Преддиспергирование и диспергирование пигментной суспензии
В чистую и сухую емкость погружной бисерной мельницы из нержавеющей стали емкостью 1 м3 загружают воду через счетчик, антисептик и диспергатор.
При работающей фрезе с весов загружается (в соответствии с регламентируемыми загрузками):
ü Двуокись титана
ü Микрокальцит
ü Мел
ü Каолин
После загрузки содержимое бисерной мельницы перемешивают в течение 25-30 мин. По окончании перемешивания лаборант отбирает пробу для проверки дисперсности замеса.
При положительных результатах производят загрузку с весов:
ü Загустителя
ü Карбамида
ü Уайт-спирита (коалесцент вводится медленно в избежание полной коагуляции)
ü Этиленгликоля
ü Пленкообразующее (дисперсия ПВА)
ü Пеногаситель
При достижении степени перетира не более 70 мкм суспензию направляют в смеситель.
Составление и постановка краски на «тип»
Составление краски проводят в смесителе, который представляет собой вертикальный аппарат с цилиндрическим корпусом, приваренным сферическим днищем и съемной сферической крышкой, оборудованной тихоходной якорно-рамной мешалкой, вращающейся со скоростью 48 об/мин, люками и штуцерами.
Перед началом загрузки компонентов смеситель продувают азотом в течение 10 минут. После того, как в смеситель загружено необходимое количество краски, якорно-рамная мешалка включается в работу не менее чем на 20 мин.
После окончания перемешивания отбирается проба для определения цвета краски и ее соответствия образцу цвета. Для этого нанесенную на пластинку и высушенную краску сравнивают с контрольным образцом цвета. При необходимости производят добавки. После каждой добавки производят перемешивание содержимого не менее 20 мин. Чем меньше количество произведенной добавки, тем большего времени требуется для равномерного распределения добавляемого вещества по всему объему.
|
|
Содержимое дежи перемешивается 15-20 мин и отбирается проба для проведения анализа краски по всем показателям ТУ или ГОСТ. При соответствии требований ГОСТ или ТУ краска передается на фильтрацию и фасовку в тару.
При не соответствии каким-либо показателям краска подлежит постановке на «тип». Для этого производят добавки необходимых компонентов и вновь анализируют краска по показателям НТД. Фильтрация и фасовка производится при полном соответствии ее качества требованиям ГОСТ или ТУ.
В процессе производства краски количество загруженного сырья, полуфабрикатов и тары записывается аппаратчиком в технологическую карту. Туда же записывается дата, время загрузки каждого компонента и фамилия лица, производившего загрузку.
|
|
Фильтрация и фасовка краски
При полном соответствии всех показателей краски требованиям ГОСТ или ТУ и после стабилизации готовую краску с помощью героторного насоса подают на фильтрацию в патронныйфильтр типа «Кюно», где она очищается от разнообразных примесей. Периодически в процессе фильтрации включается мешалка и проверяется качество очистки краски путем налива ее пробы на стекло. Фасовка готовой краски в тару производится с помощью фасовочной машины.
Фасовка краски производится в металлическую тару. Тара перед фасовкой проверяется на чистоту и исправность.
Расчёт оборудования
Исходные данные для расчета оборудования
1) производительность участка – 35000 т/год;
2) цех работает непрерывно в три смены по 8 часов;
3) остановка цеха производится на праздники (11суток) и капитальный ремонт. Капитальному ремонту подвергается в это время все оборудование.
Нормативы ресурса между ремонтами (межремонтный пробег), длительность ремонта и технологические остановки приведены в таблице 5.1
Таблица 5.1
Нормативы ресурса между ремонтами (межремонтный пробег), длительность ремонта и технологические остановки
Вид ремонтов и остановки | Норматив ресурса между ремонтами, ч | Длительность ремонта, ч |
1. Капитальный | 14700 | 120 |
2. Средний | 4320 | 48 |
3. Текущий | 720 | 4 |
4. Технологические остановки | 240 | 5 |
|
|
1. Календарный фонд времени
365 · 24 = 8760 (ч)
2. Число циклов капитального ремонта приходящихся на год
8760/14700 = 0,6
3. Общий годовой фонд рабочего времени (ОГФРВ)
n = 365 – 11 – (120/24 · 0,6) = 351 (суток)
4. Коэффициент использования оборудования
Кисп = ОГФРВ – простои на средний и текущий ремонт / ОГФРВ,
где ОГФРВ – общий фонд рабочего времени
Кисп=(351·24–((351·24/4320)·48 + (351·24/720)·4+(351·24/240)·5)) /
351·24=0,96
Дата добавления: 2018-10-25; просмотров: 196; Мы поможем в написании вашей работы! |
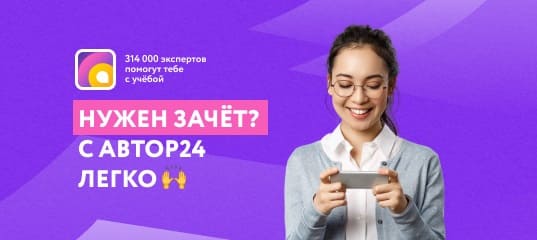
Мы поможем в написании ваших работ!