Мощность машин и её преобразование в механизмах 22 страница
4. Знак и размер катета по стандарту на типы и конструктивные элементы швов сварных соединений.
5. Для прерывистого шва - длину провариваемого участка, обозначение знака № 4 для цепного шва или № 5 для шахматного шва (см. таблицу 6) и шаг.
Для одиночной сварной точки - расчетный диаметр точки.
Для шва контактной точечной сварки или электрозаклепочного - расчетный диаметр точки или электрозаклепки, обозначение знака № 4 или № 5 (см. таблицу 6) и шаг.
Для шва контактной роликовой сварки - расчетную ширину шва.
Для прерывистого шва контактной роликовой сварки - расчетную ширину, знак умножения, длину провариваемого участка, обозначение знака 4 и шаг.
6. Обозначение вспомогательных знаков 7, 2 и 1 (таблица 6).
7. Обозначение вспомогательных знаков 6 и 3 (таблица 6).
Таблица 6. Вспомогательные знаки для обозначения сварных швов
Вспомогательный знак
Значение вспомогательного знака
Расположение вспомогательного знака относительно полки
линии-выноски, проведенной от изображения шва
Номер
Обозначение
с лицевой стороны
с оборотной стороны
1
image371
Усиление шва снять
2
Наплывы и неровности шва обработать с плавным
переходом к основному металлу
image121
image121
3
Шов выполнить при монтаже изделия, то есть при установке
его по монтажному чертежу на месте применения
|
|
image132
4
image337
Шов прерывистый или точечный с цепным расположением.
Угол наклона линии 60°
image086
5
image137
Шов прерывистый или точечный с шахматным
расположением
image089
6
Шов по замкнутой линии.
Диаметр знака 3-5 мм
7
Шов по незамкнутой линии.
Знак применяют, если расположение шва ясно из чертежа
После вспомогательных знаков, если указана последующая механическая обработка шва, ставят обозначение шероховатости поверхности обработанного шва (см. рис. 23,а).
Вспомогательные знаки (см. таблицу 6) выполняют тонкими сплошными линиями, они должны быть одинаковой высоты с цифрами, входящими в обозначение шва.
Условное обозначение стандартного шва, показанное на полке линии-выноски (см. рис. 28), расшифровывается так: шов нахлесточного соединения (буква Н), прерывистый шов по незамкнутой линии (знак 7); катет сечения шва 6 мм; длина каждого проваренного участка 100 мм, шаг 200 мм (100/200).
Рис.28
Сварочные материалы указывают на чертеже в технических требованиях или таблице швов.
Допускается сварочные материалы не указывать.
При наличии на чертеже одинаковых швов обозначение наносят у одного из изображений, а от изображений остальных одинаковых швов проводят линии-выноски с полками.
|
|
Всем одинаковым швам присваивают один порядковый номер, который наносят:
- на линии-выноске, имеющей полку с нанесенным обозначением шва;
- на полке линии-выноски, проведенной от изображения шва, не имеющего обозначения, с лицевой стороны.
Написание технических требований на чертежах сварных конструкций
В технических требованиях на чертежах сварных конструкций рекомендуется приводить следующие данные:
1) марку электродов или присадочной проволоки.
Вместо марки допускается указывать тип электрода по соответствующим государственным стандартам. Допускается вместо марок и типов электродов и марок присадочных проволок указывать необходимые требования к прочности и другим свойствам швов или сварных соединений;
2) сведения о необходимости термической обработки сварной конструкции после сварки;
3) сведения о необходимости, ограничении или запрещении правки;
4) контролируемые швы или участки швов и необходимость их контроля;
5) группу сварных соединений;
6) конструктивные и технологические нормы подготовки и сборки кромок под сварку и контролируемые размеры швов. Они должны соответствовать требованиям нормативно-технических документов.
|
|
Ниже приведены примеры записи технических требований на чертежах сварных конструкций.
Для углеродистых сталей обыкновенного качества (ГОСТ 380-88), сталей углеродистых качественных конструкционных (ГОСТ 1050-88):
1. Сварку проводить электродом Э42А (ГОСТ 9467-75).
Сварные швы по ГОСТ 5264-80.
2. Сварные швы группы ... (отраслевой стандарт).
Если на чертеже имеются стандартные и нестандартные швы, то в технических требованиях пишут:
1. Сварку проводить электродом Э42А (ГОСТ 9467-75).
Сварные швы №№ ...по ГОСТ 5264-80.
Сварка швов № ... - ручная дуговая.
2. Сварные швы группы ... (отраслевой стандарт).
Допускается на чертеже сварные швы не обозначать, особенно для пространственных конструкций из уголков, швеллеров и т.д.
Например:
... В местах стыка деталей из швеллеров сварка швами Т3 катетом не менее 5 мм и С2 по ГОСТ 5264-80 по всей длине соприкосновения деталей.
...В местах стыка деталей из листов сварка швом С2 длиной 50 мм и шагом 200 мм, приварка деталей из листов к швеллерам и фланцам швом HI катетом не менее 5 мм длиной 50 мм с шагом 200 мм по ГОСТ 5264-80.
|
|
...В местах стыка деталей из труб сварка швом У5 катетом не менее 5 мм по ГОСТ 16037-80 по всей длине соприкосновения деталей.
...В местах стыка деталей из труб со швеллерами сварка швом Т1 катетом не менее 5 мм по ГОСТ 5264-80.
... В местах стыка деталей из труб с лентой сварка швом HI no ГОСТ 5264-80.
Для легированных конструкционных сталей (ГОСТ 4543-71):
1. Сварку проводить электродом Э85А (ГОСТ9467-75).
2. Сварные швы по ГОСТ 5264-80.
3. Сварные швы группы ... (отраслевой стандарт).
Для коррозионно-стойких сталей по ГОСТ 5632-72 (сталь 12Х18Н10Т):
1. Сварные швы по ГОСТ 14771-76.
2. Сварку проводить с присадочной проволокой Св06Х19Н9Т ГОСТ 2246-70.
3. Допускается замена на проволоку Св04Х19Н11МЗ ГОСТ 2246- 70.
4. Допускается сварка электродуговая. Электрод Э-08Х17Н8М2 ГОСТ 10052-75.
5. Сварные швы группы ... (отраслевой стандарт).
Если в сварной конструкции применяются различные способы сварки, то в технических требованиях следует делать запись по типу:
1. Сварка электродуговая электрод Э-08Х20Н9Г2Б (ГОСТ 10052-75). Допускается электрод Э-08Х17Н8М2 (ГОСТ 10052-75).
1. Сварные швы группы ... (отраслевой стандарт).
3. Сварные швы, выполненные электродуговой сваркой, контролировать радиографическим методом по ГОСТ 7512-82.
4. Остальные сварные швы выполнить аргонодуговой сваркой с присадочной проволокой Св06Х19Н9Т (ГОСТ 2246-70).
5. Сварные швы, выполненные точечной сваркой, группы ... (отраслевой стандарт).
Если на сборке выполняются сварные швы из алюминиевых сплавов различных марок:
Сварные швы по ГОСТ 14806-80, кроме шва №1.
Сварку швов №7 - №5 проводить с присадочной проволокой СвАМц (ГОСТ 7871-75).
Сварка шва №1 - с присадочной проволокой СвАМгб (ГОСТ 7871-75).
Сварные швы группы ... (отраслевой стандарт).
Для титановых сплавов (ГОСТ 19807-91) (ОТ4, ВТ1-00):
1. Сварка аргонодуговая.
Сварные швы группы ... (отраслевой стандарт).
2. Сварочная проволока СвОТ4 ОСТ1.90015-77.
Допускается сварка без присадочной проволоки.
3. Сварные швы контролировать радиографическим методом по ГОСТ 7512-82.
4. После сварки выполнить правку и отжиг по инструкции ...
Ударная правка и правка с применением статических нагрузок не допускается.
Для материала ВТ14, если требуется равнопрочность сварного шва с основным материалом, то в технических требованиях пишут:
Сварочная проволока СвСПТ-2 ОСТ- 1.90015-77.
Без предъявления требований равнопрочности к сварному шву:
Сварочная проволока CвBT1-00 ОСТ - 1.90015-77.
Паяные соединения
Паяные соединения — неразъемные соединения, образуемые за счет химического или физического (адгезия, растворение, образование эвтектик) взаимодействия расплавляемого материала – припоя с соединяемыми кромками деталей. Припой-сплав (на основе олова, меди, серебра) или чистый металл, вводимый в расплавленном состоянии в зазор между соединяемые деталями. Температура плавления припоя ниже температуры плавления материалов деталей. По конструкции паяные соединения подобны сварным: нахлесточное, стыковое, в ус (рис. 29). Наибольшую прочность имеет соединение внахлестку, но при этом увеличиваются габариты соединения. Соединение встык и в ус имеет малые габариты, но невысокую прочность.
Рис.29
Паянием называют процесс образования неразъемного соединения материалов паяльником 2 (рис. 29.1) при помощи расплавленного металла или сплава, называемого припоем 1. От сварки паяние отличается тем, что кромки соединяемых деталей не расплавляются, а только нагреваются до температуры плавления припоя. В отличие от сварки пайка сохраняет: структуру, механические свойства и состав материала деталей, вызывает значительно меньшие остаточные напряжения, позволяет соединят не только однородные, но и разнородные материалы: черные и цветные металлы, сплавы, керамику, стекло и др.
Прочность паяного соединения определяется прочностью припоя и сцепления припоя с поверхностями соединяемых деталей. Припои имеют более низкую температуру плавления, чем металлы, из которых изготовлены соединяемые детали 3. Припой расплавляется и затвердевает в зазорах между поверхностями соединяемых деталей (рис. 29.1).
1
Рис. 29.1. Процесс паяния паяльником: 1 – припой; 2 – паяльник; 3 – соединяемые детали
При пайке поверхности деталей очищают от окислов и обезжиривают с целью получения хорошей смачиваемости поверхности припоем качественного заполнения им зазоров. Нагрев припоя и деталей в зависимости от их размеров осуществляют паяльником, газовой горелкой, электронагревом, в термических печах и др. Для очистки и защиты соединяемых поверхностей и припоя от окисления, улучшения смачиваемости и лучшего растекания припоя применяют флюсы. Они способствуют очищению поверхностей от загрязнений, растворяют окисные пленки, улучшают смачиваемость поверхностей припоем, обеспечивают лучшее затекание припоя в зазоры между спаиваемыми деталями. Флюсы должны обладать хорошей жидкотекучестью и иметь температуру плавления более низкую, чем у припоя, что обеспечивает их вытеснение припоем. Они делятся на химически активные (бура, борная кислота, хлористый цинк и др.) и химически неактивные (канифоль, нашатырь и спиртовые растворы). Применение первых требует тщательной промывки деталей после пайки.
Для уменьшения вредного влияния окисления поверхности деталей при пайке применяют также паяют в вакууме или в среде нейтральных газов (аргон). Расплавленный припой растекается по нагретым поверхностям стыка деталей и при охлаждении затвердевает, прочно соединении детали.
Размер зазора в стыке определяет прочность соединения. При малом зазоре лучше проявляется эффект капиллярного течения припоя, процесс растворения материалов деталей в расплавленном припое распространяется на всю толщину паяного шва (прочность образующегося раствора на 30…60% выше прочности припоя). Размер зазора обычно для легкоплавких припоев принимают зазор до 0,2...0,3 мм на сторону, для твердых припоев несколько меньше - до 0,15 мм. Но величина зазора зависит как от конструкции паяного соединения, так и от технологии пайки - для пайки в печи нужен один зазор, для пайки в соляной ванне - другой.
К легкоплавким мягким припоям с температурой плавления до 450 °С относятся оловянисто-свинцовые сплавы с содержанием олова от 18 до 90 %, например ПОС-61 (61% олова). Для понижения температуры плавления в эти сплавы вводят висмут и кадмий, а для увеличения прочности – сурьму. Твердые припои содержат в своем составе медь, цинк, никель, серебро и имеют температуру плавления выше 500 °С.
Мягкие припои применяют для получения главным образом надежных электрических контактов при пайке и герметичных соединений. Эти припои не следует применять для соединений, работающих при температуре свыше 100 °С или подверженных действию ударных нагрузок.
Среднетугоплавкие припои имеют температуру плавления выше 500 °С (серебряные или на медной основе). Такими припоями можно получить прочность паяного соединения, близкую к прочности основного металла соединяемых деталей. Твердые припои обеспечивают достаточную прочность шва при температуре свыше 100 °С, устойчивы к вибрациям, ударам и агрессивным средам. Тугоплавкие припои состоят из сплава меди, цинка, серебра, никеля, железа, кадмия и других металлов. Припой на медной основе (ВПр1, ВПр2) отличаются повешенной хрупкостью, их применяют для соединения деталей, нагруженных статической нагрузкой. Серебряные припои (ПСр40, ПСр45) применяют для ответственных соединений. Они устойчивы против коррозии и пригодны для соединения деталей, воспринимающих ударную и вибрационную нагрузки.
Маркировка и назначение некоторых припоев: ПОС-90 (олово 90%, остальное свинец, Тпл = 222 °С) - пайка посуды; ПОС-30 (Тпл =256 °С) - третник - пайка радиоаппаратуры; ПМЦ-48, (медь 48%, остальное цинк, Тпл = 865 °С) – пайка медных сплавов, имеющих температуру плавления не ниже 920 °С; ПСр-72 (серебро 72%, остальное медь, Тпл = 779 °С) – пайка чёрных и цветных металлов, имеющих температуру плавления не ниже 800 °С; ПСр-40 (серебро 40%, медь ~16,7%, цинк ~ 17,0%, кадмий ~ 26,0%, никель ~ 0,3% Тпл = 605 °С) - пайка чёрных и цветных металлов, имеющих температуру плавления не ниже 650 °С.
Достоинством паяных соединений является стойкость против коррозии, возможность соединения тонкостенных деталей, герметичность, малая концентрация напряжений вследствие высокой пластичности припоя, простота и дешевизна технологического процесса, широкие возможности его механизации и автоматизации, возможность соединения всех металлов и разнородных материалов (металл с керамикой, стеклом, резиной), малые остаточные температурные напряжения и деформации, малое электросопротивление мест соединения. Пайка позволяет получать соединения деталей в скрытых и труднодоступных местах конструкции.
Так как непосредственная пайка при соединении металлов с неметаллами невозможна, то на поверхности неметаллических материалов создают промежуточный слой из меди, никеля, серебра, который хорошо сцепляется с поверхностью этих материалов и обеспечивает качественную пайку с металлом.
Недостатком паяных соединений по сравнению со сваркой является сравнительно невысокая прочность в сравнении с основным материалом, необходимость малых и равномерно распределенных зазоров между соединяемыми деталями, что требует их точной механической обработки и качественной сборки, а также предварительной обработки поверхностей перед пайкой.
Применение паяных соединений в машиностроении расширяется в связи с внедрением пластмасс, керамики и высокопрочных сталей, которые плохо свариваются. Пайкой соединяют листы, стержни, трубы и др. Ее широко применяют в автомобилестроении (радиаторы и др.) и самолетостроении (обшивка с сотовым промежуточным заполнением). Пайка является одни из основных видов соединений в радиоэлектронике и приборостроении.
Расчет на прочность паяных соединений производят на сдвиг методами сопротивления материалов. Надо учитывать, что в нахлесточном соединении площадь расчетного сечения равна площади контакта деталей. Для нахлесточных соединений деталей из низкоуглеродистой стали, полученных оловянно-свинцовыми припоями (ПОС40), допускаемое напряжение на сдвиг [τ]с=60 Н/мм2.
Клеевые соединения
В настоящее время все шире применяют неразъемные соединения металлов и неметаллических материалов, получаемые склеиванием. Это соединения деталей неметаллическим веществом посредством поверхностного схватывания и межмолекулярной связи в клеящем слое.
Отличие клеевого соединения от паяного заключается в том, что клеи не являются металлами, в то время как припои – это либо металлы, либо их сплавы. В зависимости от состава и свойств клеев их полимерезация может происходить как при комнатной температуре, так и при нагревании.
Наибольшее применение получили клеевые соединения внахлестку (рис.30), реже — встык. Клеевые соединения позволили расширить диапазон применения в конструкциях машин сочетаний различных неоднородных материалов — стали, чугуна, алюминия, меди, латуни, стекла, пластмасс, резины, кожи и т. д.
Рис.30. Клеевое соединение внахлестку
Все клеи можно разделить на конструкционные - такие которые способны выдерживать после затвердевания нагрузку на отрыв и сдвиг, и неконструкционные - соединения с применением которых не способны длительное время выдерживать нагрузки. К конструкционным можно отнести клеи БФ, эпоксидные, циакрин и др. К неконструкционным - клей 88Н, иногда резиновый и др.
Большинство клеев требует выдержки клеевого соединения под нагрузкой до образования схватывания и последующей досушки в свободном состоянии. Некоторые клеи требуют нагрева для выпаривания растворителя и последующей полимеризации.
Применение универсальных клеев типа БФ, ВК, МПФ и других (в настоящее время употребляют более ста различных марок клеев) позволяет довести прочность клеевых соединений до 80% по отношению к прочности склеиваемых материалов. Наибольшее применение в машиностроении клееные соединения, работающие на сдвиг. Оптимальная толщина слоя клея 0,05…0,15 мм.
На прочность клееных соединений влияют характер нагрузки, конструкция соединения, тип и толщина слоя клея (при увеличении толщины прочность падает), технология склеивания, и время (с течением времени прочность некоторых клеев уменьшается).
Дата добавления: 2019-01-14; просмотров: 225; Мы поможем в написании вашей работы! |
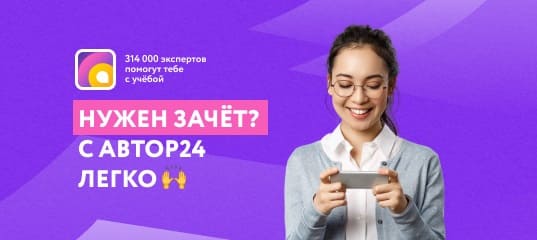
Мы поможем в написании ваших работ!