутренний шестигранник – 3 балла, наружный шестигранник и внутренний звездообразный – по 6 баллов, звездообразная головка – 9 баллов.
Винты самонарезающие
Соединения, образуемые самонарезающими винтами, широко распространены в машиностроении и других отраслях и продолжают динамично развиваться. Их отличает высокая технологичность работ по выполнению соединений – не требуется нарезки резьбы в отверстии, можно обойтись без гайки, имеется возможность получать отверстие во время сборочной операции. Самонарезающие винты применяются с деталями из низкоуглеродистых сталей, сплавов на основе алюминия и меди, из пластмасс. В порядке информации: название «самонарезающий» не соответствует фактическому характеру образования резьбы таким винтом. Резьба винта не срезает материал, а вдавливается в него, то есть имеет место пластическая деформация.
При проектировании следует руководствоваться стандартами:
ГОСТ Р ИСО 1478-93 Резьба винтов самонарезающих, ГОСТ Р ИСО 2702-93 Винты самонарезающие стальные термически обработанные. Общие технические условия, ГОСТ Р ИСО 7049; 7050 и 7051-93 Винты само-нарезающие с цилиндрической головкой и сферой с крестообразным шлицем. Технические условия (соответственно с потайной и полупотайной головками). Российских стандартов на винты с фасонной головкой и фланцем, а также винтов со звездообразным приводом пока нет, хотя это одни из наиболее прогрессивных конструкций.
Применение новых видов самонарезающих винтов в РФ осложнено из-за разных размеров резьбы. В табл. 6 приведены параметры резьбы – наружный диаметр ST и шаг Р (в мм) по трём, одновременно действующим в настоящее время стандартам. Соответственно различаются стандарты на конструкции и размеры винтов.
Таблица 6
ГОСТ 10618-80
ST
Р
3
1,25
4
1,75
5
2,0
6
2,5
Нормы Фиат-ВАЗ табл.01531,
СТП 37.101.7506-76
ST
Р
2,9
1,058
3,6
1,411
4,3
1,693
4,9
2,177
5,6
2,309
6,5
2,540
ГОСТ Р ИСО 1478-93
ИСО 1478-2005
ST
Р
2,9
1,1
3,5
1,3
4,2
1,4
4,8
1,6
5,5
1,8
6,3
1,8
В таблице 9 приведена новая форма конца винтов самонарезающих, согласно стандарту ИСО 1478-2005 - скруглённый - тип R. В ближайшее время ожидается, что все российские стандарты на самонарезающие винты будут приведены в соответствие с последними версиями стандартов ИСО. Это необходимо учитывать при новом проектировании.
Для соединений с самонарезающими винтами важно правильно назначить диаметр отверстия в зависимости от толщины листа, глубины отверстия и марки материала детали. На рис.29 показаны основные варианты соединений листовых деталей. При соединении листов толщиной S больше шага резьбы Р в верхнем листе выполняют отверстие диаметром D > d1, где d1 – наружный диаметр резьбы, а в нижнем – диаметр dотв, который зависит от толщины этого листа. Если толщина металлического листа S < Р, то отверстие может быть проколото самонарезающим винтом с конусным концом сразу в обоих листах. Одно из наиболее рациональных решений – выполнить в нижнем листе отверстие с отбортовкой – прочность соединения на вырывание винта возрастает в 1,5…1,8 раза. Популярностью пользуются соединения с одновитковой U-образной пластинчатой гайкой (таблица 9), обладающей стопорящими свойствами.
img009
Рис. 29
При определении размеров отверстий детали под винт надо стремиться обеспечить наибольшую прочность соединения. При S < (1-2)Р диаметр отверстия должен лишь незначительно превышать внутренний диаметр резьбы винта d2. Такие детали образуют соединения типа «одно- или двухвитковая гайка». ГОСТ Р ИСО 2702-93 устанавливает минимальное сопротивление скручиванию (отрыву) головки винта Мскр, которое служит ориентиром при проектировании соединений: вращающий момент, необходимый для установки винтов, не должен превышать 70…75% от момента скручивания.
Дата добавления: 2019-01-14; просмотров: 230; Мы поможем в написании вашей работы! |
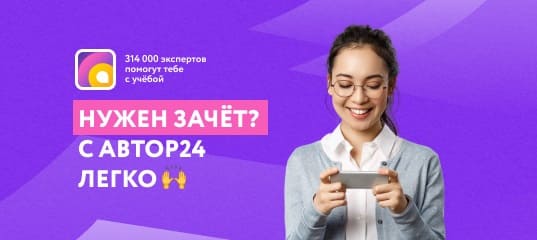
Мы поможем в написании ваших работ!