Проектирование крюковой подвески
Крюковые подвески
Крюковые подвески служат для соединения крюка с канатом. Если груз подвешивается на одной ветви каната, то последний соединяется с крюком посредством коушей, клиновых или конических втулок. При двух и более несущих ветвях применяют типовые крюковые подвески, являющиеся одновременно подвижными обоймами полиспастов. Крюковые подвески бывают двух типов: нормальные и укороченные (рисунок 5.1.).
Нормальная крюковая подвеска (рисунок 5.1, а) состоит из двух щек 1, усиленных серьгами 2 и образующих кожух подвески. Щеки и серьги имеют соосные отверстия: верхние – для оси 3 блока 4, нижние – для цапф траверс 5 крюка 6. Крюк 6 удерживается на траверсе при помощи гайки 7, опирающейся на упорный подшипник 8. Число блоков в подвеске зависит от кратности полиспаста. Блоки могут монтироваться на подшипниках скольжения или качения.
Укороченные подвески (рисунок 5.1, б) применяют для канатных одинарных и сдвоенных полиспастов с четной кратностью. В укороченной подвеске ось блоков и траверса крюка изготавливаются как одно целое, а крюк имеет удлиненный хвостовик (тип Б). С каждой стороны крюка располагается равное число блоков. Укороченные подвески имеют меньший размер по высоте по сравнению с нормальными подвесками. Это позволяет увеличить высоту подъема груза при прочих равных условиях. Размеры крюковых подвесок нормализованы. Выбор типовой крюковой подвески производится из каталога по заданному значению грузоподъемности, типу полиспаста и его кратности, а также характеристике режима работы.
|
|
а – нормальная; б) укороченная
Рисунок 5.1. Типы крюковых подвесок
При выборе типоразмера крюковой подвески необходимо соблюдение двух условий:
а) грузоподъемность крюковой подвески не должна быть меньше заданной грузоподъемности: Qп ≥ Q;
б) режим работы крюковой подвески должен соответствовать режиму работы механизма.
После выбора крюковой подвески необходимо выписать ее условное обеспечение и техническую характеристику. Эскиз подвески приводится в расчетно-пояснительной записке. На эскизе приводятся габаритные и присоединительные размеры.
В том случае, если число блоков выбранной крюковой подвески отличается от числа блоков на предварительно принятой кинематической схеме механизма, то необходимо уточнить кинематическую схему, а именно схему полиспаста. После этого следует определить передаточное число (кратность) полиспаста.
После уточнения кинематической схемы механизма и типоразмера крюковой подвески проводят проверочный расчет ее отдельных элементов.
Расчет крюковой подвески
|
|
Методика расчета приведена на примере одноблочной нормальной крюковой подвески. Подвески другой конструкции рассчитываются аналогично.
Исходными данными для расчета крюковых подвесок (рисунок 5.2) являются: грузоподъемность механизма Q; кратность полиспаста а; диаметр каната dk; скорость подъема груза υгр; группа режима работы механизма подъема. По рекомендациям раздела 3 выбрана и проверена заготовка крюка.
Расчет крюковой подвески целесообразно вести в следующей последовательности.
5.2.1. Выбор подшипника. Для фиксации крюка по значению d1 для принятого крюка по таблице П3.2 выбираем упорный подшипник ([2], таблицы 110 и 111) и проверяем его пригодность по статической грузоподъемности
Fa > C0 (5.1)
Эквивалентная статическая нагрузка
Fa = Q·KБ·КТ (5.2)
где Q- осевая нагрузка, равная грузоподъемности механизма; KБ = 1,2…1,25 – коэффициент безопасности; КТ = 1 – температурный коэффициент; C0 – статическая грузоподъемность подшипника (указана в каталогах на подшипники).
5.2.2 Расчет траверсы крюковой подвески состоит из двух этапов: определение конструктивных размеров траверсы и проверка ее на прочность.
|
|
Основные конструктивные размеры траверсы (см. рисунок 5.3) можно определить по следующим соотношениям:
- длина траверсы с одним канатным блоком | lт= (1,15…1,25) Dп; |
- расчетная высота траверсы | H0=L - (l1+l2+H); |
- диаметр отверстия в траверсе под хвостовик крюка | dкр = d1+(2…5); |
- габаритная высота траверсы | Hт=H0+0,8 H, |
где Dп и Н - соответственно наружный диаметр и высота подшипника; L, l1, l2 d1 – размеры крюка.
![]() | 1 – крюк; 2 – траверса; 3 – упорный подшипник; 4 – гайка накидная; 5 – кожух; 6 – блок; 7 – ось блока; 8 – планка боковая; 9 – радиальный подшипник. Рисунок 5.2. Крюковая подвеска |
Диаметр цапфы dц и ширина траверсы В определяются из расчета данных сечений на прочность.
Рисунок 5.3. Эскиз траверсы.
Напряжение изгиба в сечении d–d (рисунок 5.3)
, (5.3)
где Ми – изгибающий момент в сечении; W – момент сопротивления сечения.
Изгибающий момент в сечении определяется по формуле:
, (5.4)
где δ – толщина накладки; δ1 – толщина кожуха. В предварительных расчетах можно принимать: толщину кожуха δ1=5…10 мм и толщину накладки δ=6…18 мм.
Момент сопротивления сечения:
(5.5)
|
|
Допускаемое напряжение при изгибе:
, (5.6)
где σ-1 – предел выносливости при изгибе; ns - коэффициент запаса прочности; К – коэффициент концентрации напряжений. Предел выносливости при изгибе для материала траверсы рекомендуется принимать по таблице 4.2. Коэффициент запаса прочности в зависимости от режима работы механизма должен приниматься по таблице 4.3. Коэффициент, учитывающий концентрацию напряжений можно принимать К=2.
Таким образом, диаметр цапфы равен:
. (5.7)
Определение ширины траверсы (размер В).
Момент изгиба в сечении в – в:
(5.8)
Момент сопротивления сечения:
. (5.9)
Выполнив необходимые преобразования, получим выражение для определения ширины траверсы:
(5.10)
Входящие в формулу (5.12) обозначения даны ранее.
5.2.3 Определение размеров оси блока
Нагрузка на ось блока (рисунок 5.4) передается через два радиальных подшипника, распределяясь между ними равномерно.
Выбор материала оси блока рекомендуется производить по таблице 4.2.
Максимальный изгибающий момент, воспринимаемый осью:
.
Из соотношения определяем расчетное значение диаметра оси блока:
. (5.11)
Окончательно размер диаметра оси принимается после выбора и проверки радиальных подшипников.
Рисунок 5.4. Расчетная схема оси блока.
5.2.4 Подбор подшипников качения для оси блока выполняется по методике, изложенной в [3]. В данном случае необходимо иметь в виду тот факт, что вращается внешнее кольцо подшипника, поэтому кинематический коэффициент принимается равным V=1,2. Необходимые данные для выбора и расчета радиальных подшипников качения приведены в таблицах 96…99 [3].
5.2.5 Расчет размеров боковых планок выполняется из условия обеспечения прочности планки на растяжение и допускаемого удельного давления. Расчетная схема боковой планки представлена на рисунке 5.5.
Удельное давление на поверхности контакта планки с цапфой:
q=Q/(2dцd)<[q] (5.12)
где [q] – допускаемое удельное давление, принимаемое равным 30…35 МПа. Из формулы (5.12) толщина планки:
d=Q/(2dц[q]) (5.13)
Ширину планки Вп определяем из соотношения:
откуда
(5.14)
Планки изготавливают из стали Ст.3 обыкновенного качества по ГОСТ 380-71. Для данной стали допускаемое напряжение на растяжение принимается равным [s]p=90 МПа.
![]() | Рисунок 5.5. Расчетная схема планки |
5.2.6 Выбор блоков для крюковых обойм.
Минимальное значение диаметра блока, исходя из условия ограничения напряжения изгиба каната, определяют по формуле (4.1.). Найденное значение Dбл округляется до ближайшего стандартного размера.
Принимая конкретные значения Dбл, следует обращать внимание на то, чтобы наружный диаметр подшипника совпадал с размером d, а длина ступицы Н была не меньше двойной ширины подшипника оси.
Если по расчетным данным невозможно подобрать блок из таблицы, то конструкцию разрабатывают самостоятельно.
Монтажные блоки
Блоки, служащие для поднятия и перемещения груза, называются грузовыми монтажными блоками. Грузовые блоки могут быть однорольными и многорольными. Их грузоподъёмность зависит от диаметра и количества роликов. Однорольные блоки, служащие для изменения направления тягового каната, называются отводными.
Рабочим органом блока (рисунок 5.6) является один или несколько роликов(1), насаженных на ось (4). Ролик по наружному диаметру имеет канавку для каната, называемую ручьём. Размеры ручья зависят от максимально допустимого диаметра каната, идущего через блок. Ось блока (4) закреплена между двумя щеками (2), которые усилены тягами (3). Ось ролика вращается в чугунных или бронзовых втулках, либо в подшипниках качения. В верхней части щёк имеется верхняя траверса (7) , к которой крепится петля для закрепления конца каната полиспаста или крепления стропа. В нижней части - нижняя траверса (5), к которой крепится крюк, который имеет возможность вращаться вокруг оси на 3600. К крюку подвешивается груз.
1- –ролик; 2- щёки; 3- тяги; 4-ось ролика; 5 - нижняя траверса;
6 - грузовой крюк; 7 верхняя траверса; 8 – петля
Рисунок 5.6. Схема однорольного блока
В многорольном блоке, состоящем из нескольких роликов, все ролики на своих осях вращаются самостоятельно, независимо друг от друга, и отделены друг от друга щеками. Это сделано для того, чтобы исключить попадание каната между телом ролика и каната.
Монтажные блоки подбираются из трёх условий:
1) усилия, действующего на блок (грузоподъёмность блока);
2) максимально допустимого диаметра каната для блока. Он должен быть равным или больше диаметра каната, идущего на грузоподъёмный механизм;
3) диаметр блока должен быть больше или равным диаметру, определённому из условия, когда можно не учитывать дополнительное напряжение, возникающее от изгиба каната.
Пример
Подобрать грузовой блок, если усилие действующее на блок равно 29 кН, тяговое усилие создаёт электролебёдка, режим работы тяжёлый.
По справочникам подбираем грузовой блок однорольный грузоподъёмностью 30 кН, диаметром 225 мм, максимальный диаметр каната 17,5 мм. Канат для оснащения лебёдки:
R = S·K = 29·6 = 174 кН.
По справочным таблицам подобран канат двойной свивки ЛК-РО 6×36+ЮС диаметром 18 мм, что больше, чем 17,5 мм.
Подобранный блок не отвечает второму условию. Подбираем однорольный грузовой блок диаметром 250 мм с допустимым диаметром каната 19,5 мм, что больше 18 мм.
Определяем минимальный диаметр ролика блока D.
D > d·(Е - 1) = 18·(20 - 1) = 342 мм,
что больше диаметра 250 мм.
Поскольку не выдержано третье условие, подбираем однорольный блок диаметром 359 мм, что отвечает второму и третьему условиям и значительно превышает необходимую грузоподъёмность.
Однорольные блоки, применяемые в качестве отводных, изготавливают с откидной щекой (рисунок 5.7). Их преимущество перед обычным блоком состоит в том, что они позволяют быстро, без распасовки, удалить канат и изменить направление усилия. Отводные блоки можно использовать без крюка, а только с петлёй для крепления блока к якорю.
Усилие, действующее на отводной блок Q, определяется по формуле
где S - усилие в сбегающей нити каната H; α - угол между нитями каната, огибающими блок.
1 - отводной блок; 2 – тяговой канат; 3 - колонна;
4 - строп; 5 -прокладки
Рисунок 5.7. Схема крепления отводного блока к колонне
Пример 2
Определить усилие, действующее на отводной блок, и подобрать канат для привязки блока к колонне, если усилие на канат, идущее на лебёдку, составляет S=25,6 кН, а угол α между ветвями канатов, огибающих отводной блок равен 1200.
Решение:
Q=2·25,6 cos 600 = 51,2·0,5 = 25,6 кН.
По грузоподъёмности подбираем отводной блок диаметром 225 мм.
По усилию, действующему на строп, подбираем канат с учётом коэффициента запаса прочности, для стропа равным 6.
R = 25,6·6 = 153,6 кН
По таблицам подбираем канат двойной свивки типа ЛК - 3 конструкции 6×25+ЮС диаметром 17,5 мм с временным сопротивлением проволок разрыву 0=1770 И/мм .
6. ЗАДАНИЕ
на выполнение контрольной работы по дисциплине
6.1. Исходные данные
6.1.1. Габариты монтируемого фильтра и его вес (таблица 6.2)
6.1.2. Отметка металлической площадки, на которой нужно смонтировать фильтр (таблица 6.2).
6.1.3. Отметка оси неподвижного блока полиспаста, который крепится к узлу нижнего пояса фермы (рисунок 6.1).
6.1.4. Расстояние "А" от центра фильтра до колонны и место установки тяговой лебедки (таблица 6.2 и рисунок 6.1).
6.1.5. Тип лебедки и материал втулок блоков (таблица 6.2).
6.1.6. Схема строповки фильтра и угол раскрытия стропа (рисунок 6.2, таблица 6.2).
6.2. Схема монтажа фильтра:
Фильтр доставляется в зону монтажа и разгружается автокраном, затем на катках при помощи ручной рычажной лебедки перемещается под площадку.
Над местом монтажа к узлу нижнего пояса фермы подвесить собранной на отметке 0.0 полиспаст. Полиспаст запасовать по заранее рассчитанной схеме.
Подъем полиспаста к нижнему поясу фермы на заданную отметку произвести рычажной лебедкой. К колонне по оси "С" закрепить, заранее рассчитанным стропом, отводной блок. Установить тяговую лебедку. Нить каната, сбегающую с неподвижного блока полиспаста, пропустить через отводной блок и закрепить на барабан лебедки. Фильтр застропить на заводские петли фильтра 4-х ветвевым стропом и соединить строп с крюком подвижного блока полиспаста. Лебедкой поднять фильтр выше металлической площадки, к площадке приварить опорные конструкции и стравливая канат с барабана лебедки установить фильтр в проектное положение.
Таблица 6.1 - Исходные данные на контрольную работу
№ варианта | Вес груза, кН | а×b, м | h, мм | Отм. "1", м | Отм. "2", м | А, м | 2α, град | Лебедка | Материал втулок блоков | Примечание |
1 | 50 | 2.2×1.8 | 1.6 | 4.7 | 13.6 | 5.0 | 80 | ЛР-1.25 | Бронза | Лебедка барабанная ручная |
2 | 48 | 2.0×1.7 | 1.8 | 5.0 | 14.0 | 4.0 | 90 | ЛР-1.25 | Бронза | |
3 | 40 | 2.3×1.7 | 1.5 | 4.8 | 12.3 | 5.5 | 84 | ЛР-1.25 | Чугун | |
4 | 30 | 1.5×1.5 | 1.5 | 5.0 | 13.0 | 4.8 | 80 | ЛР-1.25 | Чугун | |
5 | 35 | 1.8×1.7 | 2.0 | 3.0 | 10.8 | 5.2 | 88 | ЛР-1.25 | Чугун | |
6 | 60 | 2.2×1.7 | 2.0 | 4.0 | 11.4 | 4.7 | 80 | ЛР-3.2 | Бронза | |
7 | 70 | 2.2×1.8 | 1.6 | 4.0 | 12.6 | 4.0 | 90 | ЛР-3.2 | Бронза | |
8 | 65 | 1.8×1.8 | 1.8 | 5.0 | 13.0 | 4.4 | 90 | ЛР-3.2 | Бронза | |
9 | 43 | 1.4×1.3 | 1.7 | 4.0 | 13.6 | 6.0 | 86 | ЛР-3.2 | Бронза | |
10 | 56 | 2.1×1.8 | 1.9 | 4.2 | 13.8 | 3.0 | 90 | ЛР-3.2 | Подшипник качения | |
11 | 20 | 1.6×1.4 | 1.1 | 4.0 | 10.8 | 4.2 | 78 | ЛР-1.25 | Чугун | |
12 | 28 | 1.7×1.6 | 1.7 | 3.8 | 9.9 | 3.9 | 76 | ЛР-1.25 | Чугун | |
13 | 32 | 1.7×1.6 | 1.8 | 3.9 | 9.6 | 4.2 | 90 | ЛР-1.25 | Бронза | |
14 | 38 | 2.0×1.0 | 2.0 | 2.7 | 11.9 | 4.8 | 90 | ЛР-1.25 | Бронза | |
15 | 54 | 2.1×1.6 | 1.6 | 2.8 | 12.0 | 5.0 | 90 | ЛР-1.25 | Бронза | |
16 | 26 | 1.6×1.4 | 2.3 | 3.2 | 10.0 | 3.8 | 90 | ЛР-1.25 | Бронза | |
17 | 55 | 2.8×1.9 | 2.4 | 3.6 | 12.7 | 4.2 | 90 | ЛР-3.2 | Подшипник качения | |
18 | 53 | 2.4×1.6 | 1.5 | 3.6 | 13.2 | 4.0 | 80 | ЛР-1.25 | Бронза | Лебедка приводная |
19 | 27 | 1.5×1.4 | 1.4 | 2.8 | 10.6 | 5.0 | 90 | ЛР-1.25 | Бронза | |
20 | 50 | Ø2 | 1.3 | 2.9 | 10.3 | 3.5 | 80 | ТЛ-9А-1 | Чугун | |
21 | 63 | Ø 2.2 | 1.4 | 2.3 | 8.1 | 4.1 | 88 | ПМ-2.5 | Бронза | |
22 | 47 | Ø 1.8 | 1.1 | 3.1 | 7.8 | 8.0 | 90 | ЛМ-1-80 | Чугун | |
23 | 47 | 1.5×1.4 | 1.2 | 3.6 | 10.0 | 6.0 | 84 | ЛМ-0,6За | Бронза | |
24 | 52 | 1.8×1.7 | 1.3 | 2.9 | 14.1 | 7.0 | 88 | ЛМ-1-50 | бронза |
6.3. Задание на выполнение контрольной работы
6.3.1. Произвести расчет четырехветвевого стропа по заданному весу фильтра, его габаритам и углу раскрытия стропа. Определить натяжение в ветвях стропа, подобрать стальной канат для изготовления стропа, определить длину ветви стропа и определить вес стропа.
6.3.2. Произвести расчет полиспаста, для чего определить нагрузку на подвижный блок полиспаста, определить кратность полиспаста, подобрать конструкцию подвижного и неподвижного блоков, определить нагрузку на неподвижный блок.
6.3.3. Произвести расчет усилия, воспринимаемого отводным блоком и подобрать отводной блок.
6.3.4. Произвести расчет универсального стропа для крепления отводного блока к колонне "С".
6.3.5. Определить необходимую длину каната для оснащения лебедки и сравнить с канатоемкостью, приведенной в каталоге. Если канатоемкость лебедки окажется недостаточной, предложить другую лебедку.
6.3.6. В графической части работы разработать схему монтажа фильтра, схему полиспаста.
Библиографический список
1. Александров М.П. Подъемно – транспортные машины: Учеб. для машиностроительных спец. вузов. –М.: Высш. школа, 1985. –520 с.
2. Анурьев В.И. Справочник конструктора – машиностроителя. В 3-х т. Том 1. –М.: Машиностроение, 1978. –728с.
3. Анурьев В.И. Справочник конструктора – машиностроителя. В 3-х т. Том 2. –М.: Машиностроение, 1979. –559 с.
4. Дольник A.M. Механизация такелажных работ при сооружении систем теплогазоснабжения и вентиляции [Текст]: учеб. пособие для студ. 4-го курса и дипломников спец. 270109 «Теплогазоснабжение и вентиляция» / A.M.Дольник; Воронеж. гос. арх.-строит. ун-т. - Воронеж, 2006. - 112 с.
5. Ковальский Б.С. Расчет канатных барабанов грузоподъемных машин. –Сборник научных трудов ВНИИПТМАШа. –М.: 1975, №6.
6. Курсовое проектирование грузоподъемных машин: Учеб. пособие для студентов машиностр. спец. вузов/С.А. Казак, В.Е. Дусье, Е.С. Кузнецов и др. ; Под ред. С.А. Казака. – М.: Высш. шк., 1989. – 319 с.
7. Мачульский И.И., Киреев В.С. Подъемно-транспортные и погрузочно-разгрузочные машины на железнодорожном транспорте: Учебник для вузов. – М.: Транспорт. 1989. –319 с.
8. Павлов Н.Г. Примеры расчетов кранов. –Л.: Машиностроение, 1976. –320 с.
Учебное издание
Подколзин Анатолий Алексеевич
Пискунов Олег Михайлович
Беляев Владислав Владимирович
Дата добавления: 2018-05-12; просмотров: 4155; Мы поможем в написании вашей работы! |
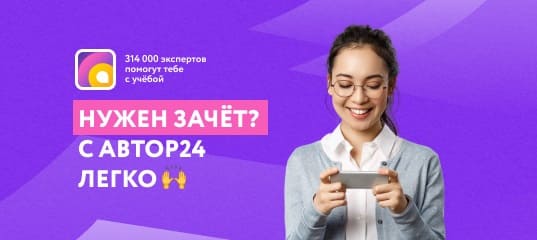
Мы поможем в написании ваших работ!