Механизм образования сервовитной плёнки
Механизмы образования сервовитной пленки различны.
Сервовитная пленка в паре «бронза-сталь» образуется при смазывании глицерином. Глицерин действует как слабая кислота, растворяя элементы бронзы, олова, цинка, железа, алюминия. Поверхность бронзы насыщается атомами меди - режим избирательного переноса (ИП).
При высоких давлениях режим ИП наблюдается в паре «бронза-сталь» в смазке ЦИАТИМ 201 и минеральных маслах в узлах трения возвратно- поступательного движения (шарниры, ползуны).
В паре «сталь-сталь» ИП может наблюдаться при смазке с добавками мелких частиц бронзы, меди, свинца, серебра и др. На поверхности появляются пленки этих металлов, коэффициент трения уменьшается, сталь не изнашивается.
Разработан ряд порошковых материалов, работающих в режиме ИП. В шихту вводятся мелкодисперсные порошки ВК3, ВК6, ВК8, где связующим веществом является медь - работает в нефти, нефтепродуктах, сточных водах.
Сервовитная пленка образуется при трении политетрафторэтилена (ПТФЭ) по стали в глицерине (с добавкой закиси меди).
В ПТФЭ (очень распространенный материал подшипников скольжения) добавляют отрезки медной проволоки (для создания режима ИП по стали).
Материал сервовитной пленки - медь находится в состоянии, подобном расплаву (рис.12). Пленка не способна к наклепу, имеет малые усилия сдвига, пориста, способна к схватыванию, при трении может переходить с одной поверхности на другую без увеличения сил трения (как сталь по льду - пленка воды - пленка медь).
|
|
Рисунок 12 - Структура граничного слоя, образующегося при трении медно-фторопластового композита по стали
Избирательный перенос в условиях абразивного износа
Считалось, что избирательный перенос может быть реализован в условиях абразивного износа - пленка разрушается. Но абразивные элементы меньше 3 мкм, наоборот - ускоряют образование пленки.
Частицы более 3 мкм изнашивают сервовидную пленку, но все же коэффициент трения относительно снижается, а интенсивность изнашивания уменьшается.
МАТЕРИАЛЫ ТРУЩИХСЯ ПОВЕРХНОСТЕЙ ПАР ТРЕНИЯ
Трущиеся детали изготавливают из материалов:
конструкционных (стали 45, 40ХН);
фрикционных (ферродо-, металлокерамика) - высокий коэффициент трения (текстолит, фибра, чугун, стали 46, 47, марганц. сталь);
антифрикционных (чугун, бронза, латунь, баббит); требования к антифрикционным материалам: достаточная статическая и динамическая прочность при повышенных температурах образования граничного слоя, низкий ƒ, прирабатываемость, технологичность, недефицитность;
износостойких (материалы в виде слоев, накладок пластин, диски фрикционных муфт) - общие требования, износостойкость обеспечивается упрочняющими технологиями (резина, пластмасса).
|
|
В одном материале все эти свойства обеспечить невозможно. Вывод: в парах трения необходимо подбирать материал; учитывать конструкцию, назначение узлов трения, условия эксплуатации, требования по прочности, сроку службы, надежности, стоимости, эксплуатационные расходы.
Примеры. Сплавы для коленчатых валов: литые дешевле кованных - из чугунов и графитизированной стали, углеродистых и легированных сталей.
Марганцовистые стали (Гатфильда) износостойкие - держат удары, наклепываются. Но при абразивном изнашивании марганцовистая сталь не имеет преимуществ перед обычными конструкционными сталями (более дешевыми), наклепывается медленнее износа, слабо сопротивляется коррозии, непригодна при эксплуатации выше 800°С.
Ретинакс (ФК-16Л), фенолформальдегидная смола, канифоль, асбест + латунная проволока - применяют при высокой нагрузке; при малой - неэффективна (повышение температуры усиливает фрикционные свойства).
Антифрикционные материалы (правило Шарля 1897 г.) - необходимо равномерно распределить в пластичной основе твердые зерна при низком коэффициенте трения с антизадирными свойствами.
|
|
Перспективны порошковые фрикционные и антифрикционные материалы. Порошковые детали выгодны при партиях 500.10000 изделий, иначе невыгодны.
Подшипники скольжения - из чугунов, применяются с остальными валами высокой твердости НRС≥55, коэффициент трения возрастает при У<0,5 м/с, удельная сила р ≤ 1,5 МПа - низкая.
Сплавы из цветных металлов - бронзы, баббиты, сплавы серебра, кадмия, алюминиевые сплавы.
Бронзы - в виде лент для втулок и подшипников типа Бр. ОЦСЧ - 4-17, Бр. АЖН.
Сплавы алюминиевые - АЛ2, АЛ4, литейный алюминий с никелем, сурьма.
Сплавы на цинковой основе - ЦАМ 9-1,5 или ЦАМ 10-15 - 9.12 % алюминия, 1.5,5 % меди, 0,03.0,06 %о магния.
Пористые порошки из спеченной бронзы, железа, графита: меди 83.85 %, олова 9.10%, свинца 4.10%, графита 1,5 .2 %. При спекании поры заполняется маслом - втулки подшипников погружаются в разогретое масло (50.100 0С). Пористость 25.35 % для больших скоростей и малых нагрузок, 18.25% - обычные условия, 10.18 % - малые скорости, высокие и средние нагрузки.
Пластмассы для подшипников:
а) полиамиды Р=5 МПа, смазка маслом;
б) полиэтилен, винипласт, фторопласт-4, коэффициент трения 0,04 без смазки - шероховатость Rа= 0,08.0,16, но размягчается. Полинозитные материалы, металлофторопластовые ленточные антифрикционные материалы (фирма «Гласье», Англия) - материал БУ.БХ. Композиция политетрафторэтила: свинец, спеченная оловянная бронза, все прикреплено к стальной подложке - работает без смазки, коэффициент трения снижается при ростер, например ƒ=0,1 при р=3 МПа;ƒ=0,04 при р=138 МПа.
|
|
ПРАВИЛА СОЧЕТАНИЯ МАТЕРИАЛОВ
Сочетать твердый материал с мягким, имеющим температуру рекристаллизации ниже средней температуры поверхности трения при работе. При таком сочетании металлы хорошо противостоят заеданию и характеризуются высокой надежностью. Хорошие результаты дают пары «хром-резина» при смазывании минеральным маслом и водой и «хром-бронза» при использовании пластичных смазочных материалов.
Сочетать твердый металл с твердым (сочетание пар из азотированной, хромированной и закаленной стали). такие пары трения обладают высокой износостойкостью вследствие малого взаимного внедрения их поверхностей. Нанесение приработочных покрытий повышает надежность пар в наиболее опасный период работы - во время приработки. Применение этих пар ограничивается скоростями скольжения. Высокая точность изготовления и сборки, значительная жесткость конструкции, тщательная приработка, улучшение условий смазывания значительно расширяют область применения пар трения из твердых материалов.
Избегать сочетаний мягкого материала с мягким (медный сплав по алюминиевому сплаву), также пар из одноименных материалов (незакаленная сталь по незакаленной стали, алюминиевый сплав по алюминиевому, хром по хрому, никель по никелю, пластмасса по пластмассе), за исключением пар из политетрафторэтилена и полиэтилена. Подобные пары имеют низкую износостойкость и ненадежны в работе. При незначительных перегрузках в парах образуются очаги схватывания, и происходит глубинное вырывание материалов с взаимным их налипанием на поверхности трения.
Применять в труднодоступных для смазывания конструкциях пористые, порошковые материалы и антифрикционные сплавы.
Применять в качестве фрикционных и антифрикционных материалов пластические пластмассы. В ряде случаев они повышают надежность и срок службы узла трения, снижают массу конструкции и расход дефицитных цветных металлов, уменьшают вибрации и улучшают акустические свойства машин.
Стремиться путем выбора материалов пары трения, смазочных материалов и присадок к ним создавать при работе пары условия реализации режима избирательного переноса.
Учитывать возможность при эксплуатации наводороживания поверхностей трения, что резко снижает износостойкость и надежность работы узла трения. Применять материалы, трудно поддающиеся наводороживанию.
Стальные детали узлов трения при окончательной доводке их поверхности подвергать финишной антифрикционной безабразивной обработке (ФАБО).
Дата добавления: 2018-09-22; просмотров: 359; Мы поможем в написании вашей работы! |
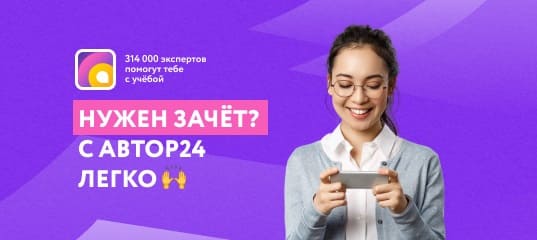
Мы поможем в написании ваших работ!