Электроды для сварки конструкционных сталей
Тип электрода | Механические свойства электрода при нормальной температуре | |||
Предел прочности, МПа | Относительное удлинение δ,% | Ударная вязкость, Дж/см2 | Угол загиба шва, град. | |
Э–38 | 380 | 14 | 30 | 60 |
Э–42 | 420 | 18 | 80 | 150 |
Э–46 | 460 | 18 | 80 | 150 |
Э–50 | 500 | 16 | 70 | 120 |
Э–42А | 420 | 22 | 150 | 180 |
Э–46А | 460 | 22 | 140 | 180 |
Э–50А | 500 | 20 | 130 | 150 |
Э–55 | 550 | 20 | 120 | 150 |
Э–60 | 600 | 18 | 100 | 120 |
Э–70 | 700 | 14 | 60 | |
Э–85 | 850 | 12 | 50 | |
Э–100 | 1000 | 10 | 50 | |
Э–125 | 1250 | 8 | 40 | |
Э–150 | 1500 | 6 | 40 |
Приложение 3.2
Обозначение рода и полярности тока
Обозначение | Рекомендуемая полярность источника постоянного тока | Напряжение холостого хода источника переменного тока, В |
0 | Обратная | – |
1 2 3 | Любая Прямая Обратная | 55 – 60 |
4 5 6 | Любая Прямая Обратная | 70 – 80 |
7 8 9 | Любая Прямая Обратная | 90 – 95 |
Приложение 3.3
Характеристики наплавленного металла
Группа индексов | При нормальной температуре | Тх ,°С | |
σв, МПа | δ, % | ||
370 (0) | 370 | Не регламентирована | Не регламентирована |
411 (0) | 410 | <16 | Не регламентирована |
412 (1) | 410 | 20 | +20 |
412 (2) | 410 | 22 | 0 |
412 (3) | 410 | 24 | –20 |
412 (4) | 410 | 24 | –30 |
412 (5) | 410 | 24 | –40 |
412 (6) | 410 | 24 | –50 |
412 (7) | 410 | 24 | –60 |
431 (0) | 430 | <16 | Не регламентирована |
432 (1) | 430 | 20 | +20 |
432 (2) | 430 | 22 | 0 |
432 (3) | 430 | 24 | –20 |
432 (4) | 430 | 24 | –30 |
432 (5) | .430 | 24 | –40 |
432 (6) | 430 | 24 | –50 |
432 (7) | 430 | 24 | –60 |
511 (0) | 510 | <16 | Не регламентирована |
512 (1) | 510 | 18 | +20 |
512 (2) | 510 | 18 | 0 |
512 (3) | 510 | 20 | –20 |
512 (4) | 510 | 20 | –30 |
512 (5) | 510 | 20 | –40 |
512 (6) | 510 | 20 | –50 |
512 (7) | 510 | 20 | –60 |
Приложение 3.4
|
|
Механические свойства наплавленного металла
Тип электрода | Механические свойства при нормальной температуре ≈ 20oC | Основное назначение | ||||
Металла шва | Сварочного соединения | |||||
σв, МПа | δ, % | ан, Дж/см2 | σв, МПа | Угол загиба в о | ||
Э38 Э42 Э46 Э50 | 380 420 460 500 | 14 18 18 16 | 30 80 80 70 | 380 420 460 500 | 60 150 150 120 | Для сварки углеродистых и низколегированных сталей σв ≤ 500 МПа |
Э42А Э46А Э50А | 420 460 500 | 22 22 20 | 150 140 130 | 420 460 500 | 150 180 150 | Тоже, но с повышенными требованиями к пластичности |
Э55 Э60 | 550 600 | 20 18 | 120 100 | 550 600 | 150 120 | Для сварки углеродистых и низколегированных сталей σв = 500 – 600 МПа |
Э70 Э85 Э100 Э125 Э150 | 700 850 1000 1250 1500 | 14 12 10 8 6 | 60 50 50 40 40 | – – – – – | – – – – – | Для сварки легированных конструкционных сталей повышенной прочности σв>600 МПа |
Приложение 3.5
Характеристика электродов для сварки углеродистых сталей
|
|
Электрод | Применение | Наплавленный металл | ||||||||
Тип | Марка | Коэффициент наплавки | Пространст-венное положение | Род тока | σв, МПа | δ, % | Ψ, % | ан, дж/см2 | Угол загиба в град. | |
+20о С | –40о С | |||||||||
Э42 | ВСП–1 ОММ–5 СМ–5 ЦМ–7 АНО–1 | 10,0 7,2 7,2 10,6 15,0 | любое любое любое любое любое | пост. и перем. постоянный пост. и перем. пост. и перем. пост. и перем. | 470 480 460 480 460 | 25 22 25 22 28 | 68 55 60 55 60 | 130 100 120 100 130 | – 50 80 40 80 | 160 160 180 160 180 |
Э42А | УОНИ–13/45 СМ–11 УП–1/45 УП–2/45 ОЗС–2 | 8,5 9,5 10,0 10,0 8,5 | – – любое – нижнее | Постоянный обратной полярности – перем. и пост. обр. пол. | 360 360 350 380 380 | 26 28 28 26 24 | 65 60 66 70 55 | 220 220 200 240 180 | 180 160 120 – – | 180 – 180 180 180 |
Э46 | АНО–3 МР–3 ОЗС–4 ОЗС–6 РБУ–4 ЗСР–2 РБУ–5 ОЗС–3 ЭРС–1 | 8,5 7,3 8,5 40,5 7,8 10,5 9,0 15,0 14,0 | любое – – – – – – – Нижнее – | пост. и перем. перем. и пост. обр. пол. пост. и перем. пост. и перем. пост. обр.пол. пост. и перем. пост. и перем. перем. и пост. обр. пол. пост. и перем. | 460 480 480 480 490 480 380 400 380 | 25 25 23 24 26 24 21 25 24 | 65 65 65 55 56 60 56 60 68 | 15 15 12 12 14 13 14 12 12 | 10 10 8 8 8 6 8 7 7 | 180 180 180 180 160 150 150 180 150 |
Э46А | Э–138/45Н | 8,5 | любое | пост. обр.пол. | 470 | 22 | – | 15 | 3 | 180 |
Э50 | ВСЦ–3 ВСН–3 УОНИ–13/55 ДСР–50 Уп–1/55 Уп–2/55 К–5А | 13–9,5 9,0 9,0 10,0 10,0 10,0 9,0 | Любое – – – – – – – | постоянный пост. обр.пол. пост. обр.пол. постоянный обратной полярности и переменности | 510 500 520 520 540 520 520 | 21 16 29 29 25 24 24 | 57 – 62 – 63 62 – | – 10 20 20 24 15 15 | – 3 14 14 – – – | 105 100 165 180 165 165 165 |
Э50А | Э–38/50Н АН–7 | 9,0 968 | любое | пост. обр.пол. | 510 525 | 24 24 | 15 15 | 3 3 | 165 165 | |
Э55 Э650 Э70 Э85 Э100 Э125 Э150 | УОНИ– 13/55 УОНИ– 13/65 ЛКЗ–70 УОНИ– 13/85 ЦЛ219 НИАТ–3М НИАТ–31 | 9,0 9,8 9,8 10 9,0 10 10 | нижнее любое нижнее любое – – | Постоянный, обратной полярности | 570 620 800 900 1060 900 1060 | 22 21 17 15 13 6 10 | 60 65 54 – 48 – – | 16 18 9 9 8 – 5 | 2 – 5 – – – – | 160 180 – – – – – |
ПАЙКА МЕТАЛЛОВ
|
|
4.1 Цель работы:
|
|
Изучить сущность пайки, составы припоев, технологию. (Приложения 4.1, 4.2)
4.2 Оборудование и материалы на рабочем месте:
4.2.1. Электрические паяльники с подставками,
4.2.2. Припои: ПОС–61 и ПОС–40; флюсы; канифоль, паяльная кислота.
4.2.3. Медный провод, стальные пластинки.
4.2.4. Напильники, наждачные шкурки.
4.2.5. Ацетон, бензин, трихлорэтилен.
4.2.6. Электроплитка.
План выполнения работы
4.3.1. Подготовить медные провода, для чего:
а) отрезать нужной длины;
б) очистить от лака и других покрытий;
в) соединить два конца провода;
г) обезжирить поверхность стружки (ацетон, бензин, трихлорэтилен).
4.3.2. Разогреть паяльник, предварительно уложив его на подставку, до температуры 250–300°С.
4.3.3. Окунуть конец паяльника во флюс (канифоль) и залудить припоем.
4.3.4. Разогреть паяльником место пайки и, нанести флюс и припой ПОС–61,спаять провода.
4.3.5. Проверить качество паяного соединения.
4.3.6. Подготовить к пайке две стальные пластинки:
а) очистить от грязи и ржавчины,
б) подогнать друг к другу;
в) обезжирить ацетоном;
г) нанестифлюс(паяльнаякислота)иоблудитьпластинкипогружением в расплавленный припой.
4.3.7. Разогреть паяльник и спаять между собой две пластинки.
4.3.8. Проверить качество пайки.
4.3.9. Подготовить технологическую карту пайки (таблица4.1).
Справочные данные
Пайка – один из важных технических процессов соединения металлов и сплавов в твёрдом состоянии благодаря металлической связи, создаваемой припоями, имеющими температуру плавления ниже температуры плавления основного металла или сплава.
Таблица 4.1 – Технологическая карта
№ п/п | Наименование операции | Оборудование и инструменты | Материал детали | Марка припоя | Марка флюса | Температура плавления припоя, Tпр, °С | Температура плавления флюса, Тфл, °С | Прочностьсоединения |
При пайке основной металл не плавится, а лишь присадочный материал. Этим пайка отличается от сварки. При пайке существенное значение имеют смачиваемость основного металла жидким припоем, их взаимная растворимость и диффузия. По технологическому процессу пайку подразделяют на капиллярную, диффузионную, контактно-реакционную и пайку-сварку.
Физическая сущность пайки заключается в способности припоя смачивать металл соединяемых деталей или образовывать с ним интерметаллические (химические) соединения.
Пайку выполняют при определённой температуре в средах, обеспечивающих хорошее смачивание, в условиях возникновения капиллярных явлений, обеспечивающих проникновение жидкого припоя в зазор между соединяемыми деталями. В процессе охлаждения припой кристаллизируется и в зазоре устанавливается прочная связь.
Преимущества пайки в сравнении со сваркой:
1. Экономичность;
2. Нет существенных изменений химического состава и механических свойств деталей;
3. Остаточные деформации меньше, чем в сварных соединениях, что обеспечивает соблюдение размеров с большей точностью;
4. Можно соединять как однородные, так и разнородные металлы.
В качестве припоев для пайки используют чистые металлы и сплавы. Припои должны отвечать следующим требованиям: иметь температуру плавления ниже температуры плавления паяемых металлов; быть достаточно жидкотекучим при рабочей температуре, хорошо растекаться и смачивать соединяемые поверхности, заполнять соединительные зазоры; обеспечивать получение прочных и коррозионностойких паяемых соединений; иметь близкий с паяемым металлом коэффициент теплового расширения; по возможности не содержать дефицитных компонентов; иметь простую технологию пайки.
В приложении 4.1 приведены наиболее распространённые в машиностроении припои.
Припои с температурой плавления до 400°С условно называются мягкими припоями. Из них выделяют группу припоев с температурой плавления ниже 100°С, называемых легкоплавкими.
Припои с температурой плавления выше 400°С называют твёрдыми. В них также иногда выделяют группу тугоплавких припоев с температурой плавления выше1000°С.
Пайку выполняют при помощи недефицитных, недорогих, легкоплавких припоев, обладающих пластичностью, коррозионной стойкостью, достаточной прочностью.
По классам припои разделяются следующим образом:
1. Особолегкоплавкие < 145оС
2. Легкоплавкие от 145оС до 450оС
3. Среднеплавкие от 450оС до 1100оС
4. Высокоплавкие от 1100оС до 1850оС
5. Тугоплавкие > 1850оС
В качестве легкоплавких широко используются ПОС – 61; ПОС – 40;
ПОС – 18 (припой оловянно-свинцовый Sn – 61%).
Пайку алюминия выполняют припоем на основе олова и цинка с добавкой алюминия (ПОС-ы не применяют, т.к. свинец резко понижает коррозийную стойкость швов).
Пайку среднеплавкими припоями используют, когда необходима высокая прочность соединения. Припоями является чистая медь, её сплавы с цинком (наиболее широко применяемый), никелем и серебром.
При пайке применяют флюсы, которые в отличие от сварочных флюсов имеют более ограниченные задачи – предохранять соединяемые поверхности от окисления и растворять имеющиеся на них окислы, а также улучшать смачивание поверхностей припоем. Флюсы должны удовлетворять следующим требованиям:
1. Температура плавления и удельный вес должны быть ниже, чем у припоя.
2. Полностьюрасплавлятьсяииметьхорошуюжидкотекучестьпритемпературе пайки, но не «уходить» от места пайки.
3. Своевременно и полностью растворять окислы основного металла.
4. Не образовывать соединений с основным металлом и припоем, а такжепоглощаться ими.
5. Не испаряться и не выгорать при температуре пайки, а продукты его разложения и окислы должны вытесняться припоем, легко удаляться после пайки и не вызывать коррозии.
Соответственно рабочему диапазону температур пайки, определяемому характером припоев, паяльные флюсы делятся на две основные группы: низкотемпературные, или флюсы для мягкой пайки, и высокотемпературные, или флюсы для твёрдой пайки.
Основные группы флюсов приведены в приложении 4.2.
Для улучшения смачивания и растекания обычно применяется канифоль. Иногда к ней добавляют для улучшения активности анилин (улучшает антикоррозийные свойства), терпентин, салициловую кислоту (аспирин).
В качестве флюсов применяют соляную кислоту, стеарин, хлористый цинк, нашатырь, фосфорную кислоту.
При пайке среднеплавкими и тугоплавкими припоями используют флюсы в составе которых имеется бура, борная кислота, хлористый цинк, фтористый калий и другие галоидные соли щелочных металлов. Например, для пайки нержавейки применяется флюс, состоящий из равных частей буры и борной кислоты, замешанных на водном растворе хлористого цинка.
При пайке серебром применяют флюс из буры, плавикового шпата, фтористого калия или хлористого цинка.
Имеются также самофлюсующиеся припои:
1. Меднофосфористый;
2. Серебряный марки ПСр72ЛМН содержащий 0,4 – 0,6% метил;
3. Соединение меди с марганцем – ВПр содержащий в качестве флюсующих элементов барий, калий и фосфор в количестве 0,1 – 0,3%.
Качество соединения зависит от подготовки поверхности, заключающейся в зачистке и обезжиривании (щелочами, этиловым спиртом), обеспечении необходимого зазора, защите поверхностей предохранительными пастами, способа нагрева.
Способы нагрева – газовые горелки, печи, индукционный, ванны с солями, электроконтактный, кварцевыми лампами и т.д.
4.5 Содержание отчета:
В отчет включается цель работы, определение пайки, мягких припоев, твердых припоев, технологическая карта пайки, выводы по качеству спаянных деталей.
Контрольные вопросы
4.6.1. Что такое пайка? Ее отличие от сварки.
4.6.2. В чем сущность пайки?
4.6.3. Какие группы припоев вы знаете?
4.6.4. Каково назначение флюса?
4.6.5. В чем заключается подготовка деталей для пайки?
4.6.6. Что такое лужение? Его назначение.
4.6.7. Для чего после пайки изделие необходимо тщательно вымыть?
Приложение 4.1
Припои и их применение
Маркаприпоя | Химический состав | Температура Тпл,°С | Назначение |
НСО | 99,99 %Cu | 1083 | Для пайки ответственных деталей из углеродистых и нержавеющих сталей и никелевых сплавов |
ГО | 99,95% Cu | 1083 | |
M1 | 99,90% Cu | 1083 | |
ПМ1–35 | 36%Cu и 64%Zn | 825 | Для пайки латуни |
ГТМ2–54 | 45%Cu и 46%Zn | 885 | Для пайки меди, бронзы, сталей |
Л–63 | 63%Cu и 37%Zn | 900 | Тоже |
ПМФ–7 | 93%Cu и7%Р | 860 | Дня пайки меди и бронзы |
ПСр70 | 70%Ag, 26%Cu и 4%Zn | 755 | Доя пайки меди и ее сплавов, сталей |
ПСр45 | 45%Ag,30%Cu и 25%Zn | 725 | Обладает высокой электропроводностью |
ПСр70 | 10%Ag,53%Cu и 37%Zn | 725 | |
Силумин | 10–13%Si, 0,8% Cu 0,3%Zn, ост.–Al | 578 | Для пайки алюминия и его сплавов |
П575А | 80%Al, 20%Zn | 620 | |
П430М | 13–15%Zn, l%Al, ост.–Mg | 600 | Для пайки магния и его сплавов |
П0С90 | 90%Sn и l0%Pb | 220 | Для пайки деталей подвергаемых гальванопокрытиям (серебрение, золочение) |
П0С61 | 61%Sn и 39%Pb | 185 | Для пайки меди и ее сплавов, сталей |
ПОСсу4–6 | 3–4%Sn, 5–6%Sb, ост.–Pb | 265 | Для лужения меди и железа |
ПСр3 | 97%Pb, 3%Ag | 304 | Для пайки медных и латунных деталей, работающих при 150 °С |
Индиевые №1 | 80%In,15%Pb,5%Ag | 156,4 | Для покрытий на керамике |
№2 | 50%In,50%Sn | 120 | Для пайки стекла |
Приложение 4.2
Основные группы флюсов
Флюс | Компоненты флюса | Содер-жание, % по массе | Темпера-тура плавления флюса, Тфл, oС | Назначение флюса | |
Бура | Тетраборно-кислыйнатрий | 100 | 800–1150 | Для пайки углеродистых сталей, чугунов, меди и ее сплавов медноцинковыми и серебряными припоями. | |
Борная кислота | |||||
№200 | Борная кислота | 68–72 | 850–1150 | Для пайки легированных сталей. | |
Бура | 19–21 | ||||
Фтористый кальций | 840 | ||||
Паяльная кислота | Хлористый цинк | 25 | 290–350 | Для пайки стали, меди и ее сплавов низкотемпературными припоями | |
Вода | 75 | ||||
Паяльная кислота | Хлористый цинк | 18 | 180–320 | То же | |
Аммоний | 6 | ||||
Вода | 76 | ||||
Паяльнаякислота | Хлористый цинк | 25 | 180–320 | Для пайки нержавеющих сталей | |
Соляная кислота | 25 | ||||
Вода | 50 | ||||
Канифоль | Канифоль | 100 | 150–300 | Для пайки меди и ее сплавов | |
КЕ | Канифоль | 25 | 150–300 | То же | |
Спирт этиловый | 75 | ||||
ЛК–2 | Канифоль | 28 | 280–300 | Для пайки меди и ее сплавов, оцинкованного железа и никеля | |
Хлористый цинк | 3 | ||||
Хлористый аммоний | 1 | ||||
Спирт этиловый | 68 | ||||
34А | Хлористый калий | 54–56 | 420–620 | Для пайки алюминия и его сплавов | |
Хлористый литий | 29–35 | ||||
Хлористый натрий | 9–11 | ||||
Хлористый цинк | 8–12 | ||||
5 РАЗРАБОТКА ТЕХНОЛОГИЧЕСКОГО ПРОЦЕССА
ЭЛЕКТРОДУГОВОЙ СВАРКИ
5.1 Цель работы:
Освоить методику разработки технологического процесса ручнойэлектродуговой сварки, научиться выбирать для конкретных условий режим электросварки,электроды, электросварочное оборудование и принадлежности рабочего места сварщика.
Задание
5.4.1. Выбрать форму разделки кромок свариваемых деталей и определить площадь сечения сварочного шва.
5.4.2.
5.4.3. Рассчитать режим сварки.
5.4.4. Обосновать технологию выполнения швов (определить количество валиков и порядок их наложения, схему выполнения шва по длине, траекторию движения конца электрода).
5.4.5. Произвести нормирование процесса сварки.
5.4.6. Заполнить карту технологического процесса.
Элементы УИРС
Научиться пользоваться справочной литературой и ГОСТами, а также составлять и заполнять технологические карты.
Методические указания и план выполнения работы
Разрабатывают технологический процесс электросварки обычно для вполне конкретных условий, т.е., когда известны марка и химсостав металла свариваемых деталей, вид соединения, толщина свариваемого металла, длина сварного шва, требования к механическим и другим свойствам сварочного шва: прочности, вязкости, пластичности, морозостойкости, положению шва в пространстве, марке, характеристике, имеющегося в цехе сварочного оборудования. Предполагается наличие сварщика требуемой квалификации, рабочего места с комплектом необходимых приспособлений и принадлежностей.
5.4.1. Выбор формы разделки
5.4.2. Форму разделки кромок свариваемых деталей определяет по ГОСТ 5264–69, вычерчивают её на миллиметровой бумаге и определяютплощадь сечениясварочного шва Fсш, по клеточкам или формулам.
5.4.3. Выбор электрода
Выбор электрода состоит из многих пунктов.
5.4.3.1. Марку электродной проволоки назначают по химсоставу близкой к марке свариваемой стали (приложение 3.5), а тип электрода должен обеспечить прочность наплавленного металла, близкую к прочности заданного материала детали (приложение 3.4).
5.4.3.2. Марку покрытия принимают из таблицы (приложение 3.5).
5.4.3.3. Диаметр электродного стержня d определяют в зависимости от толщины свариваемой детали S по формуле или таблицы 5.1.
Таблица 5.1 – Выбор диаметра электрода
Sмм | 1,5 | 2 | 3 | 4 – 5 | 6–9 | 9–12 | 13–15 | 16– 20 | Более 20 |
d мм | 1,6 | 2 | 3 | 3– 4 | 4 | 4 –5 | 5 | 5–6 | 6–8 |
5.4.3.4. Вcе последующие индексымаркировкиэлектрода принимают в соответствии с требованиями задания, используя приложение, а затем все элементы характеристик выбранного электродасводят в одну маркировку, например такую:
. ГОСТ 9466 – 75, ГОСТ 9467 – 75
Расчет режима сварки
6.1 Сила сварочного тока определяется по формуле
Jсв= К·d (5.1.)
где Jсв– сварочный ток, А,
К – коэффициент плотности тока, А/мм,
К – 40–60 А/мм при сварке углеродистых сталей, причем при сварке тонких листов металла S<1,5·d, а при сварке потолочных и вертикальных швов принимают К = 35–40 А/мм; примем К = 40А/мм,
D– диаметр стержня электрода, мм.
6.2. Длина дуги определяется из зависимости:
lд = 0,5·d + 1 (5.2.)
где lд– длина сварочной дуги, мм.
6.3Напряжение на дуге (Uд, В) для сварки постоянным током определяется по формуле:
Uд = α + β·lд (5.3.1)
где α – суммарное падение напряжения на концах анода и катода,обычно α = (10–12) В; Примем α = 10В
β – падение напряжения на I мм длины дуги, В/мм; при сварке сталей β = 2–3 В/мм. Примем β = 3 В/мм.
Напряжение на дуге для сварки переменным током определяется по формуле:
Uд = Uxx/ (2...3) (5.3.2)
6.4. Обоснование технологии выполнения швов
6.4.1 Количество валиков, накладываемых по сечению сварного шва, определяют по формуле:
(5.4.)
где N– количество валиков или число проходов, шт;
Fсш–площадь сечения сварного шва, мм2;
F1– площадь сечения первого валика, мм2;
F1 = (6...8)·d1;гдеd1= d– 1 (мм);
F2– площадь сечения второго и всех последующих валиков, мм2;
F2 = (8...10)·d.
6.5. Назначают последовательность наложения валиков по сечению и длине шва (см. рисунки5.1, 5.2 и 5.3)
В зависимости от размеров сечения швы выполняют однопроходными имногослойными (рисунок 5.1.). Однопроходная сварка производительна иэкономична, но металл шва недостаточно пластичен вследствиеегостолбчатой структуры и увеличенной зоны перегрева.
Рисунок5.1– Схема наложения швов по сечению
В случае многослойной сварки каждый нижележащий валик проходит термическую обработку при наложении последующих валиков, что позволяет получить измельченную структуру металла шва и соответственно повышенные механические свойства шва и сварочного соединения.
В зависимости от длины различают швы короткие(L≤300 мм), средние (L=350–1000 мм) и длинные(L> 1000 мм).
Короткие швы выполняют непрерывными, средние и длинные – прерывистыми, т.е. отрезками не более 350 мм(рисунок5.2).
Схему движения конца электрода выбирают такой, чтобы в сварочной ванне хорошо перемешивался расплавленный металл (рисунок5.3.). Рекомендуется принимать более сложную траекторию при больших сечениях шва и многопроходной сварке.
Рисунок5.2 – Схемы выполнения сварочных швов по длине.
Рисунок5.3 – Траектория движения конца электрода
Нормирование процесса сварки
7.1 Масса наплавленного металла определяется по формуле:
Gн = Fсш.L. ρ (5.5.)
где Gн– масса наплавленного металла, г;
Fсш– площадь сечения сварного шва, см2;
L– длина шва, см;
ρ – плотность металла, г/см3. ρ = 7,8 г/см2
7.2Норма расхода электродов определяется с учетом потерь на угар,разбрызгивание, остающиеся огарки, массы покрытия:
Gэ = Gн·(1 + Кпэ) (5.6.)
где Gэ– масса необходимых электродов, кг;
Кпэ– коэффициент, учитывающий потери электродного материала; Кпэ = 0,2–0,3 для электродов стабилизирующих и с тонким покрытием; Кпэ– 0,4–0,6 для электродов качественных с толстым покрытием. Примем Кпэ= 0,4.
7.3 Машинное время(время горения дуги) определяетсяпо формуле:
(5.7.)
где to– машинное время сварки, ч;
Gн –масса наплавленного металла, г;
Jсв– сила сварочного тока, А;
Кн– коэффициент наплавки, г/А.ч.
Величина коэффициента наплавки зависит от толщины электродного покрытия и может быть взята из таблица5.2.
Таблица 5.2 – Величина коэффициента наплавки
Характеристика покрытия | Кн, г/А.ч |
Стабилизирующее, меловое, тонкое (М) | 7–8 |
Среднее (С) | 8–10 |
Толстое (Т, Д) | 10–12 |
7.4 Норма времени для сварки с учетом перерывов и остановок в работе сварочного поста определяется из выражения:
(5.8.)
где tсв– общее время процесса сверки, ч;
tо–машинное время, ч;
Кисп – коэффициент использования сварочного поста;
Кисп =0,4–0,6 при ручной дуговой сварке коротких швов, а также в единичном производстве; примем К = 0,4.
7.5 Скорость сварки определяется по формуле:
(5.9.)
где Vсв– скорость сварки, м/ч;
L – длина шва, м;
to – время горения дуги, ч.
7.6 Скорость перемещения дуги в каждом проходе рассчитывают так
(5.10.)
где Vg– скорость перемещения дуги, м/ч;
n– число проходов, шт.
7.7. Расход электроэнергии, непосредственно используемой для сварки, определяют по формуле:
(5.11.)
гдеWp – расход электроэнергии, используемой на расплавление металла, Квт ч;
Uд – напряжение на дуге, В;
Jсв – сила сварочного тока, А;
To – время горения дуги, ч;
η – коэффициент полезного действия сварочного агрегата;
η = 0,75 – 0,90 для сварочных трансформаторов
η = 0,3 – 0,4 для генератора. Примем η = 0,4.
7.8 Общий расход электроэнергии с учетом потерь на холостой ход и перерывы в работе определяется из выражения:
Wсв = Wp + Nxx (tсв – tо) (5.12.)
где Wcв– расход электроэнергии на всю сварку, Квт ч;
Nxx– мощность источника тока на холостом ходу; Nxx = 0,2 – 0,4 для трансформатора, Nxx = 2 – 3 для генератора.
Примем Nxx= 2.
tсв–норма времени на всю сварку, ч;
to–время горения дуги (машинное время) ч.
7.9 Удельный расход электроэнергии, затраченный на 1кг наплавленного металла, определяется так:
(5.13)
где Wуд– удельный расход электроэнергии, Квт·ч;
Gн –масcа наплавленного металла, кг.
Для проверки правильности расчетов следует иметь в виду, что по ГОСТ удельный расход электрической энергии на 1 кг наплавленного металла при работе на переменном токе при ручной дуговой сварке составляет 3–4,5 кВт·ч, а при работе на постоянном токе – 6–8 кВт·ч.
Содержание отчёта
В отчёт включается цель работы, задание и его решение со схемами, расчётами, формулами, объяснениями и ссылками на использованные таблицы; технологическая карта(Приложение 5.1)
Приложение 5.1
Дата добавления: 2018-05-12; просмотров: 668; Мы поможем в написании вашей работы! |
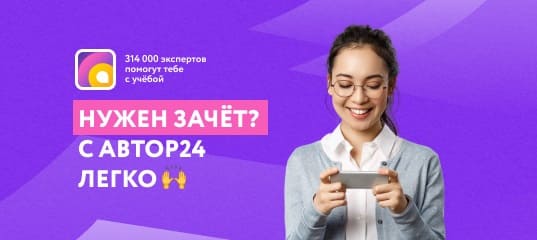
Мы поможем в написании ваших работ!