РАЗРАБОТКА ИНФОРМАЦИОННОГО И МЕТОДИЧЕСКОГО
ОБЕСПЕЧЕНИЯ УЧЕБННО-МЕТОДИЧЕСКОГО
АВТОМАТИЗИРОВАННОГО КОМПЛЕКСА
«КОМПОНОВКА СОВРЕМЕННОГО СТАНОЧНОГО ОБОРУДОВАНИЯ»
Объект исследования: этап технологической подготовки производства по выбору схемы компоновки и кинематических возможностей современного технологического оборудования.
Результаты, полученные лично автором: разработан программный модуль автоматизированной подсистемы моделирования схемы компоновки металлорежущего оборудования (программная реализация).
Под управлением станком принято понимать совокупность воздействия на его механизмы, обеспечивающие выполнение технологического цикла обработки, а под системой управления – устройство или совокупность, реализующих эти воздействия.
Прогрессивным направлением автоматизации производства является применение станков с числовым программным управлением (ЧПУ).
Благодаря оснащению многоцелевых станков (МС) устройствами с ЧПУ и автоматической смены инструмента существенно сокращается вспомогательное время при обработке и повышается мобильность переналадки. Сокращение вспомогательного времени достигается благодаря автоматическим установке инструмента (заготовки) по координатам, выполнению всех элементов цикла, смене инструмента, кантованию и смене заготовки, изменению режимов резания, выполнению контрольных операций, а также большим скоростям вспомогательных перемещений.
|
|
Применение станков с ЧПУ в сравнении с обычным оборудованием создает ряд технико-экономических преимуществ.
Главный эффект программного оборудования заключается в увеличении до 80-90% работы оборудования (15-20% у обычных станков). Обусловлено это тем, что резко сокращается вспомогательное время, время на смену инструмента и переналадку оборудования.
Разрабатываемая автоматизированная система предназначена для реализации учебно-методического автоматизированного комплекса «Компоновка современного станочного оборудования»
В качестве специального программного обеспечения при разработке автоматизированной системы расчета режимов резания была выбрана объектно-ориентированная среда программирования Visual Basic.
Для выполнения разработки необходимо выбрать следующие данные:
§ группу станка (токарные или многоцелевые сверлильно-фрезерно-расточные станки);
§ компоновку станка.
Для группы токарных станков в качестве особенностей компоновки пользователь автоматизированного модуля может указать:
§ количество шпинделей;
§ количество револьверных головок;
§ количество силовых фрезерных головок.
Для многоцелевых станков указывается (рис. 1):
|
|
§ компоновка станка (горизонтальное или вертикальное расположение оси шпинделя);
§ наличие стола-глобуса.
Рис.1 Выбор марки многоцелевого станка.
Далее осуществляется формирование отчета – результаты проделанной работы сохраняются в приложении Microsoft Office Word. При необходимости эти данные могут быть отправлены на печать.
Автоматизированная система, разработанная в данном проекте, может быть использована в работе инженеров, а также студентов при выполнении разделов выпускной квалификационной работы.
Материал поступил в редколлегию 11.04.2017
УДК 004.414
Л.С. Бравицкая
Научные руководители доценты кафедры «Технология машиностроения», к.т.н. Е.А. Польский, к.т.н. С.В.Сорокин
Sorokin.tm@mail.ru
РАЗРАБОТКА АВТОМАТИЗИРОВАННОЙ СИСТЕМЫ
РАСЧЕТА РЕЖИМОВ РЕЗАНИЯ ПРИ ПЛОСКОМ И ПЛУНЖЕРНОМ ФРЕЗЕРОВАНИИ
Объект исследования: анализпроцесса фрезерования плоских и профильных поверхностей современным металлорежущим инструментом.
Результаты, полученные лично автором: разработан модуль автоматизированной подсистемы по выбору инструмента для формирования поверхности заданного профиля и расчету технологически обоснованных режимов фрезерования (программная реализация).
|
|
Применение систем автоматизированного проектирования (САПР) охватывает сегодня самые различные виды деятельности человека — от расстановки мебели в квартире до проектирования и изготовления интегральных микросхем и современной космической техники. Каждая категория задач конструкторско-технологической подготовки производства предъявляет к этим продуктам свои требования, однако наибольшее распространение САПР получили в машиностроении.
Недостаточная оснащенность конструкторских и технологических подразделений современными САПР приводит к неполной проработке конструктивных и технологических решений, к материальным и временным потерям на стадии изготовления и во время эксплуатации. Поэтому задача создания автоматизированных подсистем технологического назначения является весьма актуальной.
В настоящее время фрезерование является широко универсальным методом обработки. В течение нескольких последних лет наряду с усовершенствованием металлорежущих станков произошло значительное расширение области применения фрезерного инструмента. Поэтому сегодня выбор способа обработки на многоцелевом оборудовании неоднозначен. В дополнение к традиционным областям использования фрез добавились такие как изготовление отверстий, обработка карманов и выборок, обработка поверхностей вращения, резьбофрезерование и т.д. Инструментальная оснастка также постоянно дорабатывается с целью повышения производительности, надежности и качества обработки.
|
|
Фреза обычно совершает резание в одном или нескольких направлениях: радиальном, периферийном и осевом. Каждый способ фрезерования можно разложить на эти три основные перемещения в сочетании с вращением фрезы.
При подготовке фрезерной операции необходимо иметь в виду следующие параметры фрезы (рис. 1): номинальный диаметр фрезы (Dc), максимальный диаметр (Dc2 или D3), эффективный диаметр (De), используемый для определения скорости резания.
Для определения скорости резания Vc при фрезеровании необходимо знать толщину стружки (hex) и код обрабатываемого материала в соответствии с классификацией ISO. Рекомендации по подачам также табулированы. Для предлагаемой фрезы анализируется угол в плане (kг).
Табличное значение скорости корректируют по твердости обрабатываемого материала. В частности, если твердость обрабатываемого материала НВ180, то по таблице нужно определить коэффициент коррекции скорости резания. Для разницы в твердости +30 единиц он составляет 0,92.
Рис. 1. Выбор исходных данных
Разработанная автоматизированная подсистема выбирает из спроектированной базы данных, представляемой в виде реляционных таблиц, вид инструмента для обработки требуемой поверхности и рассчитывает режимы резания.
Результат работы автоматизированного модуля представляются в виде приложения MSWord. При необходимости эти данные могут быть переданы в подсистему формирования технологической документации и представлены в бланках операционных карт технологического процесса.
Материал поступил в редколлегию 03.05.2017
УДК 621.75
Д.Е. Васильева
Научный руководитель: доцент кафедры «Технология машиностроения», к.т.н., Е.А. Польский
diana-032@yandex.ru
Дата добавления: 2018-10-27; просмотров: 171; Мы поможем в написании вашей работы! |
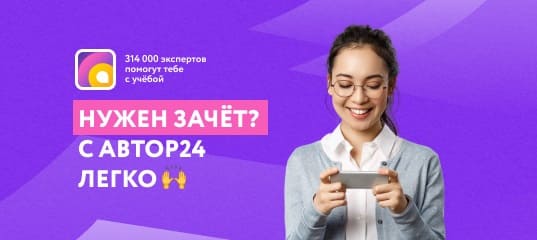
Мы поможем в написании ваших работ!