Время выдержки под пробным давлением сосудов, доизготовленных при монтаже на месте эксплуатации
Толщина стенки сосуда, мм | Время выдержки, мин |
До 50 включительно | 30 |
Свыше 50 до 100 включительно | 60 |
Свыше 100 | 120 |
Для литых, неметаллических и многослойных сосудов, независимо от толщины стенки | не менее 60 |
177. После выдержки под пробным давлением, давление снижается до обоснованного расчетом на прочность значения, но не менее рабочего давления, при котором проводится визуальный контроль наружной поверхности оборудования и всех его разъемных и неразъемных соединений.
Обстукивание стенок корпуса, сварных и разъемных соединений сосуда во время испытаний не допускается.
178. Сосуд считается выдержавшим гидравлическое испытание, если не обнаружено:
1) течей, трещин, слезок, потения в сварных соединениях и на основном металле;
2) течей в разъемных соединениях;
3) видимых остаточных деформаций;
4) падения давления по манометру.
179. Сосуд и его элементы, в которых при гидравлическом испытании выявлены дефекты, после их устранения подвергаются повторным гидравлическим испытаниям пробным давлением.
180. Результаты испытаний и значение пробного давления при испытаниях оформляются актом (в случае если испытания проведены после изготовления, ремонта или реконструкции (модернизации)) и заносятся в паспорт сосуда в порядке, установленном эксплуатирующей организацией.
181. В случаях, если проведение гидравлического испытания невозможно или нежелательно по условиям технологического процесса, гидравлическое испытание допускается заменять пневматическим испытанием (сжатым воздухом или инертным газом) при условии контроля этого испытания методом акустической эмиссии или другим методом, согласованным с эксплуатирующей организацией и организацией-разработчиком.
|
|
Величина пробного давления принимается равной величине пробного гидравлического давления с учетом гидростатического давления среды в рабочих условиях. Время выдержки сосуда под пробным давлением устанавливается организацией-разработчиком, но должно быть не менее 5 мин.
Затем давление в испытываемом сосуде должно быть снижено до расчетного и произведен осмотр сосуда с проверкой герметичности его швов и разъемных соединений мыльным раствором или другим способом, установленным в НД.
Оценка качества сварных соединений
182. В сварных соединениях сосудов и их элементов не допускаются следующие дефекты:
1) трещины всех видов и направлений, расположенные в металле шва, по линии сплавления и в околошовной зоне основного металла, в том числе микротрещины, выявляемые при микроисследовании контрольного образца;
|
|
2) непровары (несплавления) в сварных швах, расположенные в корне шва или по сечению сварного соединения (между отдельными валиками и слоями шва и между основным металлом и металлом шва);
3) подрезы основного металла, поры, шлаковые и другие включения, размеры которых превышают допустимые значения, указанные в НД;
4) наплывы (натеки) и чешуйчатость;
5) незаваренные кратеры и прожоги;
6) свищи и пористости наружной поверхности шва;
7) смещение и совместный увод кромок свариваемых элементов свыше норм, предусмотренных настоящими Правилами;
8) отклонения по геометрическим размерам и взаимному расположению свариваемых элементов;
9) несоответствие формы и размеров шва требованиям технологической документации;
10) дефекты на поверхности основного металла и сварных соединений (вмятины, расслоения, раковины).
183. Оценка качества сварных соединений сосудов и их элементов должна проводиться в соответствии с требованиями ТД и федеральных норм и правил в области использования атомной энергии, устанавливающих правила контроля основного металла, сварных соединений и наплавленных поверхностей при эксплуатации оборудования, трубопроводов и других элементов атомных станций.
|
|
Устранение дефектов в сварных соединениях
184. Дефекты, обнаруженные в процессе изготовления, монтажа и эксплуатации сосуда (в том числе при ремонте, испытаниях), должны быть устранены с последующим контролем исправленных участков. Методы и качество исправления дефектов должны обеспечивать необходимую надежность и безопасность работы сосуда.
185. Технология устранения дефектов и порядок контроля устанавливаются ТД.
Исправление дефектов следует проводить механическим способом с обеспечением плавных переходов в местах выборок. Максимальные размеры и форма подлежащих заварке выборок устанавливаются в ПКД.
Допускается применение способов термической резки (строжки) для устранения внутренних дефектов с последующей обработкой поверхности выборки механическим способом. Форма выборки должна обеспечивать возможность ее заварки.
Полнота устранения дефектов должна быть проверена визуально, методом неразрушающего контроля (капиллярной или магнитопорошковой дефектоскопией либо травлением).
186. Исправление дефектов без заварки мест их выборки допускается в случае сохранения минимально допустимой толщины стенки детали в месте максимальной выборки в соответствии с ПКД.
|
|
187. Если при контроле исправленного участка будут обнаружены дефекты, то допускается проводить повторное исправление в том же порядке, что и первое.
Исправление дефектов на одном и том же участке сварного соединения допускается проводить не более трех раз.
Не считаются повторно исправленными разрезаемые по сварному шву соединения с удалением металла шва из зоны термического влияния, устанавливаемой в соответствии с ПКД.
Документация и маркировка
188. Каждый сосуд и баллон должны поставляться организацией-изготовителем с соответствующим паспортом. Требования к содержанию паспорта сосуда и баллона приведены в приложении N 2 к настоящим Правилам .
К паспорту сосуда и баллона прилагается руководство (инструкция) по эксплуатации и расчеты на прочность (с учетом циклических и вибрационных нагрузок).
189. Элементы сосудов (корпуса, обечайки, днища, крышки, трубные решетки, фланцы корпуса, укрупненные сборочные единицы), предназначенные для изготовления, ремонта или реконструкции (модернизации), должны поставляться организацией-изготовителем с удостоверением о качестве изготовления, содержащим сведения в объеме, установленном согласно требованиям соответствующих разделов паспорта.
190. На каждом сосуде должна быть прикреплена табличка, выполненная в соответствии с ПКД. Для сосудов с наружным диаметром менее 325 мм допускается табличку не устанавливать. При этом все необходимые данные должны быть нанесены на корпус сосуда электрографическим методом, кроме сосудов, изготовленных из сталей аустенитного класса, для которых нанесение данных допускается механическим гравированием.
При проведении ремонта или модернизации сосуда с изменением его конструкции либо технических характеристик необходимо внести изменения в паспорт и табличку сосуда.
191. На табличке должны быть нанесены:
1) товарный знак или наименование изготовителя;
2) наименование или обозначение сосуда;
3) порядковый номер сосуда по системе нумерации изготовителя;
4) год изготовления;
5) рабочее давление, МПа;
6) расчетное давление, МПа;
7) пробное давление, МПа;
8) допустимая максимальная и (или) минимальная рабочая температура стенки,°С;
9) масса сосуда, кг.
Для сосудов с самостоятельными полостями, имеющими разные расчетные давления, температуру стенок, следует указывать эти данные для каждой полости.
Дата добавления: 2018-09-23; просмотров: 1274; Мы поможем в написании вашей работы! |
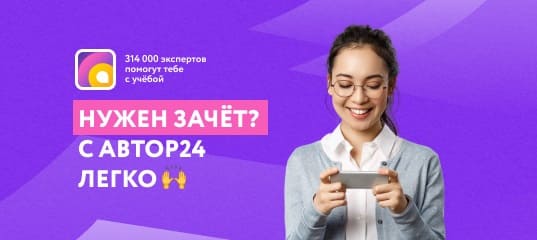
Мы поможем в написании ваших работ!