Характеристика выпускаемой продукции
Краски поливинилацетатные ВД-ВА представляют собой суспензию пигментов, наполнителей и других специальных добавок в водной гомополимерной поливинилацетатной дисперсии и применяются для покрасок внутри помещений по картону, гипсокартону, штукатурке, шпатлевке, дереву, бетону и другим строительным материалам.
Краска ВД-ВА интерьерная ТУ 2316-005-20514586-04должна соответствовать качественным показателям, приведенным в таблице 2.1
Таблица 2.1
Качественные показатели краски ВД-ВА интерьерной ТУ 2316-005-20514586-04
Наименование показателей | Значение показателей |
Внешний вид пленки | После высыхания краска должна образовывать однородную, без кратеров, пор и морщин матовую поверхность |
Цвет покрытия | Должен находиться в пределах допускаемых отклонений, установленных образцами (эталонами) или контрольными образцами цвета |
Массовая доля нелетучих веществ, %, не менее | 53,0 |
Степень перетира, мкм, не более | 70 |
Время высыхания до степени 3 при температуре (20+2)0С, ч, не более | 1,0 |
Укрывистость высушенной пленки, г/м2, не более | 120,0 |
рН краски | 6,8-8,2 |
Характеристика исходного сырья, материалов и полупродуктов
Характеристика исходного сырья, материалов и полупродуктов приведена в таблице 2.2.
Таблица 2.2
Характеристика исходного сырья, материалов и полупродуктов
№ п/п | Наименование сырья, материалов, полупродуктов | Государственный или отраслевой стандарт, технические условия или методика по подготовке сырья | Показатели, обязательные для проверки | Регламентируемые показатели с допустимыми отклонениями |
1 | 2 | 3 | 4 | 5 |
1 | Дисперсия ПВА марки ДФ-51/10с | ГОСТ 18992-80 | 1. Массовая доля сухого остатка, %, не менее 2. Условная вязкость по кружке ВМС, с 3. Показатель водородных ионов, рН | 52 11-40 4,5-6,0 |
2 | Мел М-5 | ТУ 5743-010-00186803-95 с изм. 1 | 1. Белизна,%, не менее по ФБ-2 2. Остаток на сите с сеткой 0045,%, не более | 83 0,6 |
3 | Микрокальцит | ТУ 5743-002-63925093-2009 | 1. Белизна,% 2. Плотность, г/смЗ, не менее | 96 2,7 |
4 | Диоксид титана пигментный | ТУ 24.1-05762329-001-2003 | 1. Массовая доля летучих веществ, %, не более 2. Остаток на сите с сеткой №0045, % | 0,4 0,004 |
5 | Каолин кальцинированный | ТУ 5729-010-40705684-2005 | 1. Массовая доля летучих веществ, % 2. Массовая доля остатка на сите №0045, %, не более | 0,5 0,1 |
6 | Натрия триполифосфат | ТУ 2148-095-23380904-2004 | рН 1%-ного водного раствора | 9,8 |
7 | Карбамид | ГОСТ 2081-2010 | Массовая доля воды, %, не более | 0,6 |
8 | Антивспениватель ПК-3 | ТУ 2484-129-05744685-99 | - | - |
9 | Консервант | - | рН | 3,0-5,0 |
10 | Уайт-спирит | ГОСТ 3134-78 | 1. Плотность при температуре (20,0±0,5)°С г/смі, не более 2. Содержание механических примесей и воды | 0,790 отсутствует |
11 | Бланозе | Импорт | 1. Внешний вид 2. Содержание влаги, % не более | Белый, кремовый порошок 0,2 |
12 | Этиленгликоль | ГОСТ 19710-74 | 1. Внешний вид и цвет 2. Плотность при (20±0,5)°С, г/см3, не менее | Прозрачная бесцветная жидкость без механических примесей и воды 1,11 |
|
|
|
|
Обоснование состава композиции
Рецептура краски ВД-ВА представлена в табл.2. 3
Таблица 2.3
Рецептура краски ВД-ВА интерьерной
№ п/п | Наименование компонентов | Содержание, % | Назначение |
1 | Дисперсия ПВА | 10,9 | Связующее |
2 | Мел | 20,0 | Наполнитель |
3 | Микрокальцит | 20,0 | Наполнитель |
4 | Двуокись титана | 6,0 | Пигмент |
5 | ТПФ натрия | 0,5 | Диспергатор |
6 | Антисептик | 0,5 | Консервант |
7 | Антивспениватель ПК-3 | 0,5 | Пеногаситель |
8 | Этиленгликоль | 0,5 | Антифриз |
9 | Уайт-спирит | 0,1 | Коалесцент (функциональная добавка) |
10 | Бланозе | 0,3 | Загуститель |
11 | Каолин | 6,0 | Наполнитель |
12 | Вода | 34,2 | Дисперсионная среда |
13 | Карбамид | 0,5 | Функциональная добавка |
ИТОГО | 100,0 |
Примечание:
1. Допускается погрешность дозировки отдельных компонентов по массе неболее +2%.
|
|
2. Допускается замена в эквивалентном количестве этиленгликоля на
диэтиленгликоль других производителей, в том числе импортных при условии сохранения их регламентируемых показателей качества.
Дисперсия ПВА
Краски на основе ПВА достаточно светостойки и атмосферостойки. Структуру молекулярной цепи ПВА можно представить следующим образом:
Структурная формула
[-CH2CH(OCOCH3)-]n
Основные физические и химические свойства
- физические свойства:
Поливинилацетатная дисперсия (ГОСТ 18992-80) представляет собой вязкую белую однородную жидкость с удельным весом 1,1г/см3, являющуюся продуктом полимеризации винилацетата в водной среде в присутствии эмульгатора и инициатора реакции полимеризации, смешанную с пластификатором или без него.
1. Молекулярная масса от 10 000 до 1 500 000 ;
2. Температура размягчения 30-50 °С;
3. Плотность 1,19 г/см3;
4. Относительное удлинение 10-20%;
5. Теплопроводность 0,16 Вт/(м·К);
6. Температура стеклования 280C;
7. Теплостойкость по Вику 44-500C, по Мартенсу 30-320C;
8. Электрическая прочность 1 МВ/м;
9. Влагопроницаемость (2,5-5,8)· 10-14 кг/(м·с·Па);
10. Газопроницаемость по H2 56·10-15 м3/(м·с·Па).
|
|
Поливинилацетат обладает хладотекучестью, устойчив к старению в атмосферных условиях, высокой адгезией к различным поверхностям, хорошими оптическими свойствами, износостоек. Хорошо растворим в кетонах, сложных эфирах, хлорированных и ароматических углеводородах, метаноле, хуже - в этаноле. Не растворим в воде, алифатичных углеводородах, бензине, минеральных маслах, гликолях.
- химические свойства:
Химические свойства ПВА определяются наличием сложноэфирных групп и привитых цепей, соединенных с главной цепью сложноэфирными связями. ПВА омыляется водными растворами кислот или щелочей и подвергается алкоголизу под действием каталитических количеств кислот и алкоголятов щелочных металлов в безводных средах с образованием ПВС.
Получение ПВА
В промышленности поливинилацетат получают радикальной полимеризацией винилацетата в растворе, эмульсии или суспензии. Мономер винилацетата диспергируют в воде при сильном перемешивании в присутствии эмульгаторов. В этой дисперсии мономера в воде при введении ингибитора начинается процесс полимеризации. Постепенно формируется поливинилацетат, который растворяется в остаточном мономере, но не растворяется в воде, с которой он образует эмульсию. Наряду с линейным может образовываться и разветвленный поливинилацетат.
В процессе полимеризации в растворе (обычно в метаноле) при 60-65 0C в присутствии инициатора получаемый поливинилацетат перерабатывается главным образом в поливиниловый спирт. В случае непрерывного процесса реакцию прекращают при степени превращения винилацетата 50-65%; образующийся поливинилацетат имеет меньше разветвлений, его степень полимеризации достигает 1800-2000.
Эмульсионную полимеризацию винилацетата в воде проводят при 65-900C в присутствии защитных коллоидов (например, поливинилового спирта, гидроксиэтилцеллюлозы) или ПАВ и окислительно-восстановительных инициирующих систем.
Выпускается в виде гранул (бисера), водных дисперсий или растворов (лаков).
Способы отверждения ПВА
Отверждение может происходить вследствие различных механизмов, которые в основном делятся на три группы:
1. Отверждение с добавлением солей металлов.
2. Отверждение с добавлением термореактивных смол, полученных в результате конденсации формальдегида.
3. Отверждение с добавлением изоцианата /8/.
2.3.2 Пигменты
Пигменты в рецептурах ВД-ЛКМ используют не только для обеспечения необходимых укрывистости и цвета покрытий, но и повышения атмосферостойкости и стойкости к действию УФ-излучения. В настоящее время наиболее широко применяемым белым пигментом является диоксид титана благодаря более высокому коэффициенту преломления, чем у оксида и сульфида цинка и литопона. Последние мало используются, потому что не обеспечивают высокой белизны и укрывистости покрытия, более склонны к мелению.
Диоксид титана: (двуокись титана) TiO2 – полиморфный кристаллический пигмент, кристаллизуется в двух сингониях: брукит- в ромбической, рутил и анатаз в тетрагональной, но последние различаются строением кристаллической решетки. В обоих случаях каждый атом титана находиться в центре октаэдра и окружен 6 атомами кислорода. Пространственное же расположение октаэдров разное: в анатазе на каждый октаэдр приходиться 4 общих ребра, в рутиле только 2 рис. 2.1 /5/
рутил анатаз
Рис. 2.1 Кристаллические структуры диоксида титана
Благодаря более плотной упаковке ионов в кристаллах рутил превосходит анатаз по стабильности, плотности, твердости, показателю преломления, диэлектрической постоянной и обладает пониженной фотохимической активностью.
В чистом виде диоксид титана, особенно в анатазной форме, обладает высокой фотохимической активностью, что вызывает разрушение лакокрасочной пленки («меление») и выцветание органических пигментов. Закрытие активных центров поверхности частиц титана гидроксидами Al, Si, Zn резко уменьшает фотохимическую активность. Такой модифицированный рутильный диоксид титана обладает незначительной фотохимической активностью и пригоден для атмосферостойких красок.
Диоксид титана химически инертен, нерастворим в слабых кислотах и щелочах и органических растворителях. Он может применяться со всеми видами пленкообразователей.
2.3.3 Наполнители
Наполнители - неорганические соединения, имеющие более низкий коэффициент преломления, чем пигменты (значение коэффициента преломления для наполнителей менее 1,7).
Большинство наполнителей — это природные минералы: кальцит, мел, доломит, каолин, тальк, слюда, диатомитовая земля, барит, кварц. Но некоторые из них получены реакцией осаждения (карбонат кальция или сульфат бария, пирогенный диоксид кремния). Плотность обычных наполнителей составляет 2,5—2,8, барита — 4 г/см3.
Наиболее часто применяемым наполнителем является карбонат кальция. В Западной Европе карбонат кальция в форме кристаллического кальцита и аморфного мела составляет 80—90% всех используемых наполнителей. В рецептурах многих ЛКМ в качестве наполнителя применяют только кальцит.
Однако в рецептурах матовых красок может быть использовано до шести видов различных наполнителей, отличающихся по размеру частиц, кристаллической форме и активности.
Как правило, наполнители используют для снижения стоимости материалов, но иногда они могут применяться и для модификации свойств красок. При использовании наполнителей можно достигать значений объемной концентрации пигментов (ОКП)> критической объемной концентрации пигментов (КОКП), при которых заполненные воздухом поры обеспечивают укрывистость высушенной пленки, позволяя таким образом экономить дорогой диоксид титана.
Наполнители повышают твердость покрытий, укрывистость и удельный вес краски, снижают ее себестоимость. Кроме того, тип наполнителя влияет на атмосферостойкость, устойчивость к истиранию, блеск покрытий, их устойчивость к загрязнению и газопроницаемость, а также на реологические свойства красок.
Основными свойствами наполнителей являются размер частиц, яркость и белизна. Чем мельче частицы, тем светлее наполнитель, но тем выше его впитывающая способность, характеризуемая маслоемкостью.
Кристаллическая форма наполнителя существенно влияет на его способность к диспергированию и реологическую активность в жидких ЛКМ и физико-механические свойства покрытий.
2.3.4 Функциональные добавки
Функциональные добавки - это вспомогательные вещества, применяемые для улучшения процессов пленкообразования и нанесения ЛКМ, повышения стабильности и долговечности красок и покрытий, а также для придания им каких-либо специальных свойств. Основные используемые в настоящее время добавки можно разделить по их назначению на следующие группы:
• коалесценты (пленкообразующие добавки);
• загустители;
• пеногасители;
• смачивающие или диспергирующие агенты;
• нейтрализующие агенты;
•биоциды (консерванты).
Коалесценты,как известно, позволяют снижать температуру пленкообразования водных дисперсий. Так как температура пленкообразования наиболее широко распространенных дисперсий составляет 13—18°С, а нанесение ВД-ЛКМ должно происходить при температуре, по крайней мере 5°С. практически во всех рецептурах необходимо использовать добавки, понижающие температуру пленкообразования.
Подходящими для этих целей являются растворители, которые в течение времени их испарения пластифицируют полимер. Кроме снижения температуры пленкообразования, пленкообразующие добавки влияют на время высыхания и твердость покрытия. Использование растворителей с высокой температурой кипения, из-за их высокой пластифицирующей активности может приводить к повышению грязеудержания покрытия. Пленкообразующие добавки также влияют на вязкость и смачиваемость ЛКМ и на устойчивость покрытия к мокрому истиранию.
В практической работе следует помнить, что чаше всего при добавлении коалесцентов дисперсии и краски теряют коллоидную стабильность. При быстром добавлении этих веществ могут образовываться микрогели или произойти полная коагуляция. Это явление (так называемый «шок от действия растворителя») можно предотвратить путем медленного введения коалесцента или предварительного разбавления его водой и/или растворителем, смешиваемым с водой.
В качестве самого простого коалесцента используется уайт-спирит. Уайт-спирит - бесцветная маслянистая жидкость с запахом, напоминающим керосин, но более слабым. Четкой формулы для уайт-спирита нет, поскольку это не чистое химическое вещество, а смесь углеводородов как линейного, так и ароматического строения. Химическая формула C10,5H21,0.
Загустители – это специфические реологические добавки, которые применяют для достижения реологических свойств ВД-ЛКМ оптимальных для их получения, хранения и нанесения. Загущающие системы могут быть как органической, так и неорганической природы.
Загустители повышают вязкость краски вплоть до придания ей небольшой пластичности вследствие высокой собственной, обусловленной гидратацией, вязкости в водном растворе и формирования мостичных связей между дисперсными частицами.
В качестве загустителя в нашем случае применяется натриевая соль карбоксиметилцеллюлозы (Na-КМЦ) набухающая в щелочи.
Бланозе (Blanose) или натрий-карбоксиметилцеллюлоза (Na-КМЦ) представляет собой натриевую соль целлюлозогликолевой кислоты в виде мелкозернистого или волокнистого порошка белого/кремового цвета, применяется в качестве стабилизатора и загустителя консистенции.
Ассоциативные загустители содержат в молекуле гидрофобные группы и поэтому могут адсорбироваться на поверхности частиц пленкообразователя, образуя в водной фазе мицеллярные ассоциативные комплексы. В результате можно добиться повышения вязкости красок с высоким содержанием пленкообразователя при средних и высоких скоростях сдвига. На рис. 2.2 схематически изображен ассоциативный механизм загустителя.
Рис. 2.2 Схема действия ассоциативного загустителя
Пеногасители ПАВ (эмульгаторы, смачивающие агенты, ассоциативные загустители), используемые при производстве ВД-ЛКМ, накапливаясь на поверхности жидкой фазы (границе раздела жидкость - воздух), понижают поверхностное натяжение системы. Это приводит к стабилизации воздушных пузырьков, образовавшихся в процессе диспергирования, перемешивания и транспортировки. Внешне этот эффект проявляется в виде пены или микропены. Воздушные пузырьки поднимаются к поверхности или в высоковязких системах остаются внутри жидкой фазы в виде стабильной микропены. Схема образования пузырьков пены представлена на рисунке 2.3.
Рис. 2.3 Схема образования пузырьков пены (В-воздух, С-вода)
Пузырьки воздуха, поднявшиеся к поверхности, окружены плотным эластичным двойным слоем ПАВ (рис. 2.4, а).
Стабилизированные таким образом пузырьки собираются на поверхности краски и образуют слой пены. Нанесение краски в таком виде приводит к образованию дефектов покрытия. Для предотвращения этого нежелательного явления необходимо использовать пеногасители.
Пеногасители - это жидкости с низким поверхностным натяжением, которые могут разрушать поверхностную пленку или стабилизирующий двойной слой, позволяя воздуху выходить из массы краски. Пеногаситель должен легко вводиться в жидкий слой и дестабилизировать пленку ПАВ. Распространяясь внутри этого слоя, он как жесткий монослой разрушает пузырек пены (рис.2.4.б).
В настоящее время наиболее используемыми являются пеногасители на основе минеральных и силиконовых масел. Пеногасители на основе минеральных масел недороги, но их активность ниже, чем более дорогих продуктов на основе силиконовых масел. Высокоактивные пеногасители, содержащие силикон, требуют очень тщательного выбора марки и количества, так как они могут вызывать образование дефектов покрытия (кратеры, «рыбий глаз», ячейки Бенарда). При добавлении очень мелких гидрофобных частиц, например силикагеля или воска в жидкий пеногаситель, можно повысить его активность (рис. 2.4.с). Благодаря высокому сродству ПАВ к добавляемым частицам пеногасителя, способного полностью устранить пенообразование в ВД-ЛКМ. Поэтому для каждой рецептуры необходим тщательный экспериментальный подбор типа и количества пеногасителя, а также условий его введения в композицию.
Рис. 2.4 Пузырьки пены и активность жидких и твердых пеногасителей
Консерванты и биоцидные добавки. На земле живут около 150 тысяч известных видов микроорганизмов, приспособленных для существования в водной среде при наличии в ней необходимой питательной среды.
Для бактерий и грибов питательными средами могут быть все компоненты водоразбавляемых ЛКМ: эмульсионные полимеры, поверхностно-активные вещества, диспергаторы, загустители, пеногасители, пигменты, наполнители. Так, например, производные целлюлозы, применяемые в качестве загустителей, восстанавливаются микроорганизмами до мономерных сахаридов, в результате чего вязкость красок при хранении может сильно понизиться, а пигменты образуют плотные осадки.
Признаки биопоражения: появление плесени, изменение запаха, выделение газов, расслоение эмульсии, уменьшение вязкости, ухудшение потребительских качеств продукта.
Если ВД-ЛКМ при хранении в таре заражаются микроорганизмами, это может приводить к образованию «сыворотки» (расслоению) или к изменению вязкости. Далее из-за выделения газа может повышаться давление в таре, и возникает неприятный запах. Риск заражения ВД-ЛКМ возникает при использовании природных загустителей и наполнителей. Следовательно, при хранении ЛКМ в таре необходимо использовать такие же активные водорастворимые вещества или их сочетания, как и для хранения дисперсий. В большинстве случаев микробное заражение ЛКМ происходит еще в процессе их изготовления на предприятии при наличии хотя бы одного из следующих факторов:
- микробиологически загрязненные сырье, вода или полуфабриканты;
- зараженное оборудование;
- плохая гигиена производства, неэффективные мойка и дезинфекция оборудования и помещений.
Своевременное введение консервантов и биоцидов позволяет прекратить рост и размножение микроорганизмов в системе.
Антифризы. Поскольку водные дисперсии полимеров являются системами термодинамически неустойчивыми, они далеко не всегда способны обратимо выдерживать замораживание.
Под морозостойкостью дисперсий и красок понимается способность таких систем восстанавливать первоначальные свойства после замораживания и оттаивания. О морозостойкости краски судят по числу циклов замораживания — оттаивания, которое она выдерживает без заметной коагуляции; морозостойкие краски должны выдерживать не менее 5 циклов.
В водных дисперсиях полимеров и красках на их основе всегда присутствуют водорастворимые или гидрофильные компоненты (электролиты, ПАВ, загустители и т.д.), поэтому при охлаждении ниже 0°С происходит постепенное вымораживание части дисперсионной среды и концентрирование этих компонентов в не замерзшей части воды. Полное вымораживание воды в водно-дисперсионной краске происходит обычно при температуре от -15 °С до -40 °С в зависимости от содержания и природы этих компонентов. Группы частиц в этих условиях теряют подвижность и подвергаются сжатию со стороны кристаллов льда. При этом создаются условия для возникновения необратимых контактов между частицами, т.е. для коагуляции. Для понижения температуры вымораживания в рецептуру водно-дисперсионных красок вводят антифриз, обычно этиленгликоль. Его введение повышает морозостойкость за счет увеличения содержания гидрофильных компонентов в краске. Недостатком этого пути является понижение водостойкости покрытий.
На морозостойкость могут влиять другие целевые компоненты водно- дисперсионных красок. Известно, что даже при сильном обезвоживании ионные и неионные ПАВ удерживают определенные количества воды (несколько молекул воды на одну гидрофильную группу ПАВ). Если эти ПАВ адсорбированы на поверхности дисперсных частиц, то между ними будут сохраняться жидкие прослойки. Поэтому практически все поверхностно-активные добавки водно-диспересионных красок (диспергаторы, стабилизаторы, эмульгаторы, смачиватели), а также загустители повышают морозостойкость.
Этиленгликоль представляет собой сиропообразную бесцветную прозрачную вязкую жидкость сладковатую на вкус и с незначительным запахом. Температура плавления (кристаллизации, замерзания) этиленгликоля равна минус 12,6°С, температура кипения 197,9°С, плотность при 20°С 1.11 г/см3. Этиленгликоль слабоиспаряем (малолетуч).
Синонимы этиленгликоля: гликоль, моноэтиленгликоль, 1,2-диоксиэтан, этандиол-1,2, химическая формула этиленгликоля – HO—CH2—CH2—OH. Этиленгликоль высшего сорта производится в соответствии с ГОСТ 19710-83.
Этиленгликоль растворяется в любых соотношениях в воде, спирте, ацетоне, но плохо растворим в эфире и совсем не растворим в хлороформе, в алифатических и ароматических углеводородах. Эиленгликоль обладает способностью снижать температуру замерзания водного раствора, что широко используется при производстве незамерзающих (замерзающих при отрицательных температурах!) жидкостей - теплоносителей, хладагентов, антифризов.
Водные растворы этиленгликоля (незамерзающие жидкости) кристаллизуются (замерзают) при достаточно низких температурах, поэтому очень широко применяются в качестве теплоносителя (антифриза, хладагента) в автономных отопительных системах и в системах промышленного кондиционирования общественных зданий и спортивных сооружений, различных производств, где технологически требуется поддержание в помещениях необходимой низкой температуры. При кристаллизации-замерзании водный раствор этиленгликоля принимает форму мягкой желеобразной массы, исключая при этом вероятность повреждения оборудования отопительной системы или системы промышленного кондиционирования. В зависимости от климатических режимов работы оборудования применяются теплоносители на основе водных растворов с содержанием 30%, 36%, 40%, 45%, 50%, 54% и 65% этиленгликоля, с рабочим диапазоном температур до -15°C, -20°C, -25°C, -30°C, -35°C, -40°C и -65°C соответственно и с антикоррозионными, противонакипными и противопенными присадками.
Водный раствор этиленгликоля при одной и той же концентрации имеет более низкую температуру кристаллизации (замерзания) по сравнению с водными растворами на основе пропиленгликоля. Также раствор этиленгликоля по сравнению с растворами пропиленгликоля имеет более низкую вязкость, что существенно снижает потери при циркуляции раствора этиленгликоля в системе отопления (охлаждения, кондиционирования). Раствор этиленгликоля обладает и более высокими значением и теплоемкости и теплопроводности, поэтому ему и отдается предпочтение как теплоносителю (антифризу, хладагенту) в закрытых инженерных системах.
Важнейшим теплофизическим параметром водного раствора этиленгликоля является зависимость температуры замерзания раствора от его концентрации. Эта зависимость носит нелинейный характер и температура замерзания (кристаллизации) водного раствора этиленгликоля достигает своего минимума в -65°C при концентрации 65%, затем при дальнейшем повышении концентрации до 98% температура замерзания повышается до -13°C. Концентрация, количество этиленгликоля, содержащегося в теплоносителе, формирует в основном и цену самого теплоносителя. Поэтому не целесообразно и экономически не выгодно производство и применение водных растворов этиленгликоля с концентрацией выше 70%.
Нелинейный характер зависимости температуры кристаллизации водного раствора этиленгликоля от его концентрации представлены в табл. 2.4 в виде двух функциональных зависимостей: 1) значения величины плотности водного раствора этиленгликоля в зависимости от его концентрации при температуре 20°C и 2) зависимость температуры кристаллизации водного раствора от концентрации этиленгликоля /9/.
Таблица 2.4
Влияние концентрации этиленгликоля на температуру кристаллизацию водного раствора этиленгликоля. Значения (величины) плотности раствора при температуре 20°C.
Концентрация этиленгликоля, % | Температура замерзания, °C | Плотность при 20 °C |
30% | -15 °C | 1,038 |
35% | -20 °C | 1,045 |
40% | -25 °C | 1,052 |
45% | -30 °C | 1,058 |
50% | -35 °C | 1,064 |
54% | -40 °C | 1,071 |
60% | -50 °C | 1,077 |
65% | -65 °C | 1,083 |
70% | -60 °C | 1,088 |
Смачивающие и диспергирующие добавки. Диспергирование пигментов и наполнителей в пленкообразующей системе - это сложный физико-химический процесс, во многом определяющий качество и эксплуатационную пригодность ЛКМ.
Диспергирование пигментов в пленкообразующих композициях состоит из трех процессов:
1) смачивание поверхности пигментов с удалением адсорбированных газов и заменой поверхности раздела газ - твердое тело на жидкость - твердое тело;
2) разделение агрегатов - диспергирование под влиянием расклинивающего действия адсорбционных слоев и сдвиговых механических усилий и равномерное распределение частиц пигментов во всем объеме пленкообразователя;
3)формирование адсорбционно-сольвативных межфазных слоев, препятствующих повторной коагуляции, т.е. стабилизация дисперсий.
Воздействовать на процессы смачивания и диспергирования, а также стабилизации можно с помощью поверхностно-активных веществ, к которым относятся смачивающие и диспергирующие добавки. Диспергирующие добавки, мигрируя полярными группами по твердой поверхности от одного активного центра к другому и проникая в микро- и макротрещины между отдельными частицами в агрегатах, оказывают расклинивающее действие (эффект Ребиндера), что приводит к понижению прочности пигментов и облегчению разделения агрегатов до первичных частиц. При этом диспергирующие добавки, распределяясь по поверхности частиц пигмента, удерживают их на определенном расстоянии друг от друга за счет сил электростатического отталкивания или пространственных «помех», предотвращая флокуляцию (т.е. когда частицы дисперсной фазы, имеющие адсорбционные оболочки, могут слипаться своими оболочками через прослойки межфазного адсорбционно-сольвативного слоя).
Электрическое отталкивание заключается в том, что в результате адсорбции веществ, способных диссоциировать на ионы, частицы пигмента приобретают электрический заряд. Этот заряд можно увеличить или сделать все частицы одинаково заряженными. В этом случае, благодаря действующим силам электростатического отталкивания одноименно заряженных частиц, тенденция к флокуляции значительно снижается. С увеличением толщины двойного электрического слоя, окружающего частицу, повышается стабильность пигментной дисперсии.
Этот механизм особенно эффективен для водных латексных систем. В качестве добавок в этом случае используют полиэлектролиты-высокомолекулярные вещества (полифосфаты натрия). Благодаря своей химической структуре эти соединения обладают также и смачивающим действием.
Пространственные помехи наблюдаются тогда, когда одна часть диспергатора, обладающая средством к пигменту, адсорбируется на его поверхности, а другая совместима с пленкообразователем и свободно распределяется в нем, создавая вокруг частичек пигментов оболочку, препятствующую их сближению /10/.
Смачивающими добавками являются, как правило низкомолекулярные ПАВ для границы вода - воздух. Понижение поверхностного натяжения на этой границе облегчает и ускоряет смачивание пигментов и наполнителей. Поскольку смачиватель необходимо «направить» именно на границу вода-воздух, для его выбора требуется сравнить его активность к этой границе и к границе вода-пигмент.
Кроме того, эффективное смачивание пигмента дисперсионной средой обеспечивается при понижении поверхностного натяжения в динамических условиях. Поэтому смачивающие агенты должны обладать способностью достаточно быстро диффундировать к новой или обновленной поверхности. В отличие от ПАВ, обеспечивающих агрегативную устойчивость, от смачивателя не требуется высокая поверхностная активность и прочность адсорбционной связи.
В некоторых рецептурах латексных красок функцию стабилизатора пигментных частиц выполняет загуститель. В качестве характерного примера можно привести комбинацию полифосфата натрия, обладающего хорошей диспергирующей и низкой стабилизирующей способностью, с водорастворимым эфиром целлюлозы, не обладающим диспергирующими свойствами, но выполняющим функцию коллоидного стабилизатора
Пространственные помехи наблюдаются тогда, когда одна часть диспергатора, обладающая средством к пигменту, адсорбируется на его поверхности, а другая совместима с пленкообразователем и свободна.
В большинстве рецептур воднодисперсионных лакокрасочных материалов в качестве диспергатора используется триполифосфат натрия (ТПФН) и полифосфат натрия. Диспергирующее действие фосфатов объясняется их способностью связывать ионы Са2+ и Mg2+ присутствующих в воде, которые являются сильными флоккулирующими агентами для отрицательно заряженных ионно-стабилизированных дисперсий:
3 Са2++ 2Р043-=Са3(Р04)2
3 Мg2+ + 2РО =Мg3(РО4)2↓
Полифосфаты. Линейные сшитые поли - или олигофосфаты (длина цепи 2—6 фосфатных звеньев) образуют комплексы с ионами щелочно-земельных металлов или более тяжелыми ионами и, таким образом, противодействуют неблагоприятному влиянию жесткости воды в процессе смачивания.
При повышенной температуре в процессе диспергирования или при хранении полифосфаты могут гидролизоваться до монофосфатов, в результате чего теряется их стабилизирующее действие. Некоторые фосфаты, например фосфат кальция, в процессе хранения красок могут осаждаться, образуя кристаллиты.
В отечественной практике чаше всего используют полифосфат натрия, однако его применение более оправдано в производстве недорогих материалов.
Рекомендации по применению диспергаторов. Количество диспергатора в рецептуре ЛКМ определяют по минимальной вязкости и/или седиментации пигментных паст с различным содержанием диспергирующей добавки. Так как диспергатор может взаимодействовать с пленкообразователем, влияя на качество покрытия (например, на показатель мокрого истирания), необходимо подбирать не только его количество, но и марку дисперсии, с которой его можно использовать. Обычно диспергатор применяют в количестве 0,25—0,8% от массы пигмента и наполнителя/11/.
1.5 Разбавители
Роль разбавителя в водно-дисперсионных ЛКМ играет вода. К воде предъявляются определенные требования. Она должна быть по возможности более чистой и не содержать растворенных солей. Растворенные соли резко снижают стабильность полимерных дисперсий, вызывая коагуляцию и последующее расслоение лакокрасочного материала /12/.
эмаль технологический экологический экономический
Материальный расчет
Материальный расчет сводится к составлению материального технологического процесса. Целью материального расчета является определение расходных норм по сырью на единицу массы готовой продукции (на 1 тонну), определение состава и расчет количества отходов производства, выбросов в атмосферу и сточных вод. По данным материального баланса рассчитывают и обосновывают потребность цеха в сырье и полуфабрикатах. Суточную, часовую потребность цеха в сырье и полуфабрикатах используют при расчете количества единиц оборудования необходимо для установки в цехе заданной производительности.
На данном производстве потери составляют 7 кг/т. В проектируемом производстве потери сокращаются до 4 кг/т. Это достигается за счет использования более современного оборудования (погружной бисерной мельницы, патронного фильтра и фасовочной линии), механизации и автоматизации технологических операций.
Сравнение производственных и проектируемых потерь сырья на производство1 тонны краски ВД-ВА интерьерной приведено в табл. 3.1.
Таблица 3.1
Производственные и проектируемые потери сырья на производство 1 тонны краски ВД-ВА интерьерной
Наименование стадии | Нормы потерь | |||
На предприятии % | кг/т | В проектируемом производстве | кг/т | |
1. Фасовка краски в тару | 0,1 | 1 | 0,06 | 0,6 |
2. Фильтрация краски | 0,25 | 2,5 | 0,18 | 1,8 |
3. Составление краски | 0,05 | 0,5 | 0,03 | 0,3 |
4. Преддиспергирование и диспергирование пигментной суспензии | 0,2 | 2 | 0,1 | 1 |
5. Хранение и загрузка сырья | 0,1 | 1 | 0,03 | 0,3 |
Итого | 0,7 | 7 | 0,4 | 4 |
Состав краски ВД-ВА интерьерной представлен в таблице 3.2.
Таблица 3.2
Процентное содержание компонентов в краске ВД-ВА интерьерной
№ п/п | Наименование компонентов | Количество компонента в рецептуре, кг | Процентное содержание, % |
1 | Дисперсия ПВА | 109 | 10,9 |
2 | Мел | 200 | 20,0 |
3 | Микрокальцит | 200 | 20,0 |
4 | Двуокись титана | 60 | 6,0 |
5 | ТПФ натрия | 5 | 0,5 |
6 | Антисептик | 5 | 0,5 |
7 | Пеногаситель | 5 | 0,5 |
8 | Этиленгликоль | 5 | 0,5 |
9 | Уайт-спирит | 1 | 0,1 |
10 | Загуститель | 3 | 0,3 |
11 | Каолин | 60 | 6,0 |
12 | Вода | 342 | 34,2 |
13 | Карбамид | 5 | 0,5 |
Итого | 1000 | 100,0 |
Фасовка краски
На данной стадии потери составляют 0,6 кг/т. Они возникают, главным образом, за счет испарения дисперсной среды и налипанием краски на внутренней поверхности дозировочных устройств.
На эту стадию с учетом потерь (0,06%) поступает краски ВД-ВА:
1000Ч1,0006=1000,6 кг/т которая содержит:
№ п/п | Наименование компонентов | Приход, кг/т | Потери |
1 | Дисперсия ПВА | 109*(1+0,06/1000)=109,06 | 0,06 |
2 | Диоксид титана | 60*1,0006=60,04 | 0,04 |
3 | Мел | 200*1,0006=200,12 | 0,12 |
4 | Микрокальцит | 200*1,0006=200,12 | 0,12 |
5 | ТПФ натрия | 5*1,0006=5,003 | 0,003 |
6 | Антисептик | 5*1,0006=5,003 | 0,003 |
7 | Пеногаситель | 5*1,0006=5,003 | 0,003 |
8 | Загуститель | 3*1,0006=3,0018 | 0,0018 |
9 | Вода | 342*1,0006=342,21 | 0,21 |
10 | Этиленгликоль | 5*1,0006=5,003 | 0,003 |
11 | Уайт-спирит | 1*1,0006=1,0006 | 0,0006 |
12 | Каолин | 60*1,0006=60,04 | 0,04 |
13 | Карбамид | 5*1,0006=5,003 | 0,003 |
Итого | 1000,6 | 0,6 |
Фильтрация краски
На этой стадии потери составляют 1,8 кг/т. Потери происходят из-за оседания краски на фильтрующих мешках.
На стадию с учетом потерь (0,18%) поступает краски:
1000,6+1,8=1002,4 кг/т которая содержит:
№ п/п | Наименование компонентов | Приход, кг/т | Потери |
1 | Дисперсия ПВА | 109*1,0018=109,196 | 0,196 |
2 | Диоксид титана | 60*1,0018=60,108 | 0,108 |
3 | Мел | 200*1,0018=200,36 | 0,36 |
4 | Микрокальцит | 200*1,0018=200,36 | 0,36 |
5 | ТПФ натрия | 5*1,0018=5,009 | 0,009 |
6 | Антисептик | 5*1,0018=5,009 | 0,009 |
7 | Пеногаситель | 5*1,0018=5,009 | 0,009 |
8 | Загуститель | 3*1,0018=3,0054 | 0,0054 |
9 | Вода | 342*1,0018=342,62 | 0,62 |
10 | Этиленгликоль | 5*1,0018=5,009 | 0,009 |
11 | Уайт-спирит | 1*1,0018=1,0018 | 0,0018 |
12 | Каолин | 60*1,0018=60,108 | 0,108 |
13 | Карбамид | 5*1,0018=5,009 | 0,009 |
Итого | 1001,8 | 1,8 |
Составление краски
Потери на этой стадии составляют 0,3 кг/т. Потери связаны с отбором проб краски для определения ее показателей и налипанием жидких компонентов на стенки аппарата.
На стадию с учетом потерь (0,03%) поступает краски:
1002,4+0,3 = 1002,7 кг/т, которая содержит:
№ п/п | Наименование компонентов | Приход, кг/т | Потери |
1 | Дисперсия ПВА | 109*1,0003=109,033 | 0,033 |
2 | Диоксид титана | 60*1,0003=60,018 | 0,018 |
3 | Мел | 200*1,0003=200,06 | 0,06 |
4 | Микрокальцит | 200*1,0003=200,06 | 0,06 |
5 | ТПФ натрия | 5*1,0003=5,0015 | 0,0015 |
6 | Антисептик | 5*1,0003=5,0015 | 0,0015 |
7 | Пеногаситель | 5*1,0003=5,0015 | 0,0015 |
8 | Загуститель | 3*1,0003=3,0009 | 0,0009 |
9 | Вода | 342*1,0003=342,103 | 0,103 |
10 | Этиленгликоль | 5*1,0003=5,0015 | 0,0015 |
11 | Уайт-спирит | 1*1,0003=1,0003 | 0,0003 |
12 | Каолин | 60*1,0003=60,018 | 0,018 |
13 | Карбамид | 5*1,0003=5,0015 | 0,0015 |
Итого | 1000,3 | 0,3 |
Дата добавления: 2018-10-25; просмотров: 246; Мы поможем в написании вашей работы! |
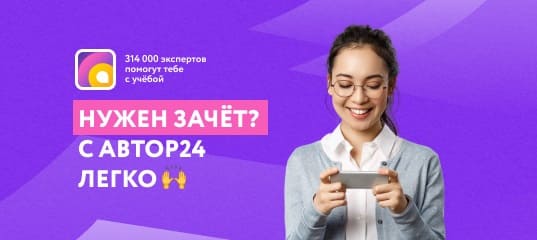
Мы поможем в написании ваших работ!