Экспериментальные методы исследования виброустойчивости станков
Для оценки виброустойчивости станков в лабораторных и производственных условиях используют следующие методы исследований: по предельной стружке, по АФЧХ, по изменению коэффициента устойчивости и др. [26] . Первые два получили наибольшее распространение.
1. Исследование виброустойчивости станков по предельной стружке.Его выполняют в процессе резания. Создают реальные условия нагружения и работы подвижных соединений, исключают погрешность, связанную с линеаризацией системы.
Предельной стружкой считают максимальную ширину (глубину) среза, при которой работа осуществляется без вибраций. Предельную стружку определяют для каждого из фиксированных параметров резания или конструкции станка (скорости резания, подачи, вылета оправки и др.) при последовательном увеличении ширины (глубины) резания до момента интенсивного роста колебаний.
Схема измерения колебаний с использованием светолучевого осциллографа O приведена на рис. 132, а.
Деталь 1 обрабатывают по цилиндрической поверхности проходным или широким резцом. Колебания регистрируют индуктивными преобразователями 2, установленными с зазором d=0,4 мм симметрично по отношению к заготовке (шпинделю). Оба преобразователя являются активными, их включают в полумост, вторая часть которого встроена в усилитель У.
На осциллограмме (рис. 132, б) приведена запись колебаний заготовки с амплитудой Aв, на фоне которых четко просматривается биение шпинделя с амплитудой Aб и более низкой частотой. Вторая кривая представляет собой запись переменного тока частотой 50 Гц и используется как отметчик времени.
|
|
Частоту колебаний заготовки определяют по отрезкам ln,lm, которые содержат соответственно n и m периодов колебаний:
.
Амплитуду колебаний Aв определяют при тарировке изменением зазора d.
Для определения предельной ширины резания bпр, например, в функции скорости резания v, при каждом фиксированном значении vi ширину резания b увеличивают до тех пор, пока измеренная амплитуда колебаний Aв не достигнет допустимого значения Aд . Условию
соответствует предельная ширина резания:
для v1 задают ряд b1, b2,…,b1пр;
для v2 задают ряд b1, b2,…,b2пр;
. . . . . . . . . . . . . . . . . . . . . .
для vn задают ряд b1, b2,…,bnпр.
По точкам vi — biпр строят границу устойчивости (рис. 133).
Периодическое возникновение и исчезновение колебаний свидетельствует о кинематических или конструктивных недостатках в станке, в частности о неудовлетворительном контакте конуса оправки.
Одним из методов поиска причин низкой виброустойчивости станков является определение форм колебаний, характеризующих пространственную деформацию станка. Под формой колебаний станка понимают совокупность отношений перемещений колеблющихся точек к какой-либо отдельной точке упругой системы, полученных в определенный момент времени. Для снятия формы колебаний выбирают опорную точку, с которой сравнивают колебания всех остальных.
|
|
Возбуждение колебаний осуществляется резанием в наиболее виброопасном режиме, измерение – индуктивными или проволочными преобразователями. Относительные амплитуды колебаний наносят на контуры станка. Дальнейшему исследованию подлежит тот элемент станка, где отклонения наибольшие.
83 Исследование виброустойчивости станка по АФЧХ динамической системы
Исследование виброустойчивости станков по АФЧХ ДС.
Наиболее точно АФЧХ определяют экспериментально. В ЭНИМСе разработаны методика и средства измерения частотных характеристик ЭУС и ПР [26] , которые позволяют прослеживать влияние отдельных конструктивных и технологических параметров на устойчивость станка.
Характеристика эквивалентной упругой системы должна определяться на работающем станке или на холостом ходу. В последнем случае сохраняется подвижность соединений, и допускаемая погрешность невелика. Но в обоих случаях возникают трудности в создании внешней нагрузки и измерении относительных смещений между подвижными звеньями станка: инструментом и заготовкой.
|
|
На практике часто характеристики WЭУС определяют на неработающем станке. Погрешность будет тем меньше, чем меньше влияние подвижных соединений упругой системы во всем или каком-либо частотном диапазоне. При значительном влиянии подвижных соединений наибольшие отклонения от действительной характеристики будут по амплитуде и фазе колебаний и наименьшие по собственной частоте [26] .
При снятии статической характеристики KЭУС нагрузка во времени постоянна. Методика и приборы те же, что и при экспериментальном определении жесткости станков. Если нагрузку между конечными звеньями станка P0, несущими деталь и инструмент, направить по равнодействующей сил резания, а отжатие y0 измерять по нормали к обработанной поверхности, то после линеаризации статическую характеристику определяют из соотношения
.
С помощью двухкоординатного самописца ПДС-021 характеристику можно строить автоматически.
При определении динамической характеристики ЭУС на несущие конструкции воздействует переменная во времени нагрузка — входная координата. В качестве выходной координаты принимают относительные упругие смещения тех же конструкций. Направление нагружающей силы и измеряемых упругих смещений сохраняются такими же, как и при снятии статической характеристики.
|
|
Блок-схема установки для снятия АФЧХ ЭУС металлорежущих станков показана на рис. 83.1. Силовое воздействие на упругую систему станка осуществляют по синусоидальному закону электромагнитным вибратором В и регистрируют преобразователем силы ПС. Относительные смещения несущих конструкций регистрируют преобразователем перемещения ПП.
|
Вибратор и преобразователь перемещения, в соответствии со схемой определения статической характеристики, жестко крепят на суппорте (столе) станка, а оправку 1 — в шпинделе.
Вибратор имеет две катушки: постоянного и переменного тока. Катушка постоянного тока питается от источника ИПТ и создает постоянную составляющую нагрузки, величина которой зависит от предварительного натяга в системе и силы резания, характерной для данного типа станка. Катушка переменного тока питается от частотного преобразователя ЧП и создает переменную составляющую нагрузки для возбуждения вынужденных колебаний. Амплитудное значение переменной нагрузки должно быть минимальным и определяется чувствительностью аппаратуры.
Частотный преобразователь должен обеспечивать диапазон частот 20–600 гц для легких и средних станков, синусоидальную форму напряжения и дискретность регулирования частоты 0,5 Гц. На схеме рис. 83.1 частоту регулируют звуковым генератором ГЗ-33, сигнал от которого усиливается трансляционным усилителем ТУ-600. От преобразователей ПП и ПС сигнал через усилитель У, фильтр Ф и генератор И подается на фазочувствительный вольтметр ФВ и электронный осциллограф О. Показания индикаторов вольтметра соответствуют координатам ReЭУС и ImЭУС АФЧХ исследуемого станка.
Перемещения и силы измеряют индуктивными и тензометрическими преобразователями. Силу можно измерять через измерительную обмотку вибратора. Наблюдение и контроль за формой сигналов осуществляют по осциллографу.
При снятии АФЧХ станка применяют бесконтактный или контактный вибратор: первый при вращающемся шпинделе, когда сохраняется подвижность соединений в несущих конструкциях, второй на неработающем станке.
Общий вид бесконтактного вибратора 1, установленного на столе координатно-расточного станка мод. КР-450, показан на рис. 135, а.
При работе станка наблюдаются быстропротекающие колебательные процессы-вибрации. Они отрицательно влияют на точность и шероховатость поверхности обрабатываемых деталей, уменьшают долговечность и ухудшают технологические возможности станка. В станках имеют место следующие виды колебаний. Свободные колебания возникают под действием кратковременной возмущающей силы, например, при пусковых и переходных процессах. Вынужденные колебания возникают под действием внешней периодической силы, например, от моментов вращающихся частей станка или при строгании, фрезеровании. Автоколебания, т. е. незатухающие, самоподдерживающиеся колебания при резании возникают под действием периодической возмущающей силы резания при сдвиге слоев обрабатываемого материала.
Параметрические колебания возникают при наличии какого-либо переменного параметра, переменной жесткости детали или узла станка, создающего эффект, аналогичный действию периодической возмущающей силы. Уравнение свободных колебаний имеет вид , где m – масса системы; d – коэффициент демпфирования сопротивлением трения; k – жесткость системы;
– соответственно перемещение, скорость и ускорение системы. Отношение
называют логарифмическим декрементом затухания колебаний;
– собственной частотой колебаний;
относительным демпфированием или декрементом затухания.
Относительное демпфирование является показателем степени виброустойчивости системы: – сильное демпфирование;
– критическое демпфирование;
– слабое демпфирование. При сильном и критическом демпфировании колебание имеет апериодический характер, т. е. затухает сразу, не переходя за положение равновесия. При слабом демпфировании колебания затухают по экспоненциальному закону
, т. е. отношение амплитуд за время
равно
(рис. 217, б), где T – период колебания, n – число колебаний за период уменьшения амплитуды до заданной. Логарифмируя отношение амплитуд, находим
и декремент затухания при
. При сильном и критическом демпфировании
. Уравнение вынужденных колебаний
, где F – возмущающая сила, w – круговая частота действия возмущающей силы.
При вынужденных колебаниях во избежание резонанса собственная частота системы не должна совпадать по величине и фазе с вынужденной частотой. Для оценки виброустойчивости системы применяют амплитудно-фазовый частотный метод. Он заключается в сообщении, например, шпинделю станка периодических вынужденных колебаний от генератора колебаний (рис. 217, а) и в записи на осциллограмме при помощи вибродатчика колебаний системы. Они, как правило, отличаются по амплитуде и по фазе от колебаний генератора (рис. 217, в). При периодическом изменении частоты генератора сравнивают амплитуды колебаний на входе и выходе системы AВЫХ/AВХ и сдвиг колебаний по фазе j. Затем строят амплитудную и фазовую j
характеристики в зависимости от частоты колебаний ω (рис. 217, г). Совмещение амплитудной и фазовой частотных характеристик в иррациональной Im и реальной Re координатах позволяют получить амплитудно-фазовую частотную характеристику АФЧХ (рис. 217, д). Радиус-вектор кривой АФЧХ характеризует отношение амплитуд, а угловое положение φ относительно положительного направления оси Re – угол сдвига фаз колебаний. Значение –1 на вещественной оси Re означает совпадение амплитуд колебаний и сдвиг по фазе φ = 180°. Это соответствует резонансу. Для устойчивости упругой системы необходимо, чтобы кривая АФЧХ не охватывала –1 на оси Re.
84 Определение АФЧХ УС методом гармонического возбуждения
Основа метода - создание на входе исследуемого элемента гармонического воздействия, при этом на выходе элемента получают гармонический сигнал той же частоты, но другой амплитуды и фазы (для линейных или линеаризованных систем). Применительно к УС станка входным воздействием является сила резания, а входным сигналом - относительные кoлебания между инструментом и заготовкой.
Источником нагружения и возбуждения колебаний служат вибраторы, основные типы которых описаны в работе [5].
Блок-схема комплекса аппаратуры П-О1М [I] показана на рис.21.
![]() |
ЭВМ по программе AFH через интерфейсный блок и блок управления задает на генераторе синусоидальный сигнал требуемой частоты и амплитуды, который после усиления поступает на обмотку переменного тока вибратора. Источник постоянного тока обеспечивает получение постоянного усилия вибратора. Параметры вибрации измеряют либо одним датчиков относительных колебаний либо двумя датчиками абсолютных колебаний. Сигналы датчиков через усилители поступают на АЦП и далее в ЭВМ.
Переменная сила определяется с помощью измерительной катушки вибратора. Сигнал силы интегрируется и подается через АЦП в ЭВМ.
Частота опроса каждого сигнала составляет 1000...2000 Гц. При частоте опроса 1000 Гц число точек вводимых сигналов задают 512, а при частоте 2000 Гц - 1024. При этом обеспечивается дискретность задания АФЧХ около 2 Гц.
Блок-схема программы AFH обработки сигналов силы и колебаний
УС станка дана на рис.22.
![]() |
Рис.22. Структура программы AFH.
Возможны два алгоритма задания частот возбуждения: жесткий и адаптивный.
При жестком алгоритме частота возбуждения изменяется по определенному закону независимо от результатов измерения. Закон изменения обычно задают в виде арифметической прогрессии либо в виде таблицы фиксированных частот, полученной по результатам предварительных экспериментов.
При адаптивном алгоритме следующее значение частоты задается в зависимости от полученного значения АФЧХ на текущей частоте. Используют два вида адаптивного алгоритма.
В первом алгоритме частота увеличивается с постоянным (большим) шагом до перехода через резонанс. Затем частота уменьшается до предыдущего значения и проходит резонанс с мелким шагом.
Во втором алгоритме анализируется расстояние на графике АФЧХ между текущей и предыдущей точкой. Если эго расстояние меньше некоторого заданного значения, то дается новое приращение частоты с большим шагом, если больше, то шаг частоты уменьшается в два раза и т.д.
Величина напряжения на выходе генератора задается в блоке 3. Эго напряжение должно обеспечить постоянство возбуждающего усилия во всем рабочем диапазоне частот. Закон изменения напряжения подбирается опытным путем при градуировке вибратора.
Значения частоты и напряжения в виде кодов поступают на ШФ 015-83 ЭВМ и далее через блок управления на генератор сигналов ГЗ-110 (блок 4).
Сигналы силы Р и колебаний у1, у2 вводятся в память ЭВМ (блок 5). Затем выполняется графический контроль сигналов (блок 6).
Для получения сигнала относительных колебаний вычитают сигналы у1 , и у2. Если колебания измеряют датчиком относительных колебаний, во вычитание не производится .
Для сигналов Р и у выполняется быстрое преобразование Фурье (блок 8), и по спектру силы определяют максимальную амплитуду и соответствующую ей дискретную частоту спектра . Эта частота с точностью ±1 Гц совпадает с заданной частотой возбуждения
. Для частоты
рассчитываются действительная и мнимая части АФЧХ:
;
где ,
,
,
- действительная и мнимая части спектров Р и
соответственно на частоте.
Далее выполняется амплитудная и фазовая коррекция АФЧХ на основе градуировочных графиков каналов измерения вибраций (блок 10).
Больше фазовые искажения дают вибродатчики абсолютных колебаний (рис.23). При градуировке должны учитываться амплитудные и фазовые характеристики канала измерения, включающего вибродатчик усилитель, мультиплексор каналов и АЦП. Градуировочные графики описываются аналитическими зависимостями, которые вводят в память ЭВМ и используют для коррекции АФЧХ УС.
f, Гц
Рис.23. Фазовая характеристика датчика абсолютных колебаний:
• - эксперимент; — - кусочно-линейная аппроксимация на участках I и II
Текущие точки АФЧХ выводятся на экран графического дисплея. После прохождения по всем частотам параметры АФЧХ печатаются в протоколе испытаний, а ее график выводится на графопостроитель.
Рис.24. АФЧХ УС токарного станка: а -ветви детали; б - ветви инструмента; в – суммарная
При измерении колебаний двумя датчиками абсолютных колебаний имеется возможность не вычитать сигналы датчиков, а получить две АФЧХ ло каждому сигналу отдельно:
W1=y1/P: W2=y2/P,
и затем суммарную АФЧХ: W=W1+W2.
Промежуточные АФЧХ W1, a W2 могут дать полезную информацию о роли ветвей детали и инструмента в формирования АФЧХ УС станка. На рис.24 показаны АФЧХ ветвей детали и инструмента для токарного станка.
85 Определение АФЧХ методом импульсного возбуждения
Источником импульсного нагружения является динамометрический молоток (рис.25). Молоток состоит из корпуса 2, внутри которого находится силоизмерительный цилиндр 4. Для измерения силы используют тензодатчики 3, наклеенные на цилиндр.
Рис.25. Динамометрический молоток
Спектральные характеристики импульсного воздействия зависят о т величины сменной массы J и материала бойка 5.
Структура комплекса аппаратуры, реализующей рассматриваемый метод, показана на рис.26.
К испытуемому объекту прикладывают серию импульсных воздействий: сначала к ветви детали, затем к ветви инструмента. Сигналы опрашиваются с частотой 2000 Гц;
Блок-схема программы обработки сигналов дана на рис.27.
Программа начинается циклом по точкам приложения возбуждавшего усилия (ветвь детали и ветвь инструмента). Три сигнала Р ,у1 и у2 вводятся в память ЭВМ в блоке 2. Затем сигналы индицируются на графическом дисплее.
Каждый вибросигнал состоит из нескольких переходных процессов; соответствующих серия импульсов. Промежутки между переходными процессами совпадают с паузами между ударами. Совокупность трех переходных процессов» соответствующих одному и тому же удару, образуют выборку (рис.28). Таким образом, в выборке исключаются промежутки между ударами. Каждая выборка подвергается быстрому преобразованию Фурье самостоятельно.
![]() |
Просматривая на экране дисплея графики вибросигналов, определяют длительность выборки, приблизительно равную длительности переходного процесса, начало каждой выборки и число выборок.
Рис.26. Блок-схема комплекса аппаратуры для определения АФЧХ
методом импульсного возбуждения:
I - вычислительный модуль; 2 - приборный модуль
Рис.27. Структура программы определения АФЧХ
Для получения относительных колебаний выполняют вычитание сигналов
, и
(блок 4). Для кадкой пары сигналов выборки выполняют быстрое преобразование Фурье (блок 6) и вычисляют автоспектры сигналов
,
и действительные и мнимые части взаимного спектра
по формулам
;
;
;
.
Затем производится осреднение (блок 8) спектров по выборкам и при этом получают спектры
,
,
и
.
Полученные спектры используют для расчетов действительной R и
Выборка1 пауза выборка2
|
время
Рис.28. Формирование выборок из вибрационных сигналов
мнимой I частей АФЧХ (блок 9)
;
.
Коррекция АФЧХ (блок 10) выполняется так же, как описано в предыдущем разделе.
87.1 Диагностика станков. Способы технического диагностирования
Система технического диагностирования
Повышение степени автоматизации и расширение функциональных возможностей современного автоматизированого технологического оборудования, особенно станков с ЧПУ и построенных на их основе ГПМ и ГПС, значительно усложняют их конструкцию и, как
следствие, усложняют их техническое обслуживание и особенно поиск причин отказов этого оборудования в процессе эксплутации.
Если в обычном, часто достаточно простом, технологическом оборудовании причин отказов, как правило, мало и они часто известны или легко определяются, то в современных высокоавтоматизированных станках, включающих в себя взаимодействующие механические, гидравлические, пневматические, электрические и электронные механизмы, устройства, блоки, причин отказов может быть очень много, и их нахождение требует значительных затрат времени и средств. Вследствие возникающих при этом значительных простоев снижается производительность работы этого дорогостоящего
Оборудования. Вследствие возникающих при этом значительных простоев снижается производительность работы этого дорогостоящего оборудования. Такие проблемы усложняются дополнительно в связи с более интенсивной эксплуатацией таких станков, работающих часто в три смены при минимальном количестве обслуживающего персонала.
Обработка заготовок благодаря применению современных режущих инструментов проводится на более высоких режимах резания, чем раньше что увеличивает нагрузки на различные механизмы и устройства станков.
Все это приводит к большей вероятности отказов в работе самих станков и его систем управления, требует значительного времени на поиск причин этих отказов.
Как показывает практика, причины целого ряда отказов могут быть очень несущественными, легко и быстро устранимы, а времени их поиска часто на порядок больше, чем время для их устранения, даже и для высококвалифицированного наладчика или оператора. Поэтому все более широкое применение получают системы технического диагностирования, особенно на современных станках с ЧПУ а также в ГПМ и ГПС.
Техническая диагностика станков
Для оценки состояния станка в процессе эксплуатации, его работоспособности (на различных этапах жизненного цикла) и выявления тех причин и элементов станка, которые оказывают основное влияние на изменение его выходных параметров, применяют техническое диагностирование.
Различают два направления диагностики станков:
- предэксплуатационная диагностика новых образцов;
- диагностика в процессе эксплуатации.
Диагностика (от греческого diagnostikos – способный распознавать).
Техническая диагностика – установление и изучение признаков, характеризующих наличие дефектов в машинах, устройствах для предсказания возможных отклонений в режимах их работы или состояниях, а так же разработка методов и средств обнаружения и локализации дефектов в технических системах.
Техническая диагностика осуществляется при помощи диагностической аппаратуры, она является важнейшим средством обеспечения и поддержания надежности станков.
Предэксплуатационная диагностика является элементом комплексных испытаний опытных образцов станков и признана выявить слабые места конструкции, указать основные причина, вызывающие недопустимые отклонения выходных параметров.
Эксплуатационная диагностикасвязана с тем, что имеется широкий диапазон условий и режимов эксплуатации, вариация начальных показателей качества станка, которые обеспечивают различные скорости потери станком работоспособности и соответственно, времени достижения предельного состояния. Поэтому весьма важно иметь методы и средства для оценки технического состояния станка, выявления причин нарушения работоспособности, установления вида и места возникновения повреждений.
Применение диагностики в процессе эксплуатации станка накладывает свой отпечаток на методы и средства диагностики, которые должны быть удобны для применения в заводских условиях, обеспечивать осуществление процесса диагностирования в минимальное время, обладать достоверностью показаний, осуществлять контроль без разборки и без нарушения работы механизма, быть экономически целесообразными. В этом случае конструкция станка должна быть приспособлена для диагностики: либо иметь встроенные приборы, оценивающие его параметры (давление в гидросистеме, температуру энергонапряженных узлов, точность движения, скорость и т.д.), либо периодически подключаться к специальному устройству, осуществляющему контроль основных параметров станка и дающему заключение о его состоянии.
87.2 Измерение и анализ диагностических сигналов
Диагностические процедуры, которые осуществляются при программном методе испытания, призваны выявить причины и источники тех или иных отклонений от заданных движений рабочих органов станка, т. е. найти взаимосвязи между выходными параметрами станка и конструктивно-технологическими параметрами его элементов. В качестве диагностических признаков (параметров технического состояния объекта), которые контролируются в процессе испытания, могут быть приняты выходные параметры станка, повреждения, возникающие при эксплуатации станка, и косвенные признаки, характеризующие его состояние (см. гл. I).
При программном методе испытания за выходные параметры станка приняты параметры траекторий опорных точек. Поэтому их анализ дает первую информацию о возможных причинах появления погрешностей в работе станка. Наличие высокочастотных составляющих траекторий свидетельствует о вибрациях в станке, а основная причина смещения всей совокупности траекторий связана, как правило, с тепловыми деформациями станка и т. д. (см. рис. 7).
Оценка повреждений, возникающих при эксплуатации станка, часто позволяет вскрыть причину тех или иных погрешностей его работы. Однако при непродолжительных испытаниях не проявляется такой мощный источник нарушения работоспособности станка, Как износ его влияние при программном методе испытания лишь прогнозируется. Здесь в качестве диагностических признаков можно использовать повреждения, связанные лишь с быстропротекающими процессами и процессами средней скорости (см. рис. 1). Это в первую очередь, силовые и тепловые деформации станка. Измерение деформаций в процессе испытания станка и их сопоставление с системой действующих сил или с параметрами температурных полей (которые являются косвенными диагностическими признаками) с одновременным измерением выходных параметров ставка — параметрами траекторий позволит выявить основные источники и причины возникновения погрешностей станка. Косвенные диагностические признаки, которые контролируются в процессе испытания, функционально связаны с работоспособностью станка и отражают изменения, происходящие в станке при его функционировании.
Косвенными диагностическими признаками могут служить акустические сигналы, температурные поля, изменения давлений в систему показатели динамического состояния системы (фазовые и частотные характеристики) и др. [3, 6, 35].
При осуществлении процесса диагностирования большое значение имеет информативность того сигнала, который поступает от соответствующего преобразователя. Различные диагностические сигналы несут неодинаковую по объему информацию и поэтому требуется оценить возможности сигнала и выбрать наиболее целесообразную его форму.
Диагностический сигнал (значение выходного параметра, степень повреждения или косвенный признак) может иметь различный характер. Наиболее простым является случай, когда данное показание датчика непосредственно характеризует состояние объекта, точность измерения достаточно велика и можно не учитывать влияние посторонних факторов. В этом случае по величине сигнала можно судить о вкладе данного элемента в нарушение работоспособности станка.
Например, измерение давления в гидросистеме позволяет делать вывод о правильном ее функционировании, так как падение давления ниже нормы свидетельствует о возрастании утечек (или о разрушении элементов при падении давления до нуля), а возрастание давления говорит о засорении или облитерации каналов, заклинивании плунжеров или других недопустимых явлениях.
Однако в ряде случаев, особенно при суждении об отказе по косвенным признакам, на данный сигнал могут оказывать влияние не только характеристики данного элемента или узла, но и посторонние факторы (помехи), искажающие полученную информацию.
Например, при оценке работоспособности шпиндельных опор качения по температуре масла следует иметь в виду, что повышение температуры может быть связано не только с состоянием подшипника, но и с повышенными нагрузками, влиянием внешних источников теплоты, засорением гидросистемы, ухудшением смазки и другими явлениями.
В этом случае для повышения достоверности показаний необходимо иметь группу признаков, характеризующих степень нарушения работоспособности, — «синдром состояния» с тем, чтобы по их сочетанию оценивать действительное состояние объекта. Так, если при диагностике подшипника одновременно с измерением температуры контролировать и точность его вращения или уровень вибраций, то вероятность правильного диагноза значительно повысится.
Значительно большую информацию, чем показания первичного преобразователя, дающего численное значение данного параметра, несет сигнал в виде функциональной зависимости. Такими сигналами будут, например, законы изменения тепловых полей объекта, изменения сил или крутящих моментов за цикл работы механизма, вибраций, возникающих в системе, амплитудно-частотные характеристики системы, виброакустические сигналы и т. п. Анализ этих функций, спектральный анализ процессов вибрации или акустических сигналов и другие методы оценки функций позволяют из одного сигнала выделить ряд составляющих, характеризующих состояние различных элементов или узлов стайка.
Таким образом, сигнал от одного преобразователя, но выдаваемый в виде реализации некоторой закономерности, может заменить показания целого ряда приборов, определяющих дискретные значения отдельных параметров.
Более сложный случай имеет место при такой форме диагностического сигнала, когда он содержит как систематические, так и случайные составляющие и в общем виде описывается некоторой случайной функцией. Случайная функция является обычно нестационарной и неэргодической, а ее детерминированная составляющая для механизма имеет период, равный периоду цикла его работы. В этом случае диагностирование слабых мест может быть осуществлено путем спектрального анализа случайной составляющей исследуемого параметра и разложением в ряд Фурье неслучайной составляющей.
При диагностировании более широкие возможности имеются при одновременном анализе входных и выходных параметров механизма или станка в целом. Это позволит определить, где находится источник отклонений (флуктуации) выходного параметра, и установить взаимосвязь между изменениями в характере диагностического сигнала и работоспособностью изделия.
Современный металлорежущий станок является сложным объектом, с большим числом взаимосвязей, широкой номенклатурой выходных параметров, работающий в разнообразных условиях эксплуатации и при различных режимах.
При диагностировании сложных объектов возникает ряд дополнительных задач. Во-первых, необходимо установить номенклатуру основных диагностических сигналов S1, S2, .., Sk с тем, чтобы они характеризовали работоспособность исследуемого станка. Во-вторых, по набору этих данных необходимо сделать вывод о техническом состоянии станка и необходимости совершенствования его конструкции или о времени, в течение которого станок сможет сохранить свою работоспособность по параметрам точности. В-третьих, необходимо разработать систему технического диагностирования, которая включает технические средства, а также алгоритм диагностирования, т. е. совокупности предписаний о проведении диагностирования и выбор метода диагностирования (функциональное или тестовое).
![]() |
Эти вопросы решаются обычно на основе общих положений технической диагностики [3, 25, 31], теории надежности машин [38] и с использованием моделей отказов (см. гл. 7).
При разработке систем и методов диагностирования сложного объекта основываются на аналитических или графоаналитических представлениях основных свойств изделия в виде так называемых диагностических моделей. Они могут быть представлены в векторной форме, в виде системы дифференциальных уравнений или передаточных функций, связывающих входные и выходные параметры. Для диагностической модели за входной параметр х можно принять значение показателя качества изделия — вектора, составляющим которого являются параметры станка х1, х2,... хl, а за выходной параметр — диагностический сигнал S. Входным параметром может быть также тот комплекс воздействий, который соответствует данному режиму работы станка при n-м цикле его испытаний (рис. 24).
В общем случае в векторной форме
x=AS,
где A — оператор, характеризующий те преобразования, которые необходимо осуществить с величинами S, чтобы получить параметр х.
Раскрытие этих связей и разработка системы диагностирования сложного объекта может осуществляться двумя основными методами или их комбинацией.
Первый метод диагностирования заключается в получении большого числа сигналов, характеризующих работу отдельных узлов и элементов станка, на основании которых делается заключение о его состоянии. Показания этих сигналов должны быть обработаны по специальной программе с тем, чтобы определить влияние характеристик элементов станка на его выходные параметры, т.е. определить оператор А. Полученные данные позволят предпринять целенаправленные действия по улучшению выходных параметров станка.
Второй метод диагностирования заключается в применении процедур, которые позволяют судить о состоянии машины по параметрам какого-либо динамического процесса, связанного с функционированием механизмов и отражающего состояние машины. Такой процесс можно разложить на составляющие и получить необходимую информацию о работоспособности отдельных механизмов. При этом в процессе возможно использовать всего один преобразователь или, во всяком случае, ограниченное число диагностических сигналов. Примером такого подхода могут служить методы акустической диагностики механических систем [35].
При работе механизмов происходят удары, возбуждающие в материале упругие колебания, которые регистрируются соответствующими измерительными преобразователями. Поскольку при возбуждении колебаний одновременно всеми кинематическими парами машины образуется единое волновое поле, основная задача при диагностировании этим методом заключается в разделении суммарного сигнала на составляющие, так чтобы можно было оценить вклад каждой кинематической пары. В большинстве случаев решение этой задачи облегчается тем, что каждая кинематическая пара характеризуется определенной частотой импульсов, зависящей от типа механизма, скорости или периодичности его работы, а также от длительности существования этих импульсов. Кроме того, между интенсивностью импульсов и состоянием пары имеется, как правило, функциональная связь.
При проведении испытаний станка по программному методу применяют оба метода диагностирования.
При использовании в качестве диагностического признака характеристик теплового поля станка обычно используют первый метод диагностирования, когда диагностические сигналы получают от отдельных термопар путем их последовательного опроса через заданные промежутки времени. На основании этих данных можно оценить параметры исследуемого теплового поля станка и выявить динамику его изменения. Для получения единой картины динамики тепловых полей и подтверждения правильности выбора точек для фиксации температуры с успехом используют тепловизоры — приборы, регистрирующие инфракрасные (тепловые) излучения. Тепловые воздействия оказывают большое влияние на точность прецизионных металлорежущих станков и поэтому целесообразно использовать тепловые поля для выявления причин изменения во времени выходных параметров станка.
На рис.25 на примере шпиндельной бабки многооперационного станка показана схема процесса диагностирования при программном методе испытания с использованием информации, которую несут тепловые поля станка. Шпиндельная бабка перемещается по направляющим скольжения от привода винт — гайка качения и одним из ее выходных параметров являются характеристики траектории опорной точки, расположенной на переднем торце бабки.
Основными источниками тепловыделения являются опоры шпинделя, особенно передняя, где выше нагрузки и влияет теплота от процесса резания, направляющие скольжения, приводные механизмы. При расположении термопар следует это учитывать. Информация, полученная от опроса термопар, и анализ динамики изменения во времени температур отдельных точек узла позволяют определить параметры теплового поля, в первую очередь получить его изотермы.
Изменение во времени t параметров теплового поля, например разности Dθ температур θmax и θmin между наиболее и наименее напряженными точками корпуса Dθ = θmax - θmin позволит дать представление и о соответствующих тепловых деформациях, а при необходимости измерить и их. Одновременно с этим определяются параметры траектории ползуна, например, при помощи оптико-электронного (лазерного) прибора, описанного выше (см. п. 12).
Измеряя параметры каждой реализации траектории, получим характеристику всей совокупности, и в первую очередь смещения траектории Dx, которое, как правило, связано с тепловыми полями.
Сравнение выходных параметров с соответствующими диагностическими сигналами позволяет оценивать влияние тепловых полей и устанавливать зависимость (детерминированную или стохастическую) между ними.
Согласно методике программного испытания эти зависимости должны рассматриваться при работе станка в различных режимах силового и теплового нагружения. Это осуществляется программными нагрузочными устройствами, которые рассмотрены в гл. 4.
Испытание с применением программных нагрузочных устройств является по существу тестовым диагностированием, когда изучается реакция объекта на различные внешние воздействия.
87 а Структура и оснащение измерительно-диагностическогокомплекса
Для выполнения тех функций, которые отведены измерительно-диагностическому комплексу в общем алгоритме испытания (см. рис. 5), его приборное оснащение должно содержать следующую аппаратуру: измерительные преобразователи первичной информации; усилительно-преобразующую аппаратуру: коммутаторы для запрограммированного опроса показаний отдельных приборов; цифровые измерительные приборы и аналого-цифровые преобразователи; ЭВМ и интерфейсные приборы для связи с объектами; устройства ввода и вывода информации.
Таким образом, здесь в единый комплекс объединены метрологическая, регистрирующая и вычислительная аппаратура и этот комплекс выполняет не только измерительно-диагностические, но и информационно-вычислительные функции.
Приборное оснащение комплекса при однотипной его структуре может быть весьма разнообразным, так как это зависит от требований, предъявляемых к точности измерений, от полноты и сложности проводимых измерений и вычислений, от наличия тех или иных моделей приборов. Приборостроение и вычислительная техника стремительно развиваются, и тот комплекс, который сегодня удовлетворяет нас и отвечает самым высоким требованиям, завтра может быть модернизирован и усовершенствован. Его отдельные приборы могут быть заменены другими или одним совмещающим различные функции, а точность приборов и их быстродействие значительно повышены. Тем не менее представляется целесообразным привести пример конкретных данных для измерительно-диагностического комплекса испытательного центра, созданного в лаборатории кафедры «Металлорежущие станки и автоматы» МВТУ им. Н. Э. Баумана, где впервые был опробирован программный метод испытания станков.
Приборное оснащение одной из систем комплекса показано на рис. 26, где указаны типы и модели применяемой аппаратуры. Эта система связана с микро-ЭВМ типа «Электроника ДЗ-28».
Рассмотрим назначение и краткие характеристики отдельных приборов и устройств (см. рис. 26).
Первичные преобразователи и соответствующая аппаратура используются для измерения составляющих сил резания - тензорезисторы универсального динамометра УДМ 100 в комплексе с тензоусилителем УТ-4-1; для измерения траекторий движения рабочих органов - фотоприемники оптико-электронного прибора МВТУ (см. рис. 18); для измерения температурных полей исследуемых узлов станка — хромель-копелевые термопары (чувствительность 0,05 мВ/°С); для измерения деформаций деталей станка — тензорезисторы в комплекте с тензоусилителем «Топаз 3-01».
К усилительно-преобразующей аппаратуре относятся приборы, обеспечивающие усиление и согласование сигналов от измерительных преобразователей первичной информации. Это различного рода усилители для тензорезисторов, селективные усилители, а также приборы, преобразующие сигналы, например фазометры.
Коммутаторы используются для поочередного подключения к измерительному устройству источников напряжений постоянного и переменного тока. Например, применялся аналоговый коммутатор Ф 240/1Б (число каналов до 80 опроса до 50 Гц). Второй коммутатор — специальной конструкции производит опрос шести каналов в любой последовательности с частотой до 100 Гц.
Аналого-цифровые преобразователи (АЦП) измеряют величину сигнала с выхода коммутатора и преобразуют его в цифровой код. Для измерения термо-ЭДС и сигналов с тензоусилителей используется интегрирующий АЦП мод. Ф4883 (пределы измерения напряжений постоянного тока от 20 мВ до 1 В, отсчет показаний — цифровой, пятизначный), а универсальный вольтметр применяется для измерения сигналов с выхода фазометра (пределы измерений напряжений постоянного и переменного тока от 1 до 1000 В, отсчет показаний — четырехзначный).
Интерфейсные приборы организуют связь между ЭВМ и всем периферийным оборудованием, которое включает все вышеперечисленные устройства, а также устройства для вывода информации.
МикроЭВМ являются основными элементами данного комплекса. Применялись специализированные управляющие электронно-вычислительные машины «Электроника ДЗ-28». Две микроЭВМ применены для более производительной работы системы и позволяют реализовать алгоритмы программного испытания станков.
Объем оперативного запоминающего устройства «Электроника ДЗ-28» 32 Кбайт, время выполнения микрокоманды 1—2 мкс, системы счисления — десятичная и шестнадцатеричная.
Ввод данных и программ возможен с клавиатуры, с кассеты встроенного накопителя на магнитной ленте и с периферийных устройств. ЭВМ работает с программами, написанными в машинных кодах или на языке БЕЙСИК, который предназначен для решения математических и инженерных задач в режиме диалога человек— ЭВМ. Он позволяет программировать широкий круг задач, сочетая в себе простоту с достаточными для многих применений возможностями.
Устройства для вывода информации в данном комплексе состоят из злектрофицированной печатающей машины «Консул 260.1», двухкоординатного самописца Н 306 и алфавитно-цифрового дисплея 15ИЭ-00-013. На печатающей машине «Консул 260.1» осуществляется вывод буквенно-цифровой информации со скоростью 10 знаков/с. На графопостроителе Н 306 изображаются различные графики и диаграммы, дисплей используется для диалогового режима работы.
Программное обеспечение является составной частью измерительно-диагностического комплекса помимо приборной оснастки. Оно в значительной мере определяет возможности комплекса, удобство пользования и, в конечном счёте, от него во многом зависит правильность и достоверность решения поставленной задачи.
Программное обеспечение состоит из рабочих программ, подпрограмм — драйверов, обслуживающих интерфейсные приборы, и банков тарировочных данных.
Данные по градуированию определяются до проведения испытания и для них отводится отдельное место в памяти машины. Рабочая программа, обращаясь в нужные моменты к этим данным, производит перерасчет входной информации, например, из величин напряжения при измерении температуры в градусы Цельсия; а при изменении перемещений —в миллиметрах или микрометрах.
При измерении перемещений с помощью оптико-электронного измерительного устройства коэффициент градуировки k определяется с помощью микроскопа путем измерения шага штрихов изображения растра. Тем самым получают соотношение между разностью фаз опорного и измерительного сигналов, которое пропорционально напряжению на аналоговом выходе фазометра.
В случае измерения температур при помощи термопар банк тарировочных данных формируется более сложным образом.
Как известно, в том диапазоне температур, который используется при испытании с достаточной степенью точности можно считать, что термоЭДС прямо пропорциональна температуре рабочего спая хромель-копелевой термопары. Однако это соотношение является индивидуальным для каждого канала измерительной программы, поэтому термоЭДС следует определять для каждой термопары, погружая ее в калориметр и изменяя температуру в нем на 0,1 0С для получения одной точки. Полученная зависимость аппроксимируется прямой линией по методу наименьших квадратов и полученные значения Uо (значения термоЭДС при 0°С) и k (коэффициент градуировки, численно равный тангенсу угла наклона прямой к оси температур) попарно заносятся в память ЭВМ, образуя массив градуировочных данных.
Подпрограммы-драйверы обеспечивают совместную работу микроЭВМ и внешних периферийных устройств через интерфейсные приборы. Применяемые в данном комплексе интерфейсы обладают широкой универсальностью и поэтому существует возможность оптимально построить процессы управления, измерения, вычисления и вывода информации.
Рабочая программа является основным элементом программного обеспечения. Она составляется для конкретного эксперимента или для цикла экспериментов и обеспечивает решение поставленной задачи. Составными частями рабочей программы часто являются научные подпрограммы, в том числе из библиотеки стандартных подпрограмм.
Управление измерительно-испытательным комплексом и содержание программного обеспечения рассмотрены в гл. 5 (см. табл. 4).
Измерительно-диагностическая система с использованием мини-ЭВМ «Искра-226» предназначена для оценки параметров траекторий рабочих органов многооперационного фрезерно-расточного станка 243ВМФ2 показана на рис. 27.
В процессе испытания измеряются перемещения гильзы вертикально расположенного шпинделя и стола станка.
Для определения траекторий опорных точек применены высокоточные четырехгранные лекальные линейки типа ЛЧ, которые устанавливают на поверхности стола.
Контактные измерительные преобразователи помещают на неподвижных стойках или на стойках, закрепленных на недеформируемой части станины. Точность перемещения рабочих органов определяется по траекториям опорных точек 1-5. Точки 1, 2 и 3 расположены на рабочей поверхности стола. Они расположены так, что возможно определить не только отклонения от прямолинейности перемещения вдоль управляемой координаты (например, по оси У, как показано на рис. 27, или оси X т. е. в двух взаимно перпендикулярных направлениях), но и отклонение — «рыскание» стола относительно вертикальной оси Z.
Пространственное положение переднего конца шпинделя определяется с помощью двух опорных точек 4 и 5. В качестве отсчетной поверхности для измерительных преобразователей, установленных в этих точках, используется поверхность гильзы шпинделя, погрешность которой составляет 3—5 мкм на длине 350 мм.
Особенностью описываемого метода является то, что отсчетные поверхности лекальных линеек, установленных на рабочей поверхности стола, были предварительно измерены для определения собственных геометрических погрешностей. По результатам измерений построены уравнения регрессии для тех граней линеек, по которым перемещаются наконечники измерительных преобразователей ИП. Эти данные введены в память мини-ЭВМ для автоматической коррекции результатов, поступающих от измерительной системы, что уменьшает погрешность измерения контактным методом до ±2 мкм.
В качестве измерительных преобразователей используют электронные измерительные системы 214 завода «Калибр» с диапазоном измерения 30 мкм, собственная погрешность системы измерения составляет 1 мкм.
Погрешность лекальных линеек от ±3,5 до ±6мкм.
Сбор и обработка экспериментальных данных обеспечивается применением мини-ЭВМ «Искра-226» шестого исполнения. От электронных измерительных систем 214 сигнал поступает в блок интерфейсный функциональный БИФ аналого-цифрового преобразователя АЦП, где из аналоговой формы преобразуется в цифровую. В оперативном запоминающем устройстве ОЗУ хранится программа выполнения конкретного эксперимента, загружаемого с помощью БИФ накопителя на гибком магнитном диске НГМД из банка программ, заранее разработанных для экспериментальных исследований и обработки результатов экспериментов.
Результаты экспериментальных исследований фиксируются в ОЗУ и выводятся на экран дисплея и графопостроителя с помощью соответствующих интерфейсных блоков. Функционирование узлов мини-ЭВМ в соответствии с заданной программой обеспечивается постоянным запоминающим устройством ПЗУ, в котором хранится системное обеспечение, загружаемое через интерфейс — «центральная шина».
Для того чтобы при испытании измерять траектории опорных точек, а не положение линеек в пространстве (см. рис. 15, а и г), предусмотрена специальная подпрограмма, которая по информации о положении стола в данный момент времени делает расчет координаты каждой из трех опорных точек. Для гильзы шпинделя этот расчет ведется по схеме, показанной на рис. 15, г.
Результаты испытания выводятся на дисплей и на графопостроитель, где поверхности геометрического образа могут быть для наглядности изображены в изометрии.
При создании измерительного комплекса большое значение имеет выбор системы координат, в которой производится измерение параметров траекторий. Часто более удобно иметь самостоятельные системы координат применительно к узлу, несущему инструмент, и узлу, несущему заготовку. При этом начальное положение оси, связанной с направлением движения стола или с осью шпинделя, может быть определено средней линией совокупности траекторий.
При наличии отдельных систем координат должно быть определено их взаимное положение на основании методов аналитической геометрии. Фиксация данного положения оси координат может быть осуществлена, например, при помощи луча лазера, как опорной базы для контроля точности перемещающегося объекта [66]. Наиболее целесообразно иметь единую систему координат, фиксированную в пространстве и не изменяющую своего положения в процессе эксперимента. Это позволит оценить параметры не только траекторий перемещающихся узлов станка, но и непосредственно определять параметры, характеризующие взаимное положение заготовки и инструмента.
89 Измерительно-диагностические комплексы
(исследование 2/№76/2)
Испытания проводятся в специально оборудованных испытательно-диагностических центрах (комплексах), где обеспечивается программное нагружение станка, имитация внешних воздействий, измерение необходимых параметров в процессе работы станка и обработка информации на ЭВМ.
Рис. Структура испытательно-диагностического центра
Функции ЭВМ:
- обрабатывать и хранить результаты испытаний;
- обрабатывать априорную информацию об эксплуатационных нагрузках и условиях эксплуатации, об износостойкости материалов, применяемых для базовых деталей, о точности обработки и др. характеристиках данной модели станка;
- осуществлять программное управление режимами работы станка и специальными нагрузочными устройствами, включая имитацию внешних воздействий – изменение величины и направления силы, наложение спектра вибраций, управление тепловыми потоками и др.;
- осуществлять расчеты показателей качества и прогнозировать показатели надежности станки.
Испытание проходит в режиме автоматизированного эксперимента и состоит из последовательных циклов, число которых должно быть достаточным для статистической обработки результатов. Каждый цикл осуществляется при своем сочетании факторов, влияющих на параметры траекторий. Полученные траектории каждой опорой точки являются реализациями некоторого случайного процесса, характеризующего движение рабочих органов станка при его эксплуатации.
Параметры траектории определяются с помощью измерительного комплекса и вводятся в ЭВМ, где производятся необходимые расчеты, результаты которых хранятся в памяти.
Кроме того, в комплексе имеется диагностическая аппаратура. При ее помощи оценивается состояние отдельных элементов станка, их тепловые поля, виброакустические сигналы и т.д.. Анализ диагностических сигналов с помощью ЭВМ позволяет судить о причинах отклонений параметров траекторий от их номинального значения.
Кроме того, ЭВМ с учетом априорной информации осуществляет прогноз о возможном изменении параметров траектории при длительной эксплуатации станка.
Т.о. при программном испытании обширную информацию о характеристиках станка и его реакции на внешние воздействия получают за счет применения специальных нагрузочных устройств измерительно-диагностической аппаратуры, ЭВМ и специальной организации этих испытаний.
90-92 Нагрузочные устройства в исследованиях станков
Нагрузочные устройства для создания сил, имитирующих рабочие нагрузки, действующие на узлы станка, широко применяют при испытании и исследовании станков.
Так, известны различного рода динамометры, применяемые при исследовании жесткости станков [60], вибраторы, используемые при снятии динамических характеристик станков [21], различные специальные нагрузочные устройства для создания сил при испытании и исследовании отдельных узлов станка.
В большинстве случаев применяемые нагрузочные устройства мало пригодны для программного метода испытания станков. При программном методе испытания должны применяться такие нагрузочные устройства, которые могут воспроизводить весь диапазон силовых воздействий, возникающих в процессе обработки, не затрудняют осуществление рабочего цикла станка, могут управляться по заданной программе.
Рассмотрим классификацию нагрузочных устройств по характеру создаваемых сил и с учетом их приспособленности для программного метода испытания (табл. 3). Имитируя силы резания, эти устройства создают нагрузки, которые являются внутренними силами станка, при взаимодействии шпинделя и суппорта или стола станка.
![]() |
По методу создания сил нагрузочные устройства можно разделить на контактные и бесконтактные. При контактном методе обычно ползун нагрузочного устройства, установленного на суппорте или столе станка, упирается через ролик в оправку шпинделя. Нагрузка создается при помощи механических, динамометрических или гидравлических устройств. Контактный способ нагружения более пригоден для статических испытаний станка. При вращении шпинделя условия контакта между роликом ползуна и оправкой существенно влияют на силовую картину процесса.
Для программного метода испытаний целесообразно применять бесконтактный метод нагружения и в первую очередь при помощи электромагнитных сил. Устройства этого типа позволяют также осуществлять наложение динамической составляющей на статическое значение силы. Характер сил, воспроизводимых нагрузочным устройством, статический или динамический — важный признак его совершенства (табл. 3).
Сила резания Р состоит из постоянной (статической) составляющей Ро и совокупности динамических гармоник с амплитудой Рi и частотой ωi: Р = Ро+ΣРisinωit. Эти гармоники, особенно если ограничиться одной первой, достаточно легко осуществить с помощью дополнительных обмоток на электромагните и этим приблизить характер нагружения к силам, действующим при обработке.
При контактном методе нагружения создание динамических составляющих возможно при помощи гидравлического пульсатора, однако эти конструкции получаются обычно более громоздкими.
Применяемые нагрузочные устройства также могут иметь постоянную точку приложения сил, что более характерно для контактных методов нагружения, и изменяющуюся при имитации процесса обработки детали. Для этой цели пригодны бесконтактные методы создания сил. Попытки разработки нагрузочных устройств, в которых и при контактном методе нагружения создается перемещение суппорта или стола станка, обычно не дают положительных результатов.
Очень важно при программном методе испытаний управлять не только величиной, но и направлением силы. Изменение направления сил может существенно повлиять на выходные параметры станка, поскольку вся схема сил резания, реактивные моменты, эпюры давлений на направляющих меняются. Применение нагрузочных устройств с возможностью изменять не только величину, но и направление сил описано ниже. Наконец, одной из главных особенностей нагрузочных устройств, используемых при программном испытании, являются методы управления нагрузками и регистрации результатов.
При обычных методах испытания широко применяют ручное нагружение (понимая под этим и ручное управление механизированным нагружением) и визуальный контроль за показаниями приборов, регистрирующими силы, устанавливаемые согласно программе испытаний. При программном методе должно осуществляться автоматизированное управление процессом нагружения по программе, заложенной в ЭВМ с использованием обратной связи для контроля за отработкой программы нагружения. В этом случае регистрация результатов испытания осуществляется в памяти ЭВМ с выводом данных на цифропечатающее устройство и дисплей. Разработка программных нагрузочных устройств, пригодных для испытания станка в автоматизированном режиме и имитирующих, в первую очередь, силовые, а в последующем и тепловые воздействия на станок, является актуальной, еще полностью не решенной задачей.
НАГРУЗОЧНЫЕ УСТРОЙСТВА ДЛЯ ТОКАРНЫХ СТАНКОВ
При создании программных нагрузочных устройств для токарных станков наиболее удобно закреплять их в суппорте станка, а нагрузку создавать за счет электромагнитных сил. При этом роль сердечника может играть оправка, закрепленная в центрах станка.
На рис. 28 показана схема разработанного нами программного нагрузочного устройства для токарных станков, обеспечивающая бесконтактное нагружение суппорта и шпинделя при их взаимном движении и возможность управления величиной и направлением силы [А. с. №988460 (СССР)].
Устройство состоит из якоря 1 в виде оправки, двух электромагнитов, состоящих из сердечника 2 и катушек 3, закрепленных в корпусе 4. Кронштейн корпуса закреплен в динамометре 5, установленном на суппорте станка 6. Данный динамометр (применялся универсальный динамометр УДМ-600) позволяет не только определять все составляющие нагружающей силы, но и использовать полученные данные для организации обратной связи в цепи управления нагрузочным устройством. Наличие обратной связи необходимо для учета величины зазора между якорем и сердечниками, который изменяется из-за деформации системы при различных нагрузках и при движении суппорта вдоль оправки.
Выход динамометра связан через блоки сравнения 7 с блоками управления 8 и с катушками устройства через усилитель 9.
Входной электрический сигнал Iвх, соответствующий номинальной силе Рн, выдается блоком управления 8. Через усилитель 9 он поступает на электромагнитную катушку 3 в виде силы тока Iэм . На выходе преобразователя сила
(1)
где Kэм — коэффициент пропорциональности, определяемый магнитными свойствами электромагнита; δн — номинальный воздушный зазор между якорем и сердечником электромагнита.
Сила Рн, действующая на упругую систему станка, вызывает ее деформацию, что приводит к уменьшению воздушного зазора δн на величину Dδ:
(2)
где j — жесткость упругой системы в направлении воздушного зазора; b —разница в величине воздушного зазора, обусловленная различием прогиба оправки в фиксированных сечениях и погрешностью формы оправки.
Реальный зазор δ=δн—Dδ и определяет развиваемую силу Р. Эта сила может быть вычислена по формуле (1) при подстановке δ вместо δн.
Сила Р регистрируется измерительным преобразователем обратной связи динамометра 5 и преобразуется в электрический сигнал обратной связи Iос. Этот сигнал поступает в блок сравнения 7, на выходе которого величина рассогласования DI между входным сигналом Iвх и сигналом обратной связи Iос суммируется с выходным сигналом.
При этом
(3)
Расчеты показывают, что использование обратной связи при управлении нагрузками позволит примерно в 1,5 раза повысить точность имитации сил резания. Например, при заданной нагрузке Р=2000 Н, жесткости упругой системы j=20000 Н/мм, воздушном зазоре электромагнитного преобразователя δ=0,5 мм величина рассогласования по силе тока DI=0,56Iвх.
Схема нагружения, показанная на рис. 28, обеспечивает возникновение сил в плоскости. Для имитации осевой составляющей силы резания суппорт через трос и устройство барабанного типа нагружается электромагнитным порошковым тормозом, который также управляется от ЭВМ.
Электромагниты устроены таким образом, что имеют обмотки постоянного и переменного тока, поэтому можно моделировать не только среднее значение силы, но и накладывать на нее динамическую составляющую синусоидального типа. Развиваемая каждым электромагнитом сила —до 2500 Н.
Другое, бесконтактное, электромагнитное нагрузочное устройство, управляемое от вычислительного комплекса «Искра 1256» и позволяющее изменять также и точку приложения силы, показано на рис. 29, а.
Нагрузочное устройство содержит якорь 1, выполненный в виде гладкого цилиндра, закрепленного в шпиндельном узле станка. Роль электромагнита в данном устройстве выполняет сердечник 2, имеющий вид замкнутого многополюсного статора, установленного зазором концентрично якорю 1. Полюсы сердечника 3 имеют Т-образную форму и снабжены катушками возбуждения 4. Сердечник 2 установлен в круглом корпусе 5, закрепленном в динамометре б типа УДМ, который, в свою очередь, находится на каретке 7 суппорта/станка. Кроме статора имеется электромагнит 8 с обмоткой возбуждения Р, который жестко закреплен на корпусе сердечника 3 и установлен с зазором по отношению специальной направляющей 10, параллельной направлению продольной подачи суппорта.
![]() |
Обмотки возбуждения статора соединены между собой попарно. При их подключении к источникам питания 14 типа Б5-46 возникает электромагнитное взаимодействие, приводящее к возникновению сил, моделирующих составляющие силы резания (на рис. 29, б показаны силы Р1 и Р2, возникающие при подключении к источникам питания только двух пар катушек возбуждения). Равнодействующая сила Р от электромагнитных сил, возникающих между статором и ротором устройства, проходит через ось центров станка и может иметь произвольную пространственную ориентацию.
Управление параметрами вектора Р осуществляется от вычислительного комплекса с микроЭВМ типа «Искра-1256». При этом по программе, введенной в процессор 11 через встроенный цифроаналоговый преобразователь 12 управляющие сигналы поступают к источникам питания 14. Для управления одновременно несколькими источниками питания в электрическую цепь управления введен блок 13(см. с. 230).
Дополнительная сила Р, используется для того, чтобы иметь возможность регулировать смещение точки приложения моделирующей силы относительно оси центров станка.
Действительно, перенос силы Р из центра О1, в точку О2, находящуюся на расстоянии а от центра (рис. 29, б), равнозначен добавлению момента М=Рва, где Рв —вертикальная составляющая силы Р.
Этот момент и создается силой Р3, приложенной в точке О3, на дополнительном электромагните, закрепленном на расстоянии b oт центра О1. Величиной силы Рв=а/в также можно управлять рассмотренным методом. Таким образом, в данном нагрузочном устройстве при постоянном сердечнике (оправке) можно управлять не только величиной и направлением, но и точкой приложения силы, моделирующей силу резания, действующую на узлы станка при обработке деталей разных диаметров.
НАГРУЗОЧНОЕ УСТРОЙСТВО ДЛЯ ФРЕЗЕРНО-РАСТОЧНЫХ СТАНКОВ
При создании программных нагрузочных устройств для станков фрезерно-расточной группы нужно учитывать их особенности как с точки зрения расположения этих устройств, так и по характеру действующих сил.
При расточных работах необходимо обеспечить вращение вектора сил, а также его перемещение вдоль оси обрабатываемого отверстия. При этом вектор сил имеет статическую и динамическую составляющие и может изменяться в определенных пределах, в том числе скачкообразно при обработке ступенчатых отверстий.
Рассмотрим разработанное нами программное нагрузочное устройство для имитации этих воздействий на фрезерно-расточных станках средних размеров с горизонтальным расположением шпинделя (рис. 30) [А. с. № 994130 (СССР)]. В устройстве применен бесконтактный электромагнитный способ создания сил с возможностью создавать и динамическую составляющую. Приспособление устанавливается на столе станка, а в шпиндель 1 вставляется оправка 2, на конце которой закреплен сердечник электромагнита 4. Сердечник имеет две обмотки постоянного и переменного тока для создания соответственно статической и динамической составляющих сил. Для питания электромагнита при вращении шпинделя на оправке имеются контактные кольца 3. На столе станка установлен корпус нагрузочного устройства 5, в расточку которого входит оправка с электромагнитом. Корпус с отверстием играет роль якоря при возникновении электромагнитных сил. При взаимодействии сердечника и якоря возникает сила, вектор которой вращается и перемещается при подаче стола или ползуна шпинделя. В данном устройстве была обеспечена постоянная сила 200 Н и переменная 25 Н, что соответствует режимам, применяемым для расточных станков дайной группы.
Для полной имитации всех сил, действующих в процессе обработки, необходимо также создавать крутящий момент на шпинделе и составляющую силы вдоль оси шпинделя. Крутящий момент создается при помощи порошкового тормоза 7 (мод. ПТИ-2,5 м), который через клиноременную передачу соединен с вращающейся оправкой. Шкив 6 находится на шариковом подшипнике, расположенном в корпусе приспособления. Крутящий момент от оправки к шкиву 6 передается через скользящую шпонку.
Осевая нагрузка создается при помощи соленоида 8, в который входит шток, закрепленный на оправке. Шток имеет дополнительную опору в виде шарикового подшипника, закрепленного в корпусе соленоида. При осевом перемещении оправки со штоком в соленоиде создается сила сопротивления, величина которой также регулируется.
Все силовые нагрузки, создающиеся в данном устройстве, устанавливаются согласно заданной программе, а их значения контролируются и регистрируются.
На рис.30 показана также схема питания и регистрации параметров при функционировании нагрузочного устройства. Питание постоянным током производится от источника постоянного тока (ИПТ) типа ВС-24 м через контактные кольца оправки. ИПТ позволяет регулировать силу тока в необходимых пределах I=0... 5 А при напряжении U=0...12 В.
Питание переменным током с регулируемой частотой производится от генератора звуковой частоты ГЗ-33 через трансляционный усилитель ТУ-600. Усиленный сигнал необходимой мощности (I=0... 1А; U=0... 30В) и частоты через токосъемник и контактные кольца передается на обмотку переменного тока электромагнита.
Результирующее силовое воздействие на исследуемый объект регистрируется при помощи тензометрических преобразователей ТП, наклеенных на внутренней стороне полой оправки. Преобразователи наклеены вдоль образующей в сечении, в котором действует радиальная электромагнитная сила F. Они собраны в полумостовую схему и их три конца выведены наружу через специальное отверстие, проложены в пазу на наружной поверхности оправки и припаяны к трем контактным кольцам. Через токосъемник и переходник преобразователи подсоединены к усилителю ТА-5, сигнал с которого через переходник шлейфов ПШ выводится на осциллограф Н-
115.
Положение оправки контролировалось при помощи измерительных преобразователей ИП индуктивного типа, также соединенных в мостовую схему. При автоматизированном эксперименте управление блоками питания и соответственно силами осуществляется от микро-ЭВМ.
НАГРУЗОЧНЫЕ УСТРОЙСТВА ДЛЯ ИМИТАЦИИ ВНЕШНИХ ВОЗДЕЙСТВИЙ
Согласно алгоритму программного испытания станка (см. рис. 5) необходимо оценить реакцию станка и на комплекс внешних воздействий не связанных с осуществлением на станке рабочих процессов.
К этой категории относятся в первую очередь вибрационные воздействия, передающиеся через фундамент или бетонное полотно цеха, на котором установлен станок, и тепловые воздействия от внешней среды и работающих по соседству со станком устройств и машин.
Вибрационные воздействия на станок могут описываться тригонометрическим рядом с различными частотами, фазами и амплитудами, значения которых зависят от условий эксплуатации и характеризуют «динамическую картину» окружающей среды. Параметры тригонометрического ряда проявляются как случайные величины.
Для того, чтобы оценить реакцию станка на наиболее характерные условия его эксплуатации, необходимо проанализировать эти условия с позиций оценки вибрационных характеристик. Так, частотный анализ спектра внешних воздействий позволит выявить частоты, для которых имеют место наиболее интенсивные вибрационные воздействия.
Следует провести анализ наиболее тяжелых условий эксплуатации из тех, в которых может находиться станок данной модели с тем, чтобы выяснить, насколько они могут исказить выходные параметры станка по сравнению с отсутствием внешних вибрационных воздействий.
Для этого необходимо иметь программное нагрузочное устройство, которое будет нагружать плиту, на которой установлен станок, колебаниями, амплитуда, частоты и фазы которых отражают спектр эксплуатационных воздействий. Таких устройств в настоящее время не имеется, хотя все элементы его существуют.
Например, применяют управляемые вибраторы, которые могут быть собраны в блок (мультивибратор). Каждый моновибратор этого блока воспроизводит свой элементарный процесс гармонических колебаний со своими характеристиками.
Установленный на фундаментной плите мультивибратор MB (рис. 31) управляется от ЭВМ и осуществляет программное нагружение вибрационными колебаниями. Анализатор А дает информацию о действительном спектре колебаний и является сигналом обратной связи для коррекции программы управления испытанием.
При программном испытании рекомендуется сравнить выходные параметры станка при наличии динамического вибрационного поля и без него, оценить эффективность виброопор или других устройств для установки станка и сделать вывод о необходимости учитывать в блок-схеме испытания внешних вибрационных воздействий.
Тепловые внешние поля, действующие на станок, наиболее характерны при его эксплуатации вне термоконстантных помещений. Тепловые потоки также имеют случайный характер и, если станок имеет слабую сопротивляемость этим воздействиям, то возможны отказы по точности высококачественного во всех других отношениях станка. Поэтому при программном методе необходимо испытание станка с учетом влияния на его выходные параметры различных вариантов тепловых потоков, которые могут иметь место в процессе эксплуатации. Для этой цели необходимо иметь программное нагрузочное устройство, обдувающее станок тепловыми потоками различной интенсивности и температуры, отражающими спектр возможных внешних тепловых воздействий на станок.
На рис. 32 показана схема программного устройства для управления тепловыми потоками при испытании станка.
В устройстве с помощью вентилятора создается воздушный лоток, который может изменяться по скорости, мощности, направлению и температуре. Оно позволяет имитировать тепловые воздушные потоки, воздействующие на металлорежущее оборудование при его эксплуатации. В устройстве обеспечено программное управление от ЭВМ направлением, мощностью и интенсивностью потоков. Это осуществляется с помощью приводов перемещений и поворота теплообменного аппарата 3, 4, 6 вокруг осей X и У. От вычислительной машины производится также управление частотой вращения вентилятора 5, температурой воздушной струи с помощью изменения силы люка в нагревателе 2 и диаметром потока за счет раскрытия заслонок 1.
Практика показывает, что на температурное поле станка существенное влияние оказывают интенсивность, направленность и температура потоков СОЖ. При программном методе необходимо учитывать этот фактор, проводя испытания с разными уровнями интенсивности действия СОЖ и оценивая изменение тепловых полей и его влияние на миграцию областей состояний выходных параметров станка.
ПРОГРАММНОЕ НАГРУЖЕНИЕ С ПРИМЕНЕНИЕМ ПРОЦЕССА РЕЗАНИЯ
Программные нагрузочные устройства, имитируя силы, возникающие при обработке различных изделий, лишь с определенной степенью приближения отражают действительную силовую картину.
Даже в том случае, когда учитывается и динамическая составляющая, она обычно воспроизводится в виде простого синусоидального процесса, хотя при резании изменение сил во времени имеет весьма сложный характер. Процесс резания сопровождается сложными термодинамическими явлениями в зоне резания, он взаимодействует с упругой системой станка, на его протекание влияет большое число факторов [24, 36], и все это определяет сложность временных зависимостей для сил резания.
При программном методе испытания предусматривается обработка типовой детали, наиболее полно отражающей характерные особенности обрабатываемых деталей и на ней проверяется близость полученных результатов к действительным условиям. Большее приближение программного нагружения к действительной картине процесса будет получено в том случае, если в программу управления нагрузочным устройством будет заложена информация о реальном процессе резания.
На рис. 33 показана схема такого метода испытания. Вначале на исследуемом станке осуществляется обработка нескольких деталей с типовыми режимами обработки (например, легким, средним и тяжелым с точки зрения силовых воздействий). Обработка осуществляется с применением динамометра УДМ, позволяющего измерить и записать всё составляющие силы резания Рх, Ру , Рz с их динамическими составляющими.
![]() |
Эти данные должны быть положены в основу управляющей программы ЭВМ, которая через блок управления должна реализовать на программном нагрузочном устройстве ПНУ кривые P=f(t).
Для этой цели оценивается математическое ожидание и дисперсия сигнала, осуществляется его спектральный анализ, учитывается случайная составляющая типа «белый шум» и производятся другие процедуры, позволяющие представить структуру зависимости P=f(f). Программное нагрузочное устройство может реализовать эту зависимость с требуемой степенью точности для полученных из опыта данных по типовым режимам, в то время как для программного испытания надо воспроизводить весь диапазон применяемых на станке режимов.
Исследования в области теории резания дают зависимости, которые можно положить в основу для коррекции этих данных применительно к режимам резания, которые не были реализованы на станке.
В общем случае каждую составляющую сил резания Рi (т. е. Рx, Рy или Рz) можно представить как [24]:
где t и S — соответственно глубина резания и подача; HВ- твердость обрабатываемого материала по Бринеллю; Сi, ni, mi, ki — коэффициенты, отражающие условия резания и применяемый инструмент.
Значения указанных коэффициентов находят в справочниках или получают из специально поставленных экспериментов. В этом случае возможна коррекция экспериментально полученных зависимостей для применения их в качестве управляющих сигналов для тех режимов резания, которые не относятся к типовым и не были опробированы. Память ЭВМ должна хранить данные для такой коррекции и осуществлять ее в процессе программного испытания.
Предложенный метод управления программным нагрузочным устройством даст значительно большее приближение к действительности для силовых воздействий на станок при их имитации в процессе испытания. Разработка различных типов программных нагрузочных устройств — важный этап в развитии программного метода испытания технологического оборудования.
93 Испытание станков (приемо-сдаточные испытания)
По существующим техническим условиям приемо-сдаточные испытания оборудования можно разделить на следующие этапы:
Установка и выверка станка.
Если станина жесткая (длина/высота <1,5...2), то станок ставят на 3 точки опоры, в противном случае – на большее число опор. Используя клиновые башмаки, станок выверяют с помощью уровня в продольном и поперечном направлениях так, чтобы погрешность не превышала 0,02…0,04 мм/м. Прецизионные станки ставят на отдельный виброизолированный фундамент.
Отклонение температуры окружающей среды от номинала в период проверок не должно превышать:
Для станков класса точности С - ±0,5º С,
Для станков класса точности А и В - ±1º С.
Дата добавления: 2018-06-27; просмотров: 1149; Мы поможем в написании вашей работы! |
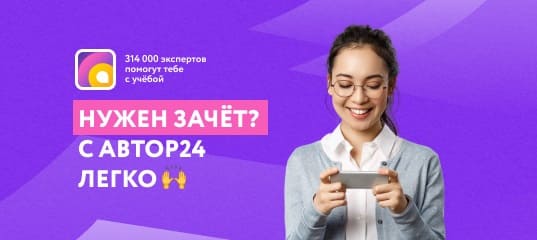
Мы поможем в написании ваших работ!