Температура плавления металла должна быть выше температуры его воспламенения в кислороде.
(Для Ст.3 температура плавления -1539°С,
а температура воспламенения – 1100-1200°С.)
Углерод заметно снижает температуру плавления. Поэтому высокоуглеродистые стали и чугуны резать обычным резаком невозможно.
Температура плавления металла должна быть выше температуры плавления его окислов.
Иначе пленка окислов будет препятствовать доступу
кислорода к металлу и горения (резки) не будет. (Окисел хрома имеет
температуру плавления 2270°С, а температура плавления для Ст.3 -1539°С).
Окислы, образующиеся при резке должны быть достаточно жидкотекучими.
При их избытке они налипают на кромки реза, и удалить их очень
трудно (Окислы кремния, хрома и др. обладают высокой вязкостью).
Металл должен плохо проводить тепло, иначе тепла от пламени будет недостаточно, чтобы нагреть кромку перед началом резки.
Технология кислородной резки
Процесс кислородной резки представлен на рисунке ниже.
Разрезаемый металл предварительно нагревается подогревающим пламенем резака, которое образуется в результате сгорания горючего газа в смеси с кислородом. При достижении температуры воспламенения металла в кислороде, на резаке открывается вентиль чистого кислорода (99–99,8%) и начинается процесс резки. Чистый кислород из центрального канала мундштука, предназначенный для окисления разрезаемого металла и удаления оксидов, называют режущим в отличие от кислорода подогревающего пламени, поступающего в смеси с горючим газом из боковых каналов мундштука.
|
|
Струя режущего кислорода вытесняет в разрез расплавленные оксиды, которые, в свою очередь, нагревают следующий слой металла, способствуя его интенсивному окислению и т. п. В результате разрезаемый лист подвергается окислению по всей толщине, а расплавленные оксиды удаляются из зоны резки под действием струи режущего кислорода.
На качество резки влияет:
- расход кислорода
Недостаток кислорода приводит к неполному окислению
металла и не интенсивному удалению окислов; а избыток – к охлаждению и выносу тепла из зоны резки.
- чистота кислорода
Снижение чистоты влияет на качество кромок реза;
Чем ниже чистота, тем больше налипает трудноотделимого шлака на нижней кромке реза.
- мощность подогревающего пламени;
Смотри конспект!!!
4. Требования электробезопасности при выполнении электрогазосварочных работ.
Билет № 5
1. Подготовка металла под сварку.
Перед сваркой после подбора металла по размерам и маркам стали необходимо выполнить следующие операции:
• правку;
• резку;
• обработку кромок и очистку под сварку.
Кромки подготавливают термическими и механическими способами.
В зависимости от толщины свариваемого металла его сварку можно вести как без разделки кромок, так и с разделкой. Разделка кромок металла начинается с 5 мм.
Существуют определенные геометрические параметры разделки кромок (рис. 13).
Обязательно в процессе сварки делают зазор b для проплавления металла на всю его толщину. Его размеры 0,5-5 мм, в зависимости от толщины свариваемого металла.
Притупление кромок с необходимо для формирования корня шва, и для того, чтобы не проплавить тонкий металл. Его размеры 2-2,5 мм.
|
|
Рис. 13. Подготовка металла под сварку
β - угол скоса кромки (15-45°);
S - толщина металла.
Разделка кромок может быть различна в зависимости от толщины металла (рис. 14). Смотри конспект!!!!
Рис. 14. Примеры подготовки кромок:
I - высота отбортовки; R - радиус закруглений; β - угол скоса кромок; α - угол разделки кромок; S и S1 - толщина металла
2. Сварочные горелки (назначение, классификация, устройство, маркировка, подготовка к работе, требования техники безопасности).
Сварочная горелка служит для смешивания горючего газа или паров горючей жидкости с кислородом и получения сварочного пламени.
Сварочные горелки подразделяются следующим образом:
• по способу подачи горючего газа и кислорода в смесительную камеру - инжекторные и безынжекторные;
• по роду применяемого горючего газа - ацетиленовые, для газов-заменителей, для жидких горючих и водородные;
• по назначению - универсальные (сварка, резка, пайка, наплавка) и специализированные (выполнение одной операции).
Инжекторная горелка (рис. 15) - эта такая горелка, в которой подача горючего газа в смесительную камеру осуществляется за счет подсоса его струей кислорода, вытекающего с большой скоростью из отверстия сопла. Этот процесс подсоса газа более низкого давления струей кислорода, подводимого с более высоким давлением, называется инжекцией, а горелки данного типа - инжекторными.
|
|
Рис. 15. Конструкция инжекторной сварочной горелки:
1 - мундштук; 2 - сменный наконечник; 3 - смесительная камера; 4 - сопло инжектора; 5 - кислородный вентиль; 6 - кислородный ниппель; 7 - ацетиленовый вентиль; 8 - ацетиленовый ниппель
Для нормальной работы инжекторных горелок необходимо, чтобы давление кислорода было 0,15-0,5 МПа, а давление ацетилена значительно ниже - 0,001-0,12 МПа.
Принцип действия ее заключается в следующем. Кислород из баллона под рабочим давлением через ниппель, трубку и вентиль 5 поступает в сопло инжектора 4. Выходя из сопла инжектора с большой скоростью, кислород создает разряжение в ацетиленовом канале, в результате этого ацетилен, проходя через ниппель 6, трубку и вентиль 7, подсасывается в смесительную камеру 3.
В этой камере кислород, смешиваясь с горючим газом, образует горючую смесь. Горючая смесь, выходя через мундштук 1, поджигается и, сгорая, образует сварочное пламя. Подача газов в горелку регулируется кислородным вентилем 5 и ацетиленовым 7, расположенными на корпусе горелки. Сменные наконечники 2 подсоединяются к корпусу горелки накидной гайкой.
Безынжекторная горелка - это такая горелка, в которой горючий газ и подогревающий кислород подаются примерно под одинаковым давлением 0,05-0,1 МПа. В них отсутствует инжектор, который заменен простым смесительным соплом, ввертываемым в трубку наконечника горелки.
Правила обращения с горелками:
1. Не допускается эксплуатация неисправных горелок, так как это может привести к взрывам и пожарам, а также ожогам газосварщика.
2. Исправная горелка дает нормальное и устойчивое свариваемое пламя.
3. Для проверки инжектора горелки к кислородному ниппелю подсоединяют рукав от кислородного редуктора, а к корпусу горелки - наконечник. Наконечник затягивают ключом, открывают ацетиленовый вентиль и кислородным редуктором устанавливают необходимое давление кислорода соответственно номеру наконечника.
Пускают кислород в горелку, открывая кислородный вентиль. Кислород, проходя через инжектор, создает разрежение в ацетиленовых каналах и ацетиленовом ниппеле, которое можно обнаружить, приставляя палец руки к ацетиленовому ниппелю.
При наличии разряжения палец будет присасываться к ниппелю. При отсутствии разряжения необходимо закрыть кислородный вентиль, отвернуть наконечник, вывернуть инжектор и проверить, не засорено ли его отверстие.
При засорении его необходимо прочистить, при этом надо проверить также отверстия смесительной камеры и мундштука. Убедившись в их исправности, повторяют испытание на подсос (разрежение).
4. Величина подсоса зависит от зазора между концом инжектора и входом в смесительную камеру. Если зазор мал, то разрежение в ацетиленовых каналах будет недостаточным, в этом случае следует несколько вывернуть инжектор из смесительной камеры.
5. Вначале немного открывают кислородный вентиль горелки, создавая тем самым разрежение в ацетиленовых каналах. Затем открывают ацетиленовый вентиль и зажигают горючую смесь.
6. Пламя регулируют ацетиленовым вентилем при полностью открытом кислородном.
7. При хлопках сначала перекрывают ацетиленовый, а потом кислородный вентили.
8. Причины хлопков:
• сильный перегрев горелки;
• засорение мундштука горелки;
• если скорость истечения горючей смеси станет меньше скорости ее сгорания, то пламя проникнет в канал мундштука и произойдет обратный удар.
9. В этом случае горелку нужно погасить, охладить ее водой и прочистить мундштук иглой.
|
|
3. Сварочные полуавтоматы (назначение, классификация, устройство, требования техники безопасности)
При механизированной сварке используют специальные сварочные аппараты, обеспечивающие механизированную подачу сварочной проволоки, а перемещение дуги вдоль оси шва выполняется вручную. Такие аппараты получили название полуавтоматов для дуговой сварки.
Полуавтоматы классифицированы по разным признакам:
• по способу защиты сварочной зоны - для сварки под флюсом, в среде защитных газов, открытой дугой;
• по способу регулирования дуги - в основном применяют полуавтоматы с саморегулированием дуги;
• по виду применяемой проволоки - сплошной, порошковой или комбинированной;
• по способу подачи проволоки - толкающего, тянущего и комбинированного типа;
• по конструктивному исполнению - со стационарным, передвижным и переносным подающим устройством.
Для сварки выпускают полуавтоматы, рассчитанные на номинальные токи 150-600 А, для проволоки диаметром 0,8-3,5 мм со скоростями подачи 1,0-17,0 м/мин.
В комплект полуавтоматов обычно входят:
• подающее устройство с кассетами для электродной проволоки;
• шкаф управления;
• сварочные горелки;
• провода для сварочной цепи и цепей управления;
• газовая аппаратура.
Устройство и основные узлы полуавтоматов. При механизированной сварке сварочная головка чаще всего разделена на две части - подающий механизм и держатель (при сварке в защитных газах – сварочная горелка), соединенные между собой гибким шлангом. Поэтому такие аппараты иногда называют шланговыми.
Полуавтоматы позволяют сочетать преимущества автоматической сварки с универсальностью и маневренностью ручной.
Типовая схема полуавтомата показана на рис. 54. В их состав входят узлы: держатель 1, гибкий шланг 2, механизм подачи сварочной проволоки 3, кассета со сварочной проволокой 4 и аппаратный шкаф, или шкаф управления 5.
Наиболее ответственным элементом полуавтоматов является механизм подачи проволоки. Его назначение и компоновка примерно те же, что и у сварочных головок автоматов для дуговой сварки. Обычно она состоит из электродвигателя, редуктора и системы подающих и прижимных роликов. Механизм обеспечивает подачу электродной проволоки по гибкому шлангу в зону сварки.
Рис. 54. Схема полуавтомата для дуговой сварки
Приводом могут служить двигатели переменного или постоянного тока.
Скорости подачи в первом случае изменяют ступенчато-сменными шестернями, во втором – происходит плавное регулирование за счет изменения частоты вращения двигателя.
Конструктивное оформление механизма подачи во многом зависит от назначения полуавтомата. В полуавтоматах для сварки проволокой большого диаметра механизм подачи размещен на передвижной тележке и располагается в отдельном корпусе. В полуавтоматах с проволокой малого диаметра он установлен в переносном футляре и расположен непосредственно на корпусе держателя.
Наибольшее распространение получили полуавтоматы толкающего типа. Подающий механизм подает проволоку путем проталкивания ее через гибкий шланг к горелке. Устойчивая подача в этом случае возможна при достаточной жесткости электродной проволоки.
В полуавтоматах тянущего типа механизм подачи или его подающие ролики размещены в горелке. В этом случае проволока протягивается через шланг. Такая система обеспечивает устойчивую подачу мягкой и тонкой проволоки.
Имеются полуавтоматы с двумя синхронно работающими механизмами подачи, осуществляющими одновременно проталкивание и протягивание проволоки через шланг (тянуще-толкающий тип).
Гибкий шланг в полуавтоматах предназначен для подачи электродной проволоки, сварочного тока, защитного газа, а иногда и охлаждающей воды к горелке. С этой целью применяют шланговый провод специальной конструкции.
Сварочные горелки предназначены для подвода к месту сварки электродной проволоки, сварочного тока и защитного газа или флюса, а также для ручного перемещения и манипулирования им в процессе сварки.
При этом сварщик удерживает держатель в руке и перемещает его вдоль шва. Быстро изнашивающимися частями держателя (при сварке в защитных газах - горелками) являются токоподводящий наконечник и газовое сопло, изготовляемые из меди.
При сварке под флюсом на держателе устанавливается бункер для флюса (рис. 55).
В полуавтомате используются приводы, работающие как на переменном, так и постоянном токе.
Рис. 55. Держатель полуавтомата для сварки под флюсом:
1 - наконечник; 2 - бункер для флюса; 3 - сварочная проволока; 4 - ручка; 5 - шланг
Техническое обслуживание полуавтоматов для дуговой сварки. Для обеспечения бесперебойной и длительной работы полуавтоматов, а также для своевременного устранения мелких неисправностей при их эксплуатации необходимо проводить профилактические работы.
Ежедневно перед началом работы следует:
• проверить состояние наконечника мундштука и газового сопла. При загрязнении очистить от брызг и нагара, восстановить надежный контакт;
• проверить место крепления мундштука к шланговому кабелю;
• проверить крепление сварочной, горелки к шланговому кабелю, осмотреть изоляцию проводов;
• опробовать работу полуавтомата пробными включениями пусковой пробки.
Не реже одного раза в месяц:
• проверить состояние роликов подающего механизма;
• проверять уровень смазки в редукторе подающего механизма и долить в случае необходимости;
• очищать от накопившейся грязи канал, по которому подается электродная проволока.
Дата добавления: 2018-08-06; просмотров: 1338; Мы поможем в написании вашей работы! |
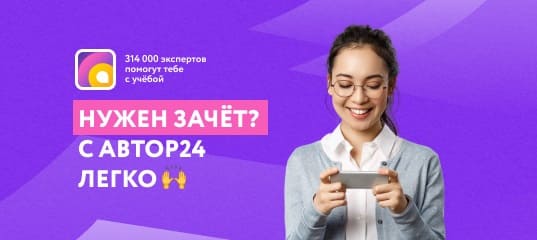
Мы поможем в написании ваших работ!