МИНИСТЕРСТВО СЕЛЬСКОГО ХОЗЯЙСТВА
И ПРОДОВОЛЬСТВИЯ РЕСПУБЛИКИ БЕЛАРУСЬ
Учреждение образования
«БЕЛОРУССКИЙ ГОСУДАРСТВЕННЫЙ
АГРАРНЫЙ ТЕХНИЧЕСКИЙ УНИВЕРСИТЕТ»
Факультет: «Технический сервис в АПК»
Кафедра: «Технологии и организация технического сервиса»
Пояснительная записка
к курсовому проекту по дисциплине «Технология ремонта машин»
на тему: «Разработать технологический процесс восстановления валика водяного насоса 50-1307052-Б (деф.1-4) двигателя Д-243»
Шифр 0 2.60.000.00.000
Студент 4 курса 10 тс группы
/Иванов В.И/
(личная подпись) (ФИО)
Руководитель
/ /
(личная подпись) (ФИО)
Минск, 2017
Учреждение образования
|
|
«БЕЛОРУССКИЙ ГОСУДАРСТВЕННЫЙ
АГРАРНЫЙ ТЕХНИЧЕСКИЙ УНИВЕРСИТЕТ »
Факультет «Технический сервис в АПК»
Кафедра «Технологии и организация технического сервиса»
Утверждаю Зав. кафедрой _________________ ______________________________ «_______»_______________20___г. |
ЗАДАНИЕ
На курсовой проект
по дисциплине «Технология ремонта машин»
Студенту Иванову В.И. группа 10 тс
Тема курсового проекта: Разработать технологический процесс восстановления валика водяного насоса 50-1307052-Б (деф.1-4) двигателя Д-243
Исходные данные:
1. Сборочный чертеж узла машины или рабочий чертеж детали, дефекты, подлежащие устранению.
2. Каталоги деталей и сборочных единиц на тракторы, автомобили и сельскохозяйственные машины по принадлежности ремонтируемой детали, узла.
Содержание расчетно-пояснительной записки:
Реферат. Содержание. Введение.
1 Анализ конструкции, условия работы и основные неисправности сборочной единицы.
2 Разработка структурной схемы разборки и маршрута доступа к ремонтируемой детали.
3 Разработка технологического процесса очистки (мойки) детали.
3.1 Обоснование требований к качеству очистки (мойки) и способов ее контроля.
3.2 Характеристика загрязнений и выбор способов очистки (мойки) детали.
|
|
3.3 Выбор оборудования, средств и режимов технологического процесса очистки (мойки).
4 Разработка технологического процесса дефектации детали.
4.1 Анализ конструкции и условий работы детали.
4.2 Виды и характеристика неустранимых и устранимых дефектов детали.
4.3 Выбор способов и средств контроля дефектов.
4.4 Разработка карты дефектации и ремонта.
5 Проектирование технологического процесса ремонта (восстановления) детали.
5.1 Описание и анализ аналога технологического процесса ремонта (восстановления) детали.
5.2 Обоснования принятых способов устранения дефектов ремонтируемой детали.
5.3 Выбор технологических баз и обоснование последовательности устранения дефектов.
5.4 Выбор средств технологического оснащения и расчет режимов выполнения технологических операций.
5.5 Техническое нормирование основных операций.
5.6 Оформление технологического процесса и ремонтного чертежа детали.
Заключение.
Список использованных источников.
Приложение: Комплект документов единичного технологического процесса восстановления детали (маршрутно-операционное описание).
Перечень графического материала:
сборочный чертеж и структурная схема разборки водяного насоса – 1 лист формата А1; ремонтный чертеж валика водяного насоса – 1 лист формата А1; карта ТП восстановления валика водяного насоса – 1 лист формата А1.
|
|
Календарный график работы над проектом:
№ | Наименование раздела, подраздела | Объем работы, % | Дата выполнения | Подпись руководителя |
1. | Анализ конструкции и условий работы узла, разработка структурной схемы разборки – формат А1 | 20 | ||
2. | Разработка технологии очистки детали | 10 | ||
3. | Разработка технологии дефектации детали | 10 | ||
4. | Разработка карты дефектации и ремонта | 10 | ||
5 | Разработка ремонтного чертежа детали – формат А1 | 10 | ||
6. | Проектирование ТП восстановления детали | 20 | ||
7. | Разработка карты ТП восстановления детали – формат А1 | 10 | ||
8. | Оформление расчетно-пояснительной записки и комплекта документов ТП | 10 |
Дата выдачи задания «___»____________________20____г.
Срок сдачи курсовой работы «___»____________________20____г.
Руководитель__________________ _________/_______________ /
Задание принял к исполнению «___»____________________20____г.
Студент___________________________________/_______________ /
|
|
Р еферат
Курсовой проект: 81с., таблиц 4, рисунков 6, использованных источников 14. Графическая часть – 3 листа формата А1.
Ключевые слова; водяной насос, разборка; валик водяного насоса, износ; очистка; дефектация; восстановление; оборудование; технологический процесс, комплект документов
Объектом исследования является водяной насос 240-1307010-А двигателя Д-243.
Цель курсового проекта – разработка перспективного технологического процесса восстановления валика водяного насоса 50-1307052-Б.
Приведен анализ конструкции, условий работы и неисправностей водяного насоса. Предложена рациональная последовательность выполняя разборочных работ при его ремонте.
На основании анализа дефектов и возможных способов их устранения разработан перспективный технологический процесс восстановления валика водяного насоса. Приведено его сравнение с базовым (аналогом) технологическим процессом, применяемым на ремонтных предприятиях
В процессе выполнения проекта разработаны технологические процессы дефектации и восстановления детали. Обоснованы необходимый измерительный инструмент, методы обнаружения дефектов и способы восстановления детали. Разработан маршрут восстановления детали, рассчитаны технологические режимы и нормы времени. Предлагаемый технологический процесс выгодно отличается от базового за счет применения прогрессивных технологических решений при очистке, дефектации и инновационной технологии восстановлений посадочных мест под подшипники электроискровым легированием, позволяющий повысить износостойкость восстанавливаемых поверхностей более чем в два раза и снизить себестоимость восстановления.
Содержание
| ||
Введение…………………………………………………………………………. | 6 | |
1 | Анализ конструкции, принцип работы и основные неисправности сборочной единицы……………………………………………….………… | 8 |
2 | Разработка структурной схемы разборки и маршрута доступа к ремонтируемой детали……………………………………………………… | 12 |
3 | Разработка технологического процесса очистки (мойки) детали………… | 18 |
3.1 Обоснование требований к качеству очистки (мойки) и способов ее контроля……………………………………………………………………… | 18 | |
3.2 Характеристика загрязнений и выбор способов очистки (мойки) детали…………………………………………………………………………. | 19 | |
3.3 Выбор оборудования, средств и режимов технологического процесса очистки (мойки)………………………… …………………………………... | 20 | |
4 | Разработка технологического процесса дефектации детали……………… | 23 |
4.1 Анализ конструкции и условий работы детали....................................... | 23 | |
4.2 Виды и характеристика устранимых и неустранимых дефектов детали………………………………………………………………………… | 24 | |
4.3 Выбор способов и средств контроля дефектов………………………... | 25 | |
4.4 Разработка карты дефектации и ремонта………………………………. | 26 | |
5 | Проектирование технологического процесса ремонта (восстановления) детали………………………………………………………………………… | 29 |
5.1 Описание и анализ аналога технологического процесса ремонта (восстановления) детали…………………………………………………….. | 29 | |
5.2 Обоснование принятых способов устранения дефектов ремонтируемой детали ……………………………………………………… | 30 |
5.3 Выбор технологических баз и обоснование последовательности устранения дефектов…………………………………………………………… | 34 | ||
| 5.4 Выбор средств технологического оснащения и расчет режимов выполнения технологических операций……………………………………… | 37 | |
5.5 Техническое нормирование основных операций.……………….………. | 49 | ||
5.6 Оформление технологического процесса и ремонтного чертежа детали | 63 | ||
Заключение…………………………………………………………….……….. | 68 | ||
Список использованных источников……………………………………….… | 70 | ||
Приложение: комплект документов единичного технологического процесса восстановления детали (маршрутно-операционное описание)..…. | 71 | ||
Введение
В процессе эксплуатации машины подвергаются типичным внешним (эксплуатационным) и внутренним воздействиям, в результате чего изменяется их техническое состояние, что ухудшает технико-экономические показатели машин: увеличивается расход топлива и масла; уменьшаются рабочие скорости и мощность, тяговое усилие; снижается производительность. Основные причины снижения исходных характеристик: нарушение исходных регулировок механизмов и систем, ослабление креплений, изменение свойств материалов, зазоров и натягов в соединениях деталей в результате изнашивания.
Эффективное использование машин и оборудования обеспечивается высоким уровнем их технического обслуживания и ремонта, наличием необходимого числа запасных частей. Сбалансированное обеспечение запасными частями ремонтных предприятий и сферы эксплуатации машин и оборудования, как показывают технико-экономические расчеты, целесообразно осуществлять с учетом периодического возобновления работоспособности деталей, восстановленных современными способами.
В настоящее время затраты на техническое обслуживание и ремонт находятся в пределах 12–13 % от себестоимости произведенной сельскохозяйственной продукции и составляют свыше 20 % в общих затратах на эксплуатацию машин и оборудования. В структуре затрат на ремонт сельскохозяйственной техники стоимость запасных частей составляет 55–70 %.
Следует отметить, что рост затрат на ремонт в значительной мере связан со снижением удельного веса восстанавливаемых деталей. Если в 80-х годах прошлого века он составлял 25 %, то в настоящее время – не более 7–8 %. Международная практика свидетельствует, что доля восстанавливаемых деталей в общем объеме потребления запасных частей достигает в зарубежных странах 30–35 % [1].
Повысить эффективность технического сервиса машин и снизить эксплуатационные затраты можно путем совершенствования организации и увеличения объемов восстановления деталей. По сравнению с производством новых деталей, при восстановлении используют на 90 % меньше материала и энергии. В этой связи прогноз на увеличение объемов восстановления деталей в ближайшей перспективе соответствует мировым тенденциям.
Причинами отказов деталей сельскохозяйственной техники являются дефекты, которые подразделяются: на конструктивные, вызванные ошибками при конструировании (до 0,01 %); производственные, связанные с ошибками при производстве (до 0,01 %); эксплуатационные – из-за естественного износа (82–99 %); аварийные (неправильная эксплуатация, несвоевременное обнаружение дефектов, усталость металла, коррозия).
При этом следует учесть, что большинство деталей машин требуют замены из-за износов, не превышающих не только десятых, но и сотых долей миллиметра. Например, свыше 85 % деталей тракторов, автомобилей, сложных сельхозмашин становятся неработоспособными при износах, не превышающих 0,3 мм. Так, в каждом списанном тракторе содержится до 20–35 % деталей, годных для вторичного использования без ремонта, 40–45 % деталей можно использовать после восстановления и только 25–30 % деталей не подлежат восстановлению и утилизируются [1].
Основными положениями концепции развития и совершенствования производств по восстановлению и упрочнению деталей предусматривается внедрение на предприятиях усовершенствованных традиционных и новых ресурсо- и энергосберегающих технологических процессов, таких как: электроконтактная наплавка ленты и проволоки; электроискровая обработка; электродуговая наплавка в среде защитных газов; газопламенная и плазменная наплавка порошковыми материалами; металлизация, детонационно-газовое напыление; лазерная наплавка (термоупрочнение); электрошлаковый переплав; гальванопокрытия (железнение, хромирование, электролитическое натирание), пластическая, термопластическая деформация; постановка дополнительных деталей; нанесение анаэробных герметиков и др.
При применении современных способов восстановления и упрочнения поверхностей долговечность восстановленных деталей при стоимости, составляющей 40…60 % от цены новых, может достигать уровня новых, а иногда и превзойти их. Кроме того, в процессе восстановления деталей количество производственных операций сокращается в 5–8 раз по сравнению с изготовлением новых. Таким образом, восстановление изношенных деталей является важнейшим источником ресурсо- и энергосбережения.
Целью курсового проекта является решение комплекса инженерно-технических задач, связанных с разработкой нового технологического процесса восстановления валика водяного насоса двигателя Д-243 в условиях ремонтного предприятия.
В процессе выполнения проекта последовательно решаются следующие задачи:
– проводится анализ конструкции, изучается принцип работы и основные неисправности сборочной единицы (водяного насоса);
– разрабатывается структурная схема разборки и маршрут доступа к ремонтируемой детали (валика водяного насоса);
– разрабатывается технологический процесс очистки (мойки) детали;
– разрабатывается технологический процесс дефектации валика водяного насоса;
– проектируется технологический процесс восстановления валика водяного насоса;
– разрабатывается комплект технологической документации на разборку (сборку), дефектацию, восстановление детали.
– выполняется графическая часть проекта (структурная схема разборки сборочной единицы, ремонтный чертеж детали, схема технологического процесса восстановления детали).
1 Анализ конструкции, принцип работы и основные неисправности сборочной единицы
В соответствии с заданием на курсовое проектирование необходимо разработать перспективный технологический процесс восстановления валика водяного насоса двигателя Д-243.
Дизельный двигатель Д-243 входит в состав семейства двигателей
Д-240/242/243,245, выпускаемых ОАО «Минский моторный завод». Они состоят из блока цилиндров, головки цилиндров, кривошипно-шатунного механизма, механизма газораспределения, а также узлов и агрегатов систем питания, смазки, охлаждения, пуска и электрооборудования.
Система охлаждения двигателя Д-243 трактора МТЗ-80/82 – закрытая, с принудительной циркуляцией жидкости. Система включает в себя следующие основные компоненты: водяной насос, термостат, радиатор водяной, вентилятор, шторку, термометр, а также водоотводящий и водоподводящий патрубки, соединительную арматуру, шланги, сливные краники и др. (рисунок 1.1).
1 – пробка радиатора; 2– радиатор; 3 – водоподводящий патрубок; 4 – термостат; 5 – термометр; 6 – водяной насос; 7 – водоотводящий патрубок; 8 –вентилятор; 9 – шторка;
10 – краник слива воды из радиатора
Рисунок 1.1 – Схема системы охлаждения двигателя Д-243
Для создания активного воздушного потока применяется вентилятор, обдувающий сердцевины водяного и масляного радиатора, а также охлаждающий наружную поверхность двигателя. Вентилятор размещается в едином узле с водяной помпой и находится на ее валу. При помощи шести болтов вентилятор крепится к шкиву насоса, а весь комплекс (водяной насос-вентилятор) присоединен болтами к верхней части передней стороны блока цилиндров. Кожух вентилятора крепится с задней стороны к стойкам водяного радиатора и служит для защиты вентилятора от посторонних предметов, а также для направления потока воздуха к двигателю.
Водяной насос двигателя Д-243 (240-1307010-А) центробежного типа предназначен для образования интенсивной циркуляции жидкости в системе охлаждения и, при помощи этого, более эффективного отвода тепла от нагретых компонентов двигателя. Крыльчатка водяного насоса смонтирована на валик и закреплена от проворачивания при помощи лыски. Она крепится на валике торцевым болтом. Два шариковых подшипника дают возможность вращаться валику вместе с крыльчаткой. Объем в корпусе между подшипниками наполняется смазкой при помощи масленки. Масляная и водяная полости помпы разделяются друг от друга дополнительным торцевым уплотнением, размещенным в крыльчатке. Уплотнение представляет собой текстолитовую шайбу, которая контактирует с хорошо обработанным торцом упорной втулки, запрессованная в корпус помпы, а также резиновую манжету, окружающая валик и поджимающая пружины.
Крыльчатка размещается в профилированной полости корпуса водяного насоса. Во время вращения крыльчатки на входе в данную полость образуется разрежение, передающееся в приемную камеру, соединенная патрубком с нижним бачком радиатора. При помощи разряжения, жидкость подается на лопасти крыльчатки и под давлением подается в спиральный канал, называемый улиткой, охватывающий крыльчатку в корпусе насоса. Далее жидкость нагнетается в продольный канал системы охлаждения двигателя.
Водяной насос дизеля и вентилятор совершают вращения от шкива коленчатого вала двигателя, используя клиновидный ремень, вращающий помимо ее еще и ротор генератора. При номинальных оборотах двигателя (2200 мин-1) вентилятор и помпа развивают 2600 мин-1.
Работоспособность системы охлаждения зависит от количества жидкости, степени изношенности лопастей крыльчатки и стенок насоса, натяжения ремней привода вентилятора, состояния сердцевины радиатора и других причин.
Количество жидкости в системе охлаждения двигателя может уменьшаться в результате негерметичности соединений, нарушения регулировок паровоздушного клапана, разрушения уплотнений водяного насоса.
Потеря охлаждающей жидкости приводит к перегреву деталей головки цилиндров, выходу из строя уплотнений стаканов форсунок, гильз цилиндров, прогоранию прокладок головки цилиндров и др. Появление значительного зазора в подшипниках или его разрушение может привести к повреждению сердцевины радиатора крыльчаткой вентилятора.
Выделение обильного количества пара, течь воды или масла из дренажного отверстия, повышенный шум и стуки указывают на неисправность системы охлаждения двигателя, в частности на неисправность водяного насоса (рисунок 1.2).
Появление значительного зазора в подшипнике или разрушение подшипника могут привести к повреждению сердцевины радиатора крыльчаткой вентилятора.
Повышенный шум и стуки указывают на предельный износ или разрушение подшипников насоса, ослабление посадочного места валика под приводной шкив.
Течь охлаждающей жидкости из дренажного отверстия или следы масла на шкиве привода свидетельствуют о разрушении уплотнений валика насоса.
При появлении неисправностей снимают водяной насос и разбирают для замены изношенных деталей.
1 – шкив; 2 – подшипники; 3 – корпус; 4 – крыльчатка; 5 – дренажное отверстие;
6 – валик; 7 – гайка
Рисунок 1.2 – Водяной насос в сборе
Если осевое перемещение валика в подшипниках превышает 0,6 мм или наблюдается ослабление внутренних колец подшипников на валике, то валик заменяют в сборе с подшипниками. При радиальном зазоре в подшипниках, превышающем 0,1 мм, подшипники заменяют. На уплотняющей шайбе торцового уплотнения допускаются кольцевые риски и следы износа глубиной не более 0,5 мм. Толщина шайбы должна быть не менее 2,5 мм. Манжета не должна иметь сквозных прорывов.
При наличии трещин корпус водяного насоса его выбраковывают. Если трещины отсутствуют, измеряют посадочные поверхности корпуса под подшипники валика и результаты сравнивают с допустимыми значениями (таблица 1.1).
Если на торцовой поверхности опорной втулки корпуса насоса имеются следы износа (кольцевые канавки) глубиной более 0,5 мм, то втулку выпрессовывают и заменяют новой.
Таблица 1.1 – Номинальные и допустимые размеры водяного насоса дизеля Д-243
Расстояние от торца опорной втулки до плоскости разъема, мм: | |
номинальное | 47,0–47,3 |
допустимое | 48,5 |
Допустимый диаметр отверстий корпуса под подшипники, мм: | |
305 | 62,07 |
304 | 52,06 |
При оборке насоса резиновые манжеты устанавливают так, чтобы отвороты с пружинами были обращены в сторону шарикоподшипников. Гайка ступицы должна быть затянута моментом 16–19 Н·м. После сборки насоса валик должен вращаться от усилия руки без заеданий крыльчатки. Концы кромок лопастей вентилятора должны находиться в одной плоскости.
2 Разработка структурной схемы разборки и маршрута доступа к ремонтируемой детали
При появлении неисправностей, приведенных в разделе 1, водяной насос снимают с двигателя для замены изношенных деталей.
Разработку технологического процесса разборки рекомендуется осуществлять в следующей последовательности [2]:
– проводится анализ конструкции, неисправностей и ремонтной технологичности сборочной единицы;
– разрабатывается структурная схема разборки с выделением последовательности выполнения операций и определением технических требований на их выполнение;
– разрабатываются технологические операции с определением их содержания, выбором технологического оборудования и оснастки, расчетом режимов и норм времени;
– оформляется технологический процесс комплектом документов на технологический процесс разборки;
Структурная схема разборки представляет собой графическое изображение условными обозначениями очередности снятия сборочных единиц и деталей при разборке ремонтируемого объекта. При этом различают укрупненную и развернутую схемы.
На укрупненной схеме показывается последовательность снятия только сборочных единиц, а на развернутой – всех составных частей (сборочных единиц и деталей).
Сборочные единицы, входящие в состав изделия, при разборке структурных схем, называют разборочными группами и подгруппами. Сборочная единица, входящая непосредственно в состав изделия, называется группой, а сборочные единицы, входящие в состав группы – подгруппами.
Различают подгруппы 1-го, 2-го и более высоких порядков. Подгруппа 1-го порядка входит в состав группы, подгруппа 2-го порядка входит в состав подгруппы 1-го порядка и т. д.
Разборочные (сборочные) группы обозначаются в структурных схемах индексами Рб-1, Рб-2, Сб-1, Сб-2, а подгруппы – Рб-1-1, Рб-1-2, Рб-2-1, Рб-2-2, Сб-1-1, Сб-1-2, Сб-2-1,Сб-2-2 или обозначением по каталогу деталей и сборочных единиц, состоящим из комбинации цифр и букв (50-1701040, 48-1701030-А).
При разработке схем разборки следует придерживаться следующих основных принципов:
– схема должна строиться в направлении слева направо или сверху вниз с условных обозначений сборочных единиц, групп, подгрупп и деталей;
– число групп и подгрупп должно быть максимальным;
– схема разборки начинается условным обозначением сборочной единицы и заканчивается условным обозначением базовой детали;
– схема сборки – наоборот: начинается с базовой детали и заканчивается сборочной единицей;
– разборка разборочных групп и подгрупп должна аналогично заканчиваться базовой деталью группы или подгруппы;
– сборка сборочных групп и подгрупп начинается также с базовой детали;
– детали изображаются на схемах с учетом очередности их снятия или установки.
Демонтаж отказавшего водяного насоса с двигателя необходимо осуществлять в следующей последовательности (рисунок 1.1)
– очистить двигатель от пыли и грязи, слить воду из системы охлаждения двигателя;
– отвернуть болты крепления правого и левого кронштейнов фар;
– кронштейны в сборе с фарами и подфарниками уложить на переднюю ось и поперечную рулевую тягу;
– отвернуть болты крепления и снять правую и левую боковины облицовки радиатора;
– отвернуть болты крепления кронштейна генератора и болт крепления регулировочной планки к водяному насосу, уложить генератор на выхлопной коллектор;
– отвернуть винты крепления и отсоединить правую соединительную панель от кожуха вентилятора;
– отвернуть болты крепления кожуха вентилятора;
– отсоединить гибкий вал тахоспидометра от редуктора привода;
– отвернуть болты крепления и отсоединить воздухоподводящую трубу компрессора от патрубка впускного коллектора;
– отсоединить от компрессора воздухоотводящую трубу пневмосистемы;
– отвернуть гайки крепления и снять компрессор;
– отвернуть болты крепления и отсоединить патрубок от водяного насоса;
– отвернуть болты крепления водяного насоса; вывести ремень из ручья шкива коленчатого вала;
– переместить кожух вентилятора вначале назад (на 50 мм), а затем вправо вдоль радиатора (на 250 мм);
– переместить вправо вдоль радиатора водяной насос в сборе с ремнем и вентилятором;
– небольшим поворотом вентилятора вправо и назад полностью извлечь насос с вентилятором наружу;
– снять ремень со шкива водяного насоса;
– отвернуть болты крепления и снять вентилятор.
1 – шкив; 2 – подшипники; 3 – крыльчатка; 4 – корпус; 5 – патрубок; 6 – валик насоса;
7 – ремень привода водяного насоса; 8 – стопорная пластина; 9 – гайка; 10 – вентилятор
Рисунок 1.3 – Взаимное расположение деталей водяного насоса Д-243 трактора МТЗ-80/82
Разборку водяного насоса целесообразно осуществлять в приведенной ниже последовательности (рисунки 1.4–1.9):
1) отогнуть стопорную пластину 3 и отвернуть гайку 1;
1 – гайка; 2 – шкив; 3– стопорная пластина
Рисунок 1.4 – Шкив водяного насоса
2) спрессовать шкив 1;
1 – шкив; 2 – двухлапчатый съемник
Рисунок 1.5 – Спрессовка шкива водяного насоса Д-243
3) снять стопорное кольцо подшипника;
Рисунок 1.6 – Снятие стопорного кольца подшипника
4) отвернуть болт 3 крепления крыльчатки 2 водяного насоса;
1 – корпус водяного насоса; 2 – крыльчатка; 3 – болт.
Рисунок 1.7 – Отворачивание болта крепления крыльчатки водяного насоса Д-243
5) выпрессовать валик насоса при помощи выколотки 2;
1– корпус водяного насоса; 2 – выколотка; 3 – крыльчатка
Рисунок 1.8 – Выпрессовка валика водяного насоса Д-243
6) спрессовать подшипники с валика насоса.
1 – подшипник; 2 – валик водяного насоса; 3 – шток пресса
Рисунок 1.9 – Спрессовка подшипника с валика водяного насоса Д-243
Структурная схема разборки водяного насоса 240-1307010-А представлена на первом листе формата А1 графической части курсового проекта.
3 Разработка технологического процесса очистки (мойки) детали
Дата добавления: 2018-11-24; просмотров: 472; Мы поможем в написании вашей работы! |
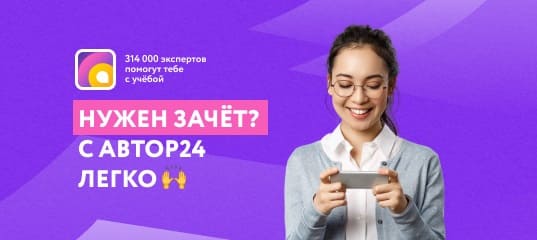
Мы поможем в написании ваших работ!