МЕТОДИКА ПОДБОРА МАТЕРИАЛОВ ПАР ТРЕНИЯ
Триботехника к настоящему времени накопила большой опыт, позволяющий сформулировать общие принципы и методику подбора материалов для пар трения. На рисунке 13 представлена схема выбора материала для трущихся деталей.
Рассмотрим подробнее отдельные этапы этой методики.
Анализ условий эксплуатации:
Условия нагружения и характеристика окружающей среды:
нагрузка и место ее приложения;
частота вращения (скорость скольжения);
режим нагружения (статический, динамический и т. д.);
ускорение;
атмосферные условия (влажность и т. д.);
температура;
вид рабочей среды и ее концентрация;
электрические воздействия;
возможность попадания инородных частиц (абразив и т.д.).
Рисунок 13 - Схема выбора материала для трущихся
Геометрические и конструктивные требования:
габариты узла;
требуемая точность;
особые требования к конструкции узла (взаимодействие с другими узлами и т.д.).
Эксплуатационные требования:
показатели надежности;
срок службы;
необходимость и возможность контроля за работой узла;
энергоемкость;
коэффициент трения;
шум;
демпфирование;
токсичность;
ионизирующие излучения;
газовыделение;
условия хранения.
Экономические и технологические требования:
объем производства;
стоимость готового изделия;
затраты энергии на производство;
производительность оборудования;
масса изделия;
внешний вид и отделка;
|
|
другие сведения.
На основе анализа условий эксплуатации составляется техническое задание на проектирование узла трения (детали).
Предварительный выбор материалов
Вначале выбирают группу материалов (черные металлы, баббиты, бронзы, полимеры и т.д.), наиболее подходящую для изготовления деталей узла трения. Затем с учетом справочных данных производят предварительный отбор материала для каждой из деталей узла трения.
Расчетно-конструктивная оценка работоспособности узла трения
Прежде всего, определяют оптимальные габариты узла трения и его конструкцию. Важным элементом геометрического расчета является установление зазоров в сопряжениях. Следует помнить, что повышенные требования к точности связаны с опасностью заклинивания при нагреве. Далее определяют нагрузочную способность детали (рассчитывают на прочность и деформацию), а затем оценивают фрикционные характеристики сопряжения (рассчитывают коэффициенты трения, определяют тепловую напряженность). И в последнюю очередь производят проверку узла трения на долговечность (рассчитывают интенсивность изнашивания). По результатам расчетов ведется конструктивная корректировка и доработка узла трения.
|
|
Окончательный выбор материала
Отобранные в результате предварительных оценок и расчетов материалы деталей пары трения необходимо экспериментально исследовать. Вначале проводят лабораторную оценку материалов на образцах, основывающуюся на применении по возможности стандартизированных методик и оборудования, выборе схем взаимодействия образцов и режимов трения, близких к эксплуатационным, в соответствии с методами моделирования. Следующий этап - испытание натурных образцов в условиях, наиболее близко имитирующих эксплуатационные. На основании испытаний натурных образцов решается вопрос о проведении опытно- промышленной проверки.
Опытно-промышленная проверка служит основным критерием окончательного выбора материала для деталей узла трения.
КОНСТРУКТИВНЫЕ СПОСОБЫ ПОВЫШЕНИЯ ИЗНОСОСТОЙКОСТИ ДЕТАЛИ
Прямая пара трения: пластическая деформация препятствует нормальной работе пары, возрастает сила трения. Пара быстро выходит из строя.
Обратная пара трения: при перегрузке пластическая деформация не препятствует работе пары (эксперимент - заедание в обратной паре при нагрузках в 15 раз больше, чем в прямой).
При конструировании пар эти особенности учитываются (рис.14).
|
|
Рисунок 14 - Конструктивные способы улучшения условий трения
К числу наиболее эффективных конструктивных способов улучшения условий трения можно отнести следующие:
снижение контактной нагруженности;
устранение возможности схватывания поверхностей;
замена сухого трения граничным, граничного трения - режимом гидродинамического или гидростатического трения;
уменьшение работы трения;
улучшение температурного режима трения;
защита узлов трения от абразивных частиц;
защита узлов трения от химических агентов внешней среды.
Защита узлов трения от абразивных частиц осуществляется с помощью различных систем масляных и воздушных фильтров, которые обеспечивают очистку масла и воздуха, поступающих к поверхностям трения.
Один из конструкторских способов повышения износостойкости узлов трения - применение герметизирующих устройств. Герметизирующее устройство (ГУ) - совокупность деталей, образующих конструкцию, предназначенную для герметизации узла трения (предотвращения утечки смазки и защиты от проникновения извне абразивных частиц).
Герметизирующие устройства делятся на подвижные и неподвижные, контактные и бесконтактные: манжеты, торцевые уплотнения, поршневые кольца, набивочные (сальниковые) уплотнения, лабиринтовые уплотнения, прокладочные герметизаторы различных типов и др.
|
|
На работоспособность любого ГУ оказывают влияние многочисленные и разнообразные по своей природе факторы, которые часто взаимосвязаны между собой.
Так, на работоспособность герметизирующих устройств влияют:
режим работы (ресурс, температура, нагрузка, скорость скольжения, условия хранения и транспортировки, наличие вибраций конструкции, пульсаций рабочих параметров и др.);
свойства герметизируемой среды;
свойства материалов сопряженных деталей и их покрытий;
технология изготовления и сборки уплотнений (способ и характер обработки поверхностей, точность изготовления и т.д.).
Дата добавления: 2018-09-22; просмотров: 805; Мы поможем в написании вашей работы! |
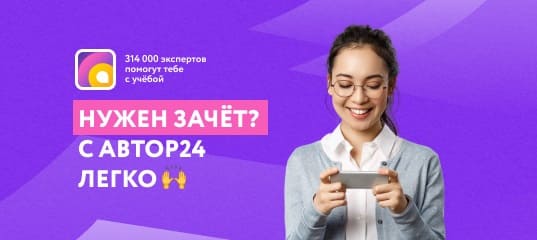
Мы поможем в написании ваших работ!