Основные виды травматизма при выполнении электрогазосварочных работ
Билет № 8
1. Устройство и назначение сварочного трансформатора.
Для дуговой сварки используют как переменный, так и постоянный сварочный ток. В качестве источника переменного сварочного тока применяют сварочные трансформаторы, а постоянного - сварочные выпрямители и сварочные преобразователи.
Источник питания сварочной дуги – сварочный трансформатор - обозначается следующим образом:
ТДМ-317, где:
Т - трансформатор;
Д - для дуговой сварки;
М - механическое регулирование;
31 - номинальный ток 310 А;
7 - модель.
Сварочный трансформатор служит для понижения напряжения сети с 220 или 380 В до безопасного, но достаточного для легкого зажигания и устойчивого горения электрической дуги (не более 80 В), а также для регулировки силы сварочного тока.
Трансформатор (рис. 22) имеет стальной сердечник (магнитопровод) и две изолированные обмотки. Обмотка, подключенная к сети, называется первичной, а обмотка, подключенная к электрододержателю и свариваемому изделию, - вторичной. Для надежного зажигания дуги вторичное напряжение сварочных трансформаторов должно быть не менее 60-65 В; напряжение при ручной сварке обычно не превышает 20-30 В.
8 нижней части сердечника 1 находится первичная обмотка 3, состоящая из двух катушек, расположенных на двух стержнях. Катушки первичной обмотки закреплены неподвижно. Вторичная обмотка 2, также состоящая из двух катушек, расположена на значительном расстоянии от первичной. Катушки как первичной, так и вторичной обмоток соединены параллельно. Вторичная обмотка - подвижная и может перемещаться по сердечнику при помощи винта 4, с которым она связана, и рукоятки 5, находящейся на крышке кожуха трансформатора.
Регулирование сварочного тока производится изменением расстояния между первичной и вторичной обмотками. При вращении рукоятки 5 по часовой стрелке вторичная обмотка приближается к первичной, магнитный поток рассеяния и индуктивное сопротивление уменьшаются, сварочный ток возрастает. При вращении рукоятки против часовой стрелки вторичная обмотка удаляется от первичной, магнитный поток рассеяния растет (индуктивное сопротивление увеличивается) и сварочный ток уменьшается. Пределы регулирования сварочного тока - 65-460 А. Последовательное соединение катушек первичной и вторичной обмоток позволяет получать малые сварочные токи с пределами регулирования 40-180 А. Диапазоны тока переключают выведенной на крышку рукояткой.
|
|
Рис. 22. Сварочный трансформатор:
а - внешний вид; б - схема регулирования сварочного тока
Свойства источника питания определяются его внешней характеристикой, представляющей кривую зависимости между током (I) в цепи и напряжением (U) на зажимах источника питания.
Источник питания может иметь внешнюю характеристику: возрастающую, жесткую, падающую.
Источник питания для ручной дуговой сварки имеет падающую вольт-амперную характеристику.
Напряжение холостого хода источника питания - напряжение на выходных клеммах при разомкнутой сварочной цепи.
Номинальный сварочный ток и напряжение – ток и напряжение, на которые рассчитан нормально работающий источник.
|
|
Способы заполнения шва по сечению.
По способу заполнения по сечению швы:
• однопроходные, однослойные (рис. 23, а);
• многопроходные многослойные (рис. 23, б);
• многослойные (рис. 23, в).
Рис. 23. Сварные швы по заполнению сечения шва
Если число слоев равно числу проходов дугой, то такой шов называют многослойным.
Если некоторые из слоев выполняют за несколько проходов, то шов многопроходный.
Многослойные швы чаще применяют в стыковых соединениях, многопроходные - в угловых и тавровых.
Для более равномерного нагрева металла шва по всей его длине швы выполняют:
• двойным слоем;
• каскадом;
• блоками;
• горкой.
В основу всех этих способов положен принцип обратно-ступенчатой сварки.
Сущность способа двойного слоя заключается в том, что наложение второго слоя производится по неостывшему первому после удаления сварочного шлака: сварка на длине 200-400 мм ведется в противоположных направлениях. Этим предотвращается появление горячих трещин в шве при сварке металла толщиной 15-20 мм, обладающего значительной жесткостью.
При толщине стальных листов 20-25 мм и более для предотвращения трещин применяют сварку:
• каскадом;
• блоками;
• поперечной горкой.
Заполнение многослойного шва для сварки горкой и каскадом производится по всей свариваемой толщине на определенной длине ступени. Длина ступени подбирается такой, чтобы металл в корне шва имел температуру не менее 200°С в процессе выполнения шва по всей толщине. В этом случае металл обладает высокой пластичностью, и трещин не образуется. Длина ступени при каскадной сварке равна 200-400 мм (рис. 24, а).
При сварке блоками многослойный шов сваривают отдельными ступенями, промежутки между ними заполняют по всей толщине слоями (рис. 24, б).
При соединении деталей из закаливающихся при сварке сталей рекомендуется применять сварку блоками. Из незакаливающихся (низкоуглеродистых) сталей - лучше выполнить сварку каскадом.
|
|
|
|
Рис. 24. Заполнение шва по сечению:
а - каскадом; б – блоками
Рис. 25. Сварка горкой
Таким образом, выполняют сварку (заполнение разделки) в обе стороны от центральной горки короткими швами. Каскадный метод является разновидностью метода горки.
При сварке методом горки (рис. 25) на участке 200-300 мм накладывают первый слой, после очистки его от шлака на него накладывают второй слой, по длине в 2 раза больший, чем первый. Затем, отступив от начала второго слоя на 200-300 мм, производят наплавку третьего слоя и т. д.
3. Баллоны для сжатых и сжиженных газов (типы, давление, окраска, надписи на баллонах, требования техники безопасности).
Для хранения и транспортировки сжатых, сжиженных и растворенных газов, находящихся под давлением, применяют стальные баллоны. Баллоны имеют различную вместимость - от 0,4 до 55 дм3.
Баллоны представляют собой стальные цилиндрические сосуды, в горловине которых имеется конусное отверстие с резьбой, куда ввертывается запорный вентиль. Для каждого газа разработаны свои конструкции вентилей, что исключает установку кислородных вентилей на ацетиленовый баллон, и наоборот.
На горловину плотно насаживают кольцо с наружной резьбой для навертывания предохранительного колпака, который служит для предохранения вентиля баллонов от возможных ударов при транспортировке.
Баллоны для сжатых, сжиженных и растворенных газов изготовляют из бесшовных труб углеродистой и легированной стали. Для сжиженных газов при рабочем давлении не свыше 3 МПа допускается применение сварных баллонов. Требования к баллонам регламентируют правила Гостехнадзора России.
В зависимости от рода газа, находящегося в баллоне, баллоны окрашивают снаружи в условные цвета, а также соответствующей каждому газу краской наносят название газа.
Например, кислородные баллоны окрашивают в голубой цвет, а надпись делают черной краской, ацетиленовый - в белый и красной краской, водородные - в темно-зеленый и красной краской, пропан - в красный и белой краской.
Часть верхней сферической части баллона не окрашивают и выбивают на ней паспортные данные баллона: тип и заводской номер баллона, товарный знак завода-изготовителя, масса порожнего баллона, вместимость, рабочее давление и дату следующего испытания.
Баллоны периодически через каждые пять лет подвергают осмотру и испытанию.
Кислородные баллоны. Для газовой сварки и резки кислород доставляют в стальных кислородных баллонах.
Кислородный баллон (рис. 53, а) представляет собой стальной цельнотянутый цилиндрический сосуд 3, имеющий выпуклое днище 1, на которое напрессовывается башмак 2. Вверху баллон заканчивается горловиной 4.
Рис. 53. Баллоны:
а - кислородный; б - ацетиленовый
В горловине имеется конусное отверстие, куда ввертывается запорный вентиль 5.
На горловину для защиты вентиля навертывается предохранительный колпак 6.
Наибольшее распространение при газовой сварке и резке получили баллоны вместимостью 40 дм3.
Эти баллоны имеют размеры:
• наружный диаметр - 219 мм;
• толщина стенки - 7 мм;
• высота - 1 390 мм;
• масса баллона без газа - 67 кг.
Они рассчитаны на рабочее давление 15 МПа, а испытательное - 22,5 МПа.
На сварочном посту кислородный баллон устанавливают в вертикальном положении и закрепляют цепью или хомутом. Для подготовки кислородного баллона к работе отвертывают колпак и заглушку штуцера, осматривают вентиль, чтобы установить, нет ли на нем жира или масла, осторожно открывают вентиль баллона и продувают его штуцер, после чего перекрывают вентиль, осматривают накидную гайку редуктора, присоединяют редуктор к вентилю баллона, устанавливают рабочее давление кислорода регулировочным винтом редуктора.
По окончании отбора газа из баллона необходимо следить, чтобы остаточное давление в нем было не меньше 0,05-0,1 МПа.
При обращении с кислородными баллонами необходимо строго соблюдать правила эксплуатации и техники безопасности, что обусловлено высокой химической активностью кислорода и высоким давлением.
При транспортировке баллонов к месту сварки необходимо твердо помнить, что запрещается перевозить кислородные баллоны вместе с баллонами горючих газов.
При замерзании вентиля кислородного баллона его надо отогревать ветошью, смоченной в горячей воде.
Причинами взрыва кислородных баллонов могут быть попадание на вентиль жира или масла, падение или удары баллонов, появление искры при слишком большом отборе газа (электризуется горловина, баллона), нагрев баллона каким-либо источником тепла, в результате чего давление газа в баллоне станет выше допустимого.
Ацетиленовые баллоны. Питание постов газовой сварки и резки ацетиленом от ацетиленовых генераторов связано с рядом неудобств, поэтому в настоящее время большое распространение получило питание постов непосредственно от ацетиленовых баллонов.
Они имеют те же размеры, что и кислородный баллон (рис. 53, б).
Ацетиленовый баллон заполняют пористой массой из активированного древесного угля (290-320 г на 1 дм3 вместимости баллона) или смесью угля, пемзы и инфузорной земли. Массу в баллоне пропитывают ацетоном (225-300 г на 1 дм3 вместимости баллона), в котором хорошо растворяется ацетилен.
Ацетилен, растворяясь в ацетоне и находясь в порах пористой массы, становится взрывобезопасным и его можно хранить в баллоне под давлением 2,5-3 МПа. Пористая масса должна иметь максимальную пористость, вести себя инертно по отношению к металлу баллона, ацетилену и ацетону, не давать осадка в процессе эксплуатации. В настоящее время в качестве пористой массы применяют активированный древесный дробленый уголь (ГОСТ 6217-74) с размером зерен от 1 до 3,5 мм.
Ацетон (химическая формула СН3СОСН3) является одним из лучших растворителей ацетилена, он пропитывает пористую массу и при наполнении баллонов ацетиленом растворяет его. Ацетилен, доставляемый потребителям в баллонах, называется растворенным ацетиленом.
Максимальное давление ацетилена в баллоне составляет 3 МПа. Давление ацетилена в полностью наполненном баллоне изменяется при изменении температуры окружающей среды (табл. 6).
Таблица 6
Давление наполненных баллонов не должно превышать при 20ºС 1,9 МПа.
При открывании вентиля баллона ацетилен выделяется из ацетона и в виде газа поступает через редуктор и шланг в горелку или резак. Ацетон остается в порах пористой массы и растворяет новые порции ацетилена при последующих наполнениях баллона газом.
Для уменьшения потерь ацетона во время работы ацетиленовые баллоны необходимо держать в вертикальном положении. При нормальном атмосферном давлении и 20°С в 1 кг (л) ацетона растворяется 28 кг (л) ацетилена. Растворимость ацетилена в ацетоне увеличивается примерно прямо пропорционально с увеличением давления и уменьшается с понижением температуры.
Для полного использования емкости баллона порожние ацетиленовые баллоны рекомендуется хранить в горизонтальном положении, так как это способствует равномерному распределению ацетона по всему объему, и с плотно закрытыми вентилями. При отборе ацетилена из баллона он уносит часть ацетона в виде паров. Это уменьшает количество ацетилена в баллоне при следующих наполнениях. Для уменьшения потерь ацетона из баллона ацетилен необходимо отбирать со скоростью не более 1700 дм3/ч.
Для определения количества ацетилена баллон взвешивают до и после наполнения газом и по разнице определяют количество находящегося в баллоне ацетилена (в кг). Масса пустого ацетиленового баллона складывается из массы самого баллона, пористой массы и ацетона. При отборе ацетилена из баллона вместе с газом расходуется 30-40 г ацетона на 1 м3 ацетилена. При отборе ацетилена из баллона необходимо следить за тем, чтобы в баллоне остаточное давление было не менее 0,05-0,1 МПа.
Использование ацетиленовых баллонов вместо ацетиленовых генераторов дает ряд преимуществ, а именно:
• компактность и простота обслуживания сварочной установки;
• безопасность и улучшение условий работы;
• повышение производительности труда газосварщиков.
Кроме того, растворенный ацетилен содержит меньшее количество посторонних примесей, чем ацетилен, получаемый из ацетиленовых генераторов.
Хранение и транспортировка баллонов.
1. Транспортировка баллонов разрешается только на рессорных транспортных средствах, а также на специальных ручных тележках или носилках.
2. При бесконтейнерной транспортировке баллонов должны соблюдаться следующие требования:
• на всех баллонах должны быть до отказа навернуты предохранительные колпаки;
• кислородные баллоны должны укладываться в деревянные гнезда (разрешается применять металлические подкладки с гнездами, оклеенными резиной или другими мягкими материалами);
• кислородные баллоны должны укладываться только поперек кузова машины так, чтобы предохранительные колпаки были в одной стороне; укладывать баллоны допускается в пределах высоты бортов;
• баллоны должны грузить рабочие, прошедшие специальный инструктаж.
3. Перевозка в вертикальном положении кислородных и ацетиленовых баллонов допускается только в специальных контейнерах.
4. Совместная транспортировка кислородных и ацетиленовых баллонов на всех видах транспорта запрещается, за исключением транспортировки двух баллонов на специальной тележке к рабочему месту.
5. В летнее время баллоны должны быть защищены от солнечных лучей брезентом или другими покрытиями.
6. Баллоны в пределах рабочего места разрешается перемещать кантовкой в наклонном положении.
7. На рабочих местах баллоны должны быть прочно закреплены в вертикальном положении.
Основы пожарной безопасности
Билет № 9
1. Сварочное пламя (способы получения, виды, основные характеристики, строение).
Сварочное пламя образуется при сгорании горючего газа или паров горючей жидкости в кислороде. Пламя при резке нагревает основной металл до температуры его горения.
Наибольшее применение при газовой сварке и резке нашло кислородно-ацетиленовое пламя, так как оно имеет высокую температуру (3150°С) и обеспечивает концентрированный нагрев. Однако в связи с дефицитностью ацетилена в настоящее время получили широкое распространение (особенно при резке металлов) газы - заменители ацетилена: пропан - бутан, метан, природный и городской газы.
Все горючие газы, содержащие углеводороды, образуют сварочное пламя, которое имеет ярко различимые зоны:
• ядро;
• восстановительную зону;
• факел.
Размеры ядра зависят от состава горючей смеси, ее расхода и скорости истечения.
Диаметр канала мундштука горелки определяет диаметр ядра пламени, а скорость истечения газовой смеси - его длину.
Восстановительная (средняя) зона располагается за ядром и по своему более темному цвету заметно отличается от него. Длина ее зависит от вида пламени и достигает 20 мм. Этой зоной пламени выполняют сварку. Она имеет наиболее высокую температуру - 3140ºС в точке, отстающей на 3-6 мм от конца ядра.
От состава горючей смеси, т. е. от соотношения кислорода и горючего газа, зависят внешний вид, температура и влияние сварочного пламени на расплавленный металл.
Изменяя состав горючей смеси, сварщик или газорезчик тем самым изменяет основные параметры сварочного пламени.
В зависимости от соотношения между кислородом и ацетиленом получают три основных вида сварочного пламени (рис. 26):
• нормальное (на один объем ацетилена подают несколько больше - от 1,1 до 1,3 объема кислорода);
• окислительное (получают при избытке кислорода, на один объем ацетилена более 1,3 объема кислорода);
• науглероживающее (получают при избытке ацетилена, когда на один объем ацетилена подается 0,95 и менее объема кислорода).
Рис. 26. Виды сварочного пламени:
а - нормальное; б - окислительное; в - науглероживающее
2. Технология и техника выполнения швов в нижнем положении.
Нижние швы являются наиболее удобными для сварки, так как в этом случае капли электродного металла под действием собственного веса легко переходят в сварочную ванну, и жидкий металл не вытекает из нее. Кроме того, наблюдение за сваркой при нижнем положении шва более удобно.
Стыковые швы применяют для получения стыковых соединений.
При выполнении стыковых швов сварку ведут в четырех направлениях: слева направо, справа налево, на себя, от себя.
Наклон электрода 15-25° от вертикали.
Угловые швы применяют для получения угловых, тавровых и нахлесточных соединений.
Сварка угловых швов может производиться наклонным электродом и в «лодочку».
При сварке углового шва, нижняя плоскость которого расположена горизонтально, возможен непровар вершины угла или одной из кромок. Непровар может образоваться на нижнем листе, если начинать сварку с вертикального листа, так как в этом случае расплавленный металл стечет на недостаточно нагретую поверхность нижнего листа. На вертикальной же полке возможно образование подрезов.
Поэтому сварку таких швов начинают, зажигая дугу на нижней плоскости в точке А, отступив от границы катета 3-4 мм. Затем дугу перемещают к вершине шва, задерживают для лучшего провара корня шва, поднимают вверх, проваривая вертикальную полку (рис. 27).
Рис. 27. Выполнение углового шва
Электрод держат под углом 45° к поверхности свариваемых деталей, слегка наклоняя его в процессе сварки то к одной, то к другой плоскости.
При сварке угловым швом в «лодочку» (рис. 28) наплавленный металл располагается в желобе, образуемом двумя полками. Это обеспечивает правильное формирование шва и хороший провар кромок металла.
Рис. 28. Выполнение углового шва в «лодочку»
3. Сварка цветных металлов (медь и е сплавы, алюминий, титан).
К техническим цветным металлам относятся медь и ее сплавы - латунь и бронза, алюминий и его сплавы, титан.
Особенность сварки цветных металлов обусловлена их свойствами:
1. Температура плавления невысокая, поэтому легко получить перегрев металла, что может привести к образованию пор и изменению состава сплава.
2. Способ окисляться с образованием тугоплавких оксидов затрудняет процесс сварки, снижает физико-механические свойства шва.
3. Повышенная способность расплавленного металла поглощать газы (кислород, азот, водород) приводит к пористости шва.
4. Большая теплоемкость и высокая теплопроводность вызывает необходимость повышенного теплового режима варки и предварительного нагрева изделия перед сваркой.
5. Относительно большие коэффициенты литейного расширения и литейная усадка приводят к возникновению внутренних напряжений, деформаций, к образованию трещин в металле шва и околошовной зоны.
6. Резкое уменьшение механической прочности и возрастание хрупкости металлов при нагреве могут привести к непредвиденному разрушению изделия.
При сварке необходимо учитывать свойства каждого из металлов.
Сварка меди и ее сплавов. Особенность сварки меди заключается в следующем.
1. Медь обладает высокой теплопроводностью, большой жидкотекучестью, способностью окисляться в нагретом и особенно в расплавленном состоянии.
2. Сварка меди в значительной степени зависит от наличия в металле различных примесей: висмута, мышьяка, свинца, сурьмы.
Они практически не растворяются в меди, но образуют с ней легкоплавкие химические соединения, которые располагаются по границам зерен, ослабляя межатомные связи.
Чистая медь обладает наилучшей свариваемостью.
3. Повышенная жидкотекучесть меди затрудняет ее сварку в различных пространственных положениях, кроме нижнего.
4. Водород в присутствии кислорода оказывает отрицательное действие на свойства меди. Расплавленная медь легко окисляется, образуя оксид меди Cu2О, который легко поглощает водород и оксид углерода (Cu2О+2Н=Н2О+2Си). При охлаждении в объеме металла выделяются пузырьки паров воды и углекислого газа, которые не растворяются в меди. Эти газы, расширяясь, создают большое внутреннее давление и приводят к образованию местных трещин. Это явление получило название водородной болезни меди.
Для предупреждения болезни следует снижать количество водорода в зоне сварки, прокаливать электроды, флюсы, использовать защитные газы.
5. При сварке меди покрытыми медными электродами без подогрева возможно возникновение горячих трещин.
6. При сварке с подогревом, создающим условие медленного охлаждения, водяной пар в большинстве случаев до затвердевания металла выходит наружу, но небольшая часть водяного пара остается между слоем сварочного шлака и поверхностью металла шва.
В результате этого поверхность металла шва после удаления шлака становится неровной. Этого можно избежать при очень медленном охлаждении шва.
Виды сварки меди:
• дуговая сварка угольным электродом (неплавящимся);
• дуговая сварка плавящимся электродом;
• автоматическая сварка под слоем флюса;
• ручная аргонодуговая сварка вольфрамовым электродом (сварка в защитных газах);
• газовая сварка.
Дуговая сварка угольным электродом (неплавящимся). Применяется для малоответственных изделий. При толщине меди до 15 мм применяют угольные электроды, при больших толщинах - графитовые.
В том и другом случае в качестве присадочного материала используют прутки из меди марки М1 и БрОФ6,5-0,15.
Для предохранения меди от окисления и улучшения процесса сварки применяют флюсы, которые наносят на разделку шва и на присадочные прутки. Флюс - прокаленная бура.
Присадочный материал не погружают в ванну, а держат под углом 30° к изделию на расстоянии 5-6 мм от поверхности ванны. Электрод держат под углом 75° к изделию.
Листы толщиной до 4 мм сваривают с отбортовкой кромок без присадочного металла. При толщине более 5 мм сваривают с разделкой кромок под углом 60-90°.
Сборка под сварку должна обеспечить минимальные зазоры (до 0,5 мм), чтобы предупредить протекание расплавленного металла шва.
Рекомендуется использовать подкладки из графита, асбеста, керамики.
Сварка производится постоянным током прямой полярности.
Скорость сварки довольно большая и при возможности - за один проход.
Для электрода Ø 4...6 мм при толщине металла до 4 мм сила тока 140-320 А, для электрода Ø более 4 мм сила тока 350-500 А.
После сварки тонкие листы проковываются в холодном состоянии, а толстые (5-20 мм) - при температуре 200-400°. Подогрев до более высокой температуры не рекомендуется, так как медь становится хрупкой.
Дуговая сварка плавящимся электродом (металлическим). Подготовка кромок и обработка шва производится так же, как и при сварке угольным электродом.
При толщине металла 5-10 мм необходимы предварительный подогрев до температуры 250-300°С и Х-образная разделка.
Металлические электроды изготавливают из меди марок Ml и М2, названные «Комсомолец-100». Электроды Ø 3 мм применяются редко вследствие низкой механической прочности.
Электроды марки ЭТ Балтийского завода со стержнем из бронзы Бр.КМц3-1. Сварку ведут максимально короткой дугой.
Высокопроизводительные электроды АНЦ-1 и АНЦ-2 обеспечивают сварку без подогрева меди толщиной до 15мм.
Используют постоянный ток обратной полярности. Максимально короткая дуга, так как увеличение дуги ведет к разбрызгиванию металла и снижает механические свойства шва.
Колебательные движения отсутствуют. Сила тока определяется по формуле I=50dэ.
Ручная аргонодуговая сварка вольфрамовым электродом (сварка в защитных газах). Выполняется угольным или вольфрамовым электродом на постоянном токе прямой полярности.
Защитный газ - аргон, гелий.
Присадочная проволока марки Ml или Бр.КМц3-1.
При толщине металла более 4 мм сваривают с предварительным подогревом.
Автоматическая сварка под слоем флюса. Производится под флюсом марок ОСЦ-45, АН 348-А, АН-20. Проволока диаметром 1,6-4 мм марки Ml или Бр.КМц3-1.
Газовая сварка. Требует повышенной мощности пламени. Для листов толщиной до 10 мм мощность пламени 150 дм3/ч на 1 мм толщины металла, а свыше 10 мм - 200 дм3/ч.
Для уменьшения отвода теплоты изделие закрывают листовым асбестом.
Пламя используют строго нормальное. Избыток ацетилена вызывает образование пор и трещин, а избыток кислорода ведет к окислению металла шва.
Нагрев и плавка меди производится восстановительной зоной.
Наклон горелки - 80-90°. Сварку ведут быстро, без перерывов, за один проход.
Присадочная проволока - чистая медь или медь с раскислителем.
Диаметр проволоки от 1,5 до 8 мм, в зависимости от толщины металла.
В процессе сварки подогретый конец присадочного прута периодически обмакивают во флюс, так его переносят в сварочную ванну.
Для получения мелкозернистой структуры металл проковывают: толщиной до 5 мм - в холодном состоянии; при большой толщине - в горячем состоянии (200-300°). После производят отжиг при температуре до 550°С и охлаждают в воде. При этом шов получается более пластичным.
Сварка латуни. Латунь - это сплав меди с цинком. Сваривается теми же способами, что и медь.
Основное затруднение при сварке латуни связано с кипением и интенсивным испарением цинка, пары которого в воздухе образуют ядовитые окислы.
При дуговой сварке применяют присадочные прутки из латуни ЛМц58-2 и флюс из молотого борного шлака или буры.
При автоматической сварке используют проволоку из меди Ml и флюс АН-348А или ОСЦ-45.
При газовой сварке нормальным пламенем выделяются пары цинка, в результате чего шов получается пористым. Поэтому применяют пламя окислительное. Избыток кислорода окисляет часть цинка, и образующая на поверхности сварочной ванны оксидная пленка защищает расплавленный металл от дальнейшего окисления.
Сварка бронзы. Бронзой называется сплав меди с любым из металлов, кроме цинка. Сваривается так же, как и медь.
Сварка алюминия и его сплавов. Алюминий обладает малой плотностью, высокой тепло- и электропроводностью. Наибольшее применение получили сплавы алюминия с марганцем АМц.
Поверхность алюминия и его сплавов покрыта тугоплавкой оксидной пленкой, плавящейся при температуре 2050°С. Эта пленка очень затрудняет сплавление основного и присадочного металла. Поэтому свариваемые кромки необходимо тщательно очистить механическим или чаще всего химическим способом.
Виды сварки те же, что и меди, но используются прутки с алюминиевой основой и сварочная проволока на основе алюминия (СвА97, СвАМц).
Газовую сварку выполняют левым способом нормальным пламенем.
Сварка титановых сплавов. Титан обладает антикоррозионной стойкостью. Титан более активен по сравнению с алюминием к поглощению кислорода, азота, водорода в процессе нагрева. Поэтому при сварке технического титана необходима особо надежная защита от этих газов. Такая защита осуществляется при дуговой сварке в инертных газах и при использовании флюсов-паст, которые являются бескислородными.
Дуговая сварка титана и его сплавов покрытыми, угольными электродами и газовым пламенем не применяется. Этими видами сварки невозможно обеспечить высокое качество сварных соединений из-за слишком большой активности титана к кислороду, азоту и водороду.
Средства пожаротушения.
Билет №10
1. Дефекты швов сварных соединений (причины возникновения, способы их устранения).
Различные отклонения от установленных норм и технических требований, ухудшающие работоспособность сварных конструкций, называются дефектами сварных швов. Они уменьшают прочность сварных соединений и могут привести к их разрушению.
Все дефекты сварных швов могут быть разделены на три основные группы:
• дефекты формы и размеров;
• наружные и внутренние макроскопические дефекты;
• дефекты микроструктуры.
Наиболее частыми дефектами формы и размеров сварных швов являются их неполномерность, неравномерные ширина и высота, бугристость, седловины, перетяжки.
Эти дефекты швов косвенно указывают на возможность образования дефектов внутри сварного шва и околошовной зоны.
К наружным и внутренним макроскопическим дефектам относят наплывы, подрезы, прожоги, непровары, трещины, шлаковые включения и газовые поры (плакат).
К дефектам микроструктуры относят перегрев и пережог.
На участке перегрева металл имеет крупнозернистое строение, что ведет к хрупкости металла. Перегретый металл плохо сопротивляется ударным нагрузкам.
Наиболее опасным дефектом является пережог. Такой металл хрупок и не поддается исправлению. Причиной образования пережога является плохая защита сварочной ванны от кислорода воздуха, а также сварка на чрезмерно большом сварочном токе.
2. Ацетиленовый генератор (назначение, классификация, устройство, подготовка к обслуживанию, требования техники безопасности).
Ацетиленовый генератор служит для получения ацетилена разложением карбида; кальция водой.
Ацетиленовые генераторы классифицируются:
• по производительности - 1,25; 3; 5; 10, 20, 40, 80, 160; 320, 640 м3/ч;
• по способу применения - передвижные и стационарные;
• по давлению вырабатываемого ацетилена – низкого давления - до 0,02 МПа, среднего давления - от 0,02 до 0,15 МПа.
• по способу взаимодействия карбида кальция с водой - ВК (вода на карбид) и KB (карбид на воду).
Рассмотрим устройство генератора типа АСП-1,25-6 (рис. 29). Это переносной генератор производительностью 1,25 м3/ч, рабочим давлением 0,01-0,07 МПа. Генератор представляет собой вертикальный цилиндрический сосуд.
Корпус 5 состоит из трех частей:
• газообразовательной, в которой образуется ацетилен за счет взаимодействия кальция с водой;
• вытеснителъной;
• промывательной.
Вода заливается через горловину. При достижении уровня переливной трубки 3 вода по трубке переливается в промыватель, который заполняется до уровня контрольной пробки 2.
Карбид кальция загружают в корзину 8. Уплотнение между крышкой 12 горловиной обеспечивается мембраной 11 усилием, создаваемым винтом 13 через траверсу 14.
Ацетилен, образующийся в газообразователе, по трубке 3 поступает в промыватель, барботируя через слои воды, охлаждается и промывается. Из промывателя ацетилен через вентиль предохранительного клапана 4 по шлангу 15 поступает в предохранительный затвор 7 и далее к горелке или резаку. По мере повышения давления в газообразователе пружина 10 сжимается, в результате чего корзина перемещается вверх, а вода вытесняется в вытеснитель. В результате уровень замочки карбида уменьшается, выработка ацетилена ограничивается и повышение давления прекращается. Давление ацетилена контролирует манометр 9. Ил из газообразователя и иловую воду из промывателя сливают через штуцера 6 и 1.
Рис. 29. Устройство генератора АСП-1,25-6
Подготовка генератора к работе:
• снять крышку и поддон от корзины;
• убедиться, что корпус чист и промыт;
• проверить закрепления вентиля и предохранительного клапана;
• открыть контрольные пробки в генераторе и водяном затворе;
• залить водой водяной затвор и генератор до уровня контрольной пробки;
• закрыть контрольные пробки;
• соединить шлангом вентиль и предохранительный затвор;
• загрузить карбид кальция;
• закрепить поддон на корзине и закрыть крышку;
Основные технические характеристики генератора приведены в таблице.
Основные технические характеристики генератора
Ацетиленовый генератор снабжен предохранительным затвором.
При работе с генератором необходимо соблюдать следующие правила:
• использовать размеры карбида кальция, указанные в паспорте;
• при перерывах в работе и в зимнее время нельзя допускать замерзания воды в генераторе, для чего генераторы утепляют;
• при работе нельзя оставлять возле генератора ил, его нужно относить в специальные ямы;
• нельзя подходить с огнем или зажженной горелкой к генератору, так как возможно выделение ацетилена в окружающую среду и образование взрывчатой смеси;
• работающий генератор нельзя оставлять без надзора;
• используют генераторы на открытом воздухе;
• генератор должен находиться от кислородного баллона на расстоянии 10 м, а от других источников тепла не менее 5 м.
3. Оказание первой помощи при поражении электрическим током и ожогах.
Билет № 11
1. Понятие свариваемости металла. Классификация сталей по свариваемости.
Вопрос 1. Понятие свариваемости металла. Классификация сталей по свариваемости.
Под свариваемостью понимается способность стали данного химического состава давать при сварке тем или иным способом высококачественное сварное соединение без трещин, пор и прочих дефектов.
На свариваемость стали влияет содержание в ней углерода и легирующих элементов.
С повышением содержания углерода в стали в ней возрастают прочностные свойства, но в то же время возрастает хрупкость и склонность к образованию трещин при сварке.
Различают физическую и технологическую свариваемость.
Физической свариваемостью обладают практически все металлы и их сплавы, т. е. способностью образовывать монолитное неразъемное соединение с установлением в нем химических связей.
Под технологической свариваемостью понимается реакция металла на воздействие конкретных условий сварки и при этом возможность образовывать соединение с требуемыми свойствами.
Для предварительного суждения о свариваемости стали известного химического состава можно подсчитывать эквивалентное содержание углерода, пользуясь формулой:
Сэкв=С+Mn/20+Ni/15+(Cr+Mo+V)/10
В целом, по признаку свариваемости все стали можно условно разделить на четыре группы (см плакат).
Дата добавления: 2018-08-06; просмотров: 968; Мы поможем в написании вашей работы! |
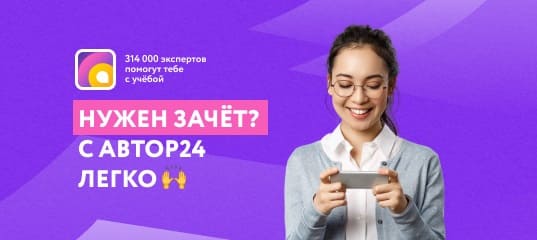
Мы поможем в написании ваших работ!