Мощность машин и её преобразование в механизмах 17 страница
На рис.3 приведена схема образования сварного соединения при рассматриваемых видах сварки. На ней обозначены: 1 – электродная проволока; 2 – сопло (насадка); 3 – токоподводящий наконечник; 4 – газ (флюс); 5 – дуга; 6 – затвердевший шлак; 7 – шов; 8 – сварочная ванна; 9 – основной (свариваемый) металл.
image010
Рис.3
При механизированной и автоматической сварке образование сварного соединения происходит следующим образом. Теплотой дуги электрод и основной металл расплавляются, капли расплавленного металла с конца электрода попадают в сварочную ванну, где перемешиваются с расплавленным основным металлом. Жидкий металл сварочной ванны подвергается металлургической обработке за счет использования газа или флюса (в этом состоит отличие от ручной дуговой сварки). То есть он раскисляется и легируется. При передвижении дуги вдоль свариваемых кромок перемещается и сварочная ванна. В ее хвостовой части металл охлаждается, кристаллизуется и образуется сварное соединение.
Различают следующие виды механизированной (автоматической) сварки.
1. В углекислом газе и его смесях с кислородом сваривают низко- и среднеуглеродистые, а также низколегированные стали. В углекислом газе сваривают стали толщиной до 40, а в смесях газов – до 80 мм. Защита смесью газов улучшает технологические и металлургические характеристики процесса сварки. Расход углекислого газа зависит от мощности дуги, вылета электрода, воздушных потоков в помещении, где выполняется сварка.
|
|
2. В инертных газах (аргоне или гелии) можно сваривать алюминий, магний, титан и их сплавы. Свариваются низко- и среднеуглеродистые, низко-, средне- и высоколегированные конструкционные стали. Использование названных газов целесообразно, так как аргон имеет плотность почти в 1,5 раза большую, чем воздух, а гелий – значительно меньшую, чем воздух и аргон. Кроме того аргон и гелий не образуют химических соединений с металлами, поэтому в этих газах можно сваривать любые металлы и сплавы.
3. Под флюсом свариваются низко- и среднеуглеродистые, низко-, средне- и высоколегированные стали, чугун, титан, медь, алюминий и их сплавы.
Флюс – порошкообразный материал, который при сварке выполняет такие же функции, как покрытие электрода при ручной дуговой сварке. Основой флюса является силикат марганца SiO2∙MnO. Флюсы в зависимости от способа изготовления бывают двух видов: плавленые и неплавленые. Плавленые получают сплавлением исходных компонентов в печах. К неплавленым относятся керамические и спеченные флюсы. Керамические флюсы изготавливаются из порошкообразных материалов, соединяемых в зерна клеящими веществами, например жидким стеклом. Спеченные флюсы получают спеканием исходных порошкообразных материалов при высоких температурах с последующим дроблением частиц до заданных размеров.
|
|
Во время сварки часть флюса расплавляется, а после затвердения образует шлаковую корку. Нерасплавленная часть флюса после просева используется повторно.
4. Порошковыми проволоками сваривают низкоуглеродистые и низколегированные стали, а специальными порошковыми проволоками – некоторые высоколегированные, в частности, нержавеющие стали, сплавы меди. Ими можно сваривать стали толщиной до 40 мм. Порошковые проволоки представляют собой металлическую оболочку, заполненную шихтой. Их некоторые поперечные сечения показаны на рис.4: a) трубчатое, б) трубчатое с захлёсткой, в) и г) – сложные сечения.
Рис.4
Наиболее простая по конструкции – порошковая проволока трубчатого поперечного сечения. Для увеличения жесткости проволоки, а также изменения соотношения компонентов материалов оболочки и шихты применяются проволоки, у которых во внутреннюю полость отогнуты кромки металлической оболочки. Состав металла оболочки выбирается в зависимости от свариваемого металла. В шихту порошковой проволоки вводят компоненты, которые могут выполнять следующие функции:
|
|
– защиту расплавленного металла от взаимодействия с кислородом и азотом воздуха;
– раскисление и легирование расплавленного металла;
– стабилизацию горения дуги;
– улучшение формирования шва.
Применяют три вида порошковых электродных проволок: самозащитные, для сварки в углекислом газе, для сварки под флюсом. Наиболее высокой технологичностью отличается сварка самозащитными порошковыми проволоками, так как отпадает необходимость в применении защитных газов и флюсов.
Сварочное оборудование. Для механизированной и автоматической сварки применяются соответственно полуавтоматы и автоматы, комплектуемые источниками тока для питания дуги.
Автоматы выполняют следующие функции: возбуждение дуги и автоматическое регулирование процесса сварки; механизированную подачу электродной проволоки со скоростью, равной скорости плавления; механизированное передвижение дуги относительно свариваемых кромок; подачу флюса или газа в зону дуги.
Автомат состоит из двух основных устройств: трактора или самоходной головки и аппаратуры управления. Автоматы для сварки в защитных газах, кроме того, имеют газовую аппаратуру, которая включает газовый редуктор, баллон с углекислотой, подогреватель газа и осушитель, предназначенный для очистки газа от влаги.
|
|
Трактор выполняет подачу электродной проволоки, а также подводит ток к месту сварки. В механизме подачи автоматов и полуавтоматов для сварки электродными проволоками обычно имеются два подающих ролика, один из которых ведущий, а другой прижимной, между этими роликами зажимается электродная проволока. Она сматывается с кассеты, проталкивается через шланг и через токопроводящее устройство подается в зону дуги.
У трактора для сварки под флюсом имеются системы подачи и уборки флюса, а у трактора для сварки в защитных газах – специальная газоэлектрическая горелка, которая предназначена для направления в зону электродной проволоки, подвода к ней сварочного тока и подачи защитного газа в зону дуги. При сварке под флюсом вместо горелки применяется держатель, на котором закреплен бункер для подачи флюса.
Применение механизированной и автоматической дуговой сварки. Механизированной сваркой можно накладывать не только прямолинейные, но и криволинейные швы, а также швы небольшой длины в труднодоступных местах. Сваривают металл малой и средней толщины. Эти виды сварки применяются при различных работах, в том числе и ремонтных. При серийном производстве прямолинейные и кольцевые сварные швы длиной более 300 –500 мм целесообразно выполнять автоматической сваркой.
В транспортном машиностроении механизированная и автоматическая дуговая сварка применяются при производстве вагонов и локомотивов. Хребтовые балки сваривают на поточных механизированных линиях автоматами под флюсом. Рамы вагонов сваривают автоматами сваркой в углекислом газе на специально оборудованных кантователях. В тракторном и сельскохозяйственном машиностроении сваркой в углекислом газе выполняется до 75% всех сварочных работ.
Автоматическая сварка под флюсом и в углекислом газе широко применяются в трубном производстве для изготовления прямошовных и спиралешовных труб большого диаметра.
Механизированная сварка под флюсом, в углекислом газе и порошковыми проволоками широко применяется при строительстве доменных печей, резервуаров для хранения нефтепродуктов, при строительстве мостов, в судостроении и т. д.
Дуговая сварка неплавящимся электродом в инертных газах
Схема дуговой сварки неплавящимся электродом в инертном газе показана на рис.5. На ней обозначены: 1 – основной металл; 2 – присадочный металл; 3 – держатель электродов; 4 – сопло; 5 – неплавящийся электрод; 6 – струя газа; 7 – дуга; 8 – шов; 9 – сварочная ванна.
Рис.5
В зоне сварки осуществляется нагрев основного и присадочного материала до жидкого состояния теплотой электрической дуги, горящей между неплавящимся электродом и основным металлом. В сварочной ванне основной и присадочный металлы перемешиваются и взаимно растворяются. Расплавленный металл в зоне сварки защищен инертным газом от взаимодействия с окружающей средой. При этом виде сварки используют один из двух способов: обдув зоны сварки инертным газом, подаваемым из горелки, либо сварка в камере с контролируемой атмосферой. Инертный газ защищает не только дугу и расплавленный металл сварочной ванны, но и нагретый выше 300 – 400 °С металл шва.
Неплавящиеся электроды для сварки в инертных газах изготавливают из чистого вольфрама (ЭВЧ), а также вольфрама с иттрием (ЭВИ-1) и с лантаном (ЭВЛ). В последнее время изготовлены электроды из титана с включением редкоземельных металлов. Такие электроды могут выдерживать температуру до 3200 °С.
Присадочный материал. Детали толщиной до 2 мм обычно сваривают без присадочного металла. При толщине более 2 мм в дугу подается присадочная проволока. Химический состав присадочного материала должен быть близок к составу основного металла.
Инертные газы. Для защиты расплавленного металла, а также нагретого, находящегося в твердом состоянии, от взаимодействия с газами окружающего воздуха используются инертные газы – аргон, гелий и их смеси. Эти газы поставляют в стальных баллонах емкостью 40 литров под давлением 14,7 МПа. В производстве особо ответственных конструкций инертный газ подвергается дополнительной очистке от влаги, кислорода и азота.
Применение. В инертных газах можно сваривать любые конструкционные металлы и сплавы. Однако инертные газы дороже и дефицитнее активных, поэтому их применяют в основном для сварки химически активных металлов – магния, алюминия, титана, цинка, тантала, молибдена и др., а также высокопрочных сталей и сплавов с особыми свойствами.
В инертных газах, как правило, сваривают ответственные конструкции. Этот способ используется для сварки химически активных и тугоплавких металлов и сплавов в авиационном, космическом, энергетическом и химическом машиностроении, а также в приборостроении. В инертных газах сваривают высокопрочные, коррозионно-стойкие и жаропрочные стали в судостроении, производстве железнодорожного подвижного состава. Изготавливают также резервуары цистерн и другие конструкции, работающие в условиях повышенных температур и сложного нагружения.
Некоторые специальные виды сварки
К специальным условно отнесены следующие виды сварки:
– термический класс: лазерная, электронно-лучевая, плазменная, электрошлаковая, термитная, газовая;
– термомеханический и механический классы: диффузионная, дугопрессовая, газопрессовая, трением, ультразвуковая, взрывом, холодная;
– контактная сварка: точечная, рельефная, шовная стыковая.
Рассмотрим некоторые из них более подробно.
Лазерная сварка. Лазерный луч с помощью оптической системы фокусируется на поверхности материала в световое пятно диаметра 100 мкм. При этом реализуется очень высокая плотность световой мощности и начинается плавление металла. В результате поглощения электромагнитного лазерного излучения металлом в пятне поглощения (световом пятне) образуется сварочная ванна. Мощные лазеры позволяют накладывать непрерывные швы с глубиной проплавления до 20 мм. Ими сваривают не только металлы, но и неметаллические материалы, например стекло, кварц и др. Лазерную сварку можно выполнять на воздухе или в камере с контролируемой атмосферой
С применением лазерной сварки приваривают наконечники к лопастям газовых турбин, закаленные режущие кромки к полотнам металлорежущих пил, соединительные планки к стволам охотничьих ружей, герметизируют корпусы приборов и др.
Преимущества лазерной сварки: швы можно накладывать в труднодоступных местах; отсутствует контакт со свариваемым металлом и поэтому не загрязняются металл сварочной ванны и шов; мала зона термического влияния и поэтому незначительно коробление сварной конструкции.
Плазменная сварка. Металл в зоне сварки нагревается плазмой до расплавления с образованием сварочной ванны. После кристаллизации происходит образование сварного шва.
Плазма – частично или полностью ионизированный газ с высокой концентрацией заряженных частиц, в котором плотности положительных и отрицательных зарядов практически одинаковы. Ионизированные частицы плазмы обладают запасом кинетической и потенциальной энергий. Для создания плазмы применяют различные источники энергии, например, электрический разряд в газах, лазерный луч, процессы горения и взрыва, ядерные реакции. С целью повышения степени ионизации плазма обжимается в канале сопла плазмотрона.
Установка для автоматической плазменной сварки состоит из плазмотрона, самоходной головки, аппаратуры управления, системы газопитания и источника тока. Катоды плазменных горелок изготовляют из вольфрама с присадками лантана, а аноды (сопла) – из меди и латуни. Поскольку в плазме развиваются высокие температуры, электроды (катод и анод) интенсивно охлаждают проточной водой.
Применение. Плазменной сваркой сваривают мембранные элементы, сифоны, термопары, тонкостенные трубы. Она применяется в производстве статоров электродвигателей, кузовов автомобилей, труб, вытяжных каналов двигателей внутреннего сгорания и др.
Преимущества. Нагрев свариваемого металла можно достаточно точно регулировать в широком интервале температур, изменяя форму и размеры сопла, состав и расход газов и т. д. Поэтому весьма стабильны геометрические параметры швов, меньше склонность их к образованию трещин.
В электрошлаковой сварке источником нагрева служит теплота, выделяющаяся при прохождении тока от электрода к изделию через шлаковую ванну. Электрошлаковая сварка предназначена для соединения деталей большой толщины. Толщина свариваемых деталей практически не ограничивается. Электрошлаковая сварка позволяет заменять сложные и тяжелые цельнолитые и цельнокованые конструкции сварными из отдельных простых отливок, поковок и листов, что значительно облегчает и снижает стоимость производства. Эта сварка применима и для чугунных отливок.
Контактная сварка основана на использовании повышенного омического сопротивления в стыке деталей и осуществляется несколькими способами. При стыковой контактной сварке через детали пропускают ток, сила которого достигает нескольких тысяч ампер. Основное количество теплоты выделяется в месте стыка, где имеется наибольшее сопротивление; металл в этой зоне разогревается до пластического состояния или даже до поверхностного оплавления. Затем ток выключают, а разогретые детали сдавливают с некоторой силой – происходит сварка металла деталей по всей поверхности стыка. Этот вид сварки рекомендуют применять для стыковых соединений деталей, площадь поперечного сечения которых сравнительно невелика.
Точечная контактная сварка относится к группе контактной сварки, при которой для образования соединения в свариваемый металл вводятся два вида энергии: тепловая и механическая. При точечной, а также рельефной, шовной сварке металл в зоне сварки нагревается до жидкого состояния с большой скоростью, достигающей десятков тысяч градусов в секунду. Затем заготовки прижимаются одна к другой, в результате чего поверхностные выступы сминаются, а зерна металла измельчаются. После выключения сварочного тока металл в зоне сварки охлаждается и кристаллизуется. В результате образуется соединение, называемое сварной точкой. Воздействие внешнего давления и пластическая деформация благоприятно влияют на уплотнение ядра при кристаллизации металла.
Точечная сварка выполняется на машинах переменного, постоянного тока и конденсаторных машинах.
Есть две разновидности точечной сварки: одноточечная и многоточечная. Многоточечная сварка применяется с целью повышения производительности труда и уменьшения коробления сварной конструкции. Выполняют только нахлесточные соединения заготовок различной конфигурации из листа, прокатных и прессованных профилей, а также из литых, кованых, обработанных резанием полуфабрикатов.
При шовной контактной сварке узкий непрерывный или прерывистый шов расположен вдоль стыка деталей. Эту сварку выполняют с помощью электродов, имеющих форму дисков, которые катятся в направлении сварки. Точечную и шовную сварку применяют в нахлесточных соединениях преимущественно для листовых деталей толщиной не более 3–4 мм и тонких стержней арматурных сеток. В отличие от точечной шовная сварка образует герметичное соединение.
Применение. Диапазон применения контактной сварки весьма широк – от микроминиатюрных полупроводниковых устройств и пленочных микросхем, до крупных космических аппаратов. Точечная сварка широко применяется в вагоно- и тепловозостроении: выполняют сварку крыш, боковых стен, настила пола цельнометаллических пассажирских вагонов. Стыковая контактная сварка применяется в производстве железнодорожных рельсов для их соединения в плети длиной до 800 м, а также при ремонте деталей подвижного состава.
Все рассмотренные виды контактной сварки высокопроизводительны, их широко применяют в массовом производстве для сварки труб, арматуры, кузовов автомобилей, металлической обшивки железнодорожных вагонов, корпусов самолетов, тонкостенных резервуаров и т. п.
Ультразвуковая сварка. Соединение при этом способе сварки образуется в результате воздействия на свариваемый материал ультразвуком в сочетании с небольшими сдавливающими усилиями. При введении ультразвука окислы и загрязнения, имеющиеся на сопрягаемых поверхностях, разрушаются и удаляются к периферии, а в металле развивается пластическая деформация и нагрев на локальных участках, на которых происходит смятие микровыступов и измельчение зерен металла.
Установка для сварки ультразвуком состоит из высокочастотного генератора электрических колебаний, магнитостриктора, преобразующего высокочастотные электрические колебания в механические, волновода, сварочного наконечника, привода сжатия.
Применение. Ультразвуком в основном сваривают пластичные металлы: алюминий, медь, никель, а также некоторые неметаллические материалы – пластмассы., стекло, полупроводники. Ультразвуком выполняют точечные и шовные нахлесточные соединения. Ультразвуковая сварка применяется в производстве конструкций из тонкого металлического листа в приборостроении и радиотехнике, а также для приварки обшивок к несущим конструкциям летательных аппаратов.
Преимущества. Из-за незначительного нагрева свариваемых деталей невелики деформации конструкции в зоне термического влияния. Возможна сварка разнородных трудносвариваемых металлов; сварка деталей из тонкого листа и фольги; можно приваривать детали малой толщины к толстым; электрическая мощность сварочного оборудования невелика.
Сварка взрывом. Для образования сварного соединения возбуждается взрыв, в результате которого подвижная заготовка перемещается с большой скоростью к неподвижной заготовке, лежащей на опорах. При высокочастотном косом их соударении создается давление, большее предела текучести материала, и поэтому развивается пластическая деформация поверхностных слоев металла. Соударяющиеся заготовки сближаются до межатомных расстояний, и между их хорошо очищенными поверхностями возникают связи, образуется сварное соединение. Сварка выполняется на полигонах, в шахтных выработках, в бетонных и стальных взрывных камерах, а также в специальных вакуумных камерах.
Дата добавления: 2019-01-14; просмотров: 231; Мы поможем в написании вашей работы! |
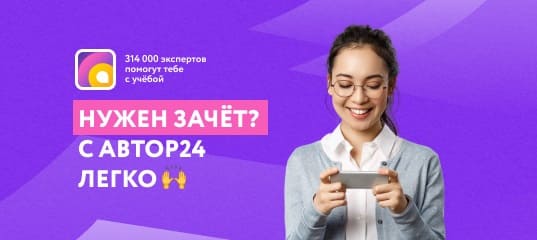
Мы поможем в написании ваших работ!