Организационно-методические основы выполнения контрольных работ
При конструировании любой машины перед конструктором стоит задача – создать машину, которая имела бы высокую производительность, достаточные надежность и долговечность, минимальную массу и габариты, простую и безопасную систему обслуживания и ремонта, была бы удобной в управлении. При этом основные параметры проектируемой машины или механизма должны соответствовать требованиям действующих ГОСТов и Правил безопасности.
Конструкции механизмов грузоподъемных машин и механизмов должны отвечать требованиям "Правил устройства и безопасной эксплуатации грузоподъемных кранов (ПБ-10-382-00) М.: ПИО. ОБТ. 2001" и "Правил устройства и безопасной эксплуатации грузоподъемных кранов (ПБ-10-1492) СПб.: Деан 2000".
После выбора схемы механизма производят его предварительный расчет:
1) определяют параметры основных нормализованных или стандартизованных изделий, входящих в состав механизма (крюковых подвесок, канатов, электродвигателей, редукторов, муфт, тормозов и др.);
2) выбирают типы (серии) и типоразмеры данных изделий;
3) определяют основные параметры изделий, не являющихся стандартизированными или унифицированными, или изделий, унификация которых охватывает лишь узкую часть типоразмеров (барабанов, блоков и т.д.).
КИНЕМАТИЧЕСКАЯ СХЕМА МЕХАНИЗМА
Группы классификации (режима) кранов и механизмов в целом
Группа классификации (режима) кранов в целом определяется по таблице 2.1 в зависимости от класса использования (U0 – U9), характеризующегося величиной максимального числа циклов за заданный срок службы, и режима нагружения (Q1 – Q4).
|
|
Режим нагружения крана характеризуется величиной коэффициента распределения нагрузок Кр, определяемого по формуле
, (2.1)
где Сi – среднее число рабочих циклов с частным уровнем массы груза Рi; СТ – суммарное число рабочих циклов со всеми грузами ; Рi – значения частных масс отдельных грузов (уровни нагрузки) при типичном применении крана; Рmax – масса наибольшего груза (номинальный груз), который разрешается поднимать краном; m=3 – показатель степени.
Группа классификации (режима) механизмов в целом определяется по таблице 2.2 в зависимости от класса использования механизма (Т0 – Т9), характеризующего общей продолжительностью использования механизма (в часах), и режима нагружения (L1 – L4).
Таблица 2.1 - Группы классификации ( | Класс использования | U9 | максимальное число рабочих циклов | более 4∙106 | А8 |
Таблица 2.2 - Группы классификации ( | Класс использования | Т9 | общая продолжительность использования, ч
| 100∙103 | М8 | ||||||||
U8 | 4∙106 | А7 | А8 | Т8 | 50∙103 | М7 | М8 | ||||||||||||
U7 | 2∙106 | А6 | А7 | А8 | Т7 | 25∙103 | М6 | М7 | М8 | ||||||||||
U6 | 1∙106 | А5 | А6 | А7 | А8 | Т6 | 12500 | М5 | М6 | М7 | М8 | ||||||||
U5 | 5∙105 | А4 | А5 | А6 | А7 | Т5 | 6300 | М4 | М5 | М6 | М7 | ||||||||
U4 | 2,5∙105 | А3 | А4 | А5 | А6 | Т4 | 3200 | М3 | М4 | М5 | М6 | ||||||||
U3 | 1,25∙105 | А2 | А3 | А4 | А5 | Т3 | 1600 | М2 | М3 | М4 | М5 | ||||||||
U2 | 6,3∙104 | А1 | А2 | А3 | А4 | Т2 | 800 | М1 | М2 | М3 | М4 | ||||||||
U1 | 3,2∙104 | А1 | А2 | А3 | Т1 | 400 | М1 | М2 | М3 | ||||||||||
U0 | 1,6∙104 | А1 | А2 | Т0 | 200 | М1 | М2 | ||||||||||||
Коэффициент распределения нагрузок Кр | 0,125 | 0,250 | 0,500 | 1,000 | Коэффициент распределения нагрузок Кт | 0,125 | 0,250 | 0,500 | 1,000 | ||||||||||
Режим нагружения | Q1 – легкий | Q2 – умеренный | Q3 – тяжелый | Q4 – весьма тяжелый | Режим нагружения | L1 – легкий | L2 – умеренный | L3 – тяжелый | L4 – весьма тяжелый |
Режим нагружения механизма характеризуется величиной коэффициента распределения нагрузок Кт, определяемого по формуле
, (2.2)
где ti – средняя продолжительность использования механизма при частных уровнях нагрузки; tТ – общая продолжительность при всех частных уровнях нагрузки ; Рi – значения частных нагрузок (уровни нагрузок), характерных для применения данного механизма; Рmax – значение наибольшей нагрузки, приложенной к механизму; m=3 – показатель степени.
|
|
Дата добавления: 2018-05-12; просмотров: 289; Мы поможем в написании вашей работы! |
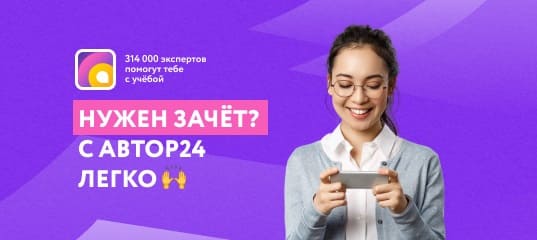
Мы поможем в написании ваших работ!