Факторы, определяющие интенсивность
Электрохимической коррозии
1. Химический состав металлического сплава. Нержавеющие стали – сплав железа с металлами, стоящими в ряду напряжений близко от железа, небольшая разность между потенциалами приводят к уменьшению скорости коррозии.
2. Структура металла в сплаве. Сплавы с однородной структурой устойчивее, чем с неоднородной. Сплав, содержащий две твердые среды, менее устойчив, чем одну твердую фазу.
3. Состояние поверхности металла. Под микроскопом видно, что поверхность металла шероховата; ионы легко отрываются от поверхности металла; не все электроны на поверхности металла компенсируются и это приводит к усилению коррозии. Поэтому производят металлы с гладкой поверхностью.
4. Механическая обработка металла. При механической обработке разрушается кристаллическая структура металла, и коррозия протекает быстрее.
5. Химический состав, свойства среды, наличие окислителей.
6. Температура. Чем выше температура, тем интенсивнее коррозия.
7. Аэрация. Участок, хуже снабжаемый кислородом, является анодом и корродирует.
Защита от коррозии
В зависимости от условий и возможностей в практике защиты металлов используются методы, основанные на одном из следующих принципов:
1) увеличение химической стойкости самого конструкционного материала;
2) снижение агрессивности технологической среды;
3) предотвращение прямого контакта с агрессивной средой путем нанесения изолирующего покрытия;
|
|
4) регулирование величины электродного потенциала защищаемого изделия – электрохимическая защита.
Наиболее надежный способ борьбы с коррозией – изготовление изделий из коррозионно-стойких материалов. Однако высокая стоимость благородных металлов практически исключает использование их, в известной мере это относится к титану и хрому. Обычно применяют легирование для создания коррозионно-устойчивых сплавов. На практике большинство изделий готовят из дешевых и доступных материалов с последующей защитой от коррозии.
Снижение агрессивности коррозионной среды достигается, либо снижением концентрации агрессивного компонента (например, применение инертной атмосферы при сварке, деаэрация водных растворов для удаления растворенного кислорода, удаление хлоридов, снижение влажности воздуха), либо введением в коррозионную среду веществ, снижающих скорость коррозии – ингибиторов. Ингибиторы, адсорбируясь на поверхности металлов, тормозят анодный или катодный процесс, или оба вместе. Они подразделяются на анодные, образующие на поверхности пленку – хроматы, нитриты, фосфаты, катодные ингибиторы (сульфаты цинка и магния, сульфит и бикарбонат натрия), которые тормозят отдельные стадии катодной реакции. Так, сульфит натрия снижает концентрацию кислорода в растворе, действуя как восстановитель. Сульфат цинка в щелочной среде снижает поверхность катодных участков за счет образования нерастворимого гидроксида цинка и т. д. Катодно-анодные ингибиторы (KВr, KI) тормозят оба электродных процесса. Часто применяются синергетические ингибирующие составы, содержащие одновременно катодные и анодные ингибиторы. Для защиты металлов и сплавов на воздухе применяются ингибиторы – контактные и летучие. Контактные ингибиторы – нитрит и бензоат натрия - используются при хранении, их наносят на металлы, погружая детали в растворы, или вводят в масла и смазки. Летучими ингибиторами, например производными циклогексиламина, пропитывают упаковочный материал; они при медленном испарении образуют тонкую адсорбционную пленку. К особому классу относятся ингибиторы-пассиваторы, приводящие к пассивации металлов. Органические ингибиторы в основном применяются при кислотном травлении металлов.
|
|
Защитные покрытия подразделяются на металлические и неметаллические. Защитное покрытие должно быть сплошным, непроницаемым, равномерным, прочным, твердым и износостойким. Металлические покрытия бывают анодными и катодными. Если потенциал покрытия более положителен, чем у защищаемого металла, такое покрытие называется катодным. Например, сталь покрывают оловом или медью. При нарушении покрытия, коррозия сильно возрастает, так как металл изделия становится анодом по отношению к металлу покрытия. К анодному покрытию (сталь покрывают цинком) требования менее высокие, так как металл изделия при нарушении целостности является катодом. Наиболее распространены неметаллические покрытия из-за меньшей стоимости. Это органические покрытия – эмали, лаки, краски, покрытия резиной, пластмассами, смазкой битумом и др. Среди неорганических покрытий распространены стекловидные эмали и дешевые покрытия из цемента. Особый класс неорганических покрытий составляют конверсионные покрытия, наносимые путем химической или электрохимической обработки металла – фосфатные и хроматные покрытия. На алюминий и его сплавы защитное покрытие наносят методом анодирования в электролите, в результате чего образуется защитная оксидная пленка.
|
|
Электрохимическая защита подразделяется на катодную и анодную.
|
|
Катодную защиту применяют для изделий, находящихся в почве и морской воде, аппаратуры химических заводов. Она осуществляется или присоединением конструкции к отрицательному полюсу внешнего источника постоянного тока, или за счет контакта изделия с массивными электродами из более отрицательного металла – протекторная защита. При протекторной защите эти электроды становятся анодами и, растворяясь, сами обеспечивают протекание катодного тока к защищаемой конструкции. В качестве таких “жертвенных” анодов используются алюминий, цинк. При использовании катодной защиты можно достичь полной защиты от коррозии, но применение ее в кислых средах экономически невыгодно, так как требует наложения больших токов и больших затрат электроэнергии.
Схема защиты от коррозии представлена на рис. 10.1. Схема катодной защиты внешним током (а): 1 – труба с покрытием; 2 – соединительные провода; 3 – источник постоянного тока; 4 – анод; Схема катодной протекторной защиты (б): 1 – стальная конструкция: 2 – протектор; 3 – наполнитель; 4 – электрический контакт с конструкцией; 5 – контрольно-измерительный вывод (Iп.з – ток протекторной защиты).
а б
Рис. 10.1
Анодная защита применима только к металлам, которые могут переходить в пассивное состояние. Ее обычно применяют для защиты аппаратуры при работе в сильно агрессивных средах. Анодная защита осуществляется присоединением защищаемого изделия к положительному полюсу внешнего источника постоянного тока или к металлу с более положительным потенциалом (катодный протектор). При этом потенциал защищаемого металла должен сместиться в область устойчивого пассивного состояния. Катоды, используемые при анодной защите, должны быть устойчивыми к агрессивной среде. Применяют платину, никель, хромоникелевые стали. В качестве катодного протектора можно использовать углеграфит, диоксиды марганца и свинца, имеющие большой положительный потенциал.
Для поддержания металла в пассивном состоянии требуется существенно меньший ток, чем при катодной защите. Скорость коррозии может быть снижена до минимума, но не до нуля, как при катодной защите. Выход из строя анодной защиты приводит к очень быстрой коррозии. Поэтому необходимо контролировать величину и направление тока и состав агрессивной среды.
Вопросы для самоподготовки
Что такое коррозия металлов?
Какие вы знаете виды коррозии?
Что такое электрохимическая коррозия?
Как влияют на коррозию металла примеси других металлов?
Где сильнее процесс коррозии металла - в речной или морской воде и почему?
Ущерб, наносимый коррозией, его размеры.
Методы борьбы с коррозией.
Металлические покрытия в борьбе с коррозией. Катодное или анодное металлическое покрытие надежнее и почему?
Дата добавления: 2018-09-22; просмотров: 378; Мы поможем в написании вашей работы! |
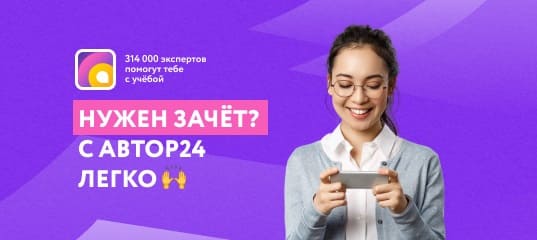
Мы поможем в написании ваших работ!