Основные характеристики способов восстановления и упрочнения деталей представлены в таблице 3.1.
Таблица 3.1 – Технологические и технические характеристики способов восстановления деталей (для учебных целей)
Группы способов восстановления сущности | Технологическая характеристика | Техническая характеристика | Удельная трудоемкость восстановления, ч/м2 | Удельная себестоимость восстановления, тыс. руб./м2 | Удельный расход материала, кг/м2 | Удельная энергоемкость, кВт · ч/м2 | |||||||||||
Dmin восстанавливаемой поверхности, мм | Толщина наращивания, мм | Коэффициенты | Микротвердость, кг/мм2 | ||||||||||||||
наружный | внутренний | Минимум | Максимум | износостойкости (Ки) | выносливости (Кв) | сцепляемости (Кс) | долговечности (Кд) | ||||||||||
1 | 2 | 3 | 4 | 5 | 6 | 7 | 8 | 9 | 10 | 11 | 12 | 13 | |||||
Обработка под ремонтный размер | Неограничен | – | – | 0,8–1,0 | 0,9–1,0 | 1,0 | 0,72–1,0 | Ном. | 10–23 | 8,7–12,3 | – | – | |||||
Установка дополнительной детали | Неограничен | – | – | 1,0 | 0,8 | 1,0 | 0,8 | Ном. | 48–65 | 39,5–76,5 | 31–55 | – | |||||
Пластическое деформирование | – | – | До номинала | 2,0 | 1,0 | 1,0 | 1,0 | Ном. | 10–25 | 8,7 | – | – | |||||
Электромеханическая высадка | 15–18 | Неогран. | Неогран. | 3,0 | 2,0 | 1,25 | 1,0 | 2,5 | 320–650 | 10,8 | 5,3 | – | – | ||||
Полимерные материалы | Неогран. | – | – | 0,15 | 1,0–2,0 | – | 0,7–1,0 | 0,7–2,0 | 300–650 | 15,9 | 7,3–7,6 | 4,7 | – | ||||
Вибродуговая наплавка | |||||||||||||||||
в жидкой среде | 15–18 | 45 | 0,5 | 3,0 | 0,85 | 0,62 | 0,75–1,0 | 0,4–0,53 | 225–500 | 33,3–36,0 | 18,6–19,0 | 35–40 | 234 | ||||
под флюсом | 40–50
| – | 0,5 | 4,0 | 0,85 | 0,62 | 0,9–1,0 | 0,48–0,53 | 450–600 | 33,3–36,0 | 18,6–19,0 | 39–50 | 234 | ||||
в среде СО2 | 15–18 | 45 | 1,0 | 3,0 | 1,15 | 0,9 | 0,8–1,0 | 0,8–1,0 | 500–600 | 33,3–36,0 | 18,8–19,3 | 35–40 | 234 | ||||
в воздушной среде | 15–18 | 45 | 1,0 | 3,0 | 0,85 | 0,62 | 0,9–1,0 | 0,48–0,53 | 325–450 | 33,3–36,0 | 18,6–19,0 | 35–40 | 234 | ||||
с термомеханической обработкой | 15–18 | 45 | 0,5 | 3,0 | 2,0 | 0,95 | 0,9–1,0 | 1,72–1,9 | 450–550 | 34,0–37,0 | 19,6–20,2 | 35–40 | 234 | ||||
Наплавка в среде защитных газов | |||||||||||||||||
в среде СО2 | 10–12 | 45 | 0,8 | 3,0 | 1,3–1,6 | 0,7 | 1,0 | 0,9–1,0 | 230–360 | 17,3–21,4 | 8,8–12,0 | 31–45 | 256 | ||||
в среде СО2 + аргон | – | 45 | 1,0 | 3,0 | 1,3–1,6 | 0,85 | 1,0 | 1,1–1,6 | 320–340 | 14,4–17,5 | 7,0–10,4 | 30–45 | 256 | ||||
Автоматическая наплавка под флюсом | |||||||||||||||||
плавленым | 44–55 | 250 | 1,5–2,0 | 3,0–4,0 | 0,91 | 0,6–1,0 | 1,0 | 0,55–0,91 | 400–600 | 21,3–24,0 | 10,8–13,2 | 38–51 | 286 | ||||
керамическим | 44–55 | 250 | 1,5–2,0 | 3,0–4,0 | 0,95 | 0,85 | 1,0 | 0,81 | 500–600 | 21,3–24,0 | 10,8–13,2 | 39–52 | 286 | ||||
Продолжение таблицы 5.1 | |||||||||||||||||
1 | 2
| 3 | 4 | 5 | 6 | 7 | 8 | 9 | 10 | 11 | 12 | 13 | |||||
порошковой проволокой | 44–55 | 250 | 1,5–2,0 | 3,0–4,0 | 0,92 | 0,85 | 1,0 | 0,8 | 560–800 | 21,3–24,0 | 10,8–13,2 | 38–51 | 286 | ||||
с термомеханической обработкой | 44–55 | 250 | 1,5–2,0 | 3,0–4,0 | 1,4–1,8 | 1,2–1,5 | 1,0 | 1,7–2,7 | 500–800 | 21,3–24,0 | 10,8–13,2 | 38–48 | 286 | ||||
Ручная наплавка
| |||||||||||||||||
Дуговая | 40–50 | 120 | 1,5 | 5,0–6,0 | 0,7 | 0,6 | 1,0 | 0,42 | 200–400 | 34,6 | 18,5–23,5 | 48–57 | 580 | ||||
Газовая | 10–12 | 120 | 1,0 | 3,0–4,0 | 0,7 | 0,7 | 1,0 | 0,5 | 200–600 | 37,0 | 20,7–22,5 | 38–51 | 580 | ||||
Аргонно-дуговая | 10–12 | 120 | 1,0 | 4,0–5,0 | 0,7 | 0,7 | 1,0 | 0,5 | 250 | 29,4 | 16,2–17,8 | 36 | 520 | ||||
Электрофизические способы | |||||||||||||||||
Электроконтактная приварка ленты | 10 | 70 | 0,1 | 1,5 | 1,0–2,3 | 0,7–1,0 | 0,7–0,8 | 0,5–1,8 | 300–800 | 22–24 | 8,4–11,2 | 3,5–15,6 | 100–110 | ||||
Электроискровая обработка | – | – | 0,01 | 0,5–1,0 | 2,0 | 0,9 | 1,0 | 0,9–2,1 | 2040 | 16,7–22,2 | 9,8–14,2 | 30 | 220 | ||||
Металлизация | |||||||||||||||||
Плазменная | 10–12 | – | 0,03 | 15,0 | 1,1–1,3 | 0,7–1,3 | 0,4–0,5 | 0,31–0,86 | 310–395 | 22,7–24,0 | 11,4–13,5 | 16–24 | 117–175 | ||||
Газопламенная | – | – | 0,4 | 15,0 | 1,1–1,3 | 0,6–1,1 | 0,3–0,4 | 0,20–0,57 | 310–395 | 22,7–24,0 | 11,4–13,5 | 16–24 | 117–175 | ||||
Электродуговая | – | – | 0,4 | 15,0 | 1,1–1,3 | 0,6–1,1 | 0,2–0,3 | 0,13–0,40 | 300–600 | 22,7–24,0 | 11,4–13,5 | 16–24 | 117–175 | ||||
Железнение | |||||||||||||||||
Вневанное (местное) | Неогран. | 40–50 | Неогран. | 0,6 | 0,9–1,3 | 0,8 | 0,65–0,80 | 0,50–0,83 | 300–600 | 26,0–33,0 | 17,3–22,4 | 4,7–8,4 | 80–220 | ||||
Ванное | – | – | – | 2,0 | 0,95–1,30 | 0,88 | 0,7–0,9 | 0,6–1,0 | 300–680 | 15,0–17,0 | 8,3–9,7 | 4,7–9,4 | 80–220 | ||||
Проточное | – | – | – | 0,8 | 1,0–1,6 | 0,8 | 0,75–1,00 | 0,60–1,25
| 300–680 | 20,0–25,0 | 12,6–14,3 | 4,7–9,4 | 80–220 | ||||
Хромирование | |||||||||||||||||
в обычном электролите | – | 40–50 | – | 0,3 | 1,67 | 0,55–0,90 | 0,9 | 0,90–1,35 | 800–1200 | 72–129 | 30,8–43,7 | 1,5–4,5 | 220–600 | ||||
в саморегулирующем холодном электролите | – | – | – | 1,0 | 2,0–4,0 | 0,88–0,95 | 1,0 | 1,6–3,8 | 800–1320 | 44–61 | 33,6–44,8 | 1,5 | 100–300 | ||||
Критерий долговечности оценивает технические возможности детали, восстановленной каждым из намеченных по технологическому критерию (Кт) способом, т. е. этот критерий оценивает эксплуатационные свойства детали в зависимости от способа ее восстановления. При этом оценка проводится по следующим основным показателям:
1) сцепляемости;
2) износостойкости;
3) выносливости (усталостной прочности);
4) микротвердости.
По результатам оценки исключаются из числа ранее назначенных те способы устранения дефекта, которые не обеспечивают выполнения технических требований на восстановленную деталь хотя бы по одному из показателей.
В общем случае коэффициент долговечности Кд является функцией трех переменных:
Кд = f (Ки, Кв, Кс), (3.4)
|
|
где Ки, Кви Кс– соответственно, коэффициенты износостойкости, выносливости и сцепляемости покрытий.
Для каждого выбранного способа дается комплексная качественная оценка по значению коэффициента долговечности Кд, определяемому по формуле
Кд = f (Ки × Кв × Кс × Кп), (3.5)
где Кп– поправочный коэффициент, учитывающий фактическую работоспособность восстановленной детали в условиях эксплуатации (Кп = 0,8–0,9).
По физическому смыслу коэффициент долговечности пропорционален сроку службы деталей в эксплуатации. Следовательно, рациональным по этому критерию будет тот способ, у которого Кд максимален (Кд → max).
Численные значения коэффициентов-аргументов Ки, Кв определяются на основании стендовых и эксплуатационных испытаний новых и восстановленных деталей.
Примерные значения коэффициента сцепляемости Кс, определенные по результатам исследований для наиболее распространенных методов восстановления, представлены в таблице 3.1.
Так, при выборе способа наплавки применительно к деталям, не испытывающим в процессе работы значительных динамических и знакопеременных нагрузок, значение коэффициента долговечности Кд определяется только численным значением коэффициента износостойкости Ки, а для деталей, работающих в условиях динамических нагрузок, решающим признаком может оказаться коэффициент выносливости Кв. Для деталей, восстановленных методами электролитического осаждения металлов, газотермического напыления, а также работающими в условиях динамических нагрузок, решающим признаком может оказаться коэффициент сцепляемости Кс.
Из числа способов, отобранных по технологическому критерию, к дальнейшему анализу принимаются те, которые обеспечивают коэффициент долговечности восстановленных поверхностей не менее 0,8. Это обусловлено тем, что ресурс капитально отремонтированной машины или агрегата не должен быть менее 80 % ресурса новой машины (агрегата). Указанное обстоятельство предполагает также, что ресурс восстановленной детали в капитально отремонтированном агрегате тем более не должен быть ниже 80 % ресурса новой детали.
По физическому смыслу коэффициент долговечности пропорционален сроку службы деталей в эксплуатации. Следовательно, рациональным по этому критерию будет тот способ, у которого Кд максимален (Кд → max).
Если установлено, что требуемому значению коэффициента долговечности для данной поверхности детали соответствуют два или несколько способов восстановления, то на этом этапе оценка способов производится по технико-экономическому (обобщенному) критерию, позволяющему принять окончательное решение о выборе рационального способа устранения дефекта детали. Данный критерий отражает технический уровень применяемой технологии и связывает экономический показатель восстановления детали с ее долговечностью.
По каждому из оставленных после оценки по техническому критерию способов устранения дефектов определяется коэффициент технико-экономической эффективности Кт.э.:
(3.7)
или
(3.8)
где Свi – себестоимость восстановления (устранения дефекта) детали i-м способом или i-го способа упрочнения детали, руб.;
КДi – коэффициент долговечности восстановленной детали i-м способом;
Ен– нормативный коэффициент эффективности капитальных вложений (Ен = 0,15);
Кудi – удельные капитальные вложения при восстановлении детали i-м способом, руб./м2.
Себестоимость восстановления детали Свi определяется по формуле:
(3.9)
где Сзi – часовая заработная плата производственных рабочих при восстановле-нии детали i-м способом, руб.;
q – коэффициент, учитывающий начисления на заработную плату;
Смчi – стоимость 1 машино-часа работы оборудования при восстановлении детали i-м способом, руб.;
Топi – время, затрачиваемое на восстановление детали i-м способом, ч.
При обосновании способов восстановления (в учебных целях) значение себестоимости Свi можно определить из выражения:
(3.10)
где Суi – удельная себестоимость восстановления i-м способом, руб./м2 (примерные значения Суi приведены в табл. 3.1);
Si – площадь восстанавливаемой поверхности детали, м2.
Предпочтение отдается тому из способов восстановления (устранения дефекта), для которого отношение (3.7) или (3.8) имеет наименьшее значение (Кт.э → min).
При оценке существующих или разрабатываемых технологий наряду с основными производственными показателями необходимо учитывать их влияние на окружающую среду, расход материальных, а также энергетических ресурсов.
Для принятия решения о выборе рационального способа устранения дефекта на данном этапе учитывается энергетический критерий. Все технологии дополнительно необходимо оценивать таким показателем, который, не подменяя собой стоимостных показателей, корректировал бы их, достоверно отражая все затраты на производство продукции. По мнению многих специалистов, к такому показателю можно отнести затраты энергии.
Энергетический критерий Кэможно выразить уравнением
(3.11)
где К1i и К2i – соответственно, коэффициенты энергоемкости и трудоемкости технологического процесса восстановления детали i-м способом;
КДi – коэффициент долговечности детали, восстановленной i-м способом.
(3.12)
(3.13)
где Qвi – удельные затраты энергии на восстановление детали i-м способом по всему циклу производства, кВт×ч/ед. наработки;
Qн – удельные затраты энергии на изготовление новой детали, кВт·ч/ед. наработки;
Твi – трудоемкость восстановления детали i-м способом, чел.-ч;
Тн – трудоемкость изготовления новой детали, чел.-ч.
Способ, который обеспечивает минимальное значение энергетического критерия – рациональный. При этом восстановление деталей таким способом целесообразно и тогда, когда его значение меньше единицы (Кэ < 1,0).
Энергетический критерий необходимо использовать тогда, когда принимаются решения о развитии нового производства, строительстве завода или крупного цеха восстановления деталей и др.
Выбранный по энергетическому критерию способ из-за воздействия цен (в основном, их роста) на энергоносители, не всегда может отвечать экономическим требованиям предприятий технического сервиса. В настоящее время экологичность инженерных решений является одним из главных критериев их прогрессивности.
В этой связи для учета экономических интересов конкретного предприятия окончательный выбор способа и оптимизацию технологического процесса восстановления деталей целесообразно проводить по комплексному (обобщенному) критерию, отражающему удельные затраты, энергоемкость, коэффициенты долговечности и экологичности:
(3.14)
где К3i и К4i – соответственно, коэффициенты энергоемкости и трудоемкости работ по обеспечению экологической безопасности технологического процесса.
(3.15)
(3.16)
где Qэi – удельные затраты на экологические мероприятия при восстановлении детали i-м способом, кВт×ч/ед. наработки;
Qэн – удельные затраты на экологические мероприятия при изготовлении новой детали, кВт×ч/ед. наработки;
Тэi – трудоемкость экологической безопасности при восстановлении детали i-м способом, чел.-ч;
Тэн – трудоемкость экологической безопасности при изготовлении новой детали, чел.-ч.
Деталь восстанавливать экономически целесообразно, если Gк < 1,0.
При определении коэффициентов, входящих в выражение (3.14), вместо показателей новой детали за базу для сравнения, как правило, принимаются показатели одного из наиболее прогрессивных способов восстановления. В этом случае коэффициент долговечности определяется по уравнениям:
(3.17)
или
(3.18)
где Т i и Тб – ресурсы деталей, восстановленных соответственно i-м и базовым способами;
Кдi и Кдб – коэффициенты долговечности деталей, восстановленных соответственно i-м и базовым способами, в сравнении с новой деталью.
Учитывая необходимость наличия обширной информации для оценки способов восстановления дефектов деталей по приведенным выше критериям, при выполнении курсового проекта рекомендуется использовать технологический (применяемости), технический (долговечности) и технико- экономический (обобщающий) критерии.
Установив рациональный способ устранения дефектов (группы дефектов) и мер, повышающих механические свойства восстановленной детали, необходимо выполнить ремонтный чертеж детали.
Исходными данными для разработки ремонтного чертежа являются: рабочий чертеж детали; технические требования на дефектацию детали; данные по выбору рациональных способов устранения дефектов; технические требования на восстановленную деталь (технические требования на новую деталь и дополнительные технические требования на восстановленную деталь).
При восстановлении деталей операции технологического процесса назначаются в следующем порядке:
– в первую очередь выполняются подготовительные операции (очистка, обезжиривание, правка, восстановление базовых поверхностей);
– механическая обработка, которая предназначена для устранения дефектов, образовавшихся в процессе эксплуатации, или придания правильной геометрической формы изношенным поверхностям, в том числе специальной (например, при электродуговом напылении – нарезка «рваной» резьбы, фрезерование канавок и т.п.);
– наращивание изношенных поверхностей (наплавка, напыление и пр.). При этом в первую очередь выполняют операции, при которых детали нагревают до высокой температуры (сварка, наплавка, термическая обработка). Если необходимо, то детали подвергают вторичной правке. Затем выполняют операции, не требующие нагрева деталей (хромирование, железнение и др.);
– окончательная обработка (токарная, фрезерная, слесарная и др.);
– контрольные операции назначают в конце технологического процесса и после выполнения наиболее ответственных операций.
Средства технологического оснащения включают:
– технологическое оборудование (в том числе контрольное и испытательное);
– технологическую оснастку (в том числе инструменты и средства контроля);
– средства механизации и автоматизации производственных процессов.
Выбор технологического оборудования производится исходя из следующих основных условий:
1) возможность формирования требуемого качества поверхностей деталей;
2) возможность выполнения технических требований, которые предъявляются к детали;
3) соответствие основных размеров оборудования габаритным размерам детали;
4) обеспечение наиболее эффективных методов обработки поверхностей.
Выбор технологической оснастки производится на основании анализа возможности реализации технологического процесса при выполнении технических требований к детали, технических возможностей технологической оснастки, а также конструктивных характеристик детали (габаритные размеры, материал, точность и т. д.) и организационно-технологических условий ее ремонта (схема базирования и фиксации, вид технологической операции, организационная форма процесса ремонта и т. д.).
Точность обработки при восстановлении детали зависит от правильного выбора технологических баз, который требует четкого представления о функциональном назначении поверхностей детали, размерной взаимосвязи между ними, их состоянии.
Технологической базой называется поверхность, сочетание поверхностей, ось или точка, используемые для определения положения детали в процессе обработки.
Технологические базы обрабатываются с высокой точностью. При их выборе руководствуются следующими требованиями:
– при наличии используются базы завода–изготовителя;
– по возможности совмещаются технологические и конструкторские базы;
– точность изготовления базовых поверхностей должна быть не ниже точности изготовления восстанавливаемых поверхностей;
– базовые поверхности обрабатываются или изготавливаются в первую очередь после восстановления формы и целостности детали;
– поверхности, для которых необходимо обеспечить точность относительного положения (соосность, перпендикулярность, параллельность осей), обрабатываются с одной установки;
– принятая технологическая база должна по возможности применяться на всех операциях технологического процесса, а если это невозможно, то за следующую базу необходимо принимать обработанную поверхность детали, размерно связанную непосредственно с обрабатываемой.
В зависимости от конфигурации детали, характера и величины износа поверхностей рекомендуются следующие схемы базирования:
– деталь базируется по сохранившейся базе, используемой при ее изготовлении;
– деталь базируется по неизношенным точно изготовленным поверхностям;
– деталь первоначально базируется по мало- или неизношенным поверхностям для правки существующих или изготовления новых технологических баз, с последующим базированием по ним.
Основными базовыми поверхностями являются фаски центровых отверстий валов, привалочные плоскости и технологические отверстия корпусных деталей.
Детали базируются на операциях обработки в основном с помощью следующих средств:
– патронов самоцентрирующихся трехкулачковых (ГОСТ 2675–80);
– патронов токарных поводковых (ГОСТ 2571–71);
– оправок (ГОСТ: 16211–86, 16212–70, 16213–70, 18438–73, 18439–73, 18440–80);
– тисков станочных (ГОСТ 14904–80);
– центров станочных вращающихся (ГОСТ 8742–85);
– центров станочных упорных (ГОСТ 13214–79);
– хомутиков поводковых для токарных и фрезерных работ (ГОСТ 2578–70);
– хомутиков поводковых для шлифовальных работ (ГОСТ 16488–72).
Средства базирования графически обозначаются в технологических документах по ГОСТ 3.1107.
При разработке технологического маршрута определяют последовательность выполнения технологических операций, основное оборудование и руководствуются следующими правилами:
– в первую очередь выполняют операции, вызывающие изменение физико-механических свойств и формы детали, возникновение остаточных напряжений (сварка, наплавка, заварка пазов);
– затем предусматривают операции, устраняющие отрицательное влияние энергетических воздействий (правка, термообработка);
– для валов, при отсутствии их изгиба, первыми выполняются операции по восстановлению или изготовлению базовых поверхностей;
– перед нанесением тонких покрытий выполняют операции по удалению дефектных слоев металла, приданию правильной формы (цилиндричность, прямолинейность и т. д.), обеспечению эксплуатационной толщины покрытия и созданию необходимой шероховатости;
– в случае возникновения необходимости обеспечения высокой твердости поверхности термической обработкой последовательность выполнения операций следующая: черновая механическая, термическая, чистовая механическая обработка;
– при изготовлении шпоночных пазов последовательность выполнения операций следующая: черновая механическая обработка цилиндрической поверхности, изготовление шпоночного паза, чистовая механическая обработка цилиндрической поверхности;
– при изготовлении точных отверстий осевым инструментом полная последовательность выполнения операций следующая: сверление (рассверливание), зенкерование, зенкование фасок, развертывание;
– вспомогательные поверхности (фаски, проточки) изготавливаются перед чистовой обработкой основных поверхностей;
– легкоповреждаемые и точные поверхности обрабатываются в конце маршрута;
– перед наплавкой радиальные отверстия под шплинты на резьбовых концах валов должны быть заглушены вставками из токопроводящих материалов;
– для корпусных деталей операции по восстановлению базовых поверхностей выполняются после восстановления целостности и формы детали (заделки трещин, пробоин и т. д.) перед механической обработкой точных отверстий (посадочных мест под подшипники, валики, оси).
Технологический маршрут описывается действиями с указанием поверхностей, номеров дефектов и основных исполнительных размеров.
Образец описания технологического маршрута восстановления детали: править фаски центровых отверстий; заварить шпоночный паз (Деф. 2); править вал; шлифовать поверхность (Деф. 1) до Ø49,6 мм; приварить ленту электроконтактным способом на поверхность (Деф. 1) до Ø50,4 мм; точить фаску 2×45º и проточку и т. д.
При разработке операций технологического процесса восстановления детали решаются следующие задачи:
– выбор основного оборудования;
– выбор вспомогательных материалов (сварочных, наплавочных и т. д.);
– формирование содержания и последовательности переходов;
– выбор средств технологического оснащения: приспособлений, вспомогательного, режущего, слесарно-монтажного, специального инструмента и средств измерений;
– назначение и расчет технологических режимов и норм времени.
Разработку технологических операций производят, используя литературные источники [3–6, 8–17].
При выборе основного оборудования учитывается:
– вид обработки;
– требуемая точность обработки поверхностей;
– габаритные размеры и масса детали;
– принятая схема базирования;
– экономичность выполнения операции.
При выборе вспомогательных материалов (сварочных, наплавочных проволок, лент и т. д.) учитываются требования к физико-механическим свойствам (твердости, износостойкости) восстанавливаемых поверхностей.
Выбор средств технологического оснащения производится в зависимости от геометрический размеров детали, точности ее установки, физико-механических свойств поверхностей (твердости, пределов прочности), точности обработки и контроля.
Порядок разработки и описания технологической операции:
– номер и наименование;
– выбор основного оборудования (наименование и обозначение);
– выбор вспомогательных материалов (проволок, лент, электролитов и т. д.);
– определение содержания вспомогательного перехода (при его наличии);
– выбор технологического оснащения вспомогательного перехода;
– определение вспомогательного времени на установку и закрепление детали;
– определение содержания технологического перехода с указанием исполнительных размеров и технических требований на его выполнение;
– выбор технологического оснащения технологического перехода;
– назначение и расчет технологических режимов и норм времени (основного и вспомогательного);
– обоснование подготовительно-заключительного времени на выполнение операции;
– расчет штучного времени.
При назначении режимов выполнения операций по восстановлению деталей необходимо пользоваться соответствующей учебной и справочной литературой. С особым вниманием необходимо назначать режимы операций по наращиванию поверхностей (наплавка, металлизация, хромирование, железнение и т. д.), так как режимы этих технологических процессов существенно влияют на физико-механические свойства и ресурс восстановленных деталей.
Выбранные режимы и материалы (например, марка наплавочной проволоки, флюсы и т. д.) должны обеспечивать выполнение технических требований к детали, изложенных на ремонтном чертеже.
При назначении видов и режимов механической обработки необходимо исходить из того, что изношенная поверхность в большинстве случаев имеет неравномерный износ, деформированные слои металла, подвергается химико-термической и механической упрочняющей обработке. Поэтому такие поверхности целесообразно обрабатывать шлифованием или точением резцами с пластинками твердого сплава или металлокерамики. При выборе режущего инструмента и режима обработки восстановленных поверхностей исходят из структуры и физико-механических свойств нанесенного металла.
Для предварительной обработки наплавленных поверхностей невысокой твердости (резание по корке наплавленных слоев, прерывистое сечение стружки, наличие ударных нагрузок) рекомендуется применять резцы с пластинками из сплава Т5К10. Наплавленные поверхности высокой твердости обрабатывают резцами из гексанита-Р и других сверхтвердых материалов. При обработке чугуна следует применять резцы с пластинками из твердого сплава ВК6, ВК8. Окончательную обработку наплавленных поверхностей, а также обработку поверхностей с гальваническими покрытиями выполняют шлифованием. В случае точения металлизированных поверхностей применяют резцы с пластинками ВК6.
При шлифовании в ремонтном производстве применяют круги из электрокорунда нормального (18А, 15А, 14А, 13А, 12АР), белого (25А, 24А, 23А) и монокорунда (45А, 44А, 43А). Предпочтение отдается кругам на бакелитовой основе, а при обработке профильных поверхностей твердости – на вулканитовой основе. Зернистость круга выбирается в зависимости от требуемой шероховатости обработанной поверхности. Обычно для черновой обработки применяются круги зернистостью 40–69, а для чистовой – зернистостью 16–25.
Для обработки твердых материалов следует принять мягкие и среднемягкие абразивные инструменты, а для обработки материалов повышенной твердости – более твердые. При шлифовании неровных, прерывистых поверхностей необходимо применять более твердые инструменты, чем при шлифовании ровных поверхностей. Для предварительных операций шлифования применяют более твердые круги, чем для чистовой операции. Поэтому для шлифования наплавленных поверхностей стальных деталей наиболее часто применяют круги средней твердости. Шлифование чугунных поверхностей производится кругами средней или среднемягкой твердости, а хромированных и железненных – кругами среднемягкими или мягкими с зернистостью 20–25.
Шлифование деталей, восстановленных хромированием, рекомендуется выполнять кругом из электрокорунда зернистостью 20–25 с мягкой связкой при следующих режимах: поперечная подача 0,002–0,005 мм/дв. ход стола, продольная подача 1–2 мм/об изделия, окружная скорость круга 30–35 м/с и детали 15–25 м/мин, подача охлаждающей жидкости 20–30 л/мин.
Для хонингования применяют бруски из электрокорунда (для чернового – зернистостью 40–60; для чистового – зернистостью 16–25) или алмазные (для чернового – АС12 или АС20, для чистового – АСМ28 или АСМ40).
Значительное преимущество для обработки наплавленных, хромированных и железненных поверхностей имеет применение новых синтетических сверхтвердых материалов (эльбор, гексанит-Р и др.). Особенно эффективен гексанит-Р, который хорошо обрабатывает твердые (закаленные, наплавленные и др.) поверхности, а также является ударостойким материалом.
Размер межоперационного припуска оказывает влияние на экономические показатели восстановления детали и точность ее обработки.
Автоматическая и полуавтоматическая наплавка под слоем флюса. Сила сварочного тока, Iсв (А), выбирается в зависимости от диаметров детали и электродной проволоки (таблица 3.2):
(3.19)
где D – диаметр детали, мм.
Таблица 3.2 – Зависимость силы тока от диаметра детали
Диаметр детали, мм | Сила тока (А) при диаметре электродной проволоки, мм | |
1,2–1,6 | 2,0–2,5 | |
50–60 65–75 80–100 150–200 250–300 | 120–140 150–170 180–200 230–250 270–300 | 140–160 180–220 230–280 300–350 350–380 |
Напряжение источника питания, В:
U = 21 + 0,04 · Iсв (3.20)
Коэффициент наплавки, г/(А·ч):
Кн = 2,3 + 0,065 (Iсв / d), (3.21)
где d – диаметр электродной проволоки, мм.
При наплавке постоянным током обратной полярности значение коэффициента наплавки принимается равным Кн = 11…14 г/(А·ч).
Скорость наплавки, м/ч:
(3.22)
где h – толщина наплавляемого слоя, мм;
S – шаг наплавки, мм/об;
γ – плотность электродной проволоки, г/см3 (γ = 7,85 г/см3).
Частота вращения детали, мин–1:
(3.23)
Скорость подачи электродной проволоки, м/ч:
(3.24)
Шаг наплавки, мм/об:
S = (2,0–2,5)·d (3.25)
Вылет электродной проволоки, мм:
H = (10–15)·d (3.26)
Смещение электродной проволоки, мм:
е = (0,05–0,07)·D (3.27)
Параметры режима наплавки подставляют в формулы (3.21)–(3.27) без изменения размерности.
Толщина наплавляемого слоя металла, мм, наносимого на наружные цилиндрические поверхности, определяется по следующей формуле:
(3.28)
где И – износ детали, мм;
t – припуск на механическую обработку после нанесения покрытия на сторону, мм (табл. 3.3);
t1 – припуск на механическую обработку перед наплавкой на сторону, мм. Принимается равным t1 = 0,1–0,3 мм.
В зависимости от необходимой твердости наплавленного слоя применяют следующие марки проволок и флюсов.
Наплавка проволоками Св-08А, Нп-30, Нп-40, Нп-60, Нп-30ХГСА под слоем флюсов (АН-348А, ОСЦ-45) обеспечивает твердость НВ 187…300. Использование керамических флюсов (АНК-18, ШСН) с указанными проволоками повышает твердость до 40–55 Н R Сэ (без термообработки).
Таблица 3.3 – Припуск на механическую обработку при восстановлении деталей различными способам
Способ восстановления | Минимальный односторонний припуск t, мм |
Ручная электродуговая наплавка | 1,4–1,7 |
Наплавка под слоем флюса | 0,8–1,1 |
Вибродуговая наплавка | 0,6–0,8 |
Наплавка в среде углекислого газа | 0,6–0,8 |
Плазменная наплавка | 0,4–0,6 |
Аргонно-дуговая наплавка | 0,4–0,6 |
Электроконтактная наплавка | 0,2–0,5 |
Газотермическое напыление | 0,2–0,6 |
Электродуговая металлизация | 0,2–0,4 |
Железнение | 0,10–0,21 |
Хромирование | 0,05–0,10 |
Вибродуговая наплавка.Режимы вибродуговой наплавки рассчитываются по следующим формулам:
– сила сварочного тока, (А)
(3.29)
где d – диаметр электродной проволоки, мм.
– скорость подачи электродной проволоки, м/ч
(3.30)
где U – напряжение источника питания, В (U = 12–25 В).
– скорость наплавки, м/ч
(3.31)
где – коэффициент перехода электродного материала в наплавленный металл (принимается равным
= 0,8–0,9);
h – заданная толщина наплавляемого слоя (без механической обработки), мм;
S – шаг наплавки, мм/об;
а – коэффициент, учитывающий отклонение фактической площади сечения наплавленного слоя от площади четырехугольника с высотой h (а = 0,7–0,85).
Между скоростью подачи электродной проволоки и скоростью наплавки существует оптимальное соотношение, при котором обеспечивается достаточно хорошее качество наплавки. Обычно Vн = (0,4–0,8) Vэ. С увеличением диаметра электродной проволоки до 2,5–3,0 мм Vн = (0,7–0,8) Vэ.
Частота вращения детали, мин-1
(3.32)
где D – диаметр детали, мм.
Шаг наплавки, мм/об
S = (1,6–2,2)·d (3.33)
Амплитуда колебаний электродной проволоки, мм
А = (0,75–1,0)·d (3.34)
Вылет электродной проволоки, мм
Н = (5–8)·d (3.35)
Индуктивность электрической цепи, Гн
(3.36)
где γ – плотность электродной проволоки, г/см3 (γ = 7,85 г/см3);
I – максимальная сила тока в цепи, А (принимается в два раза больше силы тока по амперметру);
f – частота колебаний, Гц.
Применяются следующие марки электродных проволок: Нп-65, Нп-80, Нп-30ХГСА и др. Полярность тока обратная.
Твердость наплавленного слоя зависит от химического состава электродной проволоки и количества охлаждающей жидкости. При наплавке проволокой Нп-60, Нп-80 (и другими) с охлаждением обеспечивается твердость 35–55 Н R Сэ. При наплавке низкоуглеродистой проволокой Св-08, Св-08Г2С и др. получают твердость поверхности 22–26 Н R Сэ.
Наплавка в среде углекислого газа.Сила тока, Iсв (А) выбирается в зависимости от диаметра проволоки и диаметра детали (таблица 3.4).
Скорость наплавки (Vн) частота вращения (n), скорость подачи электродной проволоки (Vэ), шаг наплавки (S), смещение электрода (е) определяются по тем же формулам, что и при механизированной электродуговой наплавке под слоем флюса.
Коэффициент наплавки при наплавке на обратной полярности Кн = 10–12 г/(А·ч), вылет электрода равен 8–15 мм. Расход углекислого газа составляет 8–20 л/мин. Наплавка осуществляется проволоками Нп-30ХГСА, Св-18ХГСА, Св-08Г2С, Св-12ГС, в состав которых должны обязательно входить раскислители – кремний и марганец.
Таблица 3.4. – Режимы наплавки в среде углекислого газа
Диаметр проволоки, мм | Диаметр детали, мм | Сила тока, А | Напряжение, В |
0,8–1,0 | 10–20 | 70–95 | 18–19 |
20–30 | 90–120 | 18–19 | |
30–40 | 110–140 | 18–19 | |
1,0–1,2 | 40–50 | 130–160 | 18–20 |
1,2–1,4 | 50–70 | 140–175 | 19–20 |
1,4–1,6 | 70–90 | 170–195 | 20–21 |
1,6–2,0 | 90–120 | 195–225 | 20–22 |
Твердость слоя, наплавленного низкоуглеродистой проволокой марки Св-08Г2С, Св-12ГС, составляет НВ 200–250, а проволоками с содержанием углерода более 0,3 % (30ХГСА и др.) после закалки – 50 Н R Сэ.
Плазменная наплавка
При плазменной наплавке расчет таких параметров режима, как скорость процесса, частота вращения детали, толщина покрытий рекомендуется выполнять по формулам, принятым для расчета режима механизированной электродуговой наплавки под слоем флюса.
Рациональное значение силы тока при плазменной наплавке находится в пределах 200–230 А. Коэффициент наплавки Кн = 10–13 г/(А·ч).
Расход порошка Q, г/с, определяется по формуле
Q = 0,1 · V · S · h · γ · Кп, (3.37)
где S – шаг наплавки, см /об (S = 0,4–0,5 см /об);
h – толщина наплавленного слоя, мм;
γ – плотность наплавленного металла, г/см3 (для порошковых твердых сплавов на железной основе γ = 7,4 г/см3; для сплавов на никелевой основе γ = 0,8 г/см3);
Кп – коэффициент, учитывающий потери порошка (Кп = 1,12–1,17).
Полярность тока прямая. Наплавка осуществляется на установках для плазменного напыления (УМП-6, УПУ-ЗД) и плазменной сварки (УПС-301), модернизированных под плазменную наплавку.
Электроконтактная приварка ленты
Частота вращения детали, продольная подача сварочных клещей и частота следования импульсов являются важными параметрами данного процесса, которые определяют его производительность. Соотношение этих величин подбирают так, чтобы обеспечить 6 или 7 сварных точек на 1 см длины сварного шва.
Рекомендуется следующий режим приварки ленты толщиной до 1 мм:
– сила сварочного тока – 16,1–18,1 кА;
– длительность сварочного цикла – 0,04–0,08 с;
– длительность паузы – 0,10–0,12 с;
– подача сварочных клещей – 3–4 мм/об;
– усилия сжатия электродов – 1,30–1,60 кН;
– ширина рабочей части сварочных роликов – 4 мм;
– скорость наплавки – 3–4 м/мин.
Частоту вращения детали при наплавке рассчитывают аналогично наплавке под слоем флюса.
При выборе материала ленты следует руководствоваться данными, приведенными в таблице 3.5.
Таблица 3.5 – Зависимость твердости наплавленного материала от марки стали
Марка стали | Твердость наплавленного слоя, HRCэ | Марка стали | Твердость наплавленного слоя, HRCэ |
Сталь 20 Сталь 40 Сталь 45 | 30–35 40–45 45–50 | Сталь 55 Сталь 40Х Сталь 65Г | 50–55 55–60 60–65 |
Аргонодуговая наплавка
Ручная аргонодуговая наплавка неплавящимся электродом – это дуговая сварка, осуществляемая с использованием вольфрамового электрода и внешней защиты аргоном, вдуваемым в ее зону. Применяется главным образом для наплавки деталей из алюминиевых сплавов.
Для получения качественной наплавки необходимо правильно выбрать силу тока, напряжение, тип электрода по допустимому значению переменного тока, а также соотношение диаметра сопла и толщины электрода (таблицы 3.6–3.8).
В зависимости от используемой силы сварочного тока устанавливают расход аргона (таблица 3.9).
Таблица 3.6 – Режимы аргонодуговой наплавки неплавящимся электродом
Толщина материала, мм | Сила тока, А | Напряжение, В | Диаметр вольфрамового электрода, мм | Диаметр присадочной проволоки, мм |
2–3 | 70–100 | 22–24 | 2–3 | 2 |
4–6 | 100–120 | 22–24 | 3–4 | 3 |
6–10 | 120–160 | 22–24 | 4 | 3–4 |
10–15 | 160–240 | 20–22 | 4–5 | 4–5 |
15 и более | 200–240 | 20–22 | 5–6 | 5–6 |
Таблица 3.7 – Зависимость диаметров сопла и электрода
Диаметр электрода, мм | 2…3 | 4 | 5 | 6 |
Диаметр выходного отверстия сопла, мм | 10–12 | 12–16 | 14–18 | 16–22 |
Таблица 3.8 – Допустимые значения переменного тока для электродов различных марок
Диаметр электрода, мм | Максимальный сварочный ток для вольфрамовых электродов, А | ||
ЭВЧ | ЭВЛ | ЭВИ-3 | |
1,0 | – | 65–75 | 70–80 |
1,6 | – | 80–100 | 100–150 |
2,0 | – | 150–180 | 200–250 |
4,0 | 180–190 | 200–220 | 300–350 |
6,0 | 240–260 | 300–340 | 410–480 |
8,0 | 360–390 | 450–500 | 490–590 |
10,0 | 450–500 | 600–650 | 650–750 |
Таблица 3.9 – Расход аргона в зависимости от силы сварочного тока
Сила сварочного тока, А | 15–20 | 20–30 | 30–40 | 40–60 | 60–100 | 100–140 | 140–180 | 180–230 |
Расход аргона, л/мин | 0,5–2 | 2–3 | 3 | 4 | 4–5 | 5–6 | 6 | 7–9 |
На ремонтных предприятиях применяют специальные установки УДГ-301, УДГ-501, УДАР-500, предназначенные для сварки (наплавки) деталей из алюминиевых сплавов в среде аргона на переменном токе. Защитный газ в этих установках подается автоматически с помощью электромагнитного клапана. Источником питания при этом служит сварочный трансформатор СТЭ-34 с дросселем насыщения ДН-300-1.
Скорость наплавки (Vн), частота вращения (n), скорость подачи электродной проволоки (Vэ), шаг наплавки (S), смещение электрода (е) определяются по тем же формулам, что и при наплавке под слоем флюса.
Электроискровая обработка
Технология электроискровой обработки металлических поверхностей основана на использовании импульсного электрического разряда, проходящего между электродами в газовой среде. Сущность его состоит в том, что при электрическом разряде в такой среде происходит разрушение материала электрода (анода) и переноса продукта эрозии на деталь (катод).
Единичный перенос электродного материала на поверхность детали происходит при высокой температуре разряда – 5000–11000 °С. Вследствие его кратковременности (до 10 мкс) и локальности нагретые микрообъемы переносимого металла на деталь мгновенно охлаждаются. При определенных режимах обработки происходит сверхскоростная закалка ее поверхностного слоя до высокой твердости. Толщина его увеличивается с ростом содержания углерода в материале детали и энергии единичного импульса.
Применение ЭИО позволяет достигнуть увеличения износостойкости деталей и инструментов в 2–5 раз.
Величина восстановления посадочных поверхностей неподвижных соединений составляет до 0,6 мм (на сторону), поверхностей трения скольжения – до 0,10 мм.
Для нанесения покрытий применяются установки типа «БИГ», «Элитрон» и др. Они универсальны, малогабаритны, мобильны, экономичны, относительно просты по конструкции, не сложны в эксплуатации и ремонте.
В качестве технологических материалов используются электроды из металлокерамических твердых сплавов, стали, чугуна, графита, меди и др.
В процессе формирования покрытия, применяя в качестве электродов различные материалы, можно получить рабочие поверхности с измененными механическими, физическими и химическими свойствами. В результате комплексных превращений в поверхностном слое катода происходит значительное увеличение микротвердости. Основными факторами, влияющими на изменение микротвердости, являются термосиловое воздействие импульсного разряда, закалочные явления, образование химических соединений (карбидов, нитридов и т. д.), осаждение на поверхности катода материала анода.
Важным достоинством электроискровой обработки материалов является возможность управлять процессом обработки и прогнозировать толщину покрытия, его текстуру и физико-механические свойства. Метод электроискрового нанесения металлопокрытий обладает высокой универсальностью и эффективностью при решении задач машиностроительного и ремонтного производства, что определяется широкими пределами значений характеристик покрытий.
Для электроискровой обработки материалов создана установка «БИГ-4», которая предназначена для нанесения металлических покрытий различного назначения (для восстановления размеров, увеличения износостойкости, жаростойкости, коррозионной стойкости, электропроводности и т. д.) на детали, режущие инструменты и рабочие части технологической оснастки.
Установка «БИГ-4» состоит их следующих элементов:
– генератора, предназначенного для создания рабочих импульсов тока и питания электромагнитного вибровозбудителя;
– вибратора, коммутирующего разрядную цепь генератора вибрирующим электродом.
Основные технические характеристики установки «БИГ-4» приведены в таблице 3.10., а характеристики покрытий, нанесенных электроискровым методом – в таблице 3.11.
Таблица 3.10 – Техническая характеристика установки «БИГ-4»
Наименование параметра | Значения параметров |
Потребляемая мощность, кВт | 0,5 |
Напряжение питающей сети, В | 220 |
Частота вибрации электрода, Гц | 600 |
Энергия импульсов, Дж | 0,045-5,0 |
Частота импульсов, Гц | 12-3000 |
Рабочий ток, А | 0,5-8 |
Количество электрических режимов | 35 |
Габаритные размеры (мм): | 170´250´430 |
Масса (кг), не более: | 14 |
Толщина покрытия сплавом Т15К6, мм* | 0,01-0,4 |
Высота неровностей профиля покрытия Ra, мкм | Ra2,0-Rz320 |
Максимальная производительность, см2/мин* | 6 |
Примечание:* - указанные параметры получены при нанесении покрытий электродом из сплава Т15К6 на заготовку из стали 45
Таблица 3.11 – Характеристики покрытий, нанесенных электроискровым методом
Характеристики покрытий | Значения |
Толщина (мкм): нанесенного слоя · белого слоя · переходного слоя | 5–400 до 250 до 400 |
Микротвердость (МПа): белого слоя · переходного слоя | 6000–16 000 3000–5500 |
Параметры рельефа поверхности: · характер рельефа поверхности · высота микронеровностей (мкм) · относительная высота выступов hв /rв · относительное расстояние между выступами Sм/Нмах | выпукло-вогнутый Ra1,6–Rz360 0,06–0,19 5–9 |
Теплопроводность электродных материалов λ, (Вт/м К) | 10–400 |
Из многолетнего опыта работы института ГОСНИТИ по применению электроискрового способа нанесения покрытий следует, что данный метод обеспечивает возможность восстановления деталей с односторонним износом до 0,1 мм (условия трения скольжения) и до 0,6 мм (в неподвижных соединениях).
Номенклатура восстанавливаемых изделий самая разнообразная: валы, оси, шкворни, цапфы, корпуса КПП, крышки, коренные опоры блока цилиндров, коленчатые валы компрессоров, золотники и корпуса гидрораспределителейи гидроусилителей руля, лопатки турбин и другие детали.
Особенность внедряемых технологий заключается, как правило, в нанесении покрытий на изношенные поверхности под размер, чтобы в последующем проводить минимальный съем нанесенного металла механической обработкой.
Основными преимуществами метода электроискрового легирования являются:
– отсутствие нагрева и деформации детали при обработке;
– высокая адгезия с основным материалом;
– восстановление детали в размер без механической обработки;
– возможность локального формирования покрытий;
– использование любого токопроводящего материала в качестве электрода;
– высокий коэффициент переноса материала до 80 %;
– низкая энергоемкость процесса (0,5–1,0 кВт);
– экологичность процесса.
Экспериментальные исследования показали, что для достижения оптимальной площади опорной поверхности целесообразно назначать припуски на укатку (раскатку) и механическую обработку наплавленной поверхности в пределах 0,1–0,7 толщины покрытия [9].
Процесс ЭИО проводится как вручную, так и с использованием средств механизации. В обоих случаях перемещение электрода, продолжительность обработки, режимы по току, амплитуде и частоте вибрации электрода выбираются так, чтобы покрытие было сплошным, равномерным, имело ровную светоотражательную характеристику.
Для обеспечения требуемых эксплуатационных свойств восстановленных поверхностей покрытия можно формировать нанесением нескольких слоев различными материалами.
В ряде случаев при восстановлении изношенных поверхностей подшипниковых узлов в пределах установленных посадок электроискровая обработка является финишной обработкой, не требующей дополнительной механической обработки.
Рекомендации по выбору технологических параметров ЭИО приводятся в источнике [16].
Гальванические покрытия
Сила тока, I (А)
I = Dк · Fк, (3.38)
где Dк – катодная плотность тока, А/дм2 (определяется условиями работы детали, видом покрытия, температурой и концентрацией электролита). Значения принимают равным: при хромировании Dк = 50–75 А/дм2, железнении Dк = 20–40 А/дм2;
Fк – площадь покрываемой поверхности, дм2.
Механическая обработка
При назначении режимов выполнения операций на металлорежущих станках необходимо пользоваться учебной и справочной литературой по обработке материалов резанием.
Токарная обработка (точение) . Разрабатывая технологический процесс обработки детали, необходимо установить режимы, от которых в значительной мере зависят производительность и стоимость обработки. Установить режим – это значит определить глубину резания (t), подачу (S), скорость резания (V) и частоту вращения (n).
Глубина резания, мм
(3.39)
где t1 – припуск на диаметр, мм.
Подача, мм/об, для чернового точения выбирается по таблице 3.11.
Таблица 3.11 – Подача при обтачивании и растачивании деталей из стали
Подача при обтачивании | ||||
Глубина резания t, мм | Диаметр детали, мм | |||
18 | 30 | 50 | 70 | |
Подача S, мм/об | ||||
До 5 | до 0,25 | 0,2–0,5 | 0,4–0,8 | 1,0–1,4 |
Подача при растачивании | ||||
Глубина резания t, мм | Диаметр круглого сечения державки резца, мм | |||
10 | 15 | 20 | 25 | |
Вылет резца, мм | ||||
50 | 80 | 100 | 125 | |
Подача S, мм/об | ||||
Сталь t = 2 t = 3 | 0,05–0,08 – | 0,08–0,20 0,08–0,12 | 0,15–0,40 0,10–0,25 | 0,25–0,70 0,15–0,40 |
Требуемая шероховатость обработанной поверхности является основным фактором, определяющим величину подачи при чистовом точении (таблица 3.12).
Таблица 3.12 – Подача в зависимости от заданной шероховатости поверхности для токарного резца со значениями главного и вспомогательного углов в плане j = j1 = 45°
Диапазон скорости резания, м/мин | Параметр шероховатости Rа, мкм | Радиус при вершине резца, мм | ||
0,5 | 1,0 | 1,5 | ||
Подача S, мм/об | ||||
Весь диапазон | 50,0 25,0 12,5 6,3 3,2 | – – 0,46 0,20–0,35 0,13 | – – 0,58–0,89 0,25–0,44 0,12–0,17 | – – 0,67–1,05 0,29–0,51 0,14–0,20 |
Скорость резания, м/мин
(3.40)
где t – глубина резания, мм;
S – подача, мм/об;
Т – стойкость инструмента, мин (принимается по таблице 3.13).
Значение С выбирается по таблице 3.14.
Значение m выбирается согласно таблице 3.15.
Значение x при обработке стали – 0,18, при обработке чугуна – 0,15.
Значение у при обработке стали – 0,27, при обработке чугуна – 0,30.
Таблица 3.13 – Стойкость резцов в зависимости от их материала и поперечного сечения державки
Материал резца | Сечение резца, мм | ||||
16´25 | 20´30 | 25´40 | 40´60 | 60´90 | |
Стойкость резцаТ, мин | |||||
Быстрорежущая сталь Металлокерамический твердый сплав | 60 90 | 60 90 | 90 120 | 120 150 | 150 180 |
Таблица 3.14 – Значения коэффициента С в зависимости от обрабатываемого материала
Обрабатываемый материал | С |
Сталь, стальное литье Серый чугун и медные сплавы | 41,7 24,0 |
Таблица 3.15 – Значения коэффициента m в зависимости от условий обработки
Обрабатываемый материал | Типы резцов | Условия обработки | m | ||
Быстрорежущая сталь | Сплав ТК | Сплав ВК | |||
Сталь, стальное литье, ковкий чугун | проходные подрезные расточные проходные отрезные | с охлаждением без охлаждения с охлаждением без охлаждения | 0,125 0,100 0,250 0,200 | 0,125 0,125 – – | 0,15 0,15 0,15 0,15 |
Зная скорость резания и диаметр заготовки при токарной обработке или диаметр сверла и фрезы, соответственно, при сверлении и фрезеровании, определяют частоту вращения, мин-1
(3.41)
где d – диаметр заготовки, мм.
Сверяя полученное значение n с паспортными данными станка, устанавливают фактическую частоту вращения шпинделя nФ, максимально приближенную к расчетной. По nФ пересчитывают фактическую скорость резания, мм/мин:
(3.42)
Сверление . Глубина резания, мм, при сверлении в сплошном материале определяется по формуле
t = D / 2. (3.43)
Глубина резания, мм, при рассверливании отверстия с диаметра d до диаметра D является припуском на обработку и определяется как:
t = (D – d) / 2, (3.44)
где D – диаметр сверла, мм;
d – диаметр предварительно подготовленного отверстия, мм (принимается по данным ремонтного чертежа).
Подача, мм/об
S = 0,035 · D0,6 (3.45)
Скорость резания, м/мин:
- при сверлении
(3.46)
- при рассверливании
(3.47)
где D – диаметр сверла, мм;
S – подача, мм/об;
Т – стойкость сверла, мин (принимается по таблице 3.16).
Значения величин С1, m, y, q, x выбираются по таблице 3.17.
Таблица 3.16 – Стойкость сверл в зависимости от их диаметра и обрабатываемого материала
Диаметр сверла, мм | 8 | 12 | 16 | 20 | 24 | 30 |
Стойкость сверла Т, мин | При обработке сталей | |||||
10 | 10 | 12 | 18 | 18 | 30 |
Таблица 3.17 – Значения коэффициентов в формуле скорости резания при сверлении и рассверливании в зависимости от условий обработки
Обрабатываемый материал | Подача S, об/мин | Сверление | Рассверливание | |||||||
C1 | m | y | q | C1 | m | y | q | x | ||
Сталь | до 0,2 свыше 0,2 | 7,0 9,8 | 0,2 0,2 | 0,7 0,5 | 0,4 0,4 | 11,6 11,6 | 0,2 0,2 | 0,2 0,2 | 0,5 0,5 | 0,4 0,4 |
Частота вращения, мин-1, определяется по той же формуле, что и для токарной обработки.
Фрезерование. Подача на зуб, мм/зуб:
– для цилиндрических фрез – Sz = 0,01…0,10 мм/зуб;
– для твердосплавных торцовых фрез – Sz = 0,2…1,0 мм/зуб.
Подача на один оборот фрезы, мм/об
Sо = Sz · z, (3.47)
где z – число зубьев фрезы.
Диаметр и число зубьев фрезы выбираются по справочной литературе. Глубина фрезерования определяется припуском на обработку.
Скорость резания, м/мин
(3.48)
где D – наружный диаметр фрезы, мм;
Т – стойкость фрезы, мин (принимается согласно таблицам 3.18 и 3.19);
В – ширина фрезерования, мм.
Значения величин С2, q, m, x, y, z, n следует выбирать по таблице 3.20
Таблица 3.18 – Стойкость фрез из твердых сплавов в зависимости от их типа, диаметра и числа зубьев
Тип фрез | Число зубьев фрезы | ||||||
4 | 5 | 6 | 8 | 10 | 12 | 16 | |
Стойкость Т, мин | |||||||
Торцовые с призматическими ножами Торцовые с круглыми ножами Дисковые Концевые: D до 30 мм D свыше 30 мм | 160 100 – | 200 100 – | 240 120 – | 320 160 240 60 180 | 400 200 300 | – 240 860 | – – 480 |
Таблица 3.19 – Стойкость фрез из быстрорежущей стали в зависимости от их типа, диаметра и числа зубьев
Тип фрез | Диаметр фрезы, мм | Конструкция фрезы | Стойкость Т, мин |
Цилиндрические | до 60 свыше 60 | монолитная | 60 90 |
Торцовые и дисковые | до 90 до 150 свыше 150 | монолитная со вставными ножами | 120 180 |
Фасонные | до 60 свыше 60 | монолитная | 180 270 |
Концевые | с цилиндрическим хвостовиком с коническим хвостовиком | 30 60 |
Таблица 3.20 – Значения коэффициентов в формуле скорости резания при фрезеровании
Материал режущей части фрезы | Обрабатываемый материал | С2 | q | m | x | y | z | n |
Быстрорежущая сталь Твердый сплав | Сталь Сталь | 30 330 | 0,45 0,20 | 0,33 0,20 | 0,30 0,10 | 0,30 0,20 | 0,10 0,20 | 0,10 0,10 |
Частота вращения фрезы, мин-1, определяется по той же формуле, что и для токарной обработки.
Минутная подача, м/мин
S = Sо · n (3. 49)
Шлифование с продольной подачей. Глубина шлифования, мм:
– при круглом чистовом шлифовании – h = (0,005–0,015) мм;
– при черновом шлифовании – h = (0,010–0,025) мм.
Число проходов:
(3. 50)
где t – припуск на шлифование (на сторону), мм.
Продольная подача, мм/об:
S = Sд · Вк, (3.51)
где Sд – продольная подача в долях ширины круга на один оборот детали;
Вк– ширина шлифовального круга, мм (Вк = 20–60 мм).
При круглом шлифовании величина S зависит от вида шлифования:
1) S = (0,3–0,5) · Вк – при черновом шлифовании деталей, изготовленных из любых материалов, диаметром меньше 20 мм;
2) S = (0,6–0,7) · Вк – при черновом шлифовании деталей, изготовленных из любых материалов, диаметром более 20 мм;
3) S = (0,75–0,85) · Вк – для деталей из чугуна;
4) S = (0,2–0,3) · Вк – при чистовом шлифовании независимо от материала и диаметра детали.
Окружная скорость детали, м/мин:
– для чернового шлифования – Vд = 20–80 м/мин;
– для чистового шлифования – Vд = 2–5 м/мин.
Скорость продольного перемещения стола, м/мин
(3.52)
где nд – частота вращения детали, мин-1 (определяется по той же формуле, что и для токарной обработки).
Шлифование с поперечной подачей (методом врезания) . Врезное шлифование является производительным методом обработки. Оно осуществляется с поперечной подачей до достижения необходимого размера поверхности (продольная подача отсутствует). Шлифовальный круг перекрывает всю ширину (длину) обрабатываемой поверхности детали. Основные параметры процесса (h, Vд) определяются так же, как и при продольном шлифовании.
Хонингование . Расчет режимов хонингования сводится к определению скоростей вращательного (VВР) и возвратно-поступательного (VВП) движения, числа оборотов хоны (nх), длины хода хонинговальной головки (Lх) и числа ее двойных ходов (nдв. х).
Окружная (VВР) и возвратно-поступательная (VВП) скорости при хонинговании выбираются в зависимости от материала и твердости обрабатываемой детали, материала хонинговальных брусков по справочной литературе.
По выбранной окружной скорости определяется количество оборотов хонинговальной головки:
(3.53)
Полученное количество оборотов уточняется с учетом паспортных данных станка 3Г833 (155, 260, 400 мин-1), а по ним подсчитывается фактическая окружная скорость доводочной головки (VВР).
Длина хода доводочной головки, мм, рассчитывается по формуле
(3.54)
где l1 – длина обрабатываемого цилиндра, мм;
l2 – перебег бруска, мм (l2 = 20–30 мм);
lБ – длина бруска, мм (lБ = 100 мм).
Число двойных ходов головки определяется по формуле
(3.55)
Дата добавления: 2018-11-24; просмотров: 12315; Мы поможем в написании вашей работы! |
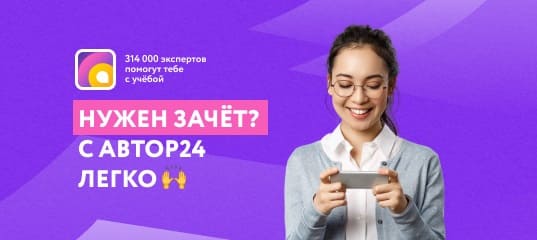
Мы поможем в написании ваших работ!