Мощность машин и её преобразование в механизмах 25 страница
Подвижные соединения определяют кинематику машины, а неподвижные – позволяют расчленить машину на отдельные блоки, элементы, детали.
С точки зрения общности расчетов все соединения делят на две большие группы: неразъемные и разъемные соединения.
Неразъемными называют соединения, которые невозможно разобрать без разрушения или повреждения деталей. К ним относятся заклепочные, сварные, клеевые соединения, а также соединения с гарантированным натягом. Неразъемные соединения осуществляются силами молекулярного сцепления (сварка, пайка, склеивание) или механическими средствами (клепка, вальцевание, прессование).
Разъемными называют соединения, которые можно многократно собирать и разбирать без повреждения деталей. К разъемным относятся резьбовые, шпоночные и шлицевые соединения, штифтовые и клиновые соединения.
По форме сопрягаемых поверхностей соединения делят на плоское, цилиндрическое, коническое, сферическое, винтовое и т.д.
Проектирование соединений является очень ответственной задачей, поскольку большинство разрушений в машинах происходит именно в местах соединений.
К соединениям в зависимости от их назначения предъявляются требования прочности, плотности (герметичности) и жесткости.
При оценке прочности соединения стремятся приблизить его прочность к прочности соединяемых элементов, т.е. стремятся обеспечить равнопрочность конструкции.
|
|
Требование плотности является основным для сосудов и аппаратов, работающих под давлением. Уплотнение разъемного соединения достигается за счет:
1) сильного сжатия достаточно качественно обработанных поверхностей;
2) введения прокладок из легко деформируемого материала.
При этом рабочее удельное давление q в плоскости стыка должно лежать в пределах q = (1,5…4)p, p – внутренне давление жидкости в сосуде.
Экспериментальные исследования показали, что жесткость соединения во много раз меньше жесткости соединяемых элементов, а поскольку жесткость системы всегда меньше жесткости наименее жесткого элемента, то именно жесткость соединения определяет жесткость системы.
Выбор типа соединения определяет инженер.
Классификация крепёжных изделий и их элементов. Терминология
Простейшая классификация крепёжных изделий может проводиться по нескольким направлениям: резьбовые и без резьбы, стержневые и с функциональным отверстием, изделия типа болт с невыпадающей шайбой относят к комбинированным и т.д.
В отдельных стандартах и в разных государствах встречаются отличающиеся друг от друга названия одинаковых деталей. В первую очередь это относится к терминам «болт» и «винт». В настоящем материале использованы определения:
|
|
привод - конструктивный элемент крепёжной детали, служащий для передачи крутящего момента;
болт – резьбовая крепёжная деталь с головкой и наружным приводом или конструктивным элементом головки, удерживающим болт от поворота (квадратный подголовок, ус и другие);
винт – резьбовая крепёжная деталь с приводом, расположенным внутри головки или стержня.
Стержневые крепёжные детали состоят из нескольких составных частей.
Конструкции таких широко применяемых изделий, как шпильки, заклёпки (в том числе полупустотелые, пустотелые), пальцы, штифты (в том числе с резьбовой частью), шплинты, многочисленные конструкции шайб и другие – не рассматриваются. Информация о них в достаточной степени имеется в справочниках, больших изменений за последние годы эти конструкции не претерпели.
Общие технические требования и нормы
Всего на крепёжные изделия имеется около 350 государственных стандартов. Из них в машиностроении используют 210 – 220. Ниже приведён перечень нескольких базовых стандартов общего назначения по состоянию на январь 2008 года. Ими следует руководствоваться при производстве и применении крепёжных деталей.
|
|
ГОСТ 1759.0-87 Болты, винты, шпильки и гайки. Технические условия.
ГОСТ 1759.1-82 Болты, винты, шпильки, гайки и шурупы. Допуски. Методы контроля размеров и отклонений формы и расположения поверхностей.
ГОСТ 1759.2-82 Болты, винты и шпильки. Дефекты поверхности и методы контроля.
ГОСТ 1759.3-83 Гайки. Дефекты поверхности и методы контроля.
ГОСТ Р 52627-2006 Болты, винты и шпильки. Механические свойства и методы испытаний. Соответствует ИСО 898-1:1999 (взамен ГОСТ 1759.4-87).
ГОСТ Р 52628-2006 Гайки. Механические свойства и методы испытаний. Соответствует ИСО 898—2:1992 и ИСО 898-6:1994 (взамен ГОСТ 1759.5-87).
ГОСТ 17769-83 Изделия крепёжные. Правила приёмки.
ГОСТ 18160-72 Изделия крепёжные. Упаковка. Маркировка. Транспортирование и хранение.
ГОСТ 24670-81 Болты, винты и шурупы. Радиусы под головкой.
ГОСТ 24671-84 Болты, винты, шурупы с шестигранной головкой и гайки шестигранные. Размеры «под ключ».
ГОСТ 27017-86 Изделия крепёжные. Термины и определения (разработан проект ГОСТ Р ИСО 1891-2007).
ГОСТ 27148-86 Изделия крепёжные. Выход резьбы. Сбеги, недорезы и проточки. Размеры.
ГОСТ 9.301-86 Покрытия металлические и неметаллические. Общие требования.
|
|
Примечание. Новые стандарты ГОСТ Р 52627 и 52628-2006, заменившие ГОСТ 1759.4 и 1759.5-87 существенных изменений в части механических свойств и методов испытаний не имеют, поэтому приводить изменения необходимости нет.
Международная система стандартов ИСО постепенно становится единой для большинства государств, национальные стандарты приводятся в полное соответствие с международными. В обновлённых стандартах повышены требования к качественным характеристикам крепёжных изделий, выпущены стандарты ИСО на большую группу новых прогрессивных конструкций.
Многофункциональность – характеристика современного крепежа
Прогрессивными называют крепёжные изделия, обладающие дополнительными функциональными свойствами, например, они могут стопориться без дополнительных деталей, сверлить себе отверстие, раскатать в нём резьбу, они обеспечивают снижение трудоёмкости сборки и технического обслуживания, имеют повышенную прочность и т.д.
Рассмотрим функции резьбовых крепёжных изделий.
Основные функции – соединить детали и сборочные единицы, создать усилие затяжки и сохранить его в заданных пределах в период эксплуатации машины. Прогрессивные крепёжные изделия характеризуются дополнительными функциями, которые позволяют решать множество задач за счёт проявления новых свойств. Дополнительные функции можно условно поделить на три группы:
а) конструктивные. Позволяют застопорить соединение, исключить вспомогательные детали, создать оптимальные напряжения на контакте;
б) сборочные. Обеспечивают надежную передачу вращающего момента, затяжку с заданным моментом, попадание в отверстие, перекрытие отверстия, установку в местах с односторонним доступом, не выпадение деталей крепежа при разборке;
в) технологические. Дают возможность во время сборки выдавить или нарезать резьбу в отверстии, очистить резьбу при завинчивании, просверлить отверстие и образовать в нем резьбу, отбортовать отверстие и образовать в нём резьбу, зачистить контактную опорную поверхность, герметизировать соединение и др.
Резьбовые соединения
Резьбовые соединения - разъемные, собираемые с помощью резьбовых крепежных деталей. Основные термины и определения резьб и резьбовых соединений стандартизованы.
Резьба – поверхность, образованная при винтовом движении плоского контура по цилиндрической или конической поверхности или совокупность чередующихся выступов и впадин определённого профиля, расположенных по винтовой линии на поверхности тела вращения (обычно цилиндра или конуса).
Применяется
- для устранения возможности перемещения соединяемых деталей;
- для удержания деталей на определенном расстоянии друг от друга;
- для обеспечения плотности стыка соединяемых деталей;
- для осуществления поступательного движения (пресса, домкраты, ходовые винты);
- для получения точных относительных перемещений (регулировочные винты).
Рис.1
Основы образования резьбы
В основе образования резьбы лежит принцип получения винтовой линии. Винтовая линия – это пространственная кривая, которая может быть образована точкой, совершающей движение по образующей какой-либо поверхности вращения, при этом сама образующая совершает вращательное движение вокруг оси.
Если в качестве поверхности принять цилиндр, то полученная на его поверхности траектория движения точки называется цилиндрической винтовой линией. Если движение точки по образующей и вращение образующей вокруг оси равномерны, то винтовая цилиндрическая линия является линией постоянного шага. На развертке боковой поверхности цилиндра (рис.2) такая винтовая линия преобразуется в прямую линию.
Рис.2
Если на поверхности цилиндра или конуса прорезать канавку по винтовой линии, то режущая кромка резца образует винтовую поверхность, характер которой зависит от формы режущей кромки. Образование винтового выступа можно представить как движение треугольника, трапеции, квадрата по поверхности цилиндра или конуса так, чтобы все точки фигуры перемещались по винтовой линии (рис.3).
Цилиндрическая резьба – резьба, образованная на цилиндрической поверхности.
Коническая резьба – резьба, образованная на конической поверхности.
Правая резьба – резьба, образованная контуром, вращающимся по часовой стрелке и перемещающимся вдоль оси в направление от наблюдателя.
Левая резьба – резьба, образованная контуром, вращающимся против часовой стрелке и перемещающимся вдоль оси в направление от наблюдателя.
Чаще всего используют правую резьбу. Левую резьбу применяют только в специальных механизмах. Если по поверхности перемещаются одновременно два, три и более плоских профиля, равномерно расположенные по окружности относительно друг друга, то образуются двух- и трехзаходные винты.
Рис.3
В качестве примера образования одно-, двух- и трехзаходной резьбы можно рассмотреть процесс навивки на цилиндрическую поверхность проволоки треугольного сечения (витки плотно прилегают друг к другу). Для однозаходной резьбы (рис.4,а) величина хода винта Рh равна шагу Р. Для двух- (рис.4,б) и трехзаходных (рис.4,в) винтов, когда осуществляется одновременная навивка соответственно двух и трех проволок указанного сечения, величина хода соответственно равняется 2Р – для двухзаходного винта и ЗР – для трехзаходного. Наиболее распространена однозаходная резьба. Все крепежные резьбы однозаходные. Многозаходные резьбы применяются преимущественно в винтовых механизмах.
Приведенные положения, с некоторыми изменениями и уточнениями, могут быть отнесены и к конической поверхности.
Рис.4
Резьбовые соединения являются наиболее совершенным, а потому массовым видом разъёмных соединений. Применяются в огромном количестве во всех машинах, механизмах, агрегатах и узлах.
Классификация резьбовых соединений
Основные типы резьб, их сравнительная характеристика и область применения.
Резьбовые (разъемные) соединения выполняют с помощью резьбовых крепежных деталей — болтов (рис.5), винтов, шпилек, резьбовых муфт, стяжек и т. п.
Резьбовое соединение – соединение деталей с помощью резьбы, обеспечивающее их относительную неподвижность или заданное перемещение одной детали относительно другой. Конструктивно резьбовые соединения очень разнообразны, но все могут быть отнесены к одному из следующих двух типов:
- резьбовые соединения, осуществляемые непосредственным свинчиванием соединяемых деталей, без использования специальных соединительных деталей;
- резьбовые соединения, осуществляемые при помощи специальных соединительных деталей: болтов, винтов и шпилек с гайками и шайбами.
На рис. 5 деталь 1 — резьба цилиндрическая, наружная; деталь 2 — резьба цилиндрическая внутренняя.
Наружная резьба – резьба, образованная на наружной, охватываемой поверхности, которая носит название болт или винт.
Внутренняя резьба – резьба, образованная на внутренней, охватывающей поверхности которая носит название гайка.
Рис. 5. Болт и гайка
Профиль резьбы - это контур сечения витка резьбы в плоскости, проходящей через ось основной поверхности. По форме профиля резьбы бывают: треугольные – метрические; трубные; дюймовые; трапецеидальные; круглые; прямоугольные (см. табл.1)
Таблица 1
№
п/п
Тип резьбы
Профиль резьбы
(некоторые параметры)
Условное изображение
резьбы
Стандарт
Примеры
обозначения
Примеры обозначения
резьбового соединения
1
Метрическая
2
Метрическая
коническая
3
Трубная
цилиндрическая
4
Трубная
коническая
5
Коническая
дюймовая
6
Трапецеидальная
7
Упорная
8
Круглая
9
Прямоугольная
Геометрические параметры резьбы.
Основными параметрами резьбы являются (рис. 6):
d - номинальный диаметр резьбы (наружный диаметр болта или винта), этот диаметр входит в обозначение резьбы и во всех документах указывается в миллиметрах, например, М5, М8, М24 (буква М указывает, что резьба метрическая);
d1 – внутренний диаметр резьбы гайки – диаметр цилиндра, касающегося вершин гребней резьбы в гайке (номинальные значения d и d1 одинаковы для винта и гайки, зазоры во впадинах образуются за счет предельных отклонений размеров диаметров);
d3 - внутренний диаметр резьбы винта – диаметр цилиндра, касающегося дна впадин между гребнями резьбы;
d2 - средний диаметр резьбы – диаметр цилиндра, на котором толщина выступов резьбы равна ширине впадин между ними;
p - шаг резьбы – расстояние между одноимёнными точками двух соседних гребней резьбы;
ph - ход резьбы – расстояние между одноимёнными точками двух соседних гребней резьбы, принадлежащих одному гребню нарезки;
α - угол профиля резьбы - угол между ее смежными боковыми сторонами в плоскости осевого сечения;
ψ - угол подъёма резьбы - угол подъема развертки винтовой линии по среднему диаметру.
Ось резьбы – прямая, относительно которой происходит винтовое движение плоского контура, образующего резьбу.
Боковые стороны профиля – прямолинейные участки профиля, принадлежащие винтовым поверхностям.
Вершина профиля – участок профиля, соединяющий боковые стороны выступа.
Впадина профиля – участок профиля, соединяющий боковые стороны канавки.
Углы наклона сторон профиля β и γ – угол между боковыми сторонами профиля и перпендикуляром к оси резьбы. Для резьб с симметричным профилем углы наклона сторон равны половине угла профиля α/2.
Рабочая высота профиля Н – высота соприкосновения сторон профиля наружной и внутренней резьб в направлении, перпендикулярном к оси резьбы.
Сбег резьбы – участок неполного профиля в зоне перехода резьбы к гладкой части.
Длина резьбы – длина участка поверхности, на котором образована резьба, включая сбег резьбы и фаску.
Длина резьбы с полным профилем – длина участка на котором резьба имеет полный профиль.
Длина свинчивания – длина соприкосновения винтовых поверхностей наружной и внутренней резьб в осевом направлении.
Между геометрическими параметрами метрической резьбы нетрудно выявить ряд соотношений. Так ход резьбы
где z – число заходов резьбы – количество параллельных гребешков образованных по общей винтовой линии.
Для угла подъёма резьбы получаем
Из последней формулы следует, что с увеличением числа заходов резьбы возрастает и угол её подъёма.
Теоретическая высота гребней метрической резьбы (как высота равностороннего треугольника) составляет
Внутренний диаметр резьбы в гайке
Для нормальных (с крупными шагами) метрических резьб, диаметры которых лежат в интервале 2≤d≤68 мм, с достаточной для практики точностью (не хуже 1,8%) этот диаметр можно вычислить по эмпирической формуле
Рис.6. Профили резьб: а — метрическая; б — дюймовая; в — трубная цилиндрическая;
г — метрическая коническая; д — трубная коническая; е — круглая; ж — прямоугольная;
з — трапецеидальная; и — упорная
По шагу резьбы разделяются на основные и мелкие. Мелкие резьбы для тех же диаметров имеют меньший шаг того же профиля, что и в основной резьбе. Применение мелких резьб меньше ослабляет сечение деталей и благодаря меньшему углу спирали нарезки лучше предохраняет соединение против самоотвинчивания.
Для диаметров свыше 20 мм уже обычно применяются мелкие резьбы.
Пример обозначения резьбы:
М16х2 - основная; М16х1,5 - мелкая.
Здесь: М - метрическая; 16 - номинальный (наружной) диаметр резьбы в мм; 2 и 1,5 - шаг резьбы в мм.
По назначению резьбы делятся на крепежные, крепежно-уплотняющие, резьбы для передачи движения и специальные (например, ниппельные).
К крепежным резьбам относят метрическую (рис. 6, а), дюймовую (рис. 6, б) и специальную (часовую).
Дата добавления: 2019-01-14; просмотров: 226; Мы поможем в написании вашей работы! |
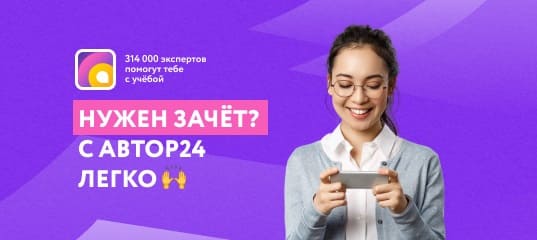
Мы поможем в написании ваших работ!