Особенности конструкции штампов закрытой штамповки
В зависимости от применяемого оборудования и плоскости разъема матриц штампы закрытой штамповки можно разделить на две группы:
1. Штампы с цельными матрицами.
2. Штампы с разъемными матрицами.
Штампы с цельными матрицами применяются для изготовления поковок типа тел вращения. Безоблойная штамповка других групп поковок возможна лишь в разъемных матрицах. Конструкция штампов с разъемными матрицами значительно усложняется и зависит от применяемого оборудования. Основным затруднением при конструировании штампов с разъемными матрицами является восприятие усилий распора. В ряде конструкций применяют рычажно-шарнирные механизмы зажима матриц, обеспечивающие автоматическое открытие и закрытие матриц, надежное сжатие их в процессе деформирования. Недостатком этой конструкции является ее сложность и необходимость большой закрытой высоты штампа для установки. Используются конструкции, в которых сжатие матриц предусматривается за счет пружинных блоков. Однако при больших усилиях распора, превышающих возможные усилия пружинных блоков, матрицы могут разомкнуться, и металл вытечет в зазор, не заполнив рабочей полости штампа.
При штамповке на прессе двойного действия конструкция штампов с горизонтальным разъемом матриц значительно упрощается. Усилие распора воспринимается непосредственно наружным ползунок пресса. Пуансон крепится и внутреннему ползуну, верхняя часть штампа – к наружному ползуну, а нижняя часть - к столу пресса. При рабочем ходе пресса наружный ползун, опережая внутренний, смыкает матрицы, и некоторое время выстаивает, обеспечивая при помощи пуансона, движущегося вместе с внутренним ползуном пресса, заполнение металлом рабочей полости штампа. Наружный ползун пресса обеспечивает надежный прижим матриц на протяжении всего рабочего хода деформирующего пуансона.
|
|
Закрытая штамповка позволяет повысить коэффициент весовой точности до 0.67...0.83, коэффициент использования металла до 0.54...0.77. Производительность повышается в 1.5...2 раза. Благодаря меньшему числу переходов и операции можно обеспечить в конце процесса деформирования необходимые для термомеханической обработки температуры, что позволяет повысить механические свойства поковок на 15...25 % по сравнению с обычной термообработкой.
Возможность штамповки поковок сложной конфигурации значительно расширит область практического применения штамповки в закрытых штампах, которая требует более высокой технической культуры производства.
ОСОБЕННОСТИ ТЕХНОЛОГИИ ГОРЯЧЕГО ВЫДАВЛИВАНИЯ
ПЛАН ЛЕКЦИИ:
1. Сущность процесса горячего выдавливания.
|
|
2. Область применения.
3. Особенности конструирования поковок.
4. Требования, предъявляемые к оборудованию и инструменту.
Сущность процесса горячего выдавливания
Выдавливанием называется операция объемной штамповки, при которой происходит истечение металла, заключенного в контейнер, под воздействием рабочего инструмента в отверстие матрица. Эта операция используется для изготовления деталей и поковок, заданных конфигураций и размеров не только по выдавленному профилю (как при прессовании), но и по остающейся в контейнере части, являющейся элементом поковки.
Надавливанием получают различные по форме элементы поковок: цилиндрические и конические, гладкие и ступенчатые, сплошные и полые, круглого и фасонного сечения. Выдавливанием можно изготовлять также детали с изогнутыми отростками.
В зависимости от направления течения металла могут быть следующие разновидности выдавливания:
1) прямое - направление течения выдавливаемого металла совпадают с направлением рабочего хода пуансона;
2) обратное - металл течет навстречу пуансону;
3) наклонное - металл течет в полость, ось которой наклонена к направлению перемещения пуансона под углом, отличным от 90°;
|
|
4) поперечное - металл течет под прямым углом к направлению движения инструмента;
5) смешанное или комбинированное, представляющее собой сочетание двух или более разновидностей выдавливания.
При выдавливании в металле в очаге деформации имеет место всестороннее неравномерное сжатие, обеспечивающее металлу наилучшие пластические свойства. Под воздействием сжимающих напряжений металл течет в направлении наибольшего градиента напряжений - от поверхности пуансона, где они имеют максимальную величину, к очку, где на свободной поверхности нормальные напряжения равны нулю. Однако не всегда во всем объеме действуют только сжимающие напряжения, в некоторых зонах действуют растягивающие напряжения.
Возникновение напряжений, различных по направлению и знаку, способствует то обстоятельство, что частицы металла перемещаются по траекториям разной длины с различной скоростью, меняющейся в процессе прохождения частицы через различные зоны матрицы.
В некоторых случаях напряжения растяжения достигают в отдельных участках заготовки значительной величины и являются причиной образования различных дефектов (прессутяжин, прострелов, трещин).
Если растягивающие напряжения не превышают предела прочности металла, то разрушения не происходит. В противном случае происходит разрушение с образованием дефектов типа трещин, разрывов, сколов на поверхности естественного конуса при наличии застойных зон.
|
|
Для оценки деформации используются показатели:
1. Коэффициент (степень) вытяжки , (1)
где - площадь наибольшего поперечного сечения утолщенного у элемента поковки;
- площадь наименьшего поперечного сечения задавленного элемента.
2. Коэффициент (степень) обжатия , (2)
где - наибольший диаметр утолщении поковки;
- наименьший диаметр стержня поковки.
3. Относительная степень деформации
. (3)
4. Логарифмическая (истинная) степень деформации
. (4)
Рассмотренные параметры характеризуют среднюю степень деформации.
Повышение степени деформации ведет к увеличению скорости течения металла и неравномерности деформации, увеличению сопротивления и росту усилия деформирования.
При малых обжатиях очаг деформации локализуется на небольшой глубине у поверхностных слоев, оставляя внутреннюю зону недеформированной, что может отрицательно сказаться на качестве детали.
При массовом производстве поковок из конструкционных сталей максимальные значения показателей степени деформации выражаются величинами:
При горячем выдавливании имеет большое значение смазка. Из жидких смазок наиболее распространены смеси минеральных или растительных масел с чешуйчатым графитом.
Применяются водные коллоидные растворы графита, водные эмульсии масла, масло с сернистым молибденом , водный раствор поваренной соли и калиевой селитры. Жидкие смазки удовлетворяют требованиям, если выдавливание производится при невысоких удельных давлениях, так как при больших давлениях наблюдается выжимание смазки с поверхностей контакта, разрыв пленки, что ведет к налипанию металла на поверхность штампа. Консистентные смазки (петролатум, масло, вода, ввязанные загустителями – парафином, воском, мылами и др.) имеют те же недостатки, что и жидкие; кроме того, их трудно наносить на штамп.
Из плавящихся смазок наибольший интерес представляют стеклянные и соляные. Высокая вязкость при хорошей прилипаемости к инструменту позволяет производить надавливание при больших удельных давлениях и скоростях деформации. (Недостатки: загрязнение штампа и трудность удалившая отекла с поверхности штампа и поковки).
Переход от сухого трения к жидкостному может быть осуществлен не только введением искусственных смазывающих веществ, но и путем оплавления тонкого поверхностного слоя заготовки в процессе деформации. Некоторые алюминиевые сплавы хорошо прессуют без применения смазки ( ). Способ смазки оплавлением не получил практического применения при выдавливании стали.
Область применения
Анализ номенклатуры поковок, выпускаемых кузнечными цехами машиностроительных предприятий, показывает, что значительная часть поковок может быть изготовлена с применением выдавливания. Вопрос о выборе рационального технологического варианта решается технико-экономическим расчетом.
Как правило, применение штамповки выдавливанием, взамен обычной, позволяет снизить расход металла на 15-20 % (для полых поковок 20-30 %). В то же время при выдавливании применяется более дорогая и менее стойкая штамповая оснастка. Поэтому экономия металла окупает повышенные затраты только при крупносерийном и массовом производстве. Применение штамповки выдавливанием стержневых поковок взамен высадки на ГКМ нецелесообразно ввиду недостаточной экономии металла, получаемой при этом.
Кроме экономии металла, выдавливание обеспечивает повышение точности поковок за счет уменьшения величины припусков и напусков, повышение производительности и снижение трудоемкости обработки. При выдавливании сравнительно легко осуществить механизацию и автоматизацию штамповки.
Поковки, изготовляемые выдавливанием, можно свести к следующим основным группам:
1. Сплошные стержневые поковки с утолщением на одном конце.
2. Поковки типа многоступенчатых валиков.
3. Полые поковки.
4. Поковки с местными утолщениями или отростками в поперечных или наклонных направлениях.
Дата добавления: 2018-06-01; просмотров: 996; Мы поможем в написании вашей работы! |
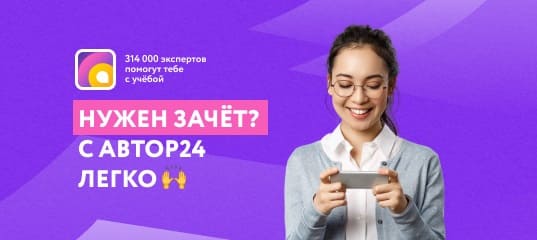
Мы поможем в написании ваших работ!