Описание и анализ аналога технологического процесса ремонта (восстановления) детали
Исходными данными для разработки технологического процесса восстановления детали являются: чертеж детали и чертеж сборочной единицы, в которую она входит (для анализа условий работы); сведения о дефектах, выявленных при дефектации детали (дефектовочная ведомость); справочные материалы о технологических методах устранения отдельных дефектов и уровне восстановления служебных свойств детали различными методами; справочные и нормативные данные по материалам, режимам восстановления и обработки, техническим нормам и т. д.; перечень имеющегося оборудования, режущего, измерительного и вспомогательного инструмента; научно-техническая информация по современным методам восстановления деталей машин; программа выпуска восстановленных деталей, от которой зависят тип производства и степень детализации технологического процесса ремонта.
Для обеспечения преемственности между изготовлением и восстановлением детали желательно также иметь технологический процесс ее изготовления. Проектирование технологических процессов восстановления в общем случае включает следующие основные этапы: анализ по конструкторской документации требований к точности размеров, геометрической формы, качеству обработки и эксплуатационным свойствам восстанавливаемых поверхностей; определение допустимых, ремонтных и предельных значений их размеров; анализ дефектов и разработка ремонтного чертежа детали; выбор методов восстановления изношенных поверхностей и устранения отдельных дефектов детали на основе ее конструктивно-технологических характеристик и требуемых физико- механических свойств; оценка технико-экономических показателей методов восстановления деталей; составление технологического маршрута ремонта детали (определение последовательности операций, выбор необходимого оборудования, приспособлений, инструментов и средств контроля по всем операциям, обеспечивающим высокую производительность и требуемое качество); разработка технологических операций (рациональное построение и выбор структуры технологических операций, задание рациональной последовательности переходов в операциях); выбор необходимых материалов, рациональных режимов восстановления поверхностей и их обработки; определение квалификации рабочих и техническое нормирование ремонтных работ.
|
|
При подробной разработке технологического процесса восстановления детали указываются операции, переходы, оборудование, приспособления, инструмент, режимы обработки и норма времени. Для повышения качества и эффективности ремонта машин наряду с широкоуниверсальными средствами технологического оснащения могут создаваться или приобретаться специальное оборудование, приспособления и инструменты, наибольший эффект от применения которых достигается при организации ремонта в специализированных цехах или участках.
|
|
Большое разнообразие деталей машин по размерам, форме, шероховатости поверхности, восстанавливаемых на различном технологическом оборудовании с разной технологической оснасткой, порождает многообразие технологических процессов на ремонт и восстановление.
Сокращение числа технологических процессов и разработка общих принципов их проектирования могут быть осуществлены на основе типизации технологических процессов, базирующихся на классификации деталей по конструктивно-технологической однородности.
К конструктивным признакам, объединяющим детали в однородные группы, относятся геометрические размеры, материал и масса детали, точность изготовления, шероховатость поверхностей.
Основные технологические признаки, влияющие на классификацию деталей: виды износа, общность дефектов и их сочетаний, применяемые способы и средства восстановления и др.
Согласно классификации, приведенной в учебном пособии [2], валик 50-1307052-Б относится к IX группе деталей: шлицевые и карданные валы, оси, шестерни. Характерными дефектами для данной группы деталей являются износ шлицев и шпоночных пазов, посадочных мест под подшипники, поверхности отверстий, износ и повреждение резьбы. К работам по устранению данных дефектов относится восстановление да номинальных размеров наружной цилиндрических поверхностей.
|
|
В соответствии с типовым процессом восстановления детали типа «вал», применяемого на ремонтных предприятиях, с дефектами, аналогичными приведенным в задании, износ шпоночного паза устраняется путем его заварки в среде углекислого газа с последующим фрезерованием; внутренняя резьба восстанавливается при помощи резьбовой спиральной вставки; наружная резьба восстанавливается путем наплавки в среде углекислого газа с последующим нарезанием резьбы; шейка под подшипник восстанавливается при помощи наплавки в среде углекислого газа с последующей закалкой и механической обработкой.
В проекте для восстановления посадочных мест под подшипники и наружной метрической резьбы предлагается использовать метод электроискровой обработки (ЭИО).
Основными преимуществами метода ЭИО являются:
|
|
– отсутствие нагрева и деформации детали при обработке;
– высокая адгезия с основным материалом;
– восстановление детали под номинальный размер без механической обработки;
– возможность локального формирования покрытий;
– использование любого токопроводящего материала в качестве электрода;
– высокий коэффициент переноса материала (до 80 %);
– низкая энергоемкость процесса (0,5–1,0 кВт);
– экологичность процесса.
Применение ЭИО позволяет достигнуть увеличения в 2–5 раз износостойкости деталей. При этом величина восстановления посадочных поверхностей неподвижных соединений составляет до 0,6 мм (на сторону), поверхностей трения скольжения – до 0,1 мм.
Для нанесения покрытий применяются установки типа «БИГ–4», «Элитрон» и др. Они универсальны, малогабаритны, мобильны, экономичны, относительно просты по конструкции, не сложны в эксплуатации и ремонте.
В качестве технологических материалов используются электроды из металлокерамических твердых сплавов, стали, чугуна, графита, меди и др.
Дата добавления: 2018-11-24; просмотров: 394; Мы поможем в написании вашей работы! |
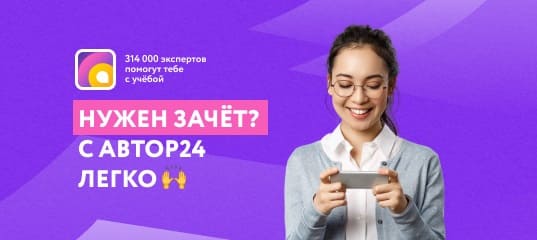
Мы поможем в написании ваших работ!