Предварительное апробирование.
Проверяются усилия в маховичках и рукоятках для ручного перемещения, работа всех органов управления, легкость нахождения нужного положения органа управления при его переключении, производятся все возможные переключения с одной скорости на другую. При этом в качестве оснастки используются динамометры сжатия, растяжения, динамометрические ключи.
Проводится испытание электрооборудования: а) повышенным напряжением для проверки изоляции проводов и двигателей в течение 1 мин с испытательным напряжением 85% от наиболее низкого, при котором аппараты испытывались до монтажа, но не менее 1500 В; б) измеряется сопротивление изоляции всех цепей (главных силовых, управления, освещения, сигнализации и т.д.) относительно корпуса станка, а также сопротивление изоляции между отдельными фазами силовых цепей; в) проверяется нагрев электрооборудования при работе станка.
Испытания на холостом ходу.
а) проверяют все частоты вращения от nmin до nmax – На максимальной частоте станок работает до установившейся температуры шпиндельных опор, характеризующей натяг;
б) проверяют правильность функционирования электрооборудования:
─ обеспечение требуемого цикла работы или правильности исполнения команд (для станков с программным управлением);
─ правильность работы путевых выключателей;
─ работу защитных блокировок;
─ надежность действия тепловой, нулевой и максимальной защиты;
|
|
─ нагрев катушек аппаратов, сопротивлений и пр.;
─ отсутствие гудения магнитных систем аппаратов;
в) проверяют подачу от Smin до Smax и работоспособность всех механизмов (патрона, пиноли, механизмов быстрого перемещения, механизмов ограничения подачи и др.);
г) проверяют правильность функционирования системы смазывания:
─ уровень масла в баке при работе насоса;
─ отсутствие вытекания масла из подшипников и уплотненных мест, минуя слив, просачивания из системы распределения;
─ правильность функционирования контрольных элементов системы смазывания и др.
д) проверка правильности функционирования системы охлаждения, конструктивного и монтажного исполнения и расположения системы охлаждения:
─ максимальное количество подаваемой жидкости в минуту;
─ потребляемая мощность электродвигателя насоса при максимальном потреблении охлаждающей жидкости;
─ нагревание корпуса насоса при максимальной подаче (потреблении) жидкости в течение одного часа и др;
е) испытание органов ручного управления:
─ контролируется расположение рукояток, правильность, ясность изображения и удобочитаемость таблиц и шкал;
─ проверяется удобство формы рукояток маховичков.
|
|
Дальнейшие испытания описываются на примере станков токарной группы:
ж) определяется время разгона и торможения шпинделя с кулачковым самоцентрирующимся патроном на максимальной частоте (проводится только при испытании опытных образцов);
з) испытание механизма главного привода в режимах частых рывков, остановов и реверсирования на nmax:
один цикл – 10 с для токарных станков с максимальным диаметром 250-320 мм;
и) измерение мощности холостого хода (определение потерь на трение). На холостом ходу последовательно включают все частоты вращения шпинделя и измеряют мощность, потребляемую двигателем из сети Pс (для серийных станков проверка осуществляется на частотах nmin, nср, nmax). Баланс мощности при работе станка, на холостом ходу выглядит так:
Рс= Рд + Рхх,
где Рс - мощность, потребляемая двигателем из сети, кВт; РЭ и, соответственно потери мощности в электродвигателе и механической части привода.
На основании результатов измерений строят графики координат Рс,n:
к) испытания на шум. Определяются уровни шума и уровни частотных составляющих спектра шума при работе станка на холостом ходу. На тех ступенях скоростей, при которых возникает максимальный уровень шума, измеряют также уровни частотных составляющих спектра шума, при этом микрофон располагают в точке, соответствующей положению рабочего;
|
|
л) испытание на вибрации при холостом ходе станка. Определяются уровни и частотный спектр вынужденных колебаний шпинделя относительно суппорта при работе станка на холостом ходу.
м) измерение температурных деформаций станка. Определяются изменения расположения оси шпинделя относительно резцедержателя суппорта в результате разогрева станка после вращения шпинделя на холостом ходу.
Испытания под нагрузкой.
Испытание проводится при нагружении главного привода станка максимальным моментом.
Нагружающий момент может быть обеспечен различными нагружающими устройствами (например, электромагнитным порошковым тормозом) или резанием заготовки с глубиной, обеспечивающей максимальный момент. При испытаниях контролируется мощность, потребляемая двигателем из сети Рс. Баланс мощности при работе привода под нагрузкой выглядит следующим образом:
Рс= Рд+ Рхх+ Рн+ Рэф,
Проверка станка на точность.
Дата добавления: 2018-06-27; просмотров: 504; Мы поможем в написании вашей работы! |
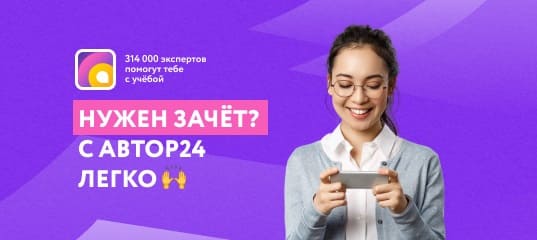
Мы поможем в написании ваших работ!