Общие сведения о процессах механической обработки деталей класса «Диск».
К классу «диски» относят детали цилиндрические, короткие, без отверстия или с относительно небольшим отверстием. Основные группы этого класса: диски, кольца, фланцы, маховики, шкивы, шестерни.
При обработке деталей этого класса необходимо обепечить концентричность всех поверхностей вращения, параллельность торцов, необходимый профиль наружной поверхности (гладкая, выпуклая, ступенчатая, фасонная).
В ряде случаев приходится иметь дело с деталями, которые ввиду больших габаритных размеров и сложности часто выполняют составными. К этим деталям относятся, например, составное зубчатое колесо привода ножниц и шкив-маховик диаметром 8 м для привода рабочей клети; вес шкива в собранном виде составляет около 90 т.
Диски малых и средних размеров с наружным диаметром до 500—600 мм обрабатывают на токарных и револьверных станках. Более крупные детали проходят обточку и расточку на карусельных станках за несколько установок. При составных дисках — большие шкивы, маховики, зубчатые колеса — обработку плоскостей разъема производят на расточных или продольно-фрезерных станках. Сверление отверстий производят на сверлильных и расточных - станках. Шпоночные пазы обрабатывают на долбежных, протяжных и переносных поперечно-строгальных станках. В зависимости от условий работы при больших размерах диски часто проходят статическую балансировку. Точность обработки отдельных поверхностей различна. Сопрягаемые поверхности часто требуется обрабатывать по 3—2-му кассам точности и 6—8-му классам чистоты.
|
|
Типовой технологический процесс обработки «Шкивов».
Деталь «шкив» представляет собой фрикционную вращающуюся деталь ремённой передачи, выполненную в виде колеса, охватываемого гибкой связью (ремнем). Служебное назначение шкива состоит в использовании его как одной из основных частей ременной передачи.
Шкивы. Технические условия на изготовление шкивов (материал чугун, алюминий): точность центрального отверстия 7 – 9 квалитет; радиальное биение по наружной поверхности 0,03 – 0,04мм; торцовое биение ступицы 0,02 – 0,03 на 50мм; торцовое биение обода 0,04 – 0,06 на радиус шероховатость поверхности отверстия Ra1,25…0,03 мкм. Шероховатость поверхности обода Rz 20…25; непараллельность шпоночной канавки к оси вращения 0,3 по длине 100мм.
Исходные материалы и заготовки для получения деталей класса «Шатун» и основные технологические задачи механической обработки.
Шатун представляет собой связующий элемент между коленчатым валом и поршнем. Его основная функция заключается в преобразовании поступательного движения поршня двигателя во вращательное движение вала.
|
|
В качестве материалов для шатунов используют сталиданный элемент двигателя изготавливают из высококачественной стали. Метод производства: литье или горячее штампование. На автомобилях спортивного класса, а также гоночных моделях, в состав двигателя входит шатун, изготовленный из сплава титана. Заготовки шатунов автомобильных и тракторных двигателей получают в закрытых штампах на молотах и кривошипных прессах, используется и поперечно-винтовойпрокат. Заготовки шатунов, как правило, получают цельными, а в процессе обработки крышку отрезают.
Технические требования на шатуны:
–отверстие под запрессовываемую втулку и отверстие в ней под поршневой палец должны быть изготовлены по посадкам Н7-Н8,для повышения точности сопряжения поршневого пальца шатуны сортируют на группы по диаметру отверстия втулок с интервалом 2,5 мкм;
–шероховатость поверхности отверстия втулки
Ra =0,63-1,25мкм;
–отверстия под вкладыши в кривошипных головках изготавливают по посадкам Н6-Н7с шероховатостьюRa =0,63-1,25мкм;
Основные понятия технологического процесса сборки изделий.
Технологический процесс сборки заключается в последовательном соединении деталей в сборочные единицы, механизмы и машины к целом в соответствии с техническими требованиями. Большинство деталей предварительно соединяют с образованием сборочной единицы. Соединение нескольких сборочных единиц составляет механизм. Целое изделие (машину) собирают из механизмов, агрегатов, сборочных единиц и отдельных деталей. Изделие в зависимости от его сложности может быть расчленено на большее или меньшее число сборочных единиц.
|
|
Любой сборочный процесс, как правило, состоит из нескольких стадий: 1) подгонки или обработки деталей в сборочной единице (эта операция характерна для единичного или мелкосерийного производств при отсутствии условий, обеспечивающих взаимозаменяемость); 2) предварительной сборки — соединения отдельных деталей в простейшие сборочные единицы и механизмы (агрегаты); 3) общей (или окончательной) сборки изделия; 4) регулирования и испытания изделия.
Дата добавления: 2018-05-02; просмотров: 1232; Мы поможем в написании вашей работы! |
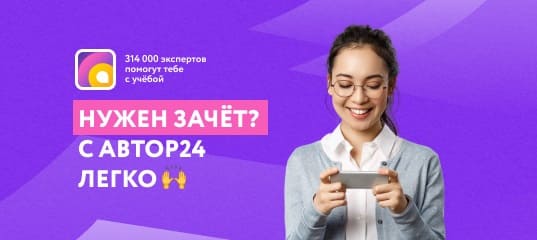
Мы поможем в написании ваших работ!