Мощность машин и её преобразование в механизмах 34 страница
k𝜎 - эффективный коэффициент концентрации напряжений в резьбе (k𝜎=3,5÷4,5– для углеродистых сталей; k𝜎=4,0÷5,5– для легированных сталей);
ψσ - коэффициент чувствительности материала к асимметрии цикла;
[Sa]=2,5÷4 – допускаемый коэффициент запаса прочности по амплитуде.
Запас статической прочности по текучести материалов проверяют по формуле
где [S]≥ 1,25 - допускаемый коэффициент запаса прочности по максимальному напряжению.
Опыт эксплуатации резьбовых соединений, подверженных действию переменных нагрузок, а также испытания соединений на усталость показывают целесообразность значительной начальной затяжки соединений для болтов из углеродистых сталей равной (0,6 – 0,7)σT, а из легированных сталей – (0,4 – 0,6)σT.
Затяжка увеличивает усталостную прочность болтов (так как уменьшает переменную составляющую напряжений в болтах) и соединяемых деталей (так как уменьшает микросдвиги). Следует учитывать, что напряжения затяжки при эксплуатации могут несколько снизиться вследствие обмятия микронеровностей на стыках и релаксации напряжений в болтах.
Конструктивные и технологические мероприятия, повышающие прочность резьбовых соединений
Основными конструктивными параметрами, определяющими прочность витков, являются отношение d/P и относительная высота гайки H/d.
Приведем влияние относительного шага P/d на прочность резьб в диапазоне применяемых значений P/d=0,02-0,2.
|
|
1. Напряжение разрыва σр существенно уменьшается с уменьшением P/d (в 1,5 раза в диапазоне P/d=0,2-0,02), что объясняется увеличением d1 с уменьшением шага резьбы.
Увеличение d и Р понижает сопротивление усталости резьбовой детали (масштабный эффект). Резьбы диаметром (30-60) мм имеют приблизительно в 2 раза меньшие пределы выносливости, чем резьбы диаметром (6-16) мм.
При переменных нагрузках для повышения податливости болта целесообразно уменьшать диаметр dс стержня болта (шпильки).
Обычно принимают
- при переменных нагрузках dc=0,8-1,05,
- при статических нагрузках dc/d1=1,05-1,15.
2. Напряжения среза слабо уменьшаются с измельчением резьбы в 1,25 раза. При статических и переменных нагрузках можно рекомендовать d/P=10-15. Не рекомендуется применять резьбу с d/P<8.
При мелкой резьбе d/P>20 может наступить явление цепкого среза, когда разрушение витков идет одно за другим и равнопрочности гайки и болта нельзя достичь даже при очень большой высоте гайки. Для гаек из пластмасс цепной срез витков возможен при d/P>7.
В целом мелкие резьбы несколько более выгодны по прочности, чем крупные. Однако точное изготовление мелких резьб сложнее, чем крупных, достичь равномерного распределения нагрузки по виткам у них труднее.
|
|
3. Напряжения смятия незначительно уменьшаются при уменьшении P/d и при m=1 составляют от 0,3 до 0,45, а при m=2 - от 0,55 до 0,8 напряжений разрыва.
4. Напряжения изгиба падают с уменьшением P/d и при m=1 составляют от 0,25 до 0,3, а при m=2 - от 0,5 до 0,6 напряжений разрыва. При стесненном изгибе (срез) напряжения в основании витков равны (0,13-0,15)σр.
При равноценных механических свойствах материала гайки и болта сопротивление усталости резьбы повышается с увеличением высоты гайки до H=1,2d. Дальнейшее увеличение высоты гайки не дает существенного возрастания прочности, так как нагрузка на первый виток изменяется очень мало.
Применение гаек с низким модулем упругости приводит к более равномерному распределению нагрузки по виткам.
Прочность ответственной силовой резьбы, нагруженной переменными усилиями, заметно снижается при стандартном для метрических резьб закруглении впадин между витками r=0,108P, поэтому принимают
r=(0,15-0,22)P.
Накатывание резьбы увеличивает усилия среза витков на (4-8)%. Ее можно проводить на всех материалах, имеющих относительное удлинение не ниже (8-10)% и предел прочности не выше 1100 МПа. Сопротивление усталости накатанной/резьбы при правильных режимах накатки и при отсутствии последующей термической обработки на 30 % больше нарезанной резьбы.
|
|
5. Снижение амплитудных напряжений. Ранее мы получили
Отсюда видно, что для уменьшения амплитудных напряжений (уменьшения доли внешней нагрузки, приходящейся на болт) нужно увеличить податливость болта. Податливость болта можно увеличить путем увеличения его длины или уменьшения его диаметра (рис. 57). Для увеличения длины болта применяют специальные дистанционные втулки. Уменьшение диаметра болта производят в ненарезанной части, за счет чего удается увеличить допустимую пульсирующую нагрузку на соединение более чем в 1,5 раза. Уменьшить х можно и за счет увеличения жесткости соединенных деталей (снижение λд) и стыка (улучшением пригонки, увеличением жесткости прокладок).
A
Рис.57
6. Уменьшение концентрации напряжений. Это достигается за счет тщательной обработки и введения галтелей при переходе от одного диаметра болта к другому и при переходе стержня болта в головку. Закругление под головкой в стандартном болте
|
|
r/d=0,016…0,05.
Изготовление резьбы методом накатки также снижает концентрацию напряжений при этом не нарушается структура металла, не перерезаются его волокна.
7. Выравнивание нагрузки по виткам. Это достигается применением гаек улучшенной конструкции. Такие конструкции приведены выше.
Расчет болтовых соединений группой болтов
Расчет таких соединений сводится к определению нагрузки для наиболее нагруженного болта. Затем рассчитывают прочность этого болта по формулам одного из случаев, рассмотренных выше.
Основные допущения при расчете.
1) Соединения, в которых более одного болта, относят к групповым соединениям.
2) Поверхности стыков остаются плоскими (недеформируемыми) при нагрузке. Это справедливо для стыков с жесткими соединяемыми деталями.
3) Поверхности стыка имеют оси симметрии, а болты расположены симметрично относительно этих осей.
4) Все болты соединения одинаковы и равнозатянуты. В некоторых случаях задается последовательность затяжки болтов.
5) В реальных условиях могут быть случаи, когда необходимо учитывать деформируемость деталей. Эта задача в данной методике не рассматривается.
6) Предположение, что все болты одинаковы, упрощает решение задачи конструирования и изготовления, но требуется четко определить наиболее нагруженный болт и расчет вести по наибольшей нагрузке. Расчет других болтов нет смысла проводить, так как они все будут менее нагружены.
Классификация групповых болтовых соединений.
Групповые болтовые соединения условно делят на:
а) Соединения, нагруженные сдвигающими силами и моментами (то есть действующими в плоскости стыка).
б) Соединения, нагруженные отрывающими силами и моментами (то есть действующими в плоскости, перпендикулярной к плоскости стыка).
в) Соединения, нагруженные сдвигающими и отрывающими силовыми факторами одновременно.
В настоящем лекционном курсе невозможно и нерационально пытаться рассмотреть все варианты группового расчета резьбовых соединений. При проектировании технических устройств и систем могут встретиться различные схемы резьбовых соединений, требующие для расчета использования методики совместности деформаций. Варианты расчета таких систем можно найти в специализированной литературе.
1. Порядок расчета группового соединения, нагруженного в плоскости стыка.
1.1) Конструируем стык.
1.2) Составляем расчетную схему нагружения. Если действуют несколько силовых факторов, они приводятся к центру тяжести стыка, заменяются проекциями главного вектора сил на оси: Fx, Fy, Fz, и составляющими главного момента, действующих относительно осей: Mx, My, Mz.
Момент, действующий в плоскости стыка, то есть относительно оси, перпендикулярной плоскости стыка, называем крутящим или сдвигающим и обозначаем Т. Остальные моменты — отрывающие. Такой прием удобен, так как позволяет четко представить себе нагружение и применить принцип независимости действия сил (принцип суперпозиции) для определения силового воздействия на каждый болт.
1.3) Предположение, что стыки недеформируемы при нагрузке, позволяет считать:
а) что при действии сил, приложенных в центре тяжести стыка, сдвигающие силы распределяются между болтами равномерно;
б) что при действии крутящего момента происходит поворот сечения относительно его центра тяжести, чему препятствует болт, поставленный без зазора, или сила трения в стыке, вызванная силой затяжки, при установке болтов с зазором.
1.4) Определяем нагружение каждого болта на примере рис.58. Рассмотрим вариант двухрядного стыка с 5 болтами в ряду. Центр тяжести стыка расположен в точке О. Оси Z и X лежат в плоскости стыка и проходят через О – центр тяжести, он же центр симметрии стыка. Ось Y перпендикулярна плоскости стыка, относительно этой оси действует момент Т.
Рис. 58. Схема нагружения болтов сдвигающими силами и моментом.
1.5) Приложим в центр тяжести О силу Fx. В силу сделанных предположений нагрузка на все болты от силы Fx одинакова по величине и направлению Fx1= Fx2 =…= Fx10 = .
1.6) Приложим в центр тяжести О силу Fz по аналогии с Fx.
Fz1 = Fz2 =…= Fz10 =
1.7) Приложим крутящий момент Т, действующий относительно оси Y (см. рис. 58). Усилия от действия момента Т распределяются между болтами неравномерно по величине и направлению. Усилие на произвольный болт направлено перпендикулярно к радиус вектору ri и по величине определяется в общем случае:
где ρi – величина расстояния от центра тяжести стыка до оси произвольного болта, zi – число болтов, расположенных на радиусе ρi.
Для определения наиболее нагруженного болта в числителе ri принимается ρmax. В случае нагружения по рис. 58 наибольшее усилие:
1.8) Суммарная нагрузка на каждый болт определяется суммой:
1.9) Наибольшая нагрузка приходится на болт 10 (см. рис. 58). Величина наибольшей нагрузки на болт 10:
Обратите внимание, что суммирование сил — векторное. Это действие проще всего выполнить графически в масштабе. Для суммирования алгебраического следует вычислять углы между векторами, а это решение громоздкое.
1.10) В случае установки болтов без зазора проводим расчет диаметра резьбы болта по методике, изложенной в пункте «Расчет соединения одиночным болтом, установленным без зазора …». Расчет ведется по усилию Fmax из условия неподвижности стыка.
1.11) В случае установки болтов с зазором проводим расчет диаметра резьбы болта по методике, изложенной в пункте «Расчет соединения одиночным болтом, установленным в отверстии деталей с зазором …». Расчет ведется по усилию Fmax из условия неподвижности стыка.
1.12) В случае, если в результате расчета болтов не выполняется условие d<dmax, т.е. размер резьбы превышает наибольший допустимый для данной детали, то следует:
а) изменить материал болта, т.е. допускаемое напряжение. Этот прием возможен при небольших отклонениях диаметров.
б) вернуться к п.1 в части конструирования стыка, изменить число болтов, размеры стыка, число рядов и т. д. В некоторых случаях надо вносить изменения в размеры соединяемых деталей.
2. Порядок расчета группового болтового соединения, нагруженного в плоскости, перпендикулярной к плоскости стыка.
2.1) Конструируют стык.
Основные правила при конструировании изложены ранее. Задаются предварительно числом болтов и другими параметрами стыка (см. рис. 59,д). Не усложняйте конструкцию стыка при первом конструировании. Задачи обычно требуют нескольких приближений, а они связаны, в основном, с конструированием стыка. На рис.59,д показан стык, состоящий из 12 болтов.
а) б) в) г) д)
Рис. 59. Схема нагружения стыка отрывающими силой Fx и моментом My:
а) схема нагружения; б) распределение отрывающей силы по болтам стыка;
в) распределение сил от отрывающего момента по болтам стыка; г) распределение суммарного нагружения по болтам стыка; д) план стыка.
2.2) Составляют расчетную схему нагружения. Если действует несколько отрывающих силовых факторов, то удобно привести их к центру тяжести стыка, заменить их главным вектором внешних сил и спроектировать его на ось, перпендикулярную плоскости стыка, и главным моментом My относительно оси Y. На рис. 59,а сила Fx – отрывающая сила, момент Мy – отрывающий момент.
2.3) Сделанные предположения о жесткости стыка позволяют считать:
а) отрывающие силы, действующие в центре тяжести стыка, равномерно воспринимаются всеми болтами.
б) отрывающие моменты вызывают поворот сечения относительно осей, проходящих через центр тяжести стыка.
2.4) Определяем нагружение каждого болта.
а) Отрывающая сила Fx распределяется между болтами равномерно. Нагружение произвольно взятого болта , где z – суммарное число болтов в стыке. На рис. 59,б показано распределение внешней отрывающей силы Fx между болтами.
б) Отрывающий момент нагружает болты неравномерно величинами, пропорциональными расстояниям от центра тяжести. Усилие, действующее на произвольный болт, см. рис. 59,г:
где z1=3 – число болтов ряда на расстоянии l3 от оси Y, z2=2 – число болтов ряда на расстоянии l4 от оси Y.
Из построенных эпюр распределения внешней нагрузки от отрывающего момента (рис. 59,в) видно, что наибольшая нагрузка в болтах 1, 2, 3 растягивающая и в болтах 7, 8, 9 – сжимающая.
в) На рис. 59,г показано суммарное нагружение болтов левого ряда. Наиболее нагружены болты 1, 2, 3.
2.5) Сила затяжки болтов для данного соединения рассчитывается по методике, изложенной в разделе 4.6. Определяется сила затяжки из условия нераскрытия стыка.
2.6) По величине FΣmax будем рассчитывать болт на прочность по методике, изложенной в разделе 2.4 «Расчёт соединения одиночным болтом, нагружённым отрывающей силой».
2.7) Из произведенного расчета определяют необходимый стандартный размер резьбы болта. Если произведенный расчет дает отклонения от предварительно принятого размера резьбы, следует:
а) изменить марку материала болта,
б) изменить конструкцию стыка под другой болт (например, если возможно изменить число болтов в ряду, изменить размеры стыка, например, l3 и l4 и т.д.).
После уточнения произвести проверочный расчет болтов до получения приемлемого результата.
3. Порядок расчета группового соединения в случае нагружения одновременно сдвигающими и отрывающими нагрузками.
3.1) Такой случай является наиболее распространенным в практике. Пример приведен на рис. 60,а.
3.2) Конструирование стыка ничем не отличается от изложенного в подразделе 2.
3.3) Составляют расчетную схему нагружения (см. п. 1.2 и 2.2), приводят отрывающие силовые факторы к проекции главного вектора отрывающих сил и отрывающему моменту (см. п. 2.2).
3.4) Приводят сдвигающие силовые факторы к проекции главного вектора Fz.
3.5) Дальнейший расчет идет по порядку, изложенному в п. 2.3 ¸ 2.6.
3.6) Выполняют проверку по условию отсутствия сдвига при принятой силе затяжки болтов, рассчитанных по методике, изложенной в п. 2.6.
где Fзат – сила затяжки болтов, z – общее число болтов соединения, Fотр – отрывающая сила (например, сила Fx), Fсдв – суммарная сдвигающая сила (например, сила Fz), f – коэффициент трения стыка о фундамент (см. литературу), S’=1,3÷2 – коэффициент запаса по сдвигу.
В приведенной формуле не учитывают действие отрывающего момента, так как он не сдвигает стык и не изменяет суммарной величины сил трения в стыке.
3.7) Если условие 3.6 не выполняется, то условие по нераскрытию стыка является не определяющим и, в тоже время, условие неподвижности стыка является основным. В этом случае можно поступить одним из следующих способов:
а) пересчитать силу затяжки из условия отсутствия сдвига и пересчитать диаметр резьбы болта:
б) установить болты (все или часть) без зазора;
в) применить разгрузочные устройства, воспринимающие всю сдвигающую нагрузку (см. литературу).
4. Расчет силы затяжки фундаментных болтов.
4.1) К этой группе болтов относятся болты, крепящие оборудование и металлоконструкции к металлическим рамам или к неметаллическим стенам, колоннам, фундаментам.
а) б) в) г) д) е)
Рис. 60. Схема к расчету силы затяжки фундаментных болтов:
1 – основание, 2 – фундамент;
а) схема нагружения; б) эпюра напряжений в стыке от силы затяжки; в) эпюра напряжений от отрывающей силы Fx;
г) эпюра напряжений в стыке от отрывающего момента Му; д) суммарная эпюра напряжений в стыке; е) план стыка.
4.2) Эти болтовые соединения относятся к соединениям, нагруженным отрывающими и сдвигающими силовыми факторами одновременно.
4.3) Обычно расчет ведут по условию нераскрытия стыка, а по условию неподвижности стыка делают проверку.
4.4) На рис. 60,а показан пример такого соединения. Размеры опорной пластины (стыка) B×H см. рис. 60,е.
4.5) До приложения внешней нагрузки Fx, Fz, My производят затяжку болтов усилием Fзат. Все болты затягивают одинаково. Тогда давление основания на фундамент (напряжение смятия):
где А=В∙Н – площадь стыка.
4.6) Внешние силовые факторы вызывают в стыке дополнительные напряжения.
а) Усилие Fx вызывает уменьшение напряжения от затяжки на величину:
где (1–𝜒) – доля внешней нагрузки, которая идет на нагружение стыка внешней силой. В фундаменте принимают χ≈0, что идет в запас прочности.
Дата добавления: 2019-01-14; просмотров: 213; Мы поможем в написании вашей работы! |
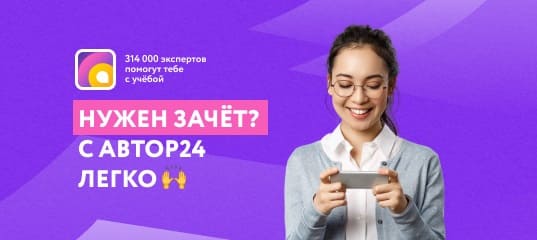
Мы поможем в написании ваших работ!