Проектирование основных сборочных единиц механизма
Проектирование блоков
Блоки служат для изменения направления гибкого органа. Блоки для стальных проволочных канатов изготавливают отливкой из чугуна марки СЧ15 для групп режимов работы механизмов 1, 2, 3 и 4, а из стали 25Л-I - для режимов 5 и 6. Стальные блоки больших диаметров изготавливают сварными.
Диаметры канатного блока (барабана):
- по средней линии навитого каната:
D0 ≥ e∙dк, (4.1)
- по дну ручья:
Dбл = D0 – dк (4.2)
Размеры канатных блоков стандартизированы. Подсчитанное по формуле (4.2) значение диаметра блока необходимо округлить в большую сторону до ближайшего значения по нормальному ряду 160; 200; 250; 320; 400; 450; 500; 630; 710; 800; 900 и 1000 мм. Канатные блоки, как правило, устанавливают на подшипниках качения. Профиль ручья канатного блока выполняют трапециевидным с расширением наружу для беспрепятственного входа и выхода каната (приложение 1). При этом:
· глубина желоба h = (1,5÷2,0)∙dк; (4.3)
· ширина по верху b = (2,0÷2,25)∙dк; (4.4)
· радиус дна r = (0,6÷0,7)∙dк. (4.5)
Рабочую поверхность профиля ручья целесообразно покрывать пластмассой, резиной, алюминием и т.п. Это приводит к снижению контактных напряжений, уменьшению трения при движении каната по блоку, т.е. повышению долговечности каната. При работе канат не должен опираться на край желоба блока. Поэтому максимальное отклонение его от средней плоскости не должно превышать 6о.
|
|
Проектирование барабанов
Барабаны служат для наматывания гибкого органа и преобразования вращательного движения привода в поступательное движение груза. Барабаны изготавливают отливкой или сваркой.
Канатные барабаны по форме внешней поверхности разделяют на цилиндрические, конические и коноидальные. Наибольшее распространение получили цилиндрические барабаны (рисунок 4.1), которые бывают гладкие или нарезные (рисунок 4.1, а, б, в).
а – литой гладкий; б – литой нарезной, в – сварной нарезной;
г – мелкая нарезка; д – глубокая нарезка
Рисунок 4.1. Типы барабанов
Гладкие барабаны применяют при многослойной навивке каната на барабан при больших высотах подъема груза и необходимости уменьшения длины барабана по условиям компоновки. При гладких барабанах больше контактные напряжения в местах касания с канатом, что уменьшает срок службы канатов. При намотке каната в несколько слоев происходит его интенсивное сплющивание, что приводит к интенсивному износу самого каната и барабана. Поэтому на практике получили наибольшее распространение нарезные барабаны. Для получения необходимого зазора Δ (рисунок 4.1, г, д) между смежными витками каната шаг нарезки принимают:
|
|
tн ≥ (1,1…1,2)∙dк . (4.6)
Полученное значение tн ложно быть округлено до значения кратного 0,5. Радиус профиля канавки принимают rж>0,54∙dк для исключения заклинивания каната. Канавки могут быть мелкими и глубокими. Мелкие канавки предпочтительнее, т.к. уменьшают длину нарезной части барабана при одинаковой канатоемкости барабана. Глубокие канавки обеспечивают лучшее направление набегающего каната. Такие барабаны применяют, например, в грейферных кранах.
Типовая конструкция барабана механизма подъема показана на рисунке 4.2.
![]() |
1-зубчатая муфта; 2-подшипник; 3-барабан; 4-ось барабана.
Рисунок 4.2. Схема барабана механизма подъема.
4.2.1 Расчет геометрических размеров барабана
Диаметры барабана по средней линии навивки каната и по дну ручья определяют по формулам (4.1) и (4.2) с последующим округлением до ближайшего значения по нормальному ряду.
Толщину стенки предварительно определяют по эмпирическим зависимостям:
- для чугунных барабанов δ = 0,02∙Dб + (6÷10) мм; (4.7)
- для стальных барабанов δ = 0,01∙Dб + 3 мм. (4.8)
Расчетные значения δ округляют в сторону увеличения, причем, исходя из технологических соображений изготовления барабанов, принимают значения:
|
|
- для чугунных барабанов δ не менее 12 мм;
- для стальных барабанов δ не менее 15 мм.
Минимальная длина барабана (рисунок 4.3) при навивке каната в один слой:
- при одной ветви каната на барабане L = L0 + L1 + 2L2;
- при двух ветвях каната на барабане L =2L0 + 2L1 + L3,
где L0 – длина участка барабана для навивки каната в один слой; L1 – длина участка барабана для крепления 3÷4 витков каната прижимными планками (L1≈3tн); L2 – длина участка вала под ребордой (ширина реборды L1≈1,5 tн); L3 – длина среднего ненарезанного участка барабана.
а)
![]() | б)
![]() |
а – при навивке одной ветви каната;
б – при навивке двух ветвей каната
Рисунок 4.3. Расчетная схема для определения длины барабана
Длина участка барабана для навивки каната в один слой:
, (4.9)
где zр – число рабочих витков для навивки каната на барабан; zн – количество неприкосновенных витков каната (по правилам Госгортехнадзора zн=1,5); zкр – число витков для крепления конца каната (zкр=3…4); Н – высота подъема груза; ап – кратность полиспаста; D0 – диаметр барабана, измеренный по средней линии навитого в один слой каната; tн – шаг навивки каната (у гладких барабанов tн=dк).
|
|
Длина среднего ненарезанного участка барабана:
L3 = A – 2∙hmin∙tg γ (4.10)
где А – расстояние между осями ручьев блоков крюковой подвески или направляющих блоков, с которых ветви каната наматываются на барабан; hmin – минимальное расстояние между осями барабана и направляющих блоков; γ – угол отклонения каната от средней плоскости блока или от направления каната на барабане (можно принимать γ = 3÷60).
Значение hmin регламентированы правилами Госгортехнадзора и принимается по заданному Q, например, для:
· Q = 3,2÷6,3 т hmin = 600÷650 мм;
· Q = 8,0 т hmin = 870 мм;
· Q = 10÷12,5 т hmin = 1000÷1050 мм;
· Q = 15÷20 т hmin = 1150÷1200 мм;
Важным показателем технической характеристики барабана лебёдки является его канатоёмкость, которая, в некоторых случаях, будет решающей при подборе лебёдки.
В тех случаях, когда по тем или иным причинам канатоёмкость неизвестна, её определяют по формуле
,
где W - канатоёмкость, м; m - число витков каната, укладываемое по всей рабочей длине барабана ( ); l - рабочая длина барабана, мм; t - шаг навивки каната, мм (для гладкого барабана t = d; для барабана с канавками t=1,1d); n - число слоев навивки каната; d - диаметр каната, мм; D - диаметр барабана, мм; 2·π·D - длина двух витков каната, которые должны оставаться на барабане для уменьшения нагрузки на узел закрепления каната.
Пример 1
Определить длину каната, наматываемого на барабан диаметром 300 мм, длиной рабочей части 700 мм, число слоев навивки каната n=4, диаметр каната d = 17,5 мм. Поверхность барабана с канавками.
Решение:
Число витков каната, укладываемого на барабан в один слой
Канатоёмкостъ барабана лебёдки W:
м.
4.2.3 Крепление каната на барабане
Узлы крепления свободных концов каната должны быть конструктивно простыми, удобными для осмотра и монтажа, обеспечивать легкость замены каната и надежность его крепления, исключать резкие перегибы каната. Крепление каната на барабане осуществляется разными способами (рисунок 4.4), которые регламентированы правилами Госгортехнадзора.
Рисунок 4.4. Способы крепления каната на барабане
Наибольшее распространение получили крепления наружными прижимными планками, которые бывают с полукруглыми (сечение А-А) или трапецеидальными канавками (сечение Б-Б). Применение вместо полукруглых опорных поверхностей у прижимных планок трапецеидальных увеличивает давление на наклонных поверхностях, что увеличивает величину приведенного коэффициента трения. Однако такие планки способствуют повышенной деформации канатов в узлах крепления.
Планки бывают одно- и двухболтовые. При dк≤31 мм следует закреплять канат не менее чем двумя одноболтовыми прижимными планками или одной двухболтовой планкой, а при dк>31 мм – двумя двухболтовыми планками.
При стальных барабанах прижимные планки крепят болтами или винтами, а при чугунных барабанах – вместо болтов используют шпильки. Это обусловлено возможностью выкрашивания резьбы в чугунных барабанах при частых подтягиваниях узлов крепления каната в процессе эксплуатации.
Длина свободного конца каната от последнего зажима на барабане должна быть не менее двух диаметров каната. Изгибать свободный конец каната под прижимной планкой и возле нее не допускается.
Поскольку перед узлом крепления располагаются неприкосновенные витки каната, то усилие sкр, выдергивающее канат из узла крепления, оказывается за счет сил трения меньше, чем усилие в рабочей ветви smax. Используя известное соотношение между усилиями в набегающей и сбегающей ветвях гибкой нити, можно записать
, (4.14)
где е=2,7 – основание натуральных логарифмов; f – коэффициент трения скольжения каната о поверхность барабана (для реальных пар трения f = 0,1÷0,16); α – угол обхвата барабана витками неприкосновенного запаса (при zн = 1,5 α = 3π; при zн = 2 α = 4π;).
Для того чтобы канат был надежно закреплен, необходимо затяжкой болтов создать силы трения не менее sкр. Тогда требуемое усилие затяжки болтов:
![]() ![]() ![]() ![]() ![]() | при полукруглых планках:
![]() |
![]() ![]() ![]() ![]() | при трапецеидальных планках:
![]() |
где Fб – необходимое суммарное усилие затяжки болтов;2f –число, учитывающее наличие и работу двух пар трения "канат – барабан" и "канат – планка с полукруглыми канавками";f1 – приведенный коэффициент трения для планок с трапецеидальными канавками (здесь β = 400 – угол наклона боковой грани прижимной планки).
Для расчета болта на прочность необходимо вначале задаться диаметром болта. Опытом установлены следующие рекомендации:
- при диаметре каната до 12,5 мм принимают болты М12;
- при диаметре каната до 15,5 мм принимают болты М16;
- при диаметре каната до 17,5 мм принимают болты М20.
Крепежные болты испытывают сложное напряженное состояние, определяемое напряжениями растяжения σр от усилия Fб, напряжениями изгиба σи от усилия Sкр, а также касательными напряжениями кручения τ, создаваемыми суммарным действием моментов трения в резьбе и на торце головки болта. Поэтому суммарные напряжения в опасном сечении одного болта
, (4.17)
где 1,3 – число, учитывающее влияние τ; k – коэффициент надежности крепления (k≥1,5); zб – число крепежных болтов; d1 – внутренний диаметр резьбы болта; [σр] – допускаемые напряжения.
При необходимости из этой формулы можно определить потребное количество болтов zб.
Допускаемое напряжение в болтах (винтах), изготовленных из стали Ст 3, имеющей предел текучести σт=240 МПа:
[σр] = σт/2,5. (4.18)
Если условие прочности (4.17) не выполняется, то необходимо или увеличить число болтов или принять большее число витков каната, охватывающих барабан (увеличится угол α и уменьшится Sкр).
4.2.4 Расчет оси барабана
Исходными данными для расчета оси барабана являются: максимальное натяжение каната Smax; группа режима работы механизма подъема; конструкция и размеры оси барабана (рисунок 4.2.). Расчетная схема оси барабана представлена на рисунке 4.5.
В процессе подъема положение каната относительно опор барабана меняется непрерывно. Поэтому значения реакций опор будут также изменяться во времени. Если канат занимает положение посередине, то RA=RD=Fmax/2 (Fmax=Smax), где RA и RD соответственно реакции в опорах A и D. Наибольшие значения реакций будут соответствовать крайним положениям каната (точки В и С на рисунке 4.5).
Определим реакции RA и RD (рисунок 4.5). При определении реакций возможны два случая:
а) канат находиться в крайнем левом положении над ступицей В:
откуда:
RA=Fmax(l+l1+l3)/(l+l1+l2+l3);
RD=Fmax-RA.
б) канат находиться в крайнем правом положении над ступицей С:
откуда:
RD=Fmax(l+l2)/(l+l1+l2+l3);
RA=Fmax-RD
Размеры l, l1, l2, l3 - принимаются по рисунок 4.5.
Строим эпюры изгибающих моментов для расчетных положений каната и определяем суммарные значения моментов в точках В и С.
Максимальные значения моментов:
МВ max=RAl2
МC max=RD(l3+l1)
Значения моментов МВ и МC для крайних положений каната можно определить из графического построения эпюр изгибающих моментов (рисунок 4.5).
Суммарные значения изгибающих моментов:
Дальнейший расчет оси рекомендуется вести по большему значению суммарного изгибающего момента.
Диаметр оси под ступицей барабана (рисунок 4.6):
(4.19)
Рисунок 4.5. Расчетная схема оси барабана.
Допускаемое напряжение на изгиб определяется по формуле:
[s]и=s-1/nsK' (4.20)
где s-1 – предел выносливости при изгибе для материала оси (таблица 4.2); ns - коэффициент запаса прочности для деталей механизма подъема, принимаемый в зависимости от режима работы (таблица 4.3); K' – коэффициент, учитывающий конфигурацию деталей K'=1.3…1.6. Для гладких деталей, ослабленных шпоночными пазами K'=2.0…2.8.
Рисунок 4.6. Ось барабана
Диаметры остальных участков оси определяются по следующим соотношениям:
- диаметр оси для посадки подшипников:
dп=(0.85…0.9)dc n, мм (4.21)
- диаметр оси в среднем сечении:
dcp=(1.15…1.25)dc n, мм (4.22)
Полученные численные значения диаметров оси dп и dcp необходимо округлить в соответствии с ГОСТ 8032 (ряды предпочтительных чисел). Длины отдельных участков оси определяются по конструктивным соображениям.
Таблица 4.2 - Материалы, рекомендуемые для изготовления осей барабанов
Марка стали | Диметр заготовки, мм | Твердость НВ, не ниже | Механические характеристики, МПа | ||
sв | sт | s-1 | |||
Сталь 45 | до 80 | 200-270 | 560-900 | 280-650 | 250-380 |
Сталь 40Х | до 120 | 200-270 | 730-900 | 500-750 | 320-410 |
Сталь 40ХН | до 200 | 240-270 | 820-920 | 650-750 | 360-420 |
Сталь 20Х | 120 | 197 | 650 | 400 | 300 |
Сталь 12ХН3А | 120 | 260 | 950 | 700 | 420 |
Таблица 4.3 - Допускаемые значения коэффициентов запаса прочности [ns] для деталей механизмов подъема
Группа режима работы | Прокат и поковки | Литье |
1; 2; 3 | 1,4 | 1,7 |
4 | 1,6 | 1,9 |
5 | 1,7 | 2,0 |
6 | 1,85 | 2,2 |
По эпюрам изгибающих моментов (рисунок 4.5) определяют наиболее опасные сечения оси, которые необходимо проверить на прочность. Такими сечениями являются: участок оси под ступицей В (сечение В-В), где изгибающий момент имеет наибольшее значение; сечение; сечение Е - Е – ослабленное галтельным переходом; сечение С - С - ослабленное шпоночным пазом.
Прочность сечения определяется по значению коэффициента запаса прочности:
ns=(s -1)D / sні[ ns], (4.23)
где (s -1)D – предел выносливости материала оси; sи = – расчетное напряжение изгиба в опасном сечении; [ns] – допускаемое значение коэффициента запаса прочности (таблица 4.2).
Предел выносливости материала в рассматриваемом сечении:
(s -1)D=s -1/(Ks)D (4.24)
Предел выносливости при изгибе s-1 принимается по таблице 4.2.
Коэффициент концентрации напряжения для рассчитываемого сечения:
(4.25)
где Кs - эффективный коэффициент концентрации напряжений (таблица 4.4); КD – коэффициент, учитывающий влияние размеров поперечного сечения оси (таблица 4.5); КF – коэффициент, учитывающий влияние шероховатости поверхности (для RA=0.1…0.4 мкм - КF =1; для RA =3.2…0.8 мкм - KF =1.05…1.25); Kv – коэффициент, учитывающий влияние поверхностного упрочнения (таблица 4.6).
Если условие (4.23) не выполняется, то для обеспечения необходимой прочности оси можно принять либо более прочный материал, либо увеличить диаметры соответствующих участков оси, либо предусмотреть другой вид термообработки.
Радиус галтели r принимается в зависимости от значений меньшего из сопрягаемых диаметров:
Диаметр оси d, мм: | 32…45 | 50…70 | 80…100 |
Радиус галтели r, мм: | 2 | 2.5 | 4 |
Напряжение изгиба в опасном сечении оси
sе=М/W (4.26)
где М – изгибающий момент в проверяемом сечении (рисунок 4.5);
W – осевой момент сопротивления в расчетном сечении оси.
Осевой момент сопротивления:
а) для оси круглого сплошного сечения W=0,1d3;
б) для оси со шпоночной канавкой W=0,1d3-bt(d-t)2/(2d), (4.27)
где d – диаметр оси в проверяемом сечении; b и t – размеры шпоночного паза ([2], С. 520-522).
Таблица 4.4 - Выбор эффективного коэффициента концентрации напряжений
t1/r | r/d | Ks при sB (МПа) | |||
500 | 700 | 900 | 1200 | ||
2 | 0.01 | 2,55 | 1,6 | 1,65 | 1,7 |
0.02 | 1,8 | 1,9 | 2,0 | 2,15 | |
0.03 | 1,8 | 1,95 | 2,05 | 2,25 | |
0.05 | 1,75 | 1,90 | 2,0 | 2,2 | |
3 | 0.01 | 1,9 | 2,0 | 2,1 | 2,2 |
0.02 | 1,95 | 2,1 | 2,2 | 2,4 | |
0.03 | 1,95 | 2,1 | 2,25 | 2,45 | |
5 | 0,01 | 2,1 | 2,25 | 2,35 | 2,5 |
0,02 | 2,15 | 2,3 | 2,45 | 2,65 |
t1=(dсp-dcm)/2 –разность сопрягаемых диаметров (рисунок 4.6).
Таблица 4.5 - Выбор коэффициента масштабного фактора
Напряженное состояние и материал | Значение Kd при диаметре d, мм | ||||
30 | 40 | 50 | 70 | 100 | |
Изгиб для углеродистой стали | 0,88 | 0,85 | 0,81 | 0,76 | 0,71 |
Изгиб для высокопрочной легированной стали | 0,77 | 0,73 | 0,70 | 0,67 | 0,.62 |
Таблица 4.6 - Значения коэффициента Кv.
Вид упрочнения | sв, МПа | Кv | ||
для гладких осей | KsЈ1.5 | KsЈ1.8-2.0 | ||
Закалка с нагревом ТВЧ | 600-800 800-1000 | 1,5-1,7 1,3-1,5 | 1,6 - | 2,4-2,8 - |
Дробеструйный наклеп | 600-1500 | 1,1-1,25 | 1,5-1,6 | 1,7-2,1 |
4.2.5 Подбор подшипников для оси барабана
Исходными данными для подбора подшипников являются: реакции в опорах, диаметры посадочных участков оси dп, на которых устанавливаются подшипники, долговечность работы подшипника и режим работы механизма подъема.
Рекомендуемая последовательность подбора подшипников качения:
а) назначить тип и класс точности подшипника. Опорные узлы осей барабанов воспринимают в основном только радиальные нагрузки. Поэтому в данных узлах могут быть применены шариковые или роликовые подшипники качения. Но в процессе навивки каната на барабан возможны эксцентричные нагрузки способные вызвать перекос оси. Кроме того, в отдельных конструкциях барабанов опоры располагаются вне барабана, что может вызвать также перекос оси. Поэтому для осей барабанов целесообразно использовать радиальные сферические шарикоподшипники или роликоподшипники ([2], таблицы 100 и 102).
Для данного типа опорных узлов рекомендуется назначить подшипники 0-го или 6-го класса точности (как более экономичных);
б) по диаметру посадочного участка оси dn подобрать подшипники ([2], таблицы 100 и 102) и выписать значения его динамической (С) и статической (С0) грузоподъемности;
в) определить реакции R в опорах оси барабана;
г) вычислить динамическую эквивалентную нагрузку для опор А и D (рисунок 4.5).
RE = VXRKБKТ (4.28)
где V – кинематический коэффициент, учитывающий число нагружения тел качения (при вращении с осью внутреннего кольца подъемника КК=1; если вращается внешнее кольцо подшипника, то КК=1.2); R – значение радиальной реакции в рассчитываемой опоре; X – коэффициент соотношения осевой и радиальной нагрузок (для опор, нагруженных только радиальными силами, X=1); КБ – коэффициент безопасности, принимаемый в зависимости от назначения и условий эксплуатации оборудования (для строительных и монтажных кранов, подъемников и т.п. КБ = 1,1 – 1,2); КТ – температурный коэффициент (для стандартных подшипников КТ =1).
д) определить частоту вращения барабана:
nб =υгр/(pD0), об/мин (4.29)
где υгр – скорость подъема груза, м/мин; D0 – диаметр барабана по центрам каната, м.
е) по отношению С/RE и известном nб по таблицам 63 и 64 [2] определить ориентировочное значение долговечности подшипника в часах Lh. Если расчетный ресурс подшипника Lh окажется меньше требуемого (таблица 4.7), то необходимо принять подшипники более тяжелой серии.
Таблица 4.7 - Требуемый ресурс работы подшипников
Группа режима работы | 1, 2, 3 | 4 | 5 | 6 |
Суммарное время работы, ч | 1000 | 3500 | 5000 | 10000 |
Требуемая долговечность подшипников Lh, ч | 500 | 2000 | 4000 | 6000 |
ж) Определить требуемую динамическую грузоподъемность подшипника:
(4.30)
где р – показатель степени, принимаемый: для шариковых подшипников равным 3, для роликовых – 10/3.
Дата добавления: 2018-05-12; просмотров: 1581; Мы поможем в написании вашей работы! |
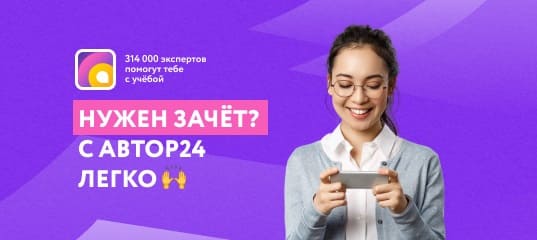
Мы поможем в написании ваших работ!