ВІДНОВЛЕННЯ ДЕТАЛЕЙ НАНЕСЕННЯМ
КОМПЕНСАЦІЙНОГО ШАРУ МЕТАЛУ
4.1 Наплавлення під шаром флюсу
Дуговим наплавленням під шаром флюсу відновлюють деталі з досить великим зносом (до 3...5 мм).
Цей спосіб дозволяє збільшити потужність зварювальної дуги за рахунок збільшення припустимої щільності струму до 150...200 А/мм2 (при ручному дуговому зварюванні електродом, що плавиться, струм не перевищує 15...30 А/мм2) без небезпеки перегріву електрода. Продуктивність сварочно-наплавочных робіт підвищується в 6...7 разів у порівнянні з ручним дуговим зварюванням.
Горіння дуги під шаром флюсу сприяє різкому зниженню теплообміну із зовнішнім середовищем, у результаті чого питома витрата електроенергії при наплавленні металу зменшується з 6...8 до 3...5 кВт-ч/кг. Значно поліпшуються умови формування наплавленого металу і його хімічний склад. Так, наприклад, кисню в наплавленому шарі в 20 разів, а азоту втроє менше, ніж при наплавленні ручним електродом.
Механізація процесу дозволяє скоротити втрати електродного матеріалу на розбризкування й недогарки з 20...30 до 2,..4%, а також знизити вплив кваліфікації зварника на якість сварочно-наплавочных робіт.
Розрахунок режимів автоматичного наплавлення під шаром флюсу
Швидкість наплавлення VH, м/ч
(4.1)
де – коефіцієнт наплавлення, г/Агод (при наплавленні постійним струмом зворотної полярності
= 11—14;
|
|
сила струму, А;
товщина наплавленого шару, мм;
– крок наплавлення, мм;
— щільність електродного дроту, г/см3 (
= 7,85).
Сила струму приймається в залежності від діаметру поверхні деталі, що наплавляється і діаметру електродного дроту по таблиці 4.1
Таблиця 4.1. Залежність сили струму від діаметрів деталі і електродного дроту
Діаметр шийки деталі, що наплавлюється d, мм | Сила струму, А при діаметрі електродного дроту dдр, мм | |
dдр=1,2 – 1,6 | dдр=2,0 – 2,5 | |
30...40 40...50 50...60 60...75 75...100 100...200 | 80...100 100..120 120...140 140...170 170...200 200...250 | 100...120 120...140 140...160 160...220 220..280 280...350 |
Частота обертання деталі n,
, (4.2)
де d — діаметр деталі, мм.
Швидкість подачі дроту , м/год
, (4.3)
де — діаметр електродного дроту, мм;
Крок наплавлення , мм/об
. (4.4)
Виліт електрода, мм
. (4.5)
Зсув електрода , мм
. (4.6)
Параметри режиму наплавлення підставляти у формули без зміни розмірностей.
Товщина покриття , мм, що наноситься на зовнішні циліндричні поверхні, визначається по наступній формулі:
|
|
(4.7)
де знос деталі, мм;
z1 – припуск на механічну обробку після нанесення покриття, мм.(див.таблицю 12)
товщина шару металу, що знятий при підготовці поверхні до наплавлення звичайно приймають
мм.
Застосовуються наступні марки дротів: Нп-40, Нп-80, Нп-50М, Нп-65М, Нп-30ХГСА.
Флюси: АН-348А, ОСЦ-45, АНК-19 таі ін.
Твердість і відносна зносостійкість наплавленного шару металу під флюсом АН348А наведена в таблиці 4.2
Таблиця 4.2. Твердість і відносна зносостійкість наплавленного шару металу під флюсом АН348А
Дата добавления: 2018-05-12; просмотров: 216; Мы поможем в написании вашей работы! |
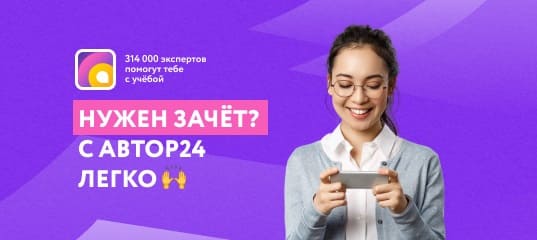
Мы поможем в написании ваших работ!