Выполнение под руководством работника, имеющего право самостоятельного проведения работ, отдельных операций по внедрению новой техники и освоению передовых технологий.
При создании нового оборудования значительную часть времени от технического задания до серийного производства занимают различного рода испытания, которые увеличивают сроки внедрения новой техники. Однако проведение испытаний – совершенно необходимый этап в процессе разработки и внедрения новой техники.
Испытания позволяют:
на стадии научно-исследовательских работ (НИР) и разработки проектной документации – выбрать оптимальный вариант конструктивных решений, выбрать материалы;
в процессе разработки и приемки опытных образцов оценить соответствие показателей надежности элементов изделия и конструкции в целом требованиям технического задания;
на стадии освоения производства новой техники – оценить возможности технологического процесса завода-изготовителя в обеспечении заданного уровня надежности при серийном производстве;
на стадии установившегося серийного производства – контролировать работоспособность выпускаемых машин по завершении технологического процесса их изготовления, периодически проверять соответствие показателей надежности требованиям технических условий, контролировать стабильность производства по этим показателям;
при усовершенствовании серийной продукции – оценить эффективность внесенных изменений по показателям надежности;
на стадии ремонта – проверять качество ремонта.
На различных стадиях проектирования и изготовления станков испытания носят различный характер. На стадии НИР и на первых этапах разработки конструкторской документации должны проводиться два вида испытаний материалов:
|
|
испытания в эталонных условных режимах, которые позволяют получить объективную сравнительную оценку показателей качества материалов, влияющих на надежность;
испытания в контролируемых условиях внешних воздействий, которые обеспечивают моделирование режимов эксплуатации в реальных условиях.
Все испытания первого вида проводятся по стандартным методикам, к которым относятся определение относительной износостойкости материалов при трении о закрепленный абразив (ГОСТ 17367-71); определение прочности (ГОСТ 21318-75); определение предельных нагрузочных характеристик: предела выносливости (ГОСТ 2860-65), критической температуры смазочных масел при трении (ГОСТ 17604-72), максимально несущей способности по критерию задира и др.
При испытаниях второго вида учитываются конструктивные и эксплуатационные особенности работы реальных узлов. Для узлов трения такие испытания проводятся на машинах трения с герметическим и тепловым моделированием сопряжений с учетом эксплуатационных нагрузок, скоростей, температур и т.д. Результаты этих испытаний для различных материалов сопоставляются, что дает возможность выбрать лучшие материалы для данных условий работы.
|
|
При испытании узлов станка оценивают долговечность и безотказность работы применительно к типовым режимам нагрузок, в качестве которых могут использоваться режимы максимальных нагрузок или скоростей.
В системе испытаний очень важным является рациональное сочетание испытаний отдельных элементов изделия и изделия в собранном виде. Преимущества поэлементных испытаний заключаются в следующем:
испытания обеспечивают получение информации о надежности машины на более ранних этапах создания, например на стадии разработки его отдельных узлов. Данные, полученные по результатам испытаний отдельных узлов, могут использоваться для их конструктивной и технологической доводки. Доводка на ранних этапах разработки дает большой экономический эффект, так как на более поздних стадиях изготовления всякая доводка одного узла приводит к изменению (иногда существенному) конструкции и технологии изготовления других узлов;
испытания дают возможность на большом статистическом материале определить надежность машины, оптимальную надежность узлов и деталей.
|
|
Выполнение работ по проведению модернизации электрического и электромеханического оборудования, внедрению новой техники и освоению передовых технологий
Большинство промышленных предприятий нашей страны работают на морально и физически устаревшем оборудовании произведенном 15 и более лет назад. Основными недостатками данного оборудования являются низкая ремонтопригодность в связи с отсутствием запчастей, относительно низкий уровень производительности и качества выпускаемой продукции, частые простои из-за выхода из строя отдельных узлов оборудования, большие затраты времени на поиск неисправности.
Для решения этой проблемы наилучшим способом является установка современного оборудования в замен устаревшего. Но основным препятствием для реализации данного способа зачастую служит высокая стоимость нового оборудования. При этом существует необходимость в остановке данной части технологической линии производства или снижения объемов производства на время проведения демонтажных работ, работ по подготовке к установке нового оборудования и проведения монтажных и пуско-наладочных работ.
|
|
Основным решением данной проблемы может являться замена устаревшего оборудования в несколько стадий. Как показывает опыт эксплуатации промышленного оборудования наибольшему влиянию времени подвержены приводная техника, электрооборудование и системы управления и автоматизации. Что касается силового электрооборудования, то в этом случае можно обойтись заменой устаревшей защитной и коммутационной аппаратуры на современную, более компактную и надежную, без изменения, или незначительного изменения, структуры и схемы питания установки.
Источник: http://www.elec.ru/articles/modernizaciya-starogo-oborudovaniya/
Ознакомление с видами работ по модернизации электрического и электромеханического оборудования и изучение способов их выполнения, освоение технологий их проведения. Выполнение отдельных видов работ (операций) по модернизации электрического и электромеханического оборудования с соблюдением технологий и правил охраны труда. Выполнение под руководством работника, имеющего право самостоятельного проведения работ, отдельных операций по внедрению новой техники и освоению передовых технологий.
Выполнение работ по подготовке к проведению испытаний, техническому освидетельствованию и сдаче в эксплуатацию вновь установленного или отремонтированного электрического и электромеханического оборудования.
Правила приёмки электроустановок в эксплуатацию
Смонтированные или реконструированные электроустановки и пусковые комплексы должны быть приняты в эксплуатацию в порядке, установленном действующими правилами.
Перед приемкой в эксплуатацию электроустановок должны быть проведены: приемосдаточные испытания оборудования и пусконаладочные испытания отдельных систем электроустановок; в период строительства и монтажа зданий и сооружений - промежуточные приемки узлов оборудования и сооружений, в том числе скрытых работ.
Приемосдаточные испытания оборудования и пусконаладочные испытания отдельных систем должны быть проведены подрядчиком (генподрядчиком) по проектным схемам после окончания всех строительных и монтажных работ по сдаваемой электроустановке.
Перед приемосдаточными и пусконаладочными испытаниями должно быть проверено выполнение ПУЭ, СНиП, государственных стандартов, включая стандарты безопасности труда, правил органов государственного надзора, правил техники безопасности и промышленной санитарии, правил взрыво- и пожаробезопасности, указаний заводов-изготовителей, инструкций по монтажу оборудования.
Дефекты и недоделки, допущенные в ходе строительства и монтажа, а также дефекты оборудования, выявленные в процессе приемосдаточных и пусконаладочных испытаний, должны быть устранены строительными, монтажными организациями и заводами-изготовителями до приемки электроустановок в эксплуатацию.
Перед приемкой должны быть подготовлены условия для надежной и безопасной эксплуатации электроустановок: укомплектован, обучен (с проверкой знаний) эксплуатационный персонал; разработаны эксплуатационные инструкции и оперативные схемы, техническая документация; подготовлены и испытаны защитные средства, инструмент, запасные части и материалы; введены в действие средства связи, сигнализации и пожаротушения, аварийного освещения и вентиляции.
До приемки в эксплуатацию электроустановки должны быть приняты потребителем (заказчиком) от подрядной организации по акту. После этого потребитель (заказчик) представляет инспектору государственного энергетического надзора проектную и техническую документацию в требуемом объеме и электроустановки для осмотра и допуска их в эксплуатацию.
Приемка в эксплуатацию электроустановок с дефектами и недоделками запрещается. Включение напряжения на новые электроустановки после приемки их в эксплуатацию производится в соответствии с действующими «Правилами пользования электрической энергией».Состав работ при проведении испытаний оборудования
В состав бригады, проводящей испытания, могут быть включены лица из ремонтного персонала с группой по электробезопасности не ниже II для выполнения подготовительных работ, охраны испытываемого оборудования. До начала испытаний производитель работ должен проинструктировать этих работников о мерах безопасности при испытаниях.
В состав бригады, осуществляющей ремонт или монтаж оборудования, для проведения испытаний могут быть включены лица из персонала наладочных организаций или электролаборатории. В этом случае испытаниями руководит производитель работ либо по его указанию старшее лицо с группой по электробезопасности не ниже IV из персонала лаборатории или наладочной организации.
Проведение испытаний в процессе монтажа или ремонта оговаривается в наряде в строке "Поручается".Установки для проведения испытаний
На предприятиях существует разные установки для проведения испытаний электрооборудовании, например, испытательный стенд для испытаний обкатки электродвигателя напряжением на 380 и 500. В; испытательный стенд для испытаний дневного света и лампочки накаливания; оборудование для испытаний кабельных линий выпрямленным напряжением и определения мест повреждения кабельных линий; приборы для определения трасс, глубины залегания и определения мест повреждений изоляции силовых кабельных линий и испытательно-измерительные установки.Приемка оборудования из ремонта и оценка его качества
Приемку установок из капитального, среднего или текущего ремонта производит комиссия. В состав комиссии включаются:
- заместители главного инженера по эксплуатации и ремонту;
- общий руководитель ремонта установок;
- начальники цехов, в ведении которых находятся ремонтируемые установки;
- руководители ремонтных работ предприятий, участвующих в ремонте;
- инженер-инспектор по эксплуатации;
- инспектор по охране труда и техники безопасности;
- представители отдела планирования и подготовки ремонта.
Допускается включать в состав комиссии руководителей групп (цехов) наладки, лабораторий. В состав комиссии может входить представитель управляющей (генерирующей) компании.
Приемку оборудования, входящего в состав установок, из ремонта производят комиссии, возглавляемые начальниками эксплуатационных цехов.
Оценка качества отремонтированного оборудования, входящего в установку, и оценка качества выполненных ремонтных работ устанавливаются:
- предварительно - по окончании приемо-сдаточных испытаний;
- окончательно - по результатам подконтрольной эксплуатации, но не позднее 3 дней после ее окончания.
Оценка качества отремонтированной установки в целом устанавливается, по результатам подконтрольной эксплуатации.
Дата добавления: 2018-05-12; просмотров: 1226; Мы поможем в написании вашей работы! |
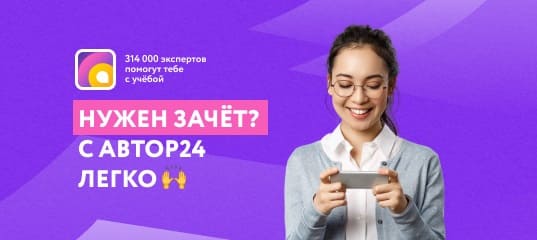
Мы поможем в написании ваших работ!