Обоснование принятых способов устранения дефектов ремонтируемой детали
Для устранения каждого дефекта должен быть выбран рациональный способ, т. е. технически обоснованный и экономически целесообразный.
Рациональный способ восстановления деталей определяют, пользуясь критериями: технологическим (применяемости), техническим(долговечности)и технико-экономическим (обобщающим).
Технологический критерий характеризует принципиальную возможность применения нескольких способов восстановления исходя из конструктивно-технических особенностей детали или определенных групп деталей. К их числу относятся: геометрическая форма и размеры, материал, термическая или другой вид поверхностной обработки, твердость, шероховатость поверхности и точность изготовления детали, характер нагрузки, вид трения и износа, размеры износа. Для устранения дефектов, указанных в задании, предварительно намечаем отдельные способы восстановления и проводим их сравнение. Так, для восстановления дефектов № 2 и № 4, возможно использование вибродуговой наплавки, наплавки в среде углекислого газа, электроискровой обработки.
Вибродуговая наплавка – разновидность дуговой наплавки металлическим электродом. Процесс наплавки осуществляется при вибрации электрода с подачей охлаждающей жидкости на наплавленную поверхность.
К наплавляемой поверхности детали, которая вращается в центрах токарного станка, роликами подающего механизма из кассеты через вибрирующий мундштук подается электродная проволока. Из-за колебаний мундштука, вызываемых эксцентриковым механизмом, проволока периодически прикасается к поверхности детали и расплавляется под действием импульсных электрических разрядов, поступающих от генератора. Под действием вибратора мундштук вместе с проволокой вибрирует с частотой 50 Гц и амплитудой колебания до 4 мм (практически – 1,8–3,2 мм).
|
|
Вибрация электрода во время наплавки обеспечивает стабильность процесса за счет частых возбуждений дуговых разрядов и способствует подаче электродной проволоки небольшими порциями, что обеспечивает лучшее формирование наплавленных валиков.
Качество соединения наплавленного металла с основным зависит от нескольких факторов. Основными из них являются полярность тока, шаг наплавки (подача суппорта станка на один оборот детали), угол подвода электрода к детали, качество очистки и подготовки поверхности, подлежащей наплавлению, толщина слоя наплавки и др.
Вибродуговая наплавка имеет ряд преимуществ: дает возможность наплавлять металл только на изношенную часть, что уменьшает трудоемкость последующей механической обработки; получать наплавленный слой без пор и трещин; деформация детали – минимальная и не превышает полей допусков посадочных мест; минимальная зона термического влияния.
|
|
Недостатком вибродуговой наплавки является уменьшение до 40 % сопротивления усталости наплавленных деталей. Этот показатель можно улучшить термообработкой.
Наплавка в среде углекислого газа.Этот способ в значительной степени отличается от других способов восстановления деталей: не нужно ни флюсов, ни электродных покрытий. Дуга между электродом и наплавляемым изделием горит в струе газа, вытесняющего воздух из плавильного пространства и защищающего расплавленный металл от воздействия кислорода и азота.
Наплавку в среде углекислого газа выполняют на постоянном токе обратной полярности. Скорость наплавки устанавливают в зависимости от толщины наплавляемого металла и качества формирования наплавленного слоя. Наплавку валиков осуществляют с шагом 2,5–3,5 мм. Каждый последующий валик должен перекрывать предыдущий не менее чем на 1/3 его ширины.
Автоматическая наплавка в среде углекислого газа имеет следующие преимущества: при наплавке отсутствуют вредные выделения и шлаковые корки; открытая дуга дает возможность наблюдать и корректировать процесс, проводить наплавку при любом пространственном положении наплавляемой плоскости, механизировать наплавку, выполняемую на мелких деталях (валах диаметром 10 мм и более).
|
|
К недостаткам способа относятся: повышенное разбрызгивание металла (5– 10 %), необходимость применения легированной проволоки для получения наплавленного металла с требуемыми свойствами, открытое световое излучение дуги.
Электроискровая обработка. В основе всех технологических операций по обработке металлов электрической искрой лежит ее способность обеспечивать высокую плотность потока тепла на малом участке электродов и на поверхности обрабатываемой детали. При таком воздействии электрод быстро нагревается, затем плавится и частично испаряется.
К основным достоинствам электроискрового легирования следует отнести локальную обработку поверхности; отсутствие необходимости специальной предварительной подготовки обрабатываемой поверхности; возможность диффузионного обогащения поверхности катода составными элементами анода без изменения размера детали-катода; высокую прочность сцепления нанесенного материала с основой; отсутствие нагрева детали в процессе обработки; возможность использования в качестве обрабатывающих материалов как чистых металлов, так их сплавов, металлокерамических композиций и тугоплавких соединений.
|
|
Испытания показали, что при ЭИО поверхности материала графитовым электродом износ уменьшается в 1,84 раза; после натирания Al2O3, Si3N4, ZrN и TiN и ЭИО графитом – в 1,26; 1,35; 2,3 и 4 раза соответственно.
Комбинирование электроискровой наплавки и поверхностно-пластического деформирования (ППД) позволяет восстановить номинальный размер детали, дополнительно упрочнить поверхностный слой, повысить сопротивление усталости детали за счет изменения остаточных напряжений растяжения на остаточные напряжения сжатия, снизить пористость покрытия, сформировать масляные карманы оптимального качества, способные удерживать смазку в зоне трения.
Применение метода ЭИО для восстановления размеров изношенных деталей позволяет уменьшить количество используемого при ремонте как универсального, так и специального оборудования.
Электроискровые технологии обладают высокой технической и экономической эффективностью. Кроме этого, эти технологии экологически чистые и повышают культуру ремонтного производства.
Технический критерий (долговечности)оценивает каждый способ (выбранный по технологическому признаку) устранения дефектов детали с точки зрения восстановления свойств поверхностей, т. е. обеспечения работоспособности за счет достаточной твердости, износостойкости и сцепляемости покрытия восстановленной детали.
Коэффициент долговечности определяется как функция
В общем случае коэффициент долговечности Кд является функцией трех переменных:
Кд = f (Ки, Кв, Кс), (5.1)
где Ки – коэффициент износостойкости;
Кв – коэффициент выносливости;
Ксц – коэффициент сцепляемости.
Из числа способов, выбранных по технологическому критерию, к дальнейшему анализу принимают те, которые обеспечивают коэффициент долговечности восстановленной поверхностей не менее 0,8 [2].
Технико-экономический критерий связывает стоимость восстановления детали с ее долговечностью после устранения дефектов и характеризуется коэффициентом технико-экономической эффективности, определяемым по формуле
КЭ = СВ / КД, (5.2)
где КЭ– коэффициент технико-экономической эффективности;
СВ – удельная себестоимость восстановления 1 см2 изношенной поверхности восстановления.
Эффективным считается способ, у которого КЭ ® min.
Значения коэффициентов сцепления, выносливости и сцепляемости являются табличными значениями и принимаются из таблицы 3.1.
Данные по характеристикам выбранных способов восстановления и результаты расчетов приводятся в таблице 5.1.
Таблица 5.1 – Характеристика способов восстановления дефектов детали
| |||||||
Наименование способов восстановление |
Коэффициенты | Удельная себестоимость восстановления руб./м2 | № дефекта
| ||||
КИ | КВ | КСЦ | КД | КЭ | |||
1.Наплавка в среде СО2 | 1,3–1,6 | 0,7 | 1,0 | 0,8 | 15,07 | 8,8–12,0 | 2, 3, 4 |
2.Электроконтактная приварка ленты | 1,0–2,3 | 0,7–1,0 | 0,7–0,8 | 0,8 | 14,04 | 8,4–11,2 | 2 |
3.Вибродуговая наплавка | 2,0 | 0,95 | 0,9–1,0 | 0,9 | 21,70 | 19,6–20,2 | 2,3,4 |
4.Электроискровая обработка | 2,0 | 0,9 | 1,0 | 0,9 | 10,81 | 9,8–14,2 | 2 |
5. Метод ДРД (резьбовая спиральная вставка) | 1,0 | 0,8 | 1,0 | 0,8 | 49,37 | 39,5–76,5 | 1 |
6. Метод ДРД (установка втулки с двусторонней резьбой). | 1,0 | 0,8 | 1,0 | 0,8 | 49,37 | 39,5–76,5 | 1 |
7. Фрезерование нового шпоночного паза | 0,8–1,0 | 0,9–1,0 | 1,0 | 0,8 | 10,85 | 8,7–12,3 | 3 |
Для дефекта № 1 наименьшим коэффициентом технико-экономической эффективности обладает установка резьбовой спиральной вставки. Данный способ восстановления достаточно производительный, прост и широкодоступен. Этот способ восстановления принимаем в качестве основного, а допускаемый способ – установка втулки с двусторонней резьбой.
Для дефекта № 2 наименьшим коэффициентом технико-экономической эффективности обладает электроискровая обработка. Этот способ восстановления принимаем в качестве основного, а допускаемый способ – наплавка в среде углекислого газа.
Для дефекта № 3 наименьшим коэффициентом технико-экономической эффективности обладает фрезерование нового шпоночного паза под углом 180° относительно изношенного. Этот способ восстановления принимаем в качестве основного, а допускаемый способ – заварка изношенного паза в среде углекислого газа с последующим фрезерованием.
Для дефекта № 4 наименьшим коэффициентом технико-экономической эффективности обладает наплавка в среде углекислого газа. Этот способ восстановления принимаем в качестве основного, а допускаемый способ –вибродуговая наплавка.
Дата добавления: 2018-11-24; просмотров: 599; Мы поможем в написании вашей работы! |
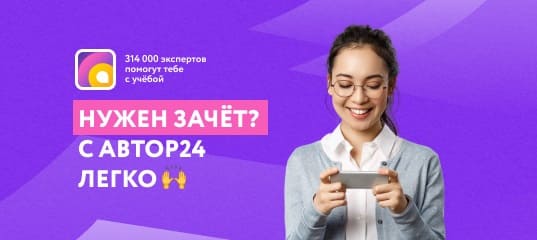
Мы поможем в написании ваших работ!