Обработка заготовок на сверлильных станках
При обработке на вертикально – сверлильных станках (наиболее распространенных) заготовка остается неподвижной, а РИ, вставляемый в шпиндель станка, совершает вращательное и поступательное движения.
В качестве РИ используют:
1. Сверла,
2. Зенкеры,
3. Развертки,
4. Метчики.
При сверлении можно получить отверстия диаметром 0,25 – 80 мм. Если диаметр сверла до 20 мм то он может иметь цилиндрический хвостовик. Конический хвостовик имеют сверла диаметром 6 – 80 мм. Сверла выполняют 2-х перыми из быстрорежущей стали Р9, Р12, Р18, Р6М5, Р6М5К5, низколегированной – 9ХС, твердосплавные ВК6, ВК8, ВК10, ВК15 и др. если диаметр получаемого отверстия в сплошном материале превышает 30 мм, то обработку ведут последовательно 2-мя сверлами.
Сверлением можно получить отверстие по 12 квалитету и Rz = 40 мкм.
Зенкерование выполняется после сверления или чернового растачивания. Припуск под зенкерование составляет около 0,5 – 2,0 мм на сторону, или составляет (0,05 – 0,1)dз.
Режущую кромку зенкеров изготавливают из быстрорежущей стали или твердых сплавов. Форма хвостовика – цилиндрическая и коническая.
По форме режущей части существуют цилиндрические, ступенчатые и конические зенкеры. Конические зенкеры можно использовать после получения предварительного отверстия сверлом.
Зенкеры выполняют из быстрорежущей стали Р9, Р12, Р18, Р6М5, Р6М5К5, низколегированной – 9ХС, твердосплавные ВК6, ВК8, Т5К10, Т15К6 и др.
|
|
Зенкерованием можно получить отверстие по 10 квалитету и Ra = 10 мкм.
Следует различать зенкерование, зенкование и цекование.
Зенкование — обработка заготовок с целью получения конических или цилиндрических углублений, опорных плоскостей вокруг отверстия и снятия фасок центровыхотверстий (рис. 3.52, а).
Зенковка — осевой многолезвийный инструмент для обработки конического входного участка отверстия.
Как и зенкование, цекование является разновидностью зенкерования.
Цекование — обработка поверхности заготовки вокруг отверстия. Оно предназначено для образования плоскостей под головку винта, шайбу, упорное кольцо и др. (рис. 3.52, б).
Цековка — осевой многолезвийный инструмент для обработки цилиндрического и (или) торцевого участка отверстия заготовки. Цековка имеет нижнюю гладкую направляющую часть, вставленную в отверстие, вокруг которого осуществляется обработка, что обеспечивает взаимную перпендикулярность получаемой поверхности и оси отверстия.
Развертывание выполняют после зенкерования (иногда после сверления) или чистового растачивания. Развертка является мерным инструментом (заточенной на определенный размер). Припуск под развертывание составляет 0,08 – 0,2 мм на сторону, или составляет около 0,005dр. форма режущей части (получаемое отверстие) аналогична зенкерам.
|
|
Развертки изготавливают для черновой, получистовой и чистовой обработки. Развертки имеют четное число зубьев. По конструкции хвостовика разделяют развертки с коническим и цилиндрическим хвостовиком.
Развертки выполняют из быстрорежущей стали Р9, Р12, Р18, Р9К5, Р6М5К5, низколегированной – 9ХГС, твердосплавные ВК6, ВК6М, Т15К6, Т5К10 и др.
Развертыванием можно получить отверстие по 6- 9 квалитету и Ra = 0,63 мкм.
Метчиком можно получить резьбу в отверстии на М1 – М52 мм. ручные метчики изготавливают из углеродистой стали У10, У12, машинные из быстрорежущих сталей.
Обработка заготовок на фрезерных станках
При обработке на вертикально и горизонтально – фрезерных станках (наиболее распространенных) заготовка остается неподвижной, а РИ, вставляемый в шпиндель станка, совершает вращательное и поступательное движения.
В качестве РИ используют следующие типы фрез:
1. Цилиндрические,
2. Торцевые,
3. Концевые,
4. Дисковые.
Фрезы с пластинами твердого сплава имеют в 1,5—2 раза более высокую стойкость, позволяют на 20—25 % сократить затраты времени резания, число фрез, обращающихся в производстве, по сравнению с обычными фрезами из быстрорежущих и инструментальных сталей.
|
|
Многообразие конструкций фрез, применяемых в производстве, вызывает необходимость классифицировать их по ряду признаков.
По материалу режущей части фрезы делятся на углеродистые, быстрорежущие и твердосплавные.
По форме режущих зубьев различают фрезы с остроконечными и затылованными зубьями (см. рис. V.2).
По направлению режущих зубьев фрезы подразделяются на прямозубые с винтовыми (см. рис. V.3) или спиральными зубьями.
По своему назначению (характеру выполняемых работ) и расположению лезвий фрезы разделяются на цилиндрические (рис. V.6, а) и торцевые (рис. V.6, б), применяемые для обработки плоскостей; дисковые двусторонние (рис. V.6, в) для фрезерования уступов и дисковые трехсторонние для фрезерования пазов (рис. V.6, г); прорезные (рис. V.6, д) и концевые (рис. V.6, е), используемые для обработки небольших по размеру плоскостей, пазов, уступов, поверхностей криволинейных контуров у изделий плоских форм и др.; угловые (рис. V.6, ж) для обработки угловых пазов и канавок и фасонные (рис. V.6, з) для обработки фасонных поверхностей.
|
|
По способу закрепления на станке фрезы разделяются на насадные, насаживаемые на оправку, и концевые, закрепляемые хвостовиком.
По конструкции фрезы разделяются на цельные, зубья которых выполнены заодно с корпусом; сборные — со вставными зубьями (в виде ножей или непосредственно режущих пластин); составные, например составленные из двух половин и прокладки между ними для восстановления первоначальной длины фрезы после переточки.
По размерам и числу зубьев различают фрезы с мелкими и крупными зубьями. Мелкозубыми принято называть фрезы, число зубьев z которых больше 1,5 ,а крупнозубыми называют фрезы, число зубьев z которых меньше 1,5
, где D — диаметр фрезы, мм. К крупнозубым фрезам относят фрезы со вставными ножами и применяют их для чернового и получистового фрезерования. Мелкозубые фрезы используют для чистового и отделочного фрезерования.
Числа зубьев для мелко- и крупнозубых фрез каждого типа в зависимости от их диаметра установлены государственными стандартами.
В некоторых случаях целесообразно применять одно- и двузубые фрезы, т.е. сборные фрезы, в корпусе которых закреплены один или два диаметрально расположенных зуба. Такие фрезы, называемые иногда летучими, обычно используют для обработки единичных деталей фасонного профиля, а также для фрезерования некоторых цветных металлов и легких сплавов. Широко используются фрезы-летучки в условиях ремонтного производства.
Значения диаметров и ширины фрез нормализованы. Они образуют геометрический ряд со знаменателем прогрессии ф = 1,26. Наружные диаметры стандартных фрез принимаются равными: 16, 20, 25, 32, 40, 50, 63, 100, 125, 160, 200, 250 мм и т.д. до 630 мм. Нормальная ширина цилиндрических фрез составляет ряд с размерами 50, 63, 100, 125 мм. В отверстиях фрез предусмотрены продольный шпоночный паз для передачи крутящего момента от шпинделя с помощью шпонки и внутренняя выточка (во фрезах шириной больше 24 мм).
Хвостовики концевых фрез диаметром меньше 20 мм изготовляют цилиндрическими; у фрез большего диаметра хвостовики выполняют с конусом Морзе или метрическим, стандартизированным по ГОСТ 24644—81.
4.4. абразивная обработка
Абразивная обработка — процесс обработки материалов резанием. Слой металла (припуск) с заготовки снимается в результате резания, осуществляемого абразивным инструментом с большим количеством микрорезцов — абразивных зерен.
К абразивной относятся следующие виды обработки.
Шлифование — обработка вращающимся инструментом — шлифовальным кругом. Вращение круга является главным движением резания и осуществляется со скоростью 10—100 м/с. Шлифование применяют для удаления определенного слоя металла (припуска), придания заготовке требуемой формы, получения заданных чертежом размеров и формы детали, а также требуемой шероховатости поверхности. Шлифование обеспечивает 5—7-й квалитеты, и шероховатость по параметру Ra = 1,2 – 0,1 мкм.
Доводка — обработка, осуществляемая, как правило, после шлифования и направленная на достижение наиболее высокой точности размеров и формы детали, а также высокого качества поверхности. При доводке инструмент и заготовка в большинстве случаев совершают одновременно несколько движений (вращательное, возвратно-поступательное, колебательное) со скоростью 0,1—3 м/с. Доводку используют как финишную технологическую операцию при изготовлении наиболее точных деталей. Доводка обеспечивает 0,1—4-й квалитеты, и шероховатость по параметру Ra =0,10—0,01 мкм.
Полирование — обработка деталей в целях уменьшения шероховатости, получения зеркального блеска, а также удаления дефектного слоя. В результате полирования микронеровности на поверхности детали приобретают сглаженную, закругленную форму, что значительно увеличивает отражательную способность поверхности. В качестве инструмента применяют диск с рабочей торцовой поверхностью. Полированием получают блестящие поверхности с шероховатостью по параметру Ra =0,1—0,04 мкм.
Отрезка — разделение заготовки, например прутка, на части с помощью специального отрезного круга. Отрезку используют также для удаления литников, прибылей с заготовок, полученных литьем. Производительность абразивной отрезки, особенно при высокой (80—100 м/с) скорости, значительно превосходит производительность других видов отрезки (фрезами, дисковыми пилами и др.).
Отделочная обработка — обработка, целью которой являются: удаление поверхностного дефектного слоя металла; снятие заусенцев после обработки резанием и облоя после штамповки и точного литья; закругление кромок; подготовка поверхностей под покрытия; удаление окалины, образовавшейся при термообработке; придание деталям товарного вида. В большинстве случаев отделочную обработку осуществляют путем воздействия на заготовку потока свободных абразивных зерен.
Дата добавления: 2018-04-15; просмотров: 542; Мы поможем в написании вашей работы! |
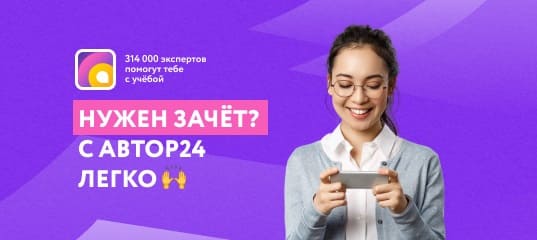
Мы поможем в написании ваших работ!