Технология изготовления поковок IV группы
При изготовлении поковок с отростками применяют штамповку в разъемных матрицах.
При выдавливании на окончательной операции необходимо предусматривать компенсационные полости для размещения избыточного объема металла. Компенсационные полости размещают в тех зонах ручья, которые заполняются в последнюю очередь. Размеры компенсационных полостей должны быть такими, чтобы обеспечить сопротивление (подпор) течению металла, необходимое для четкого заполнения ручья. В простейшем случае необходима одна штамповочная операция – выдавливание, а в более сложных – еще операция окончательной закрытой или открытой штамповки (с сохранением положения плоскости разъема во избежание заштамповки заусенцев).
При выдавливании в поперечных направлениях металл течет в отростки преимущественно по нижней части полости матрицы, как бы прижимаясь под воздействием деформирующего усилия к нижней стенке и отставая от верхней стенки. Чем больше суммарное проходное сечение поперечных полостей по сравнению с сечением контейнера, тем больший зазор образуется между верхней стенкой и металлом. Поэтому усилие раскрытия матриц с горизонтальным разъемом в стадии выдавливания невелико. Сила трения металла о стенки контейнера направлена вниз (в направлении деформирующего усилия), т.о. сжимает матрицы и значительно уменьшает величину раскрывающего усилия.
В стадии заполнения полостей (после достижения металлом торцевой стенки) усилие раскрытия матриц начинает расти, резко увеличиваясь во время заполнения кромок и компенсационных полостей. Наибольшее усилие раскрытия матриц при штамповке с горизонтальным разъемом не превышает 50 % усилия штамповки.
|
|
При выдавливании боковых отростков могут возникнуть дефекты в результате образования застойных зон или встречных потоков металла. Застойные зоны образуются в резко очерченных полостях и углублениях ручья, расположенных в стороне от траекторий течения основной массы металла. В этом случае следует применять штамповку, состоящую из 2-х операций: выдавливания бокового отростка при плавных очертаниях в застойных зонах и окончательной штамповки в разъемных матрицах или в открытом штампе в зависимости от сложности конфигурации поковки.
Если боковые отростки значительно различаются по длине, то при одновременном их выдавливании короткий отросток заполняется быстрее; в результате применяется форма очага деформации и направление течения металла (завихрения). При этом заполнении короткий стержень становится застойной зоной.
Рациональным процессом является штамповка, состоящая из 2-х операций: частичного выдавливания длинного отростка; одновременного выдавливания короткого и длинного отростков. Обе операции выполняют в закрытом штампе с разъемными матрицами.
|
|
При штамповке за 1-ну операцию поковок с боковыми отростками и центральными полостями образуются утяжины. Поэтому следует применять 2 перехода: выдавливание боковых отростков и окончательная штамповка с образованием полостей в разъемных матрицах или в открытом штампе, в зависимости от сложности формы поковки.
Определение работы деформирования и выбор оборудования
1. Усилие пресса в конце хода должно быть не менее потребного расчетного усилия деформирования, а график усилий деформирования должен вписываться в график допустимых нагрузок по ходу ползуна.
Запас работы маховика и двигателя должен быть достаточный для осуществления требуемой деформации металла с учетом допустимого коэффициента неравномерности вращения маховика.
При одновременной штамповке в нескольких ручьях в график допустимых нагрузок пресса должен вписываться суммарный график усилий деформирования в этих ручьях.
2. Число ходов в минуту и скорость движения ползуна пресса должны быть достаточны для высокопроизводительной работы и применения скоростного режима деформирования. Необходимо учитывать, что большая скорость деформирования, повышая производительность, в то же время может привести к образованию разрывов на выдавливаемом стержне и к неблагоприятной структуре металла.
|
|
3. Величина хода ползуна пресса должна обеспечивать:
а) достаточное расстояние между матрицами и пуансонами в верхнем положении для укладки исходной заготовки, перекладки полуфабриката из ручья в ручей и удаления поковки;
б) подъем заготовок из ручьев штампа на требуемую высоту в том случае, если в штампе применяется выталкивающая система.
4. Закрытая высота, размеры стола и ползуна пресса должны быть достаточными для размещения инструмента.
5. Пресс должен быть снабжен выталкивателями. Следует применять пневмомеханическую систему выталкивания, действующую синхронно с ходом ползуна или независимо от него. Она обеспечивает выдачу готовых поковок и исключает поломки выталкивателей при попадании увеличенной по объему заготовки.
Если прессы общего назначения не удовлетворяют перечисленным требованиям, следует применять прессы со специальной характеристикой.
Работа деформирования определяется площадью, ограниченной осями координат и графиком усилие-путь, который строят, откладывая в масштабе усилие деформирования при характерных положениях рабочего торца пуансона, а именно:
|
|
1) начало деформации - открытое выдавливание;
2) начало заполнения полости контейнера;
3) начало установившегося процесса закрытого выдавливания;
4) окончание процесса выдавливания, определяемое заданной высотой утолщения поковки.
Под относительным удельным давлением понимается среднее относительное нормальное напряжение , которое получается осреднением пространственной эпюра относительных нормальных напряжений
в контактной плоскости.
, (6)
где - объем пространственной эпюры относительных нормальных напряжений в контактной плоскости;
- площадь проекции поверхности контакта поковки с деформирующим инструментом на плоскость, перпендикулярную к направлению деформирующего усилия.
Удельное усилие штамповки определяется
. (7)
Усилие штамповки
, (8)
где - коэффициент, учитывающий степень приближения формоизменения к плоскому деформированию (
= 1.155) или осесимметричной деформации (
= 1).
Величина предела текучести деформируемого материала зависит от температурно-скоростных условий процесса
, (9)
где - предел текучести металла при
деформации;
- коэффициент, комплексно учитывающий упрочняющий эффект, обусловленный скоростью и неравномерностью деформации,
= 2-3 для КГШП,
= 1-1.5 – гидравлических прессов.
Дата добавления: 2018-06-01; просмотров: 332; Мы поможем в написании вашей работы! |
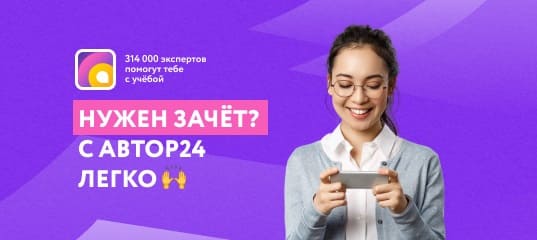
Мы поможем в написании ваших работ!