Устройство и назначение сварочного преобразователя.
Сварочный преобразователь (рис. 43) представляет собой машину, служащую для преобразования переменного тока в постоянный сварочный ток.
Он состоит из сварочного генератора постоянного тока и приводного трехфазного асинхронного электродвигателя 8, сидящих на одном валу и смонтированных в общем корпусе. Сварочный генератор состоит из корпуса 11 с укрепленными на нем магнитными полюсами 10 и приводимого во вращение якоря 12.
Рис. 43. Сварочный преобразователь
Тело якоря набрано из отдельных лакированных пластин электротехнической стали. В продольных пазах его уложены витки обмотки. Рядом с якорем находится коллектор, состоящий из большого числа изолированных друг от друга медных пластинок 1, к которым припаяны начала и концы каждой группы витков якоря.
Магнитное поле внутри генератора создается магнитными полюсами обмоток возбуждения, которые питаются постоянным током от щеток 2 самого генератора. В распределительном устройстве 4 размещены пакетный выключатель, регулировочный реостат 3, вольтметр 6, доски зажимов 5 высокого и низкого напряжения и другая аппаратура. При включении электродвигателя якорь начинает вращаться в магнитном поле и в витках его возникает переменный ток, который с помощью коллектора преобразуется в постоянный.
К коллектору прижимаются угольные щетки 2, с помощью которых постоянный ток снимается с коллектора и подводится к зажимам 5 («+» и «-»). К этим же зажимам присоединяют сварочные провода, подводящие сварочный ток к электроду и изделию. Для охлаждения преобразователя во время его работы на валу имеется вентилятор 7.
Ходовая часть преобразователя состоит из переднего поворотного колеса с тягой 9 и двух задних колес, сидящих на одной оси. Это позволяет передвигать его на небольшое расстояние. Для подъема и перемещения преобразователя предусмотрены два рым-болта.
Сварочный ток регулируется с помощью маховичка 3 реостата: при вращении его по часовой стрелке сварочный ток увеличивается, и наоборот.
|
|
Медицинские осмотры работников
Билет № 12
1. Сварочная проволока (назначение, требования, химический состав, маркировка).
Сварочная проволока (назначение, требования, химический состав, маркировка).
Для сварки сталей применяется специальная стальная проволока по ГОСТу 2246-70. Используется в основном низкоуглеродистая и низколегированная сталь. Предусмотрено 77 марок сварочной проволоки различного химического состава.
К сварочной проволоке предъявляются следующие требования:
• она должна расплавляться спокойно и равномерно;
• температура плавления должна быть меньше или равна температуре плавления основного металла;
• должна быть очищенной от ржавчины и грязи;
• должна по химическому составу соответствовать химическому составу свариваемого металла.
Условное обозначение проволоки рассмотрим на примере.
2Св-08А, где:
2 - диаметр проволоки 2 мм;
Св - сварочная проволока;
08 - 0,08% - содержание углерода;
А - повышенное качество металла.
В марке могут присутствовать две буквы АА (Св-08АА), что говорит о том, это материал проволоки особо качественный.
Под качеством понимается пониженное содержание в стали вредных примесей - серы и фосфора. Повышенное содержание углерода в проволоке приводит к снижению пластичности металла.
В марке проволоки могут присутствовать легирующие элементы (Св-12ГС; Св-15ГСТЮЦА):
Г - 1% марганца; С - 1% кремния.
Если после буквы, обозначающей легирующий элемент, не стоит цифра, то содержание этого элемента в стали до 1%. Цифра показывает содержание элемента в целых долях процента.
Условные обозначения легирующих элементов:
С - кремний
Н - никель
М - молибден
Т - титан
Ю - алюминий
Ц - цирконий
Г - марганец
X - хром
В - вольфрам
Ф - ванадий
Проволока различается по диаметру. Диаметр проволоки - от 1 до 12 мм.
Проволока диаметром от 1,6 до 6 мм применяется для ручной дуговой сварки (металлический стержень электрода). Проволока диаметром более 6 мм называется прутами и применяется для сварки чугуна и цветных металлов, наплавочных работ. Проволока диаметром от 2 до 5 мм - для автоматической сварки.
Диаметр проволоки для газовой сварки выбирается в зависимости от толщины металла и способа сварки.
Для сварки правым способом диаметр присадочной проволоки равен d=S/2.
Для сварки левым способом диаметр присадочной проволоки равен d=S/2+1.
|
|
|
|
2. Высокопроизводительные виды ручной дуговой сварки (значение, виды, техника выполнения).
Под производительностью в сварке понимают количество сварочного шва в метрах, выполненного за определенный интервал времени.
Этого можно достичь, используя различные прогрессивные приемы и усовершенствования выполнения ручной сварки (организация рабочего места сварщика, уменьшение время на переход с одной операции на другую). Все это позволяет увеличить сварщикам время горения дуги в течение рабочего времени на 10-15%, так как время смены электрода составляет 7-10% времени рабочего дня.
Чтобы увеличить производительность сварочных работ, существуют еще и специальные технические мероприятия и способы, а именно:
• сварка высокопроизводительными покрытыми электродами;
• сварка сдвоенным электродом, гребенкой электродов, трехфазной дугой;
• сварка глубоким проплавлением;
• сварка лежачим электродом;
• сварка наклонным электродом.
|
|
Рис. 33. Схема сдвоенного электрода (а), гребенки (б) и сварка трехфазным током (в, г):
1 - связка электродов; 2 - трехфазный трансформатор; 3,4 - электроды; 5 - дуга
Рассмотрим эти способы.
Сварка высокопроизводительными покрытыми электродами. Наиболее эффективны электроды с железным порошком в покрытии. Это повышает коэффициент наплавки. При сварке покрытыми электродами с железным порошком в образовании шва принимает участие не только металл электродного стержня, но и железный порошок, введенный в состав покрытия. Эти электроды должны называться высокопроизводительными.
Производительность электродов характеризуется массой электродного металла, перешедшего на изделие за единицу времени.
К этим электродам относятся электроды марок: АНО-1, ОЗС-3, АНО-19, которые при содержании 50-65% железного порошка дают 65-70 г/мин наплавленного металла (по сравнению с 23-30 г/мин для обычных электродов: АНО-4, MP-3, ОЗС-4 и др.). Однако следует учитывать, что высокопроизводительные электроды позволяют выполнять сварку только в нижнем и наклонном (угол 15-20°) положениях. Источники питания для сварки этими электродами должны иметь повышенное напряжение холостого хода.
Сварка сдвоенным электродом, гребенкой электродов, трехфазной дугой. При сварке сдвоенным электродом процесс ведут двумя стержнями, соединенными между собой контактной точечной сваркой (рис. 33, а).
Дуга переходит с одного стержня на другой, попеременно оплавляя их. Производительность сварки повышается на 20-40% по сравнению со сваркой одностержневым электродом. Это повышение достигается попеременным подогревом каждого из стержней дугой, горящей между соседними стержнями и изделием, увеличением времени горения дуги, уменьшением времени на смену электродов.
Электроды располагаются так, чтобы их общая ось совпадала с осью шва или при большой разделке кромок была перпендикулярна этой оси.
Сварочный ток составляет:
• от 100-180 А - при диаметре электродов 3+3 мм;
• 300-400 А - при диаметре 6+6 мм.
Сдвоенными электродами можно сваривать за один проход металл толщиной до 12 мм.
Электроды можно располагать по несколько стержней в ряд в виде гребенки (рис. 33, б).
Дуга возбуждается на электроде, находящемся на более близком расстоянии от свариваемого изделия. При плавлении электрода дуга переходит с одного на другой стержень и т. д.
Электродная гребенка позволяет глубоко опускаться в разделку кромок. Производительность сварки повышается вдвое по сравнению со сваркой обычным электродом.
Производительность ручной дуговой сварки можно повысить еще на большую величину, если использовать трехфазный ток (рис. 33, в).
При сварке трехфазной дугой применяют два электрода, к которым подводятся две фазы от источника питания, а третья фаза - к свариваемому изделию. В каждый данный момент в процессе изменения синусоидального тока могут гореть одна или две дуги. При этом выделяется большое количество теплоты, скорость плавления металла возрастает, и производительность сварки увеличивается на 50-60% по сравнению со сваркой однофазной дугой.
Однако при сварке трехфазной дугой сильно утяжелен электрододержатель, что ведет к утомляемости сварщика. Поэтому такую сварку лучше выполнять механизированными способами.
Сварка глубоким проплавлением. Этот вид сварки еще называют сваркой опиранием.
Для сварки применяют электроды с увеличенной толщиной покрытия. Стальной стержень электрода плавится несколько быстрее покрытия, в результате чего на конце электрода из покрытия образуется втулка (козырек). Опирая втулку электрода на поверхность изделия, сварщик перемещает дугу вдоль шва.
Образующиеся при плавлении покрытия газы своим давлением вытесняют жидкий металл из сварочной ванны, образуя валик, изделие проплавляется на большую величину, чем при сварке электродом на весу. При этом объем наплавленного металла в сварном шве значительно уменьшается без снижения прочности шва.
Этот способ сварки позволяет уменьшать глубину разделки кромок и сваривать металл значительной толщины без разделки кромок с большой скоростью. Сварку выполняют без колебательных поперечных движений электрода.
Техника сварки опиранием заключается в том, что после зажигания дуги сварщик устанавливает электрод под углом 70-80° к плоскости изделия, опускает покрытие электрода на поверхность изделия, и дуга автоматически будет перемещаться по оси шва.
Способ сварки опиранием особенно целесообразно применять при выполнении угловых швов в положении в «лодочку», используя для этого электроды марки ОЗС-3.
Сварку опиранием в вертикальном положении по направлению сверху вниз можно выполнять электродами АНО-9.
Сварка наклонным электродом (рис. 34, а).
Электрод опирается краем покрытия о свариваемый металл. Второй конец электрода зажат в обойме, которая во время сварки свободно опускается, скользя по штанге. Угол наклона электрода остается постоянным. Дуга возбуждается так же, как и при сварке лежачим электродом.
Производительность труда сварщика при использовании этих способов возрастает, так как один сварщик может работать сразу на нескольких постах.
Для сварки наклонным и лежачим электродом необходимы специальные электроды марок ОЗС-12, ОЗС-15Н (наклонный электрод), ОЗС-17Н. Электроды изготовляют диаметрами 4, 5, 6 мм и длиной от 450 до 700 мм.
Сварка лежачим электродом (рис. 34, б).
В разделку свариваемых деталей укладывают один или несколько электродов, длина которых обычно в два раза больше стандартных. От вытекания металла при выполнении стыкового шва предохраняет медная подкладка. При выполнении углового шва подкладка не требуется. Сверху электроды прижимаются к кромкам деталей медной или бронзовой колодкой. Дуга возбуждается вспомогательным электродом и затем продолжает гореть, расплавляя электрод и основной металл. Длина дуги равна толщине покрытия, составляющей 1,5-3,0 мм.
Сварку лежачим электродом можно осуществлять и под слоем флюса. Она может применяться для выполнения как прямолинейных, так и криволинейных швов, для чего необходимы специальные приспособления.
Рис. 34. Схема сварки:
а - наклонным электродом: 1 - электрод; 2 - обойма; 3 - штанга;
б - лежачим электродом: 1 - шов; 2 - дуга; 3 - лежачий электрод; 4 - свариваемый металл
3. Газовые шланги (рукава) (назначение, классификация, требования техники безопасности).
Рукава служат для подвода газа к горелке или резаку. Рукава, применяемые при газовой сварке и резке, должны обладать достаточной прочностью, выдерживать определенное давление, быть гибкими и не стеснять движений сварщика.
Согласно ГОСТу 9356-75, рукава делают из вулканизированной резины с тканевыми прокладками.
Кислородные рукава имеют внутренний и наружный слой из вулканизированной резины и несколько слоев из льняной или хлопчатобумажной ткани.
В зависимости от назначения резиновые рукава для газовой сварки и резки металлов подразделяют на следующие классы:
• I - для подачи ацетилена, городского газа, пропана и бутана под давлением до 0,63 МПа;
• II - для подачи жидкого топлива (бензина, уайт-спирита, керосина или их смеси) под давлением до 0,63 МПа;
• III - для подачи кислорода под давлением до 2 МПа.
Внутренний диаметр рукавов равен 6,3; 8,0; 9,0; 10,0; 12,0; 12,5; 16,0 мм.
Рукава поставляют длиной 10 и 14 м.
В зависимости от назначения наружный слой рукава окрашивают в следующие цвета:
• красный - рукава I класса;
• желтый - рукава II класса;
• синий - рукава III класса.
Рукава предназначаются для работы при температуре от +50 до -35°С (238°К), для более низкой температуры изготовляют рукава из морозостойкой резины, выдерживающей температуру до -65°С (208°К).
Все рукава должны иметь не менее чем трехкратный запас прочности при разрыве гидравлическим давлением. Рукава II класса должны быть бензостойкими.
Для нормальной работы горелкой или резаком длина рукавов не должна превышать 20 м, при использовании более длинных рукавов значительно снижается давление газа.
В монтажных условиях рукава можно удлинять до 40 м, на использование более длинных требуется специальное разрешение.
Для удлинения кислородных рукавов служат латунные, а ацетиленовых - стальные ниппели, снаружи закрепляющиеся специальными хомутами. Запрещается применение ниппелей для соединения рукавов, по которым проходит бензин или керосин, так как горючее может просочиться в соединение.
Количество соединений рукавов не более трех.
Рукава необходимо надежно крепить на горелках, резаках, редукторах, бачках жидкого горючего. Хранят рукава в помещении при температуре от 0 до +25°С.
Дата добавления: 2018-08-06; просмотров: 1007; Мы поможем в написании вашей работы! |
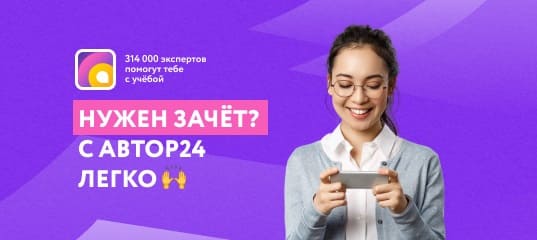
Мы поможем в написании ваших работ!