Мощность машин и её преобразование в механизмах 16 страница
Разъемными называют соединения, которые можно многократно собирать и разбирать без повреждения деталей. К разъемным относятся резьбовые, шпоночные и шлицевые соединения, штифтовые и клиновые соединения.
По форме сопрягаемых поверхностей соединения делят на плоское, цилиндрическое, коническое, сферическое, винтовое и т.д.
Проектирование соединений является очень ответственной задачей, поскольку большинство разрушений в машинах происходит именно в местах соединений. Многие аварии и прочие неполадки в работе машин и сооружений обусловлены неудовлетворительным качеством соединений.
Так, например, опытом эксплуатации отечественных и зарубежных самолетов установлено, что долговечность фюзеляжа определяется прежде всего усталостными разрушениями, из которых до 85% приходится на резьбовые и заклепочные соединения. Отметим, также, что в конструкциях тяжелых широкофюзеляжных самолетов (например, ИЛ-96, АН-124) насчитывается до 700 тыс. болтов и до 1,5 млн заклепок.
К соединениям в зависимости от их назначения предъявляются требования прочности, плотности (герметичности) и жесткости.
Основным критерием работоспособности и расчета соединений является прочность. Необходимо стремиться к тому, чтобы соединение было равнопрочным с соединяемыми элементами. Наличие соединения, которое обладает прочностью, составляющей, например, 0,8 от прочности самих деталей, свидетельствует о том, что 20% нагрузочной способности этих деталей или соответствующая часть металла конструкции не используется.
|
|
При оценке прочности соединения стремятся приблизить его прочность к прочности соединяемых элементов, т.е. стремятся обеспечить равнопрочность конструкции.
Требование плотности является основным для сосудов и аппаратов, работающих под давлением. Уплотнение разъемного соединения достигается за счет:
1) сильного сжатия достаточно качественно обработанных поверхностей;
2) введения прокладок из легко деформируемого материала.
При этом рабочее удельное давление q в плоскости стыка должно лежать в пределах q = (1,5…4)p, p – внутренне давление жидкости в сосуде.
Экспериментальные исследования показали, что жесткость соединения во много раз меньше жесткости соединяемых элементов, а поскольку жесткость системы всегда меньше жесткости наименее жесткого элемента, то именно жесткость соединения определяет жесткость системы.
Желательно, чтобы соединение не искажало форму изделия, не вносило дополнительных элементов в его конструкцию и т. п. Например, соединение труб болтами требует образования фланцев, сверления отверстий под винты, установку самих винтов с гайками и шайбами. Соединение труб сваркой встык не требует никаких дополнительных элементов. Оно в наибольшей степени приближает составное изделие к целому. С этих позиций соединение болтами может быть оправдано только разъемностью.
|
|
Выбор типа соединения определяет инженер.
Сварные соединения
Из истории сварки. Виды сварки.
Возникновение сварки относится к IV веку до н. э. Тогда трипольские племена, обитавшие на территории Западной Украины, Молдавии и Румынии, выполняли кузнечную сварку меди, а в II веке до н. э. – бронзы.
В 1802 году академик Петров В. В. открыл явление электрической дуги, но использована она была в сварочном производстве спустя 80 лет. Только в 1882 году русский изобретатель Бернандос Н. Н. применил электрическую дугу для сварки. Он изобрел также точечную контактную сварку.
В 1888 году русский инженер Славянов Н. Г. предложил выполнять дуговую сварку металлическим электродом. Он впервые в мире создал электросварочный аппарат.
С 1930 года в нашей стране сварку стали применять в большом объеме не только при ремонте, но и при производстве новых машиностроительных и строительных конструкций. Осуществлялось интенсивное внедрение сварки в производство, литые детали и клепаные конструкции частично или полностью начали заменяться сварными.
|
|
Институт сварки им. Патона Е. О. с 1940 года начал активное внедрение в производство механизированной сварки под флюсом. Наряду со сваркой в производстве широко применяются различные методы наплавки, наварки и пайки металлов.
Сварка — это технологический процесс получения неразъемного соединения металлических или неметаллических деталей с применением нагрева (до пластического или расплавленного состояния), выполненного таким образом, чтобы место соединения по механическим свойствам и своему составу по возможности не отличалось от основного материала детали.
Процессы сварки целесообразно рассматривать с трех основных точек зрения: конструктивной, технологической и по природе самих процессов.
С конструктивной точки зрения сварка представляет собой процессы создания неразъемных соединений металлических деталей. Сварные соединения необходимо рассматривать как элементы конструкций.
С технологической точки зрения сварка является важнейшими операциями процесса сборки металлических деталей в узлы и целые конструкции.
|
|
По природе процессов сварка является сложными металлургическими, разнообразными по форме процессами.
Сварка успешно заменяет поковки, отливки, клепаные соединения, упрощая технологический процесс, снижая трудоемкость и уменьшая вес изделия. Известно около 70 способов сварки. В соответствии с традиционной классификацией они делятся на две большие группы: сварка плавлением и сварка давлением.
При сварке плавлением металл нагревается в зоне сварки до жидкого состояния. К этому виду относятся дуговая, плазменная, лазерная, электрошлаковая, электронно-лучевая, ионно-лучевая, индукционная, газовая, термитная, литейная и др.
Для сварки давлением обязательным условием является наличие внешних сжимающих усилий. Это контактная, диффузионная, термокомпрессорная, дугопрессовая, шлакопрессовая, газопрессовая, трением, взрывом, холодная, магнито-импульсная и другие способы сварки.
При соединении деталей с помощью сварки плавлением к расплавляемой области подводят присадочный материал, который заполняет свариваемое место (рис. 1). Затвердевший после сварки металл, соединяющий сваренные детали, называют сварным швом. Формирование сварочного шва сопровождается частичным оплавлением поверхностей деталей, участвующих в образовании сварного соединения. Поверхности свариваемых деталей, подвергающиеся частичному оплавлению при формировании сварчного шва и участвующие в образовании соединения, называются свариваемыми кромками.
В зависимости от вида источника энергии различают термический, термомеханический и механический классы сварки.
Основные виды электросварки — дуговая, газовая и контактная.
Дуговая сварка - наиболее распространенный вид. Применяется везде, где есть источники электроэнергии.
Разновидности дуговой сварки:
- ручная сварка; этот метод сварки отличается низкой производительностью, но легко доступен для применения;
- полуавтоматическая сварка под слоем флюса; применяется для конструкций с короткими прерывистыми швами;
- автоматическая сварка под слоем флюса; этот метод сварки высокопроизводителен и экономичен, дает хорошее качество шва, применяется в крупносерийном и массовом производстве.
Газовая сварка применяется в основном там, где нет источников электроэнергии, например, при ремонте в полевых условиях.
При газовой сварке свариваемый и присадочный металлы расплавляют в пламени, получающемся при сгорании какого-либо горючего газа (чаще всего – ацетилена) в смеси с кислородом.
Газовую сварку осуществляют и без применения присадочного материала, где формирование шва проводят за счет расплавления кромок основного металла (соединения - стыковое с отбортовкой и угловое).
Эту сварку применяют в основном при ремонтных работах, при заварке дефектов чугунного литья, при сварке тонколистовых конструкций из малоуглеродистых сталей (толщиной до 5 мм) и некоторых цветных металлов.
По сравнению с электродуговой сваркой, газовая сварка - процесс малопроизводительный.
Недостатки: прочностные качества сварных соединений на сталях и алюминии невысоки, и также возникают значительные деформации свариваемых деталей.
Контактная сварка применяется в серийном и массовом производстве при нахлесточном соединении тонкого листового металла (точечная, роликовая) или при стыковом соединении круглого и полосового (стыковая сварка).
Для образования соединения на специальных контактных машинах стык разогревают электрическим током или силами трения до пластичного состояния металла и сдавливают.
Например, на долю стыковых соединений контактной сварки приходится более половины выпуска сварного режущего инструмента, где режущая (рабочая) часть из качественной быстрорежущей стали приварена силами трения и сжатия к хвостовой части из углеродистой или легированной стали меньшего качества (более дешевой).
Контактную точечную и шовную сварку применяют для соединения деталей из тонкого (δ≤3мм) листового материала. При точечной сварке листы нагревают и сдавливают электродами 1 (рис.1.1), при шовной – роликами 2 (рис.1.2).
При контактной сварке (сварка давлением) присадочный материал не применяют. Контактная сварка основана на использовании тепла, выделяющегося в месте соприкосновения свариваемых деталей (например, при прохождении через них электрического тока). Сварка производится с применением механического давления, под действием которого детали, предварительно нагретые в месте соединения (контакта) до пластического состояния или оплавления, образуют сварной шов.
Рис. 1. Получение сварного шва газовой сваркой
сварка8
Рис.1.1. Точечная сварка
сварка8
Рис.1.2. Шовная (роликовая) сварка
Рис.1.3. Стыковая сварка
Технологические процессы различных способов сварки и область их применения рассматриваются в курсе «Технология металлов и конструкционные материалы».
Выбор способа сварки определяется следующими факторами:
- маркой свариваемого материала;
- требуемыми свойствами сварного соединения;
- конструкцией сборочной единицы.
Необходимо принимать во внимание и дополнительные факторы, влияющие на выбор способа сварки (например, общий объем сварки в изделии, серийность и стоимость процесса сварки), и рассматривать их с учетом конкретных условий производства сварной конструкции.
Сварным соединением называют неразъемное соединение деталей с помощью сварных швов. Если в заклепочном соединении соединяющим элементом является заклепка, то в сварных - расплавленный металл, создающий при остывании неразъемное соединение, то есть такое, которые не может быть разобрано без повреждения деталей. Сварные соединения лучше других приближают составные детали к целым и позволяют изготавливать детали неограниченных размеров. Прочность сварных соединений при статических и ударных нагрузках доведена до прочности деталей из целого металла. Освоена сварка всех конструкционных сталей, включая высоколегированные, цветных сплавов и пластмасс.
Масса сварных конструкций при тех же габаритах значительно меньше клепаных (на 15%). Экономия металла достигается за счет использования полной площади сечения, а также возможности более рационального конструирования (например, применения стыковых соединений в тех случаях, когда при заклепочном соединении приходится применять накладки).
Стандарты, регламентирующие основные типы, конструктивные элементы, размеры и условные обозначения сварных соединений, даны в таблице 1.
Таблица 1
ГОСТ
Наименование
5264-80
Ручная дуговая сварка. Соединения сварные
8713-79
Сварка под флюсом. Соединения сварные
11533-75
Автоматическая и полуавтоматическая дуговая сварка под флюсом.
Соединения сварные под острыми и тупыми углами
11534-75
Ручная дуговая сварка.
Соединения сварные под острыми и тупыми углами
14771-76
Дуговая сварка в защитном газе. Соединения сварные
14776-79
Дуговая сварка. Соединения сварные
14806-80
Дуговая сварка алюминия и алюминиевых сплавов в инертных газах. Соединения сварные
15164-78
Электрошлаковая сварка. Соединения сварные
15878-79
Контактная сварка. Соединения сварные
16038-80
Сварка дуговая. Соединения сварные трубопроводов из меди и медно-никелевого сплава
16310-80
Соединения сварные из полиэтилена, полипропилена и винипласта
23518-79
Дуговая сварка в защитных газах. Соединения сварные под острыми и тупыми углами
23792-79
Соединения контактные, электрические, сварные
Ручная дуговая сварка
Схема ручной дуговой сварки покрытым электродом приведена на рис.2. На ней обозначены: 1 – хвостовик электрода; 2 – электродное покрытие; 3 – дуга; 4 – капля, переходящая с конца электрода в сварочную ванну; 5 – свариваемый металл; 6 – жидкий шлак; 7 – сварочная ванна; 8 – газопаровая оболочка; 9 – затвердевший шлак; 10 – шов.
image004
Рис.2
Для выполнения сварочной операции металл в зоне сварки нагревается и расплавляется под действием теплоты дуги, горящей между электродом и основным металлом. В результате развивается эмиссия электронов и ионизация газов и паров в промежутке между электродом и основным металлом, загорается дуга. Материал электрода, расплавленный дугой, заполняет стык соединяемых элементов. После остывания расплавленного металла образуется сварной шов. Для защиты плавящегося металла от попадания вредных веществ из воздуха на поверхность электрода наносится толстая защитная обмазка, выделяющая при плавлении электрода большое количество шлака и газов. Так как шлак имеет меньшую плотность, чем металл, он всплывает на поверхность сварочной ванны и изолирует металл от окружающей среды.
Технология сварки. Технологический процесс ручной дуговой сварки состоит из следующих операций:
– обработка свариваемых кромок;
– очистка поверхностей свариваемых заготовок;
– сборка и прихватка;
– сварка;
– правка;
– очистка швов от шлака закристаллизовавшихся брызг металла;
– контроль качества сварной конструкции.
Для выполнения сварочной операции возбуждают дугу прикасанием свободным от покрытия торцом электрода к основному металлу, а прерывают дугу – отрывом от него.
При ручной дуговой сварке швы накладываются во всех пространственных положениях – нижнем, вертикальном, потолочном. Наиболее высокое качество швов получается в нижнем положении.
Выбор режима сварки заключается в определении диаметра электрода и силы сварочного тока и зависит от толщины свариваемых элементов.
Сварочные электроды. Электрод для ручной дуговой сварки – это металлический стержень, на который нанесено покрытие. Как отмечалось ранее, при воздействии теплоты дуги компоненты покрытия электрода расплавляются, образуя жидкие шлаки и газы.
Государственным стандартом электроды подразделяются на классы: У – для сварки углеродистых и низколегированных сталей; Л – для сварки легированных конструкционных сталей; Т – для сварки легированных теплоустойчивых сталей; В – для сварки высоколегированных сталей с особыми свойствами.
Стандартом установлены следующие типы электродов: Э38, Э42, Э46 и Э50, Э55 и Э60 – для сварки углеродистых и низколегированных конструкционных сталей; Э42А, Э46А и Э50А – для сварки углеродистых и низколегированных конструкционных сталей, если к металлу сварных швов предъявляют повышенные требования по пластичности и ударной вязкости; Э70, Э85, Э100, Э125, Э150 – для сварки легированных конструкционных сталей повышенной прочности. В марках электродов число после буквы Э обозначает предел прочности наваренного металла, кгс/мм2 (1кгс/мм2 = 10 МПа), буква А указывает на то, что материал электрода – высококачественная сталь. Выбор электрода для сварки конкретной стали осуществляется с учетом требуемых химического состава и механических свойств металла шва, технологических и других характеристик электродов, а также специфики производства.
Сварочное оборудование. Ручную сварку выполняют на постоянном и переменном токах. При сварке на переменном токе потребляется меньше электроэнергии, источники переменного тока имеют более простую конструкцию, они долговечнее и надежнее. Однако при постоянном токе устойчивее горит дуга.
Для понижения напряжения в сети применяются трансформаторы. Питание электрической дуги выпрямленным током осуществляется различными сварочными выпрямителями. При сварке тонких деталей применяются специальные преобразователи с электронным блоком управления, которые обеспечивают хорошую стабилизацию тока.
Применение. Ручная дуговая сварка в основном применяется при монтажных и ремонтных работах, а также в единичном и мелкосерийном производствах. На предприятиях железнодорожного транспорта с применением ручной дуговой сварки выполняется более половины всего объема сварочных работ. Этим способом заваривают трещины и другие дефекты, наваривают изношенные поверхности деталей подвижного состава.
Преимущества. При ручной дуговой сварке можно накладывать швы в любом пространственном положении; выполняются сварные соединения всех типов; применяемое оборудование отличается простотой, надежностью и небольшими габаритами.
Недостатки. Низкая производительность; невысокое качество швов; автоматически не регулируется сила сварочного тока.
Механизированная и автоматическая дуговая сварка
Механизированная (или полуавтоматическая) сварка – это дуговая сварка, при которой подача плавящегося электрода и перемещение дуги относительно изделия выполняются с использованием механизмов. С ее помощью выполняют любые сварные соединения: стыковые, угловые, тавровые, нахлесточные и др.
Автоматической называют дуговую сварку, при которой возбуждение дуги, подача электрода и перемещение дуги относительно изделия выполняются механизмами без непосредственного участия человека, в том числе и по заданной программе.
Дата добавления: 2019-01-14; просмотров: 235; Мы поможем в написании вашей работы! |
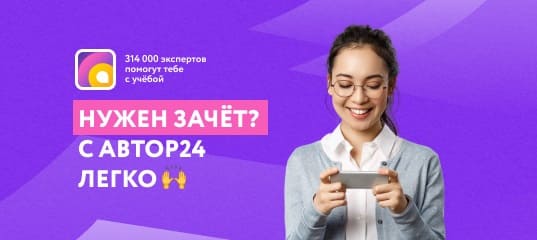
Мы поможем в написании ваших работ!